Common Challenges in Stainless Steel CNC Machining
Stainless steel is a popular material across a variety of industries due to its durability, corrosion resistance, and aesthetics. However, machining stainless steel can present some challenges that require careful consideration and expertise.
In this article, we will explore some of these issues with stainless steel CNC machining and provide recommendations for addressing them.
1.High Work Hardening Rate
One of the main challenges with CNC machining stainless steel is its high work hardening rate. When the cutting tool comes into contact with the material, heat is generated, causing the stainless steel to harden. This can lead to increased tool wear, reduced cutting speeds, and a poor surface finish.
To overcome this challenge, it is critical to use the right cutting tools and techniques. It is recommended to use carbide or ceramic cutting tools with high heat resistance and hardness for stainless steel CNC machining. In addition, the use of coolants or lubricants can help dissipate heat and reduce work hardening.
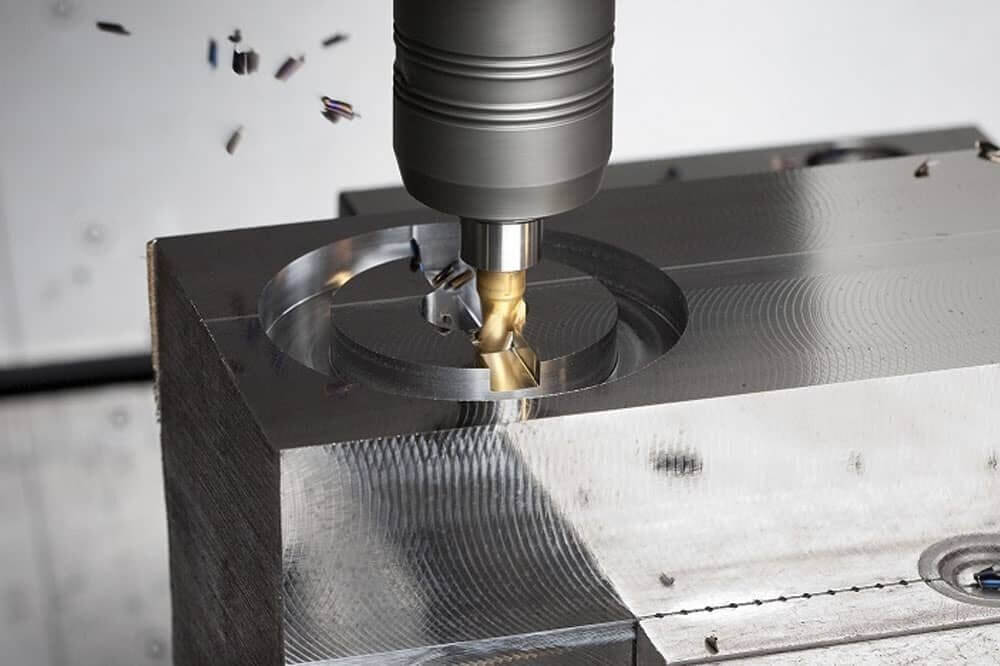
2.Low Thermal Conductivity
Another challenge with stainless steel CNC machining is its low thermal conductivity. Stainless steel has a relatively low ability to conduct heat, which can cause heat to build up during machining. This can result in thermal expansion, deformation, and even tool failure.
To address this challenge, it is important to optimize cutting parameters such as cutting speed, feed rate, and depth of cut. Lower cutting speeds and higher feed rates help minimize heat buildup and increase machining efficiency. Additionally, using coolants or lubricants can help dissipate heat and prevent thermal issues.
3.High Strength and Toughness
Stainless steel is known for its high strength and toughness, which makes it difficult to achieve precision and accurate CNC machining. This is because the hardness of the material can cause excessive tool wear and chipping, resulting in dimensional inaccuracies and poor surface finish.
To overcome this challenge, it is necessary to select cutting tools with high wear resistance and toughness. Additionally, using proper cutting techniques such as reducing cutting forces, using small depths of cut, and using high-speed machining can also help improve accuracy and surface finish.
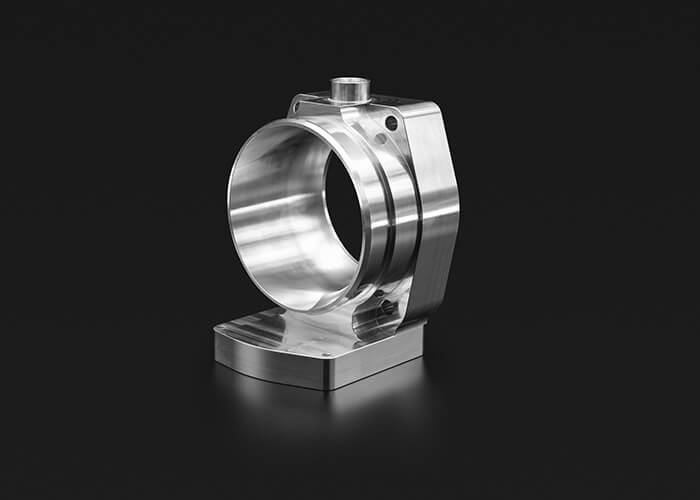
4.Chip Control
Another challenge with stainless steel CNC machining is chip control. Stainless steel tends to produce long, elongated chips that can wrap around the cutting tool, causing chip jams and tool breakage.
To address this challenge, it is important to use chip breakers or chip evacuation techniques. Chip breakers are specially designed features on cutting tools that help break up chips into smaller, more manageable pieces. Additionally, using high-pressure coolant or airflow can help evacuate chips and prevent chip-related issues.
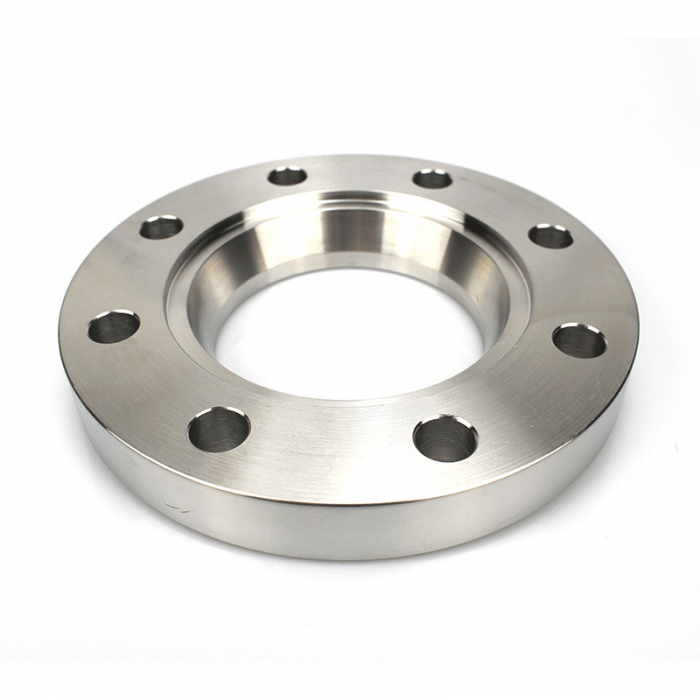
5.Hardness and Work Hardening
Maintaining a good surface finish during CNC machining of stainless steel can be challenging due to the hardness and work hardening properties of stainless steel materials. Achieving a smooth, defect-free surface requires careful selection of cutting tools, appropriate cutting parameters, and a proper toolpath strategy.
Using sharp cutting tools with a small nose radius can help reduce tool marks and improve surface finish. Additionally, employing down milling techniques and optimizing toolpath strategies can minimize vibration and improve surface quality.
In summary, stainless steel CNC machining presents several challenges that require careful consideration and expertise. High work hardening rates, low thermal conductivity, high strength, chip control, and surface finish are some of the common challenges faced when machining stainless steel.
These challenges can be overcome by using the right cutting tools, optimizing cutting parameters, employing chip evacuation techniques, and selecting a proper toolpath strategy. With the proper knowledge and techniques, stainless steel CNC machining can be successfully performed to produce high-quality and precise components.