Rapid Tooling Technology: A Magical Weapon for Gaining Competitiveness
Rapid Tooling Technology (RT) is based on Rapid Prototyping Technology (RP). It is a new manufacturing technology developed to shorten the new product development cycle and launch marketable, customized, multi-variety, and small-batch products to the market as soon as possible.
The market needs efficiency and agility. The ever-changing manufacturing environment has led to the development of innovative processes. Due to the rapid development of rapid prototyping technology and 3D software, a new field of rapid tooling technology has emerged to meet the specific market needs of the manufacturing industry. Therefore, this article will take you to fully understand the rapid tooling design process and manufacturing process, as well as their development overview.
1.Rapid Tooling Design Technology
Rapid tooling design technology refers to the use of some current commercial 3D software, such as Pro/E, UG, etc. First, use 3D software to design the 3D model of the product, and then design the mold structure based on this 3D model, and perform simulation analysis in the 3D software to check the reliability of the structure of the designed mold and predict the defects that may occur in the mold, so as to provide some guiding opinions for the actual manufacturing of the mold, shorten the mold design cycle, and reduce the mold cost.
(1) Establishment of product 3D model
Mold designers can establish product 3D models through 3D software such as Pro/E and UG. Using the extension, cutting, rotation, and surface modeling functions of 3D software, you can design a 3D model of the product, or directly establish a 3D model of the product in the 3D software according to the design ideas and design requirements of the parts design department.
(2) Establishment of mold 3D model
According to the 3D model of the designed product, establish the 3D model of the mold in 3D software such as Pro/E and UG. First, import the 3D model of the product into the mold design module of the 3D software as the prototype of the mold design, and then gradually establish the design of other parts of the mold based on this prototype, such as the design of the mold cavity, core, slider, pouring system, ejection system and other related structures. You can also use the assembly module for 3D assembly design.
(3) Traditional mold design technology VS new rapid tooling design technology
The traditional mold design process is a typical serial process. Each design process is highly constrained by each other, the production cycle is long, and it is very labor-intensive and time-consuming. At the same time, it is easy to cause inconsistency between processing data and design data, increasing the probability of producing scrap.
The new rapid mold design technology adopts a parallel process flow, avoiding some defects of traditional mold design technology, greatly shortening the mold design and manufacturing cycle, and mold design and manufacturing are based on a unified geometric model, ensuring the uniformity and correctness of model data, showing its unique superiority, and is being widely used in the field of mold design and manufacturing.
2.Rapid tooling manufacturing technology
Rapid tooling manufacturing technology refers to the use of some advanced processing technologies and manufacturing methods, such as information technology, CNC processing technology, rapid prototyping technology, etc., to improve the quality of mold manufacturing and shorten the mold manufacturing cycle.
(1) Overview of rapid tooling prototyping technology
Rapid tooling prototyping technology (RPM) is a new technology that uses 3D model data of parts to quickly and accurately manufacture the parts. It is a multi-disciplinary and multi-technical new technology that integrates CAD technology, CNC technology, laser processing, new materials science, and mechanical and electronic engineering.
Rapid tooling technology uses the physical prototype generated by RPM as the mold core or mold sleeve, combined with precision casting, powder sintering or electrode grinding technology to quickly manufacture the functional mold required for the product. Its manufacturing cycle is generally 1/5~1/10 of the traditional CNC cutting method, which can significantly improve production efficiency. The mold can be directly manufactured using RPM technology, or it can be manufactured using rapid physical prototypes through intermediate conversion.
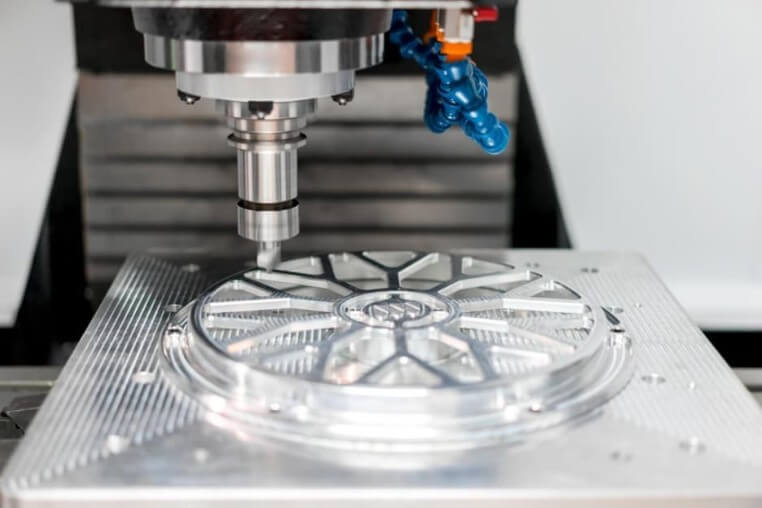
(2) Direct mold manufacturing using RPM
Using the prototype directly as a vaporization mold or replacing the wax mold for investment casting simplifies the mold making process and saves mold making time. In addition, the prototype can also be used to replace the wooden mold to make sand molds, which not only reduces the mold making cost, but also greatly improves the mold precision. Because the prototype uses better materials and better mechanical properties, the mold is not easy to warp and crack when under pressure or heat.
① Use LOM method to make molds
Laminar entity manufacturing (LOM) method uses paper coated with hot melt on one side to heat and bond together with a heating roller. The laser beam located above cuts the paper into the required shape along the outline of the layered product generated by CAD and pastes it on the previously made laminate. After repeated layer-by-layer cutting, bonding and cutting, the entire part model is completed.
After surface treatment such as peeling, grinding, polishing, and spraying, the model has good mechanical strength and can withstand high temperatures of 200~C.
Uses:
The treated model can be used as a wooden mold for sand casting, a casting mold for low-melting alloys, a plastic mold for trial production, and a mold for lost wax casting wax molds.
② Use SIS method to make molds
Selective laser sintering (SLS) method uses the controlled movement of a laser emitting device to scan the powder layer by layer. Where the laser scans, the powder sinters to form a component of the physical model until a complete physical model is formed.
The SLS method can selectively fuse metal powder wrapped with thermoplastic binder to form a semi-finished mold, which is then placed in a heating furnace to burn out the contained binder, sinter the metal powder, and infiltrate a second metal (such as copper) in the gap to make plastic molding molds such as injection molding, die casting, extrusion, and sheet metal forming molds. The plastic mold made in this way has a relatively long life.
(3) Indirect mold manufacturing using RPM
The indirect molding method refers to the use of mold prototype manufacturing technology to first make a mold core, and then use this mold core to copy a hard mold, or make a master mold to copy a soft mold. By combining advanced mold manufacturing technologies such as precision casting, intermediate soft mold transition method, metal spraying, electrospark machining, and grinding with rapid prototyping, various simple rapid tooling and steel molds can be quickly manufactured.
① Make simple molds
If the batch size of the parts is small or used for trial production of products, simple molds with relatively low production costs can be made of non-steel materials.
This type of mold generally uses RP technology to make a prototype of the part, and then according to the prototype, it is made into a silicone rubber mold, a metal mold, a resin mold or a plaster mold, or the prototype of the part is surface treated and a layer of alloy with a lower melting point is plated by metal spraying or physical evaporation deposition to make the mold.
If the master mold is used to make a plaster mold, and then cast aluminum, zinc and other non-ferrous alloy molds under vacuum conditions, small batch injection products can also be produced.
② Making steel molds
There are currently some methods for making steel molds using rapid tooling forming technology:
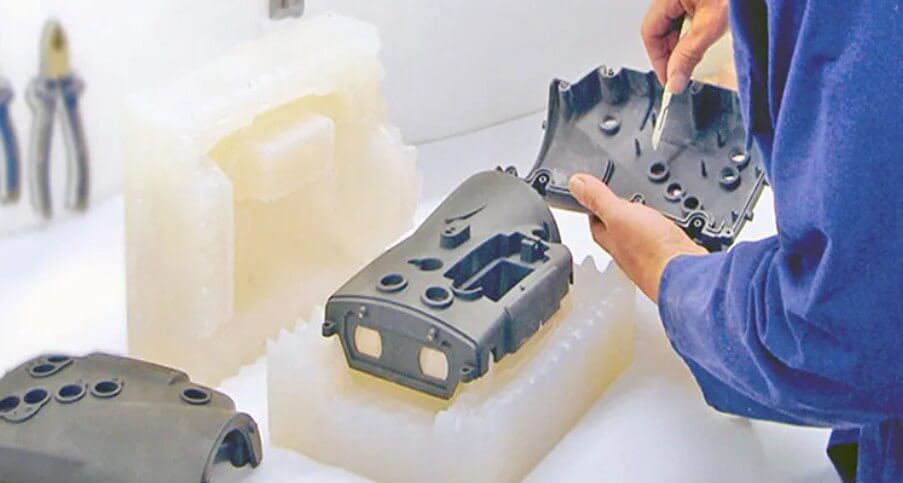
[1] Ceramic mold precision casting method
This method can be used for single-piece or small-batch production of steel molds. The process is: RPM prototype as master mold – dip and hang ceramic mortar – solidify the mold shell in the roasting furnace – burn the master mold – preheat the mold shell – cast the steel mold cavity – polish – add pouring and cooling system – make an injection mold. This mold has good machining performance and can be partially cut to achieve higher precision.
【2】 Lost wax precision casting method
When mass-producing metal molds, first use the RPM prototype or a soft mold made according to the prototype to make a wax mold molding mold, then use the molding mold to produce a wax mold, and then use the lost wax precision casting process to cast a steel mold with a metal-based synthetic material. The mold life can reach 1,000 to 10,000 pieces. When producing complex molds in a single piece, the RPM prototype can also be used directly instead of the wax mold.
【3】 Electrospark machining method
This method uses the RPM prototype as the matrix, and makes metal electrodes or graphite electrodes by spraying or coating metal, powder metallurgy, precision casting, pouring graphite powder or special grinding, and then uses electrospark machining to make steel molds. The production process is generally as follows:
BPM prototype-three-dimensional grinding wheel-graphite electrode-steel mold
(4) CNC technology for molds
CNC machining technology CNC rapid prototyping: innovative developmentfor rapid tooling refers to a method of using digital signals to control the movement of machine tools and their mold processing processes, such as CNC turning technology, CNC milling technology, and ultra-high-speed cutting technology.
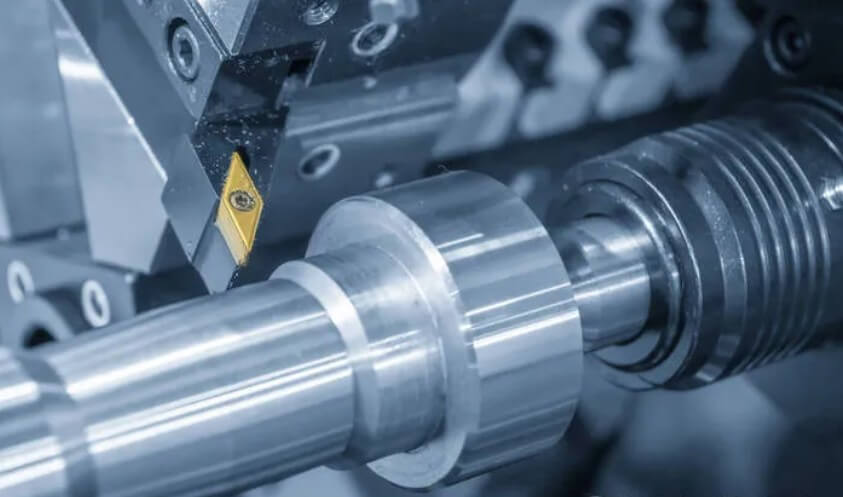
The wide application of CNC machining technology in mold manufacturing provides new process methods and processing methods for modern mold manufacturing, making the computer design process finally transformed into reality. It not only improves the processing accuracy of the mold, but also greatly shortens the mold design cycle by combining it with rapid mold design technology, realizing parallel design of the mold.
① CNC milling technology
CNC milling technology refers to inputting processing programs on CNC milling machines to process mold parts with different shapes, such as die-casting molds for motorcycle cylinders and plastic molds for TV sets.
Advantages and applications:
CNC milling technology has high production efficiency and processing accuracy, can realize multi-axis linkage, and can process mold parts with complex shapes. It is increasingly widely used in the mold industry.
② CNC turning technology
CNC turning technology refers to the method of processing mold parts by clamping the workpiece on the fixture of the lathe for high-speed rotation, using a computer to control the geometric movement of the turning tool in the X and Z directions, and controlling the rotation speed of the lathe spindle and the feed speed of the turning tool at the same time.
Advantages and applications:
CNC turning technology has the characteristics of high precision, small surface roughness of the processed mold parts, and the ability to process molds with complex contours. It can be used for processing parts with ultra-precision, ultra-low surface roughness, and complex surfaces, such as disks, CDs, eye lenses and other high-precision molds. It has accelerated the development trend of complexity and precision in the production of rapid tooling.
③ Ultra-high-speed cutting technology
Ultra-high-speed cutting technology is an advanced manufacturing technology that cuts parts at a speed about 10 times higher than conventional technology. Ultra-high-speed cutting technology is the direction of future cutting processing and a product of the development of the times. It relies on the emergence of basic technologies such as CNC technology, microelectronics technology, new materials and novel components.
Advantages and applications:
It has the advantages of high efficiency, good processing quality and low processing cost. It has strong vitality and broad application prospects in the mold industry such as automobile and aviation.
3.Comparison and analysis of molds
(1) Rapid tooling and rapid prototyping
Making a rapid tooling refers to the production of a tool or mold that enables manufacturers to quickly produce product parts with tool functions.
Rapid tooling prototyping technology is a technology or method that helps to quickly produce physical parts for final use or use as prototypes.
The following is a comparison between rapid tooling and rapid prototyping:
Aspect | Rapid Tooling | Rapid Prototyping |
Cost | Initial setup cost may be higher (tooling costs), cost-effective for low-to-medium production volumes. | Initial cost is lower (no tooling fees), ideal for early design verification. |
Delivery Time | Short lead time (especially for production tools), suitable for fast product development cycles. | Quick turnaround for prototypes, limited impact on overall product development time. |
Material | Mold usually made of metal; workpieces can be plastic or metal parts. | Supports wide range of materials (plastics, metals), often uses materials simulating final product properties. |
Accuracy | High accuracy (especially for production-level tools), suitable for small tolerance and precise requirements. | Accurate for prototyping, but may have limitations in achieving the same accuracy as rapid tooling in final production. |
Complex Geometry Handling | Capable of handling complex geometries; ideal for intricate tool designs. | Ideal for visualizing/testing basic to moderately complex designs; challenging with extremely complex geometries. |
Application Areas | Ideal for industries needing economical small batch production (small to medium runs). | Mainly used for design verification/rapid iteration; common in industries requiring rapid iteration. |
(2) Rapid tooling and traditional mold
In the manufacturing industry, the choice between CNC rapid tooling and traditional mold determines its subsequent production efficiency and cost. Rapid tooling has significant advantages in providing product speed and precision, while traditional mold provides stability for long-term, large-scale production.
The following is a comparison between rapid tooling and traditional mold:
Category | Rapid Tooling | Traditional mold |
Event Ticket Price List | Generally speaking, it is more cost-effective for shorter production cycles. | The initial cost is higher, but it may be economical for large-scale production. |
Delivery time | The delivery time is significantly shortened. It is very suitable for quick response to market needs. | Longer lead time, especially for complex molds. Reliable for large-scale, long-term production. |
Material | A variety of material options to meet different manufacturing needs. The mold is mainly made of metal materials. | Supports multiple materials and often has more options than rapid tooling. It is suitable for diverse production requirements. The mold is mainly made of steel metal. |
accuracy | Generally has higher accuracy and is suitable for production-level tools. | Provides high precision and accuracy, especially suitable for long-term stable production. |
complex | Capable of handling complex geometries and suitable for sophisticated tool designs. | Ideal for extremely complex geometries and detailed tooling requirements. |
Application Areas | Ideal for industries that require flexibility, fast adaptation and small to medium production. Use for prototypes only when product development projects are underway and 90% certain to succeed. | As samples for testing before large and small batch production. |
(3) Rapid tooling and die casting
Rapid tooling and die casting are two different production methods. Rapid tooling emphasizes speed and flexibility, in stark contrast to die casting, the biggest feature of which is the ability to manufacture large-scale complex parts with maximum efficiency.
The following is a comparison between rapid tooling and die casting:
Category | Rapid Tooling | Die Casting |
Event Ticket Price List | Generally speaking, it is more cost-effective for shorter production cycles. | May have higher initial tooling costs but can provide cost benefits for high volume production. |
Delivery time | Significantly shortens delivery time, ideal for quick response to market demands. | The initial tooling may take longer, but once it is set up, production lead times are relatively short, allowing for efficient mass production. |
Material | A variety of metal and plastic materials are available to meet different manufacturing needs. | Applicable to various metal alloy materials, especially aluminum, zinc, magnesium and other metals. |
accuracy | Generally has higher accuracy and is suitable for production-level tools. | It offers high precision and accuracy, making it suitable for complex and detailed parts. |
complex | It is capable of handling complex geometries and is suitable for intricate tool designs. | Ideal for complex part designs, providing high-detail reproduction. |
Application Areas | Ideal for industries requiring flexibility, quick adaptation and small to medium production. | Typically used in high-volume production of complex parts in industries such as automotive, aerospace and electronics. |
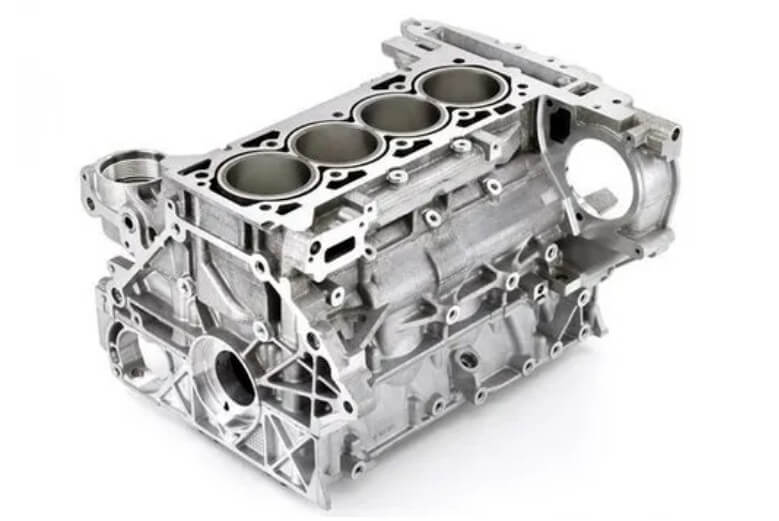
(4) Rapid tooling and injection molding
As above, each production method has its own advantages. Rapid tooling emphasizes speed and flexibility, while injection molding emphasizes the production of large quantities of complex plastic parts in an efficient manner.
The following is a comparison between rapid tooling and injection molding:
Category | Rapid Tooling | Injection Molding |
Event Ticket Price List | Since the molds are cheaper, the cost is significantly reduced. | May have higher initial tooling costs but can provide cost benefits for high volume production. |
Delivery time | Significantly shortens delivery time, ideal for quick response to market demands. | The initial tooling may take longer, but once it is set up, production lead times become efficient, especially for high volume production. |
Material | A variety of material options to meet different manufacturing needs. | A wide range of materials is supported, especially plastics, and various additives can be adapted to obtain specific properties. |
accuracy | Generally has higher accuracy and is suitable for production-level tools. | Offers high precision and accuracy, making it suitable for complex and detailed parts. |
complex | Capable of handling complex geometries and suitable for sophisticated tool designs. | Suitable for complex part design, providing high-detail reproduction. |
Application Areas | Ideal for industries requiring flexibility, quick adaptation and small to medium production. | It is commonly used in the mass production of plastic parts across a variety of industries, including automotive, consumer goods and medical devices. |
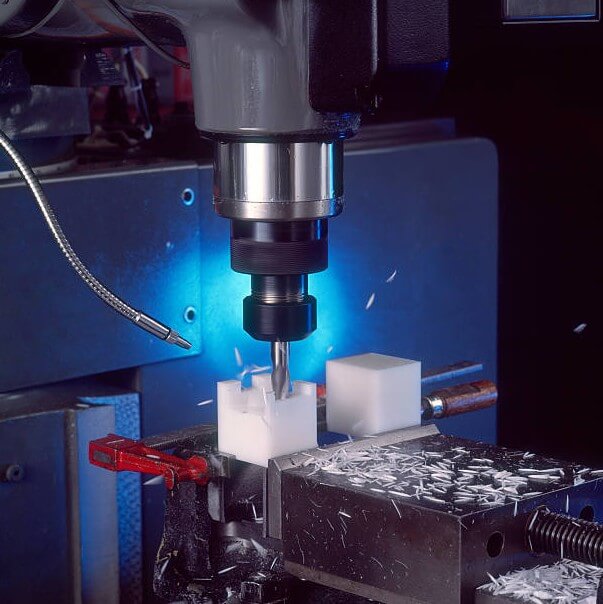
Injection mold
(5) Soft mold making and hard mold making
In the field of rapid tooling, soft mold making and hard mold making are two commonly used terms.
Soft mold making generally uses silicone molds and polyurethane casting processes. Similar to rapid tooling, soft mold making is mainly used for prototyping, transition mold making and small batch production.
Hard mold making is a synonym for metal mold making and is most commonly used in the field of injection molding. Aluminum can be used as the main material to produce hard molds using rapid tooling methods. Hard molds are durable and can be used for large-scale production, but their cost is much higher than soft mold making or most rapid tooling methods, so they are more suitable for mass production.
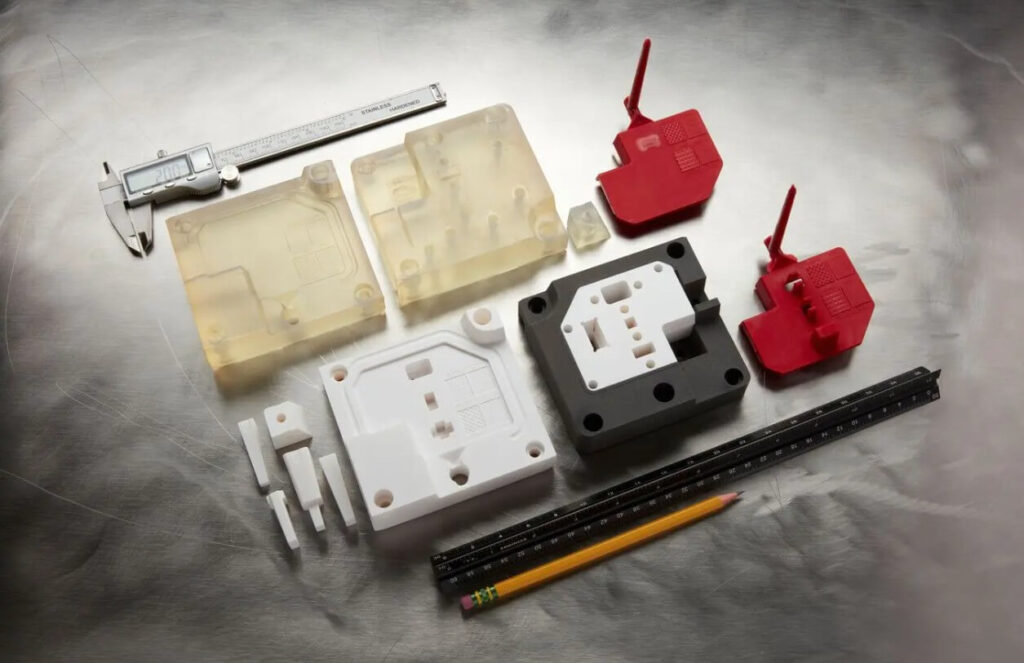
4.Summary
Nowadays, rapid tooling technology has been more and more widely used in industry and manufacturing. By using rapid tooling technology, products that meet user needs can be quickly launched in a short period of time, which greatly reduces the cost of new product development and investment risks, and meets the requirements of modern manufacturing industry for time, quality and cost. In order to enhance the competitiveness of enterprises, it is necessary to master and apply rapid tooling technology.
If you are looking for an experienced rapid tooling and prototyping manufacturer,Xavier is your ideal choice. The Xavier team is well equipped to provide high-quality rapid tooling and prototyping solutions. If you need more information or want to discuss your design needs with us, please feel free to contact us.