The Advantages of Prototype CNC Machining in Manufacturing
The manufacturing industry has seen significant advancements in recent years, most notably the rise of prototype CNC machining. Whether it’s on small parts like the automotive parts cleaner machine or precision parts like the automotive industry.
This cutting-edge technology has revolutionized the way products are developed and produced, offering many advantages over traditional manufacturing methods. From design support to finished products, prototypes and low-volume production to repetitive production, computer integrated machining delivers precise results.
In this section, we will explore the advantages of prototype CNC machining in manufacturing industries such as automotive parts cleaner machine.
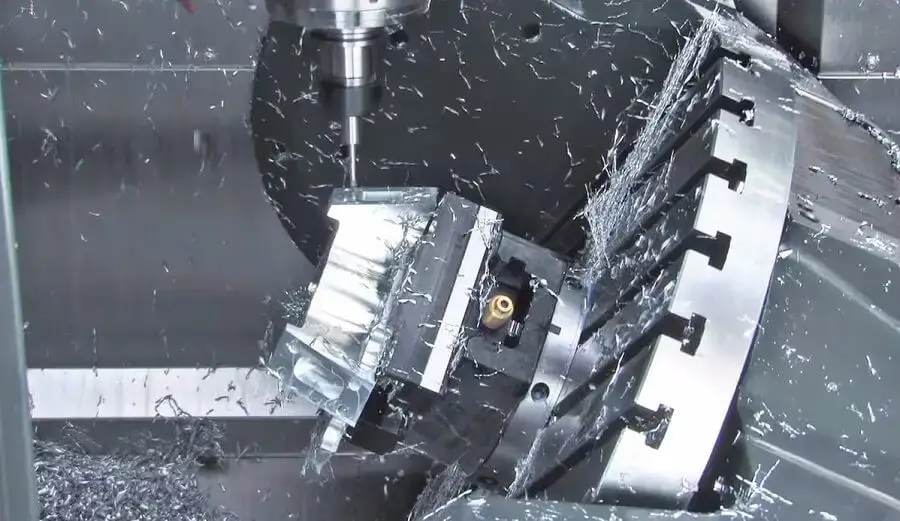
First and foremost, prototype CNC machining offers unparalleled precision and accuracy. Unlike manual machining, which is prone to human error, CNC machines are controlled by computer programs that ensure consistent and precise results. This level of precision is crucial in industries where even the slightest deviation can have severe consequences, such as aerospace or medical device manufacturing. With prototype CNC machining, manufacturers can achieve tight tolerances and intricate designs with ease, resulting in high-quality products that meet the most demanding specifications.
Another advantage of CNC machining of prototypes is its versatility. Because CNC machines can process a variety of materials, including metals, plastics, and composites, this versatility allows manufacturers to explore different design possibilities and select the most appropriate materials for their products. Additionally, CNC machines can handle complex geometries that are challenging or impossible with traditional machining methods. This flexibility of CNC machine tools opens up new possibilities for product innovation and customization, providing manufacturers with a competitive advantage in the market.
Speed is yet another advantage of prototype CNC machining. Traditional manufacturing methods often involve time-consuming processes, such as manual tool changes or setup adjustments. In contrast, CNC machines can perform multiple operations simultaneously, significantly reducing production time. Moreover, once a CNC program is created, it can be easily replicated and reused, further speeding up the manufacturing process. This increased efficiency allows manufacturers to meet tight deadlines and respond quickly to market demands, ultimately improving their competitiveness.
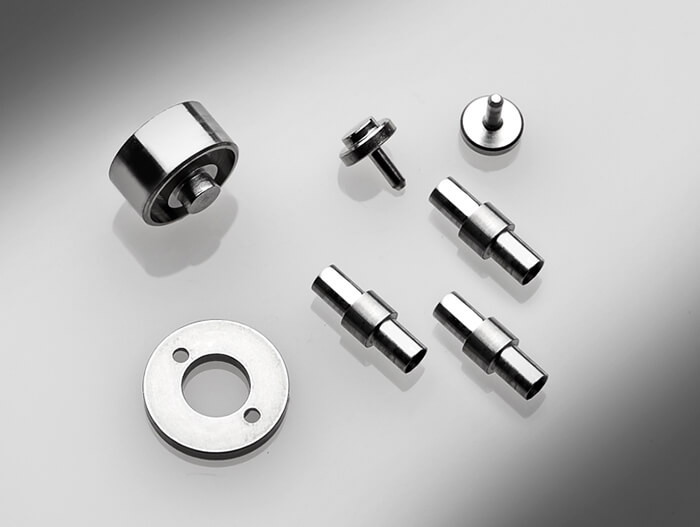
Cost-effectiveness is a crucial consideration for any manufacturing process, and prototype CNC machining delivers in this aspect as well. While the initial investment in CNC machines may be higher than that of traditional machines, the long-term benefits outweigh the costs. CNC machines require minimal human intervention, reducing labor costs and the risk of errors. Additionally, the high precision and repeatability of CNC machining minimize material waste, resulting in cost savings. Furthermore, the versatility of CNC machines allows manufacturers to consolidate multiple operations into a single machine, reducing the need for additional equipment and streamlining production lines. All these factors contribute to a more cost-effective manufacturing process.
Lastly, prototype CNC machining offers improved safety in the manufacturing industry. Traditional machining methods often involve manual handling of heavy materials and tools, posing a risk of accidents and injuries. With CNC machines, operators can program the machine to perform the necessary tasks, eliminating the need for manual intervention. This automation not only reduces the risk of accidents but also improves the overall working conditions for operators.
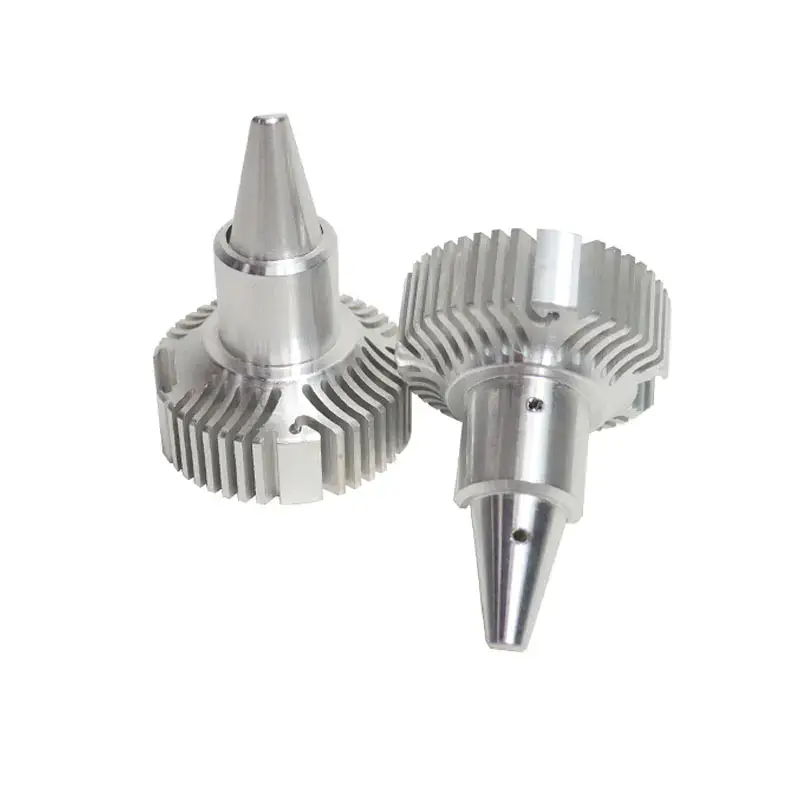
In conclusion, prototype CNC machining has revolutionized the manufacturing industry by offering numerous advantages over traditional manufacturing methods. The precision, versatility, speed, cost-effectiveness, and safety provided by CNC machines make them the future of manufacturing. As technology continues to advance, we can expect further enhancements in CNC machining, leading to even more efficient and innovative manufacturing processes.