CNC machining: advantages and techniques for small batch machining
In the manufacturing industry, things have evolved to a point that favors flexibility and efficiency. Low-volume CNC machining involves producing products or components on a small scale, typically between 10-1000. From CNC turning and milling to low-volume parts and prototypes, Prime Machining has your outsourcing needs covered.
Low-volume CNC machining has become a key strategy that offers countless benefits and uses specialized techniques to meet the needs of different industries. Here’s an exploration of the benefits and techniques of low-volume CNC machining:
1.Benefits of low-volume CNC machining
1) Cost-effectiveness and rapid profitability
Small-volume production can save costs in materials, setup, and tooling. This is especially beneficial for companies that want to test the market or produce limited quantities. At the same time, due to the shortened time to market brought about by low-volume CNC machining, the cash flow between customers and companies is increased, and the turnover rate of companies is also improved. Products quickly enter the market, drive sales, and enable companies to quickly generate revenue and profits.
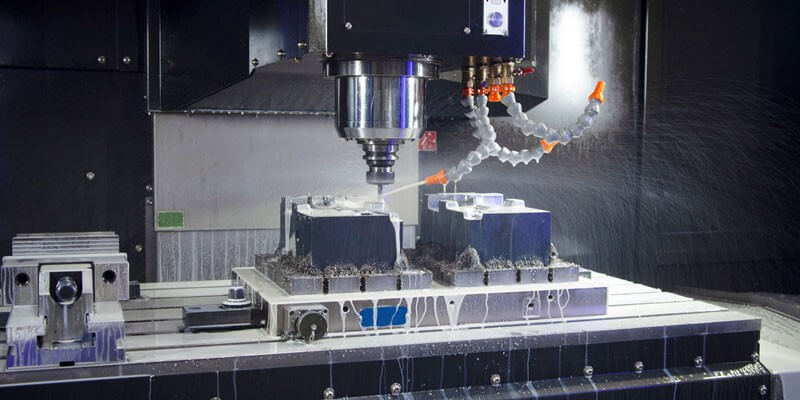
2) Rapid prototyping
Small batches are very suitable for prototyping, which can achieve rapid iteration and modification. Agility in the prototyping stage can accelerate product development.
3) Reduced material waste
Compared with large-scale production, small-volume machining can minimize material waste. This is in line with sustainable development goals and helps to fulfill environmental responsibilities.
4) Flexibility and Customization
Manufacturers can easily accommodate design changes or customization requests when dealing with low-volume products. This flexibility is critical for industries where product specifications may evolve rapidly.
5) Market Testing
Small-volume production allows companies to test the market without having to commit to large-scale production. This mitigates the risks associated with producing large quantities of unproven products.
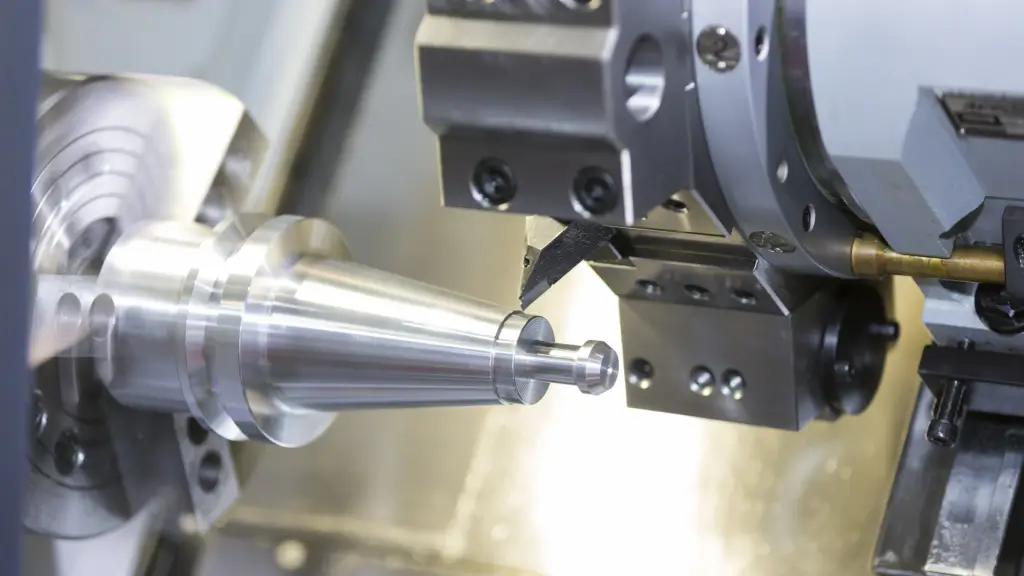
2.Low-volume CNC machining technology
1) Fast setup
An efficient setup procedure is essential. Utilizing modular fixtures and standardized tools allows for quick setup changes, minimizing downtime between batches.
2) Advanced tool path strategies
Implementing advanced tool path strategies, such as high-speed machining and optimized cutting paths, can improve efficiency and reduce machining time.
3) Multi-axis machining
Low-volume production often involves complex geometries. The use of multi-axis machining capabilities allows complex components to be produced in a single setup.
4) Tool management system
Automatic tool changers and integrated tool management systems minimize manual intervention and optimize tool usage, thereby increasing efficiency.
5) Simulation and Validation
Using computer-aided design (CAD) and computer-aided manufacturing (CAM) software to simulate the machining process before actual machining can help identify and correct potential problems.
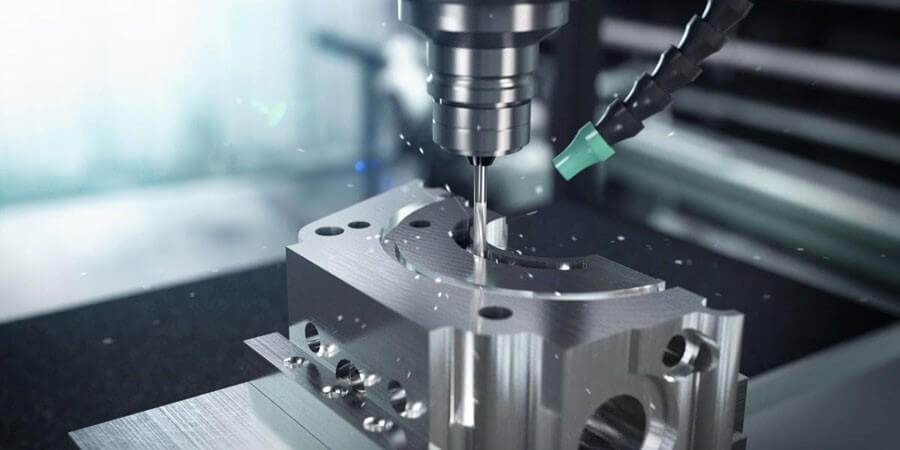
6) Material Selection
Optimal material selection is critical for low-volume CNC machining. Understanding material properties and selecting the right alloy or composite material for the application ensures performance and durability.
7) Quality Control Integration
Integrating quality control measures into the machining process ensures that each component in a small batch meets the required specifications. Inspections and feedback loops in the process help ensure consistency.
8) Collaborative Design and Manufacturing
Encouraging collaboration between the design and manufacturing teams helps to make a seamless transition from prototype to production. This iterative approach ensures that the final product meets the design intent.
9) Avoid Tight Tolerances
Tolerances, especially tight ones, can increase setup time. In addition to setup time, they increase the time for inspection and low-volume CNC machining, as well as the need for specialized production techniques or secondary operations. Therefore, it is best to ensure that tolerances are only tight enough to meet the structural and functional requirements of the design.
In summary, the benefits and technologies of low-volume CNC machining have converged to create a dynamic and responsive manufacturing environment. From cost-effective production to the adoption of advanced machining strategies, low-volume machining enables the industry to meet the challenges of customization, prototyping, and market testing with unparalleled precision and efficiency. As technology continues to advance, the landscape of low-volume CNC machining will continue to evolve, providing greater possibilities for innovation and manufacturing excellence.