Removing anodize: Analysis and Comparison of Common Methods
Anodized films are widely used for metal surface treatment because of their hardness, abrasion resistance, and aesthetics.
However, in some cases, such as machining errors or surface defects, it is necessary to removing anodize film. In this article, we will discuss and compare several common methods of removing anodize and compare them to help readers choose the most suitable treatment for their needs.
1.Anodic oxidation process and mechanism
(1) Anodic reaction in electrolyte
In the anodic oxidation process, the metal is placed in the electrolyte solution as an anode. When the current passes, the metal surface undergoes an oxidation reaction to form an oxide film. Specifically, the anodic reaction mainly includes the dissolution of the metal and the formation of oxides. In the case of aluminum, for example, aluminum atoms lose electrons at the anode to form aluminum ions, and these aluminum ions combine with oxygen ions in the solution to form an aluminum oxide film.
(2) The role and effect of cathodic reaction
In the anodic oxidation process, the main role of the cathode is to conduct electricity and promote the precipitation of hydrogen. The cathode reaction helps to maintain the charge balance in the electrolyte solution, which indirectly affects the growth and quality of the anodic oxide film. The selection of cathode materials and structural design has an important impact on the stability and efficiency of the anodic oxidation process.
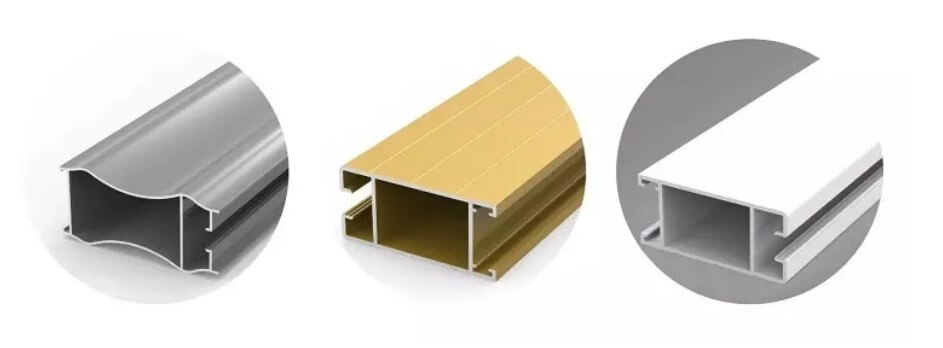
(3) Formation and control of oxide film
The formation process of the oxide film is affected by a variety of factors, including electrolyte composition, current density, temperature, etc.. By adjusting these parameters, the thickness, structure and performance of the oxide film can be controlled. For example, in the anodic oxidation process of aluminum, the commonly used electrolytes are sulfuric acid, oxalic acid, etc. Different electrolytes will form oxidized films with different characteristics. Changes in current density and temperature will also affect the growth rate and dissolution rate of the oxide film, thus affecting the final film thickness and film quality.
2.Why removing anodize?
Anodizing is a treatment technique commonly used on metal surfaces to generate an oxide film on the surface through an electrolytic process to improve the corrosion resistance, wear resistance and decorative properties of the material. However, in some cases, the anodized film needs to be removed for further processing or repair. Several reasons for removing anodize film will be described below:
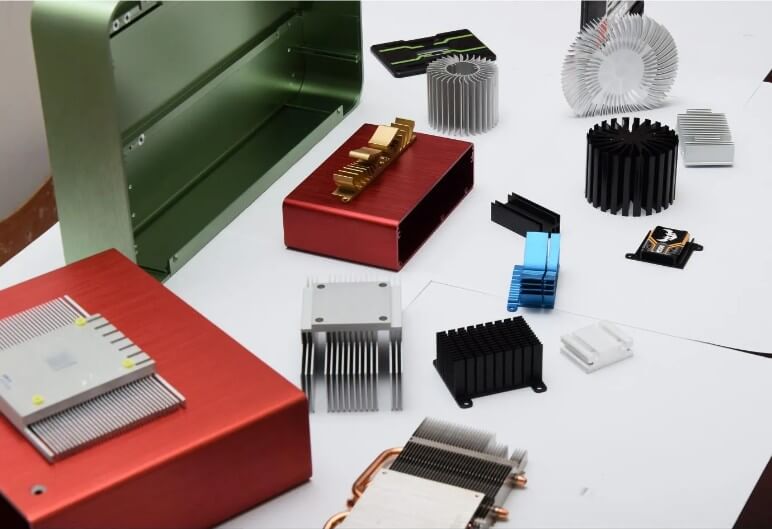
(1) Enhancement of electrical conductivity:
Although anodic oxide film can enhance corrosion resistance, in some application scenarios, such as electronic component manufacturing, good electrical conductivity is required, and removing the anodic oxide film ensures that the current passes through smoothly.
(2) Enhanced bonding effect:
In the need for bonding or coating the surface of the workpiece, the presence of anodic oxide film will affect the adhesive penetration and adhesion, remove the anodic oxide film can significantly improve the bonding strength and coating uniformity.
(3) Improvement of appearance:
Anodic oxide film may lead to uneven color or defects on the surface of the workpiece, by removing the anodic oxide film can make the surface of the workpiece smoother and more beautiful, to meet the high standard of appearance requirements.
(4) Facilitate subsequent processing:
In the subsequent process of machining, welding and other subsequent processes, the oxide film will become an obstacle, and the removal of anodic oxide film can ensure the smoothness of subsequent processing and processing quality.
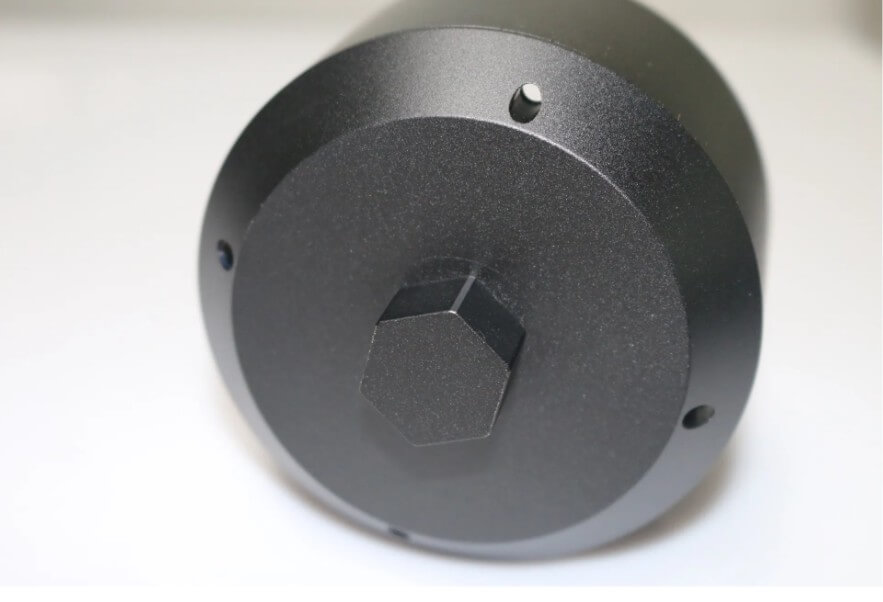
3.How to removing anodize? Common method analysis
(1) Mechanical removal method
1) Sanding paper:
Use different grit sandpaper from coarse to fine sanding gradually, can gradually removing anodize film. This method is simple and direct, but it is suitable for small area or local treatment, and it is less efficient for removing the oxide film in large area, and it is easy to produce scratches.
2) Sandblasting:
Use high-pressure air to spray fine abrasives onto the metal surface, and removing anodize film through the impact of abrasives. Sandblasting treatment is relatively uniform and suitable for large area treatment, but it requires specialized equipment and protection, and the operation cost is high.
(2) Chemical removal method
1) Acid washing method:
Use acidic solutions such as nitric acid, sulfuric acid or phosphoric acid to soak or spray the metal, the oxide film will be dissolved under the action of acid. Acid washing method is more efficient, but care needs to be taken to control the concentration of acid and treatment time to avoid excessive corrosion of the base material. For example, a mixture of nitric acid and hydrofluoric acid (volume ratio of 3:1) treated at room temperature for 5-15 seconds can effectively removing anodize film on aluminum alloy products containing silicon or manganese.
2) Alkaline washing method:
Soak the metal in hot sodium hydroxide solution, the oxide film will be removed by chemical reaction under the action of alkali. The alkali washing method is more effective for removing oil and natural oxide film, but it is also necessary to control the solution concentration and treatment time to prevent corrosion of the base material. For example, the traditional process uses a mixed solution of sodium phosphate, sodium hydroxide and sodium silicate for degreasing and alkaline washing treatment.
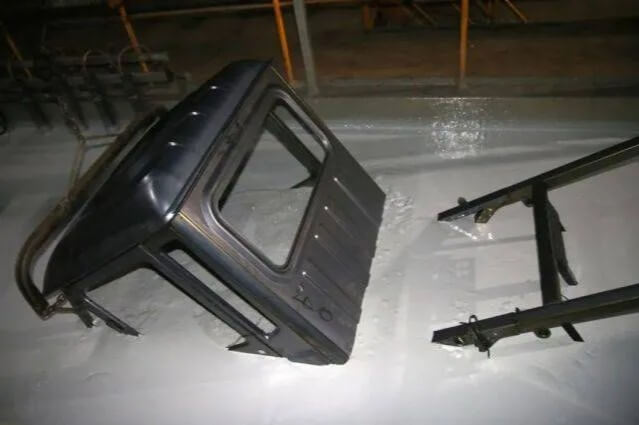
(3) Electrolytic removal method
1) Electrolytic polishing:
The metal is used as the anode and energized in a specific electrolyte to removing anodize film on the surface through electrolysis. Electrolytic polishing can not only remove the anodic oxide film, but also make the surface smooth and delicate, but requires specialized equipment and electrolyte formula, and the operation process requires strict control of the current density and processing time.
2) Reverse electrolysis:
In the anodizing electrolyte, the metal is energized as the cathode, and the oxidized film is dissolved through reverse electrolysis. This method is suitable for removing anodize film, but attention needs to be paid to controlling the current and time to avoid excessive corrosion of the substrate material.
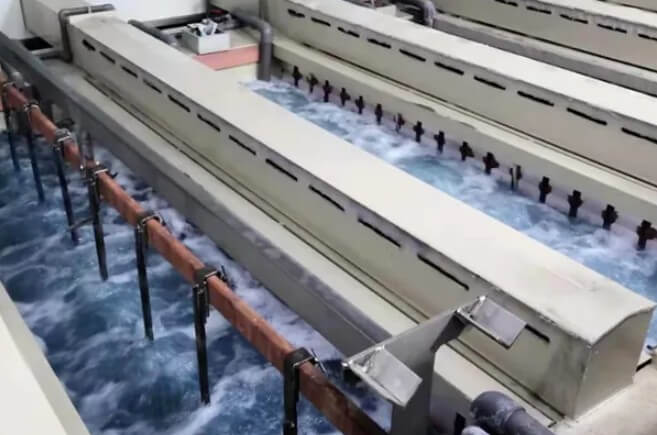
(4) Comprehensive methods
1) Acid washing combined with mechanical friction:
First use an acidic solution for the initial treatment of metal products, soften or local removal of anodic oxide film, and then combined with mechanical friction methods to further removing anodize film. This method combines the advantages of chemical and physical methods, which improves the removal efficiency and reduces the risk of corrosion of the chemical solution on the base metal.
2) Ultrasonic cleaning:
The metal products will be placed in an ultrasonic cleaning machine containing acidic or alkaline solution, the use of ultrasonic cavitation to accelerate the dissolution and removing anodize film. Ultrasonic cleaning has the advantages of good cleaning effect, no damage to the base metal, but requires specialized ultrasonic cleaning equipment.
(5) Laser removal method
1) principle:
Laser removal method uses the high energy density of the laser beam to irradiate the surface of the anodic oxide layer, so that it rapidly warms up and gasification or stripping. Because of the precise controllability of the laser beam, it can realize the local and selective removing anodize layer, and the effect on the base metal is very small.
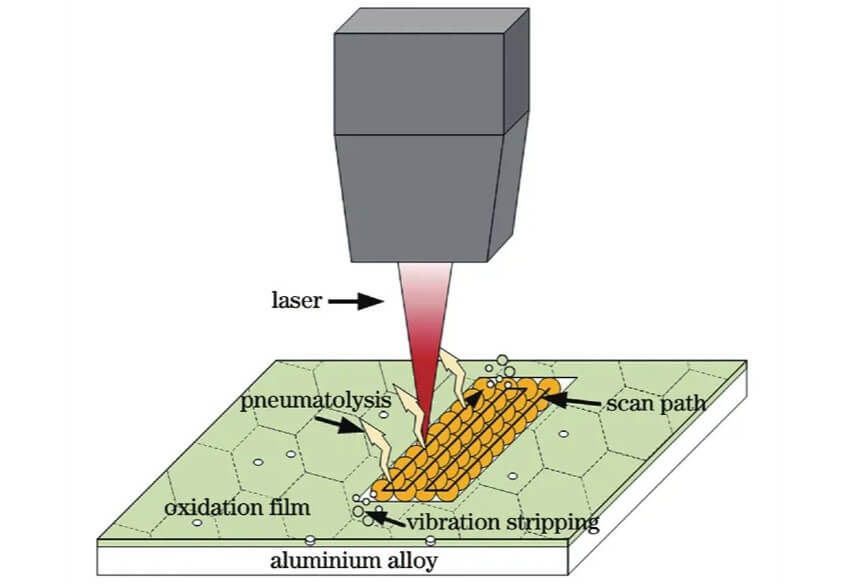
.
Laser Removal Process of Anodized Film on 5083 Aluminum Alloy
.
2) Advantages:
High precision: the laser beam can be focused to a very small spot to achieve micron-level removal accuracy.
Small damage: due to the short laser action time, small heat-affected zone, the damage to the base metal is almost negligible.
High efficiency: the laser removal speed is fast, suitable for large area and high efficiency removal operation.
Strong flexibility: laser parameters (such as power, wavelength, pulse width, etc.) can be adjusted to adapt to different thickness, material and shape of the workpiece.
3) Application:
Laser removal is widely used in aerospace, automobile manufacturing, electronic products and other fields, especially in occasions requiring high precision and low damage, such as repairing precision parts and removing anodize layers.
(6) Precautions
1) When carrying out the operation of removing the anodic oxide film, protective gloves, goggles and other protective equipment should be worn to prevent the chemical solution from splashing on the skin or eyes and causing injury.
2) The surface of treated metal products should be cleaned and dried in time to prevent re-oxidation or corrosion.
4.Comparison of the best methods for removing anodize aluminum oxide
There are various methods to removing anodize aluminum oxide, and each method has its advantages and disadvantages as well as applicable scenarios. The following is a comparison of several common methods of removing anodize aluminum oxide:
(1) Chemical immersion method
1) Application scenario: suitable for small-scale, light oxide layer removal.
2) Advantages: simple operation, lower cost.
3) Disadvantages: It takes a long time, and there is a certain risk of corrosion on the aluminum substrate.
(2) Electrolysis
1) Applicable scenarios: suitable for large-scale industrial production, able to accurately control the removal thickness.
2) Advantages: high removal efficiency, can selectively control the amount of anodic oxide layer removal.
3) Disadvantages: high cost of equipment, complex operation, requiring specialized knowledge and skills.
(3) Mechanical grinding method
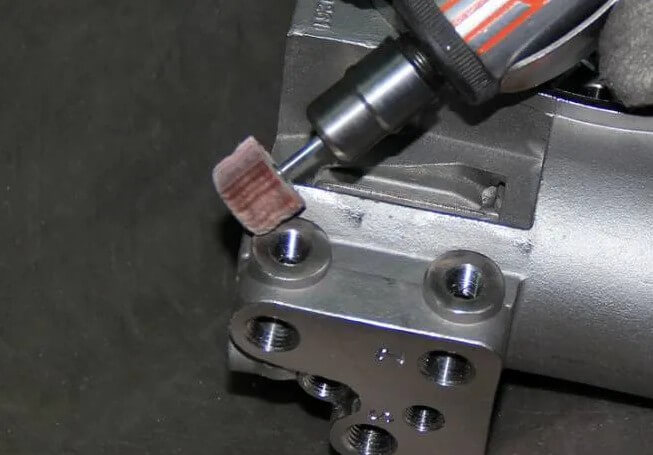
1) Applicable scene: suitable for local or small area oxide layer removal.
2) Advantages: direct and effective, can instantly see the removal effect.
3) Disadvantages: labor-intensive, not suitable for large area treatment, easy to damage the aluminum substrate.
(4) Laser removal method
1) Applicable scenarios: suitable for high-precision, small area of the oxide layer removal.
2) Advantages: extremely high precision, no damage to the surrounding area, automated control.
3) Disadvantages: expensive equipment, high maintenance costs, relatively slow processing speed.
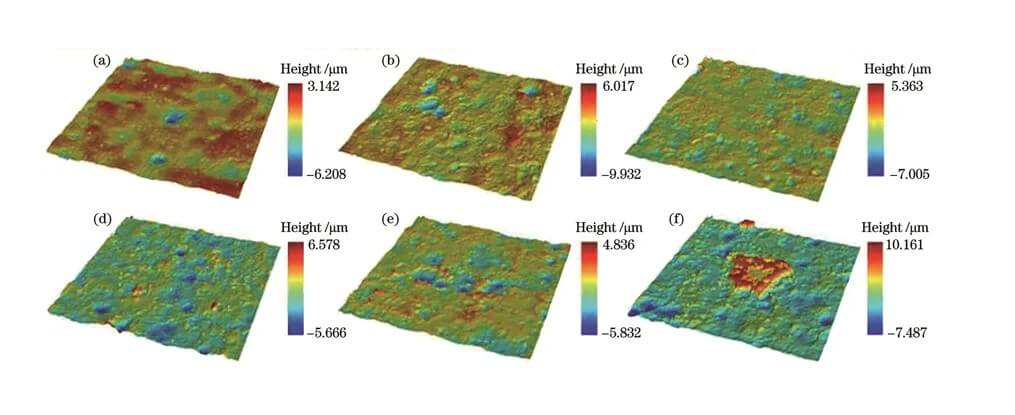
.
Surface changes of anodized film after laser removal
.
Summary:
When choosing the method of removing anodize aluminum, it should be based on the specific needs (such as the removal area, precision requirements, cost budget, etc.) to consider comprehensively and adopt the most suitable method to achieve the best results.
5.Can vinegar removing anodize layer? Question Answer
(1) The nature of vinegar:
Vinegar is a weak acid, the main component is acetic acid. Acetic acid is corrosive and can react chemically with a variety of metal oxides.
(2) Properties of anodic oxide layer:
The anodic oxide layer is usually a dense oxide film generated electrochemically on the metal surface to enhance the corrosion resistance, wear resistance and aesthetics of the metal. The main component of this oxide film is usually the oxide of the metal.
(3) The effect of vinegar on the anodic oxide layer:
Due to the weak acidity of vinegar, it can theoretically react with the metal oxides in the anodic oxide layer, thus dissolving or weakening the oxide film to a certain extent. However, this effect is usually more limited because the anodized layer is more dense and stable.
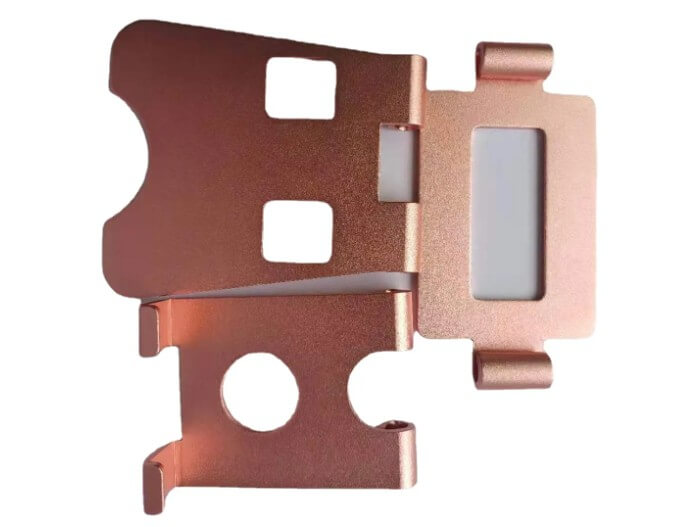
(4) Practical considerations:
Although vinegar can affect the anodic oxide layer to a certain extent, it is not common to removing anodize layer with vinegar in practice. Because of the weak acidity of vinegar, it takes a long time to see a noticeable effect, and it may not be completely removed.
(5) Other removal methods:
If you need to removing anodize layer, the common methods include mechanical grinding, chemical etching (such as the use of strong acid), etc. These methods are usually more effective than the use of vinegar, but the operation is also more complex and has a certain degree of danger.
6.Summary
By analyzing and comparing chemical immersion, electrolytic polishing, mechanical polishing, laser removal and ultrasonic cleaning, we can see that each method has its own unique advantages and limitations. Choosing the appropriate method for removing anodize requires comprehensive consideration of factors such as material properties, cost, efficiency and environmental impact. It is hoped that the discussion in this paper can provide valuable references for related industry practitioners in practical operation.