Importance of Rapid Injection Molding
Rapid injection molding is an injection molding method designed to produce parts quickly and efficiently, bridging the gap between initial prototypes and mass production. It is ideal for producing anywhere from a few to 10,000 parts in a matter of weeks. It embodies a combination of speed and accuracy, making it a top choice for companies across a wide range of industries.
They are powerful enough to manufacture anywhere from a few parts to thousands of parts. Many manufacturers use this process to produce molded parts based on customer requirements. Most importantly, it is the most convenient way to efficiently meet customer needs and specifications without the hassle. Rapid injection molding stands out for its ability to streamline the entire process from concept design to finished product, offering a number of advantages.
1.Speed and Efficiency of Prototyping and Production
One of the most notable advantages of rapid injection molding is its unparalleled speed and efficiency. The process allows for rapid development of prototypes, which speeds up the transition to the production phase. This rapid progress is essential to beating competitors in the market and testing concepts without incurring expensive delays.
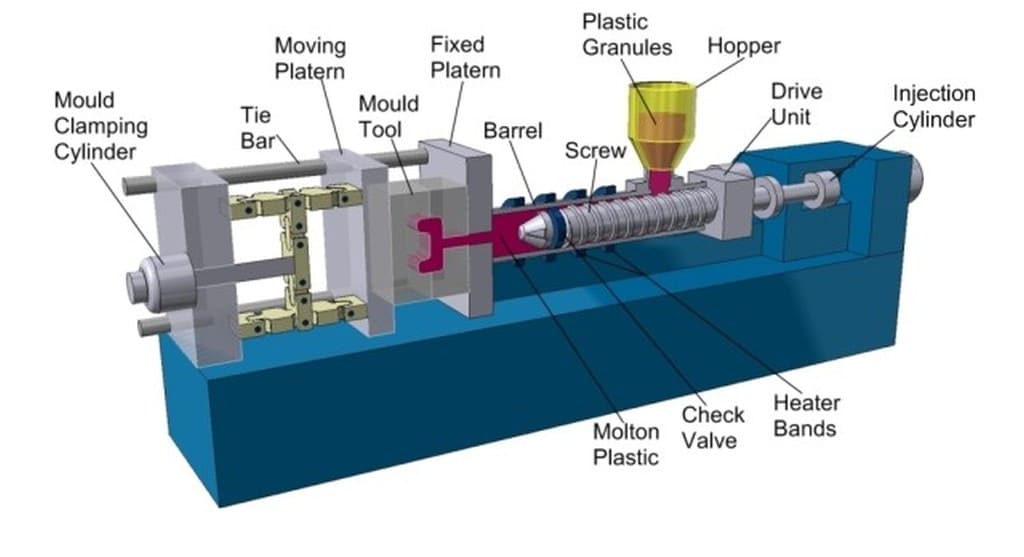
2.Cost-effectiveness of Small and Medium-Scale Production
Rapid injection molding is cost-effective, especially for small and medium-scale production. Using aluminum molds, which are cheaper and faster to manufacture than traditional steel molds, can significantly reduce upfront costs. This affordable price allows companies to manage budgets more effectively while still achieving high-quality output.
3.Diversity of Materials and Design Capabilities
The process offers exceptional versatility to accommodate a wide range of materials and design specifications. Whether you are working with engineering resins, ABS, polypropylene, or polycarbonate, rapid injection molding can accommodate a wide range of material requirements. In addition, it supports complex designs, ensuring that the final part meets precise specifications.
4.Improve Precision and Consistency in Part Production
Achieving precision and consistency is critical in the manufacturing process. Rapid injection molding excels at producing parts with tight tolerances and uniform quality. This precision ensures that every part will function properly and meet or exceed the performance standards set for the project.
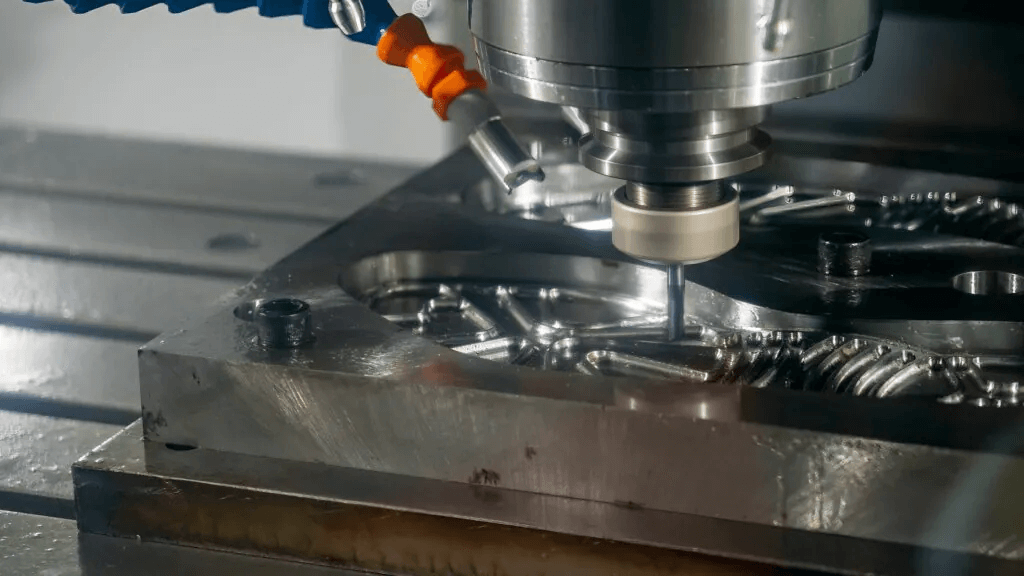
5.Enhanced Product Development Flexibility
Rapid injection molding provides unparalleled flexibility in product development. Design changes can be implemented quickly and without significant cost penalties, allowing for iterative design improvements. This adaptability is essential for optimizing product design and functionality.
6.Reduced Time to Market
A direct result of the speed and efficiency of the process is a significant reduction in time to market. Companies can quickly move from concept to commercialization, gaining a competitive advantage in a fast-paced market. This agility is essential for responding to consumer demands and market trends.
7.Sustainable Manufacturing and Waste Reduction
The precision of rapid injection molding minimizes waste generation and is consistent with sustainable manufacturing practices. Efficient use of materials not only conserves resources, but also reduces the overall environmental impact of the manufacturing process.
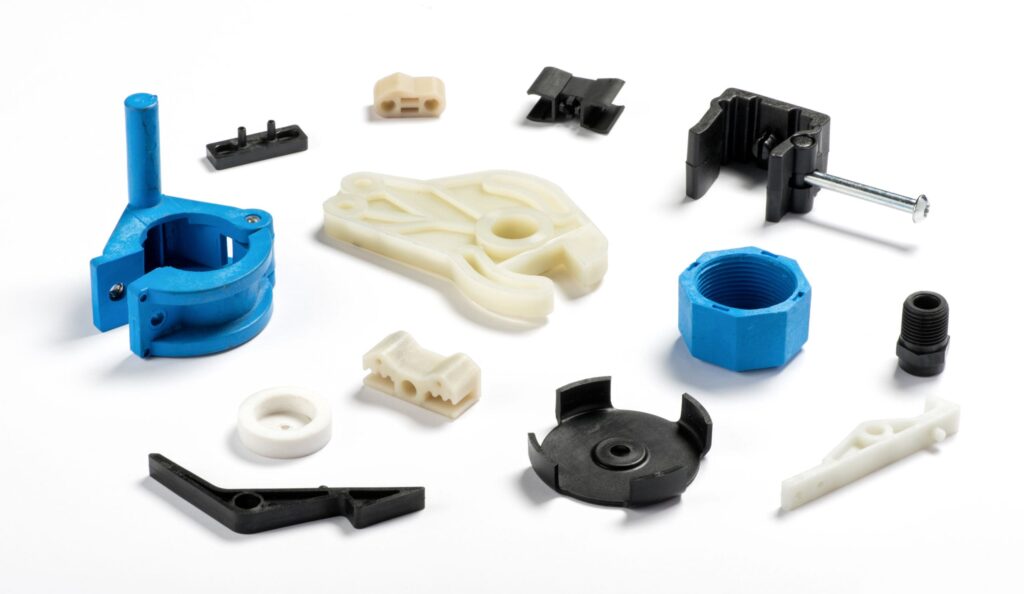
8.Ability to Respond Quickly to Market Changes
Finally, rapid injection molding enables companies to respond quickly to market changes. Whether it’s adapting to new consumer preferences or incorporating the latest technological advances, the process supports dynamic adaptation, ensuring companies remain relevant and competitive.
Rapid injection molding represents a major advancement in the manufacturing industry, providing speed, flexibility, and high-quality production. The future of rapid injection molding in the manufacturing industry is bright. As technology evolves and the demand for faster, more efficient production continues to increase, rapid injection molding will continue to be an important tool for innovators and manufacturers.