Comprehensive Guide to Aerospace CNC Machined Parts: Applications, Materials, Challenges, and Solutions
Aerospace CNC machined parts play a key role in the aerospace industry and help produce critical components for aircraft and spacecraft. Let’s explore the applications, materials and common challenges encountered in aerospace CNC machined parts.
1.Applications of Aerospace CNC Machined Parts
Aerospace CNC machined parts play a key role in shaping the modern landscape of aviation and space exploration. Their applications span critical components that help improve the functionality and performance of aircraft and spacecraft.
Here is an overview of the various applications:
1) Aircraft Structural Components:
CNC machining is widely used to manufacture structural parts that are critical to the integrity and durability of aircraft. This includes fuselage components, wing structures, and complex landing gear components.
2) Engine Components:
Precision CNC machining is integral to the production of complex engine components. From turbine blades to combustion chambers, CNC machining ensures that components are manufactured to withstand the extreme conditions of aircraft engines.
3) Avionics Systems:
Avionics are electronic systems used on aircraft that rely on CNC machining to produce precision parts. This includes control panels, sensors, communications equipment, and other electronic components that are critical to navigation and communication.
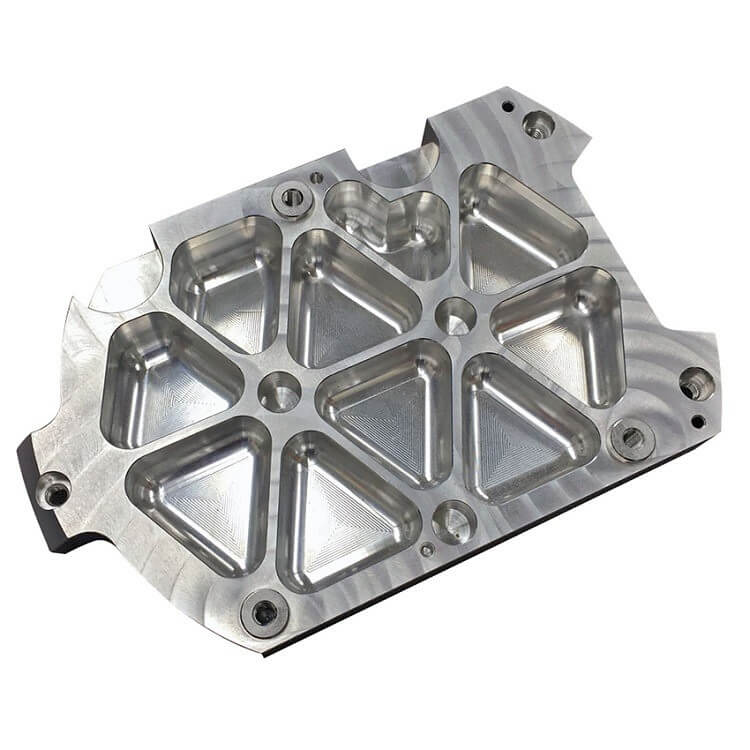
4) Spacecraft Components:
CNC machining is an integral part of the manufacturing of spacecraft components. This covers everything from satellite components to propulsion system elements that support exploration and communications beyond the Earth’s atmosphere.
5) Landing Gear Components:
Landing gear is a critical component for the safe takeoff and landing of aircraft, and its precision components are precisely manufactured using CNC machining to ensure reliability and durability in the challenging aerospace environment.
6) Aircraft Structures and Wings:
CNC machining is used to manufacture aircraft structures, such as wings and tails, as well as airfoils such as wings and propellers. These components are critical to the aerodynamic performance of aircraft.
7) Satellite Components:
CNC machining plays an important role in the production of satellite components, including structural elements, communications systems, and scientific instruments. The accuracy of CNC machining is critical to the successful operation of satellites in orbit.
8) Propulsion System Parts:
CNC machining helps manufacture components essential to propulsion systems, including rocket engines in spacecraft. This includes the manufacture of nozzles, thrust chambers, and other complex components.
The application of CNC machining parts in aerospace highlights its importance in ensuring the structural integrity, functionality, and overall performance of aircraft and spacecraft. The precision and reliability achieved through CNC machining contribute to the safety and success of the aerospace industry.
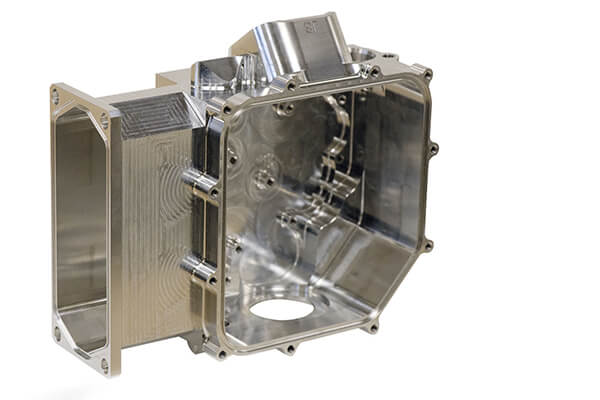
2.Materials used for aerospace CNC machined parts
The aerospace industry requires materials that can withstand extreme conditions while providing the strength, durability, and lightweight properties necessary for aircraft and spacecraft. CNC machining in the aerospace industry relies on a range of specialized materials.
The following are commonly used key materials:
1) Titanium Alloys:
Titanium and its alloys are known for their excellent strength-to-weight ratio and are widely used in aerospace CNC machining. These materials are highly resistant to corrosion and are critical for both aircraft and spacecraft components.
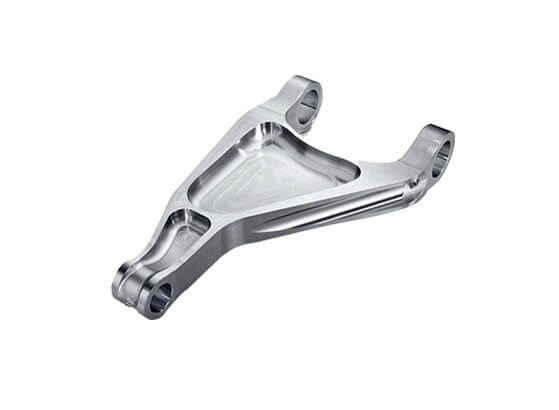
2) Aluminum Alloys:
Aluminum alloys are favored for their light weight and versatility. Aluminum alloy CNC machining is very common in aerospace applications, especially when producing parts where weight is a key factor.
3) Stainless Steel:
Stainless steel is chosen for its corrosion resistance and durability. Although slightly heavier than titanium and aluminum, stainless steel is valuable in aerospace components that require enhanced strength and resistance to environmental factors.
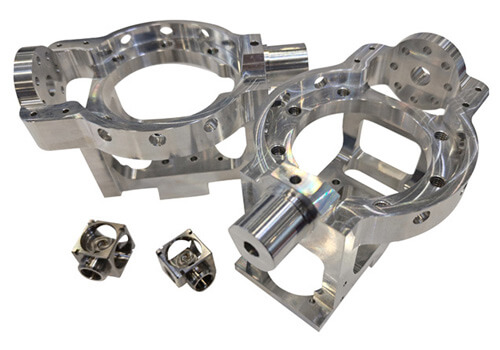
4) High Performance Alloys (Inconel, Monel):
Specialized high performance alloys such as Inconel and Monel are used in CNC machining aerospace components in extreme temperatures and corrosive environments. These alloys have excellent heat and corrosion resistance.
5) Carbon Fiber Reinforced Polymer (CFRP):
CFRP is a composite material consisting of carbon fibers embedded in a polymer matrix. CNC machining is used to mold components to achieve a balance between strength and lightness. CFRP can be used in aircraft structures.
6) Nickel-Based Alloys:
Nickel-based alloys, similar to Inconel, are used in aerospace CNC machining for their high temperature resistance and excellent mechanical properties. These alloys are often used in components exposed to high temperatures, such as jet engines.
7) Copper Alloys:
Certain copper alloys are used in specific aerospace applications where electrical conductivity is a key factor. CNC machining is used to mold copper components for avionics and electrical systems.
8) Plastics and polymers:
Some aerospace components, especially in non-structural and non-critical applications, are made of high-performance plastics and polymers. CNC machining is used to precisely shape these materials.
The selection of the right material for aerospace CNC machined parts depends on the specific requirements of the part, including its function, environmental exposure, and weight considerations. The combination of these materials with advanced CNC machining technology ensures that parts that meet the stringent requirements of the aerospace industry are produced.
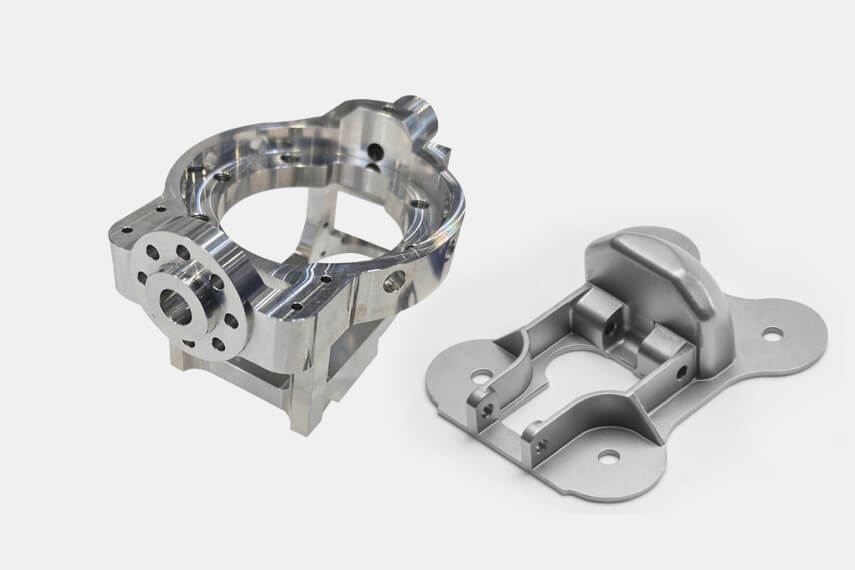
3.Common Challenges and Solutions in Aerospace CNC Machined Parts Manufacturing
Aerospace CNC machining involves complexity and precision, and challenges are inevitable.
The following are common problems faced in the manufacturing process of aerospace CNC machined parts and effective solutions:
1) Tight tolerances:
Challenges: Aerospace CNC machined parts often require extremely tight tolerances, which poses a challenge for precision machining.
Solutions: Utilize advanced CNC machines with high-precision capabilities. Regular maintenance and calibration are essential to maintain accuracy. Implement in-process checks to ensure that tolerances are always met.
2) Material Complexity:
Challenges: A variety of specialized materials are used, each with unique processing characteristics.
Solution: Use cutting tools and machining strategies tailored for each material type. Work closely with material experts to optimize cutting parameters and tool selection based on material properties.
3) Complex Geometries:
Challenge: Complex part geometries need to be machined.
Solution: Implement multi-axis CNC machining to machine parts from multiple angles. This allows for machining of complex contours and intricate features in a single setup, increasing efficiency and accuracy.
4) Heat Generation:
Challenge: Excessive heat generated during machining can affect material properties.
Solution: Optimize cutting speeds to effectively control heat generation. Use high-performance tool coatings and use appropriate coolants to dissipate heat. Continuously monitor machining parameters to help prevent overheating.
5) Quality Assurance:
Challenge: Ensure the highest quality standards for aerospace CNC machined parts.
Solution: Implement a rigorous quality control process. Perform inspections at multiple stages of production, including in-process inspections and final quality inspections. Utilize advanced metrology tools for precise measurements.
6) Tool Wear and Breakage:
Challenge: Tools can wear or break due to the demanding nature of aerospace materials.
Solution: Implement a proactive tool maintenance program. Regularly inspect tools for signs of wear and replace before they reach critical failure points. Use high-quality tool materials and coatings to extend tool life.
7) Chip Control:
Challenge: Manage chips generated during machining, especially in materials prone to chip formation.
Solution: Optimize cutting parameters to control chip formation. Implement effective chip evacuation systems to prevent chip accumulation. Select cutting tools designed for improved chip control.
8) Material Compatibility:
Challenge: Some materials may exhibit challenging machining behaviors, such as work hardening or thermal sensitivity.
Solution: Select cutting tools designed for challenging materials. Adjust machining parameters to mitigate issues such as work hardening. Work with material experts to understand material behavior and optimize machining strategies.
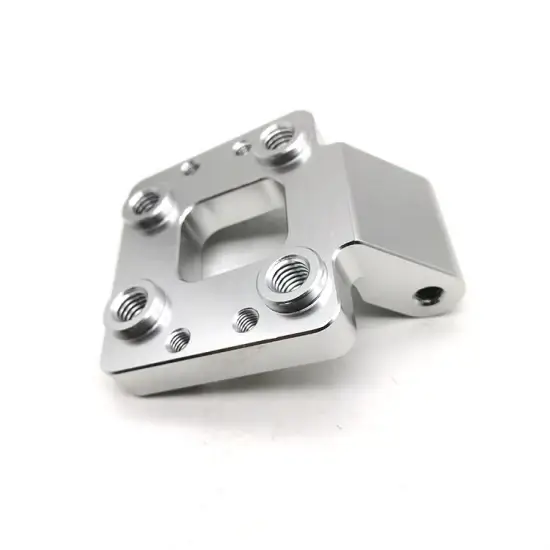
4.Summary
Addressing these challenges in aerospace CNC machining requires a holistic approach that combines advanced technology, expertise, and continuous process improvement. The integration of innovative solutions ensures the continued production of high-quality aerospace CNC machined parts.
Whether you are an aerospace engineer or a worker in other industries, Xavier can provide you with CNC machining services. Please upload your aerospace CNC machined parts project files immediately and we can turn your project into reality.