spot welding:An important welding process
Welding process is a process that has been around for a long time and still plays a role today. There are many types of welding, and the type of project usually determines the type of welding adopted by the manufacturer. One of the very important welding processes is spot welding.
So, what is spot welding? How to spot weld? What are the three elements of spot welding? What are the advantages and disadvantages of this welding process? What are the types of spot welding? What are the welding challenges of different materials and how to deal with them? If you have these questions, please continue reading, we will provide answers to these questions and other important information you need to know about spot welding.
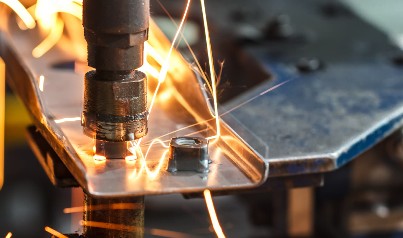
1.What is spot welding
Spot welding is a process that uses welding rods to melt metal parts at high temperatures through arcs to form temporary metal fusion joints at the bevel positions of the welds that need to be connected.spot welding:An important welding process
Spot welding helps to simplify the welding process and its main purpose is to fix the workpiece, maintain gaps, reduce stress, align according to drawings, guide the welder and control deformation. The technology is applied in the work through bridging, gap filling and standard methods.
It seems that the spot welding process is not important in determining the qualification of the work, but in fact it determines the defects, quality, qualification, and acceptance of the work in the final stage. How to spot weld accurately? This is also a difficult task in the welding process.
2.How to spot weld
In spot welding,spot welding:http://spot welding:An important welding process copper alloy electrodes are placed on both sides of the metal sheets to be welded, and current flows between them. Heat is then generated and the metal melts at the contact point, while the pressure from the electrode squeezes the molten metal to form a weld.
The entire welding process of spot welding includes the formation of technical drawings, spot welding procedures, welding execution, final inspection and work acceptance. The specific welding process is as follows:
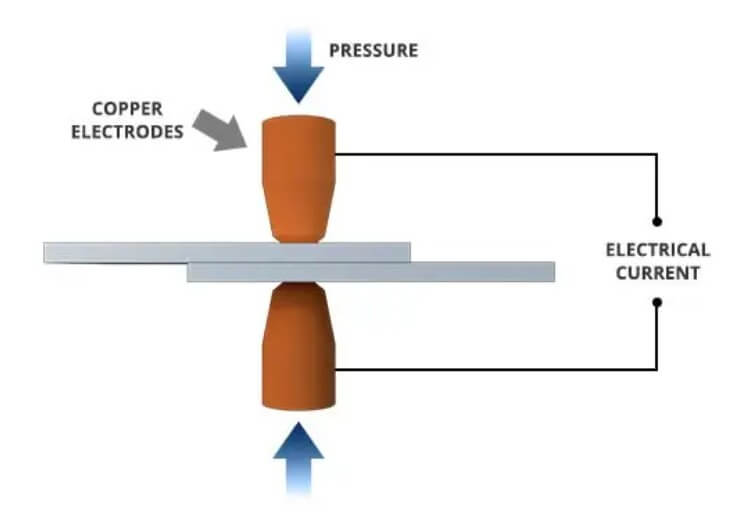
(1) Feed the workpiece joint between the upper and lower electrodes of the spot welding machine and clamp it;
(2) Turn on the power to heat the contact surface of the two workpieces, melt locally, and form a molten core;
(3) After the power is turned off, maintain the pressure so that the molten core cools and solidifies under the action of pressure to form a weld:
(4) Remove the pressure and remove the workpiece.
3.The three elements of spot welding
The three elements of the spot welding process include: current size, welding time and pressure size.
(1) Current size refers to the current intensity passing through the workpiece during welding. It directly affects the temperature and melting morphology of the welding area, and also has an important impact on the performance of the weld. Generally speaking, too small a current will result in insufficient melting, while too large a current may result in excessive melting.
(2) Welding time refers to the heating time, that is, the time for the current to flow through the welding part. Too short a time will result in poor weld quality, while too long a time will cause the area to over-melt and reduce the weld strength.
(3) Pressure refers to the force applied to the welding area. It also has a great impact on the weld morphology and quality. Too small a pressure will result in a weak weld, while too large a pressure will damage the metal surface.
4.Types of spot welding
The different forms of spot welding process depend on how it connects workpieces, fills gaps, becomes part of the final weld, and the technical purpose. The following are the types of spot welding processes:
(1) Standard spot welding
It involves spot welding or tag welding of workpieces before the final assembly of the joint and becomes part of the final weld length. It is the final component of the weld, so welding process assessment and inspection are its main requirements.
(2) Bridge spot welding
The process of performing short-length operations by creating a bridge between two parts of the workpiece so that the final weld bead will not distort the alignment and tolerance of the weldment.
(3) Heat welding
Thermal welding is a post-weld process that fills cavities and eliminates stress concentration points.
(4) Ultrasonic positioning
Using ultrasonic energy to make temporary welds and convert it into heat energy to achieve final alignment.
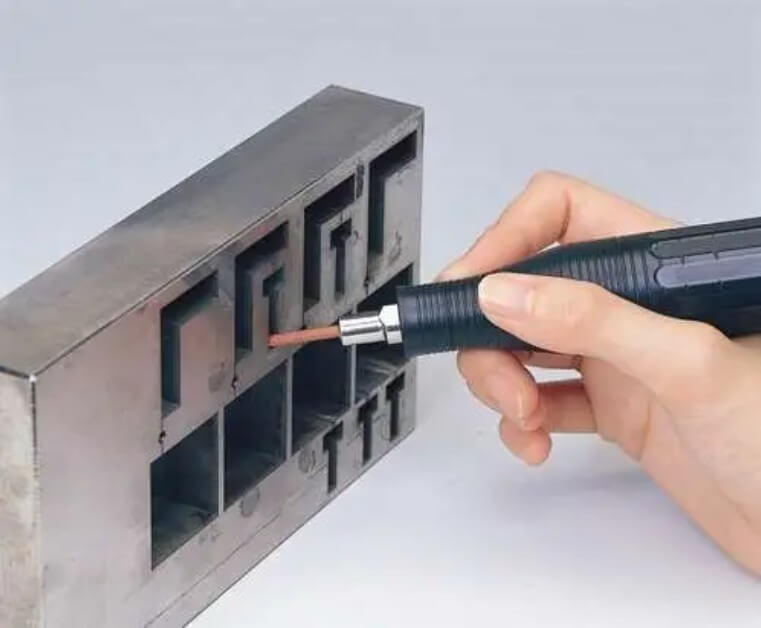
(5) Thermite welding
Temporary welding is performed by reacting magnesium powder and aluminum powder to release heat to form a temporary weld for alignment.
5.Uses of spot welding process
(1) Spot welding is often used in the production and manufacturing of automobiles and electric vehicles. A car body panel often has more than 1,000 spot welds.
(2) Resistance spot welding is also common in the aerospace, railway, manufacturing, electronics and construction industries. Most spot welding work is done by robots in large industrial environments.
(3) Manual spot welding is popular with engineers because it can produce complex shapes with much less work than TIG or MIG welding methods.
6.Advantages and Disadvantages of Spot Welding Process
Advantages of Spot Welding
- It is relatively simple to operate, easy to complete, fast and efficient.
- It has a wide range of uses and can be used on any conductive metal.
- This type of welding allows manufacturers to test their designs before making permanent connections.
- It is cheap, and manufacturers can use non-consumable welding wire instead of expensive filler materials in the process.
- The welded parts can still be moved even without re-welding.
- Spot welding helps to fix parts that are difficult to stabilize by hand or with work clamps.
- Spot welding produces strong, durable welds.
- The process can be automated, making it easy to use in large-scale production.
Disadvantages of Spot Welding
- This type of weld is usually weak and does not last long.
- Both parts must be able to reach the required heat, which is difficult to weld on large parts or areas close to the edges of parts.
- If only filler wire is used, the welding cost can be high. This is especially true when there is no scrap wire
- The spot welding process requires high concentration to prevent accidentally connecting the wrong parts.
- Since the voltage used is extremely small (1-20V), any fluctuation will affect the quality of the weld.
- Spot welding affects the chemical and physical characteristics of the melted metal and may reduce the corrosion resistance of stainless steel, aluminum and other metals.
- Spot welding is not suitable for welding extremely thin or thick metal sheets, and spot welding cannot weld non-conductive materials. for welding extremely thin or thick metal sheets, and spot welding cannot weld non-conductive materials.
7.Challenges and solutions for welding different materials
When the spot welding process keeps the work at a uniform gap, different challenges arise. After the spot welding is completed, the weld reaches room temperature very quickly, and for carbon steel, the microstructure becomes martensite.
This welding process becomes too difficult to break when a small force is applied without post-weld heat treatment of spot welding. Therefore, the metal processing industry needs to solve such problems. One solution is to shot peen the weld bead, which causes stress distribution.Therefore, carbon steel does not face challenges when properly treated. The low melting temperature may cause interference in its microstructure due to large workpiece sinking and small temperature gradient. Aluminum may have problems during spot welding.
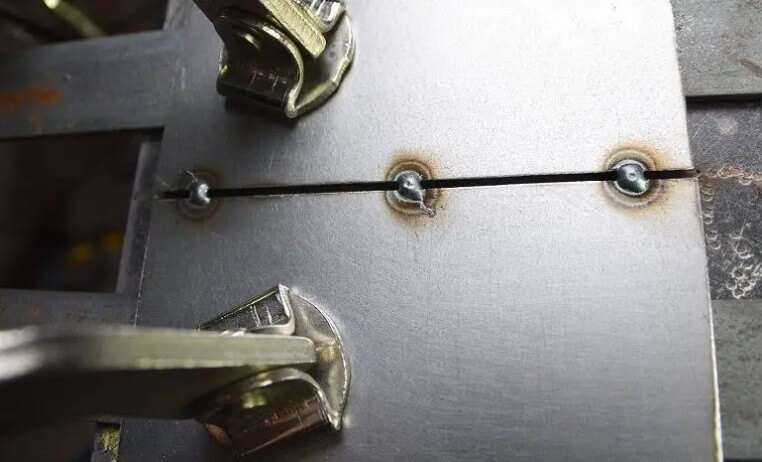
(1) Can you spot weld aluminum?
The answer is yes, but it is difficult. The main reasons are as follows:
•Aluminum alloy has good conductivity and low resistance, so it is difficult to generate resistance heat
Aluminum alloy spot welding is to form a dense molten core by applying electricity and pressure to the two aluminum plates in contact with each other through electrodes. According to Joule’s law, the total heat in the welding area Q=I2Rt. The size of R directly determines the amount of heat generated. Aluminum alloy is a good conductor. A large part of the heat generated locally will be lost. It is difficult to gather enough energy locally.
•Solution:
In order to increase the contact resistance, it is necessary to properly retain the surface oxide film and the appropriate size of the electrode contact surface. Only in this way can the maximum resistance heat be formed and a weld nugget be generated.
•Aluminum alloy has fast thermal conductivity, which makes it difficult to form a weld nugget
Resistance heat Q=I2Rt. According to this theory, an increase in t (time) can lead to an increase in Q, but the heat dissipation is fast. The overall result is that an increase in spot welding time will lead to a decrease in energy.
•Solution:
Therefore, the aluminum alloy spot welding equipment requires the pressurization system of the spot welding equipment to move as fast as possible. In order to achieve this goal, the equipment generally adopts a thin film air cylinder system for the pressurization system, which can complete the pressurization and welding process in a very short time.
•Aluminum alloy spot welding requires high energy
Aluminum alloy spot welding equipment requires extremely high energy. If a thyristor welding power supply is used, the energy loss of the transformer will be very large.
•Solution:
Therefore, this welding process requires the aluminum alloy spot welding equipment to use a medium frequency, inverter welding power supply to achieve a higher energy conversion.
•Weld core is prone to cracks
After the power is turned off, the molten core begins to cool. The shrinkage speed of the aluminum alloy weld core is fast, which is easy to cause defects such as shrinkage holes and cracks.
•Solution:
After spot welding, heat treatment is performed. One solution is to shot peen the weld to cause stress distribution.
(2) Can you spot weld stainless steel?
The answer is yes, but you need to have certain spot welding technology.
For stainless steel, its microstructure is crucial because it will affect the weld. Sudden cooling may deform the body, but the preheating effect prevents temperature gradients between the tack weld and the workpiece. Thus, proper preheating of the weld joint and groove space allows uniform spot welding of stainless steel.
(3) Can you spot weld galvanized steel?
The answer is yes. However, you must be careful because the zinc in this steel is toxic when heated.
The outer surface of this steel has a zinc coating that can react with the welding material and cause the tack weld to crack. Therefore, the zinc coating must be removed before spot welding. Grinding can remove the zinc layer and make the bare metal surface visible so that it can fuse with the metal material. It is also important to weld the complete zinc removal surface and the bare metal surface. Otherwise, the zinc inclusions will destroy the chemical properties of the weld metal.
8.Conclusion
The welding process plays an important role in the manufacturing industry. The spot welding process helps to temporarily fix metal parts together. It helps manufacturers and welders ensure that the parts have the correct orientation and joint gap. The type of filler material used and the number of spot welds determine the strength of the spot welding process.