Stainless steel turned parts: processing challenges and techniques
In modern manufacturing, stainless steel turned parts are widely used in aviation, aerospace, chemical industry and medical equipment due to their excellent corrosion resistance and high strength. However, stainless steel turning faces challenges such as severe tool wear, high cutting temperature and poor surface quality, which requires the tool to have high strength and good cutting performance. Therefore, this article will discuss the challenges of stainless steel turned parts processing, mainly including tool wear and life management, tool selection and optimization, surface treatment technology and application.
1.Analysis of advantages and processing difficulties of stainless steel turned parts
Stainless steel materials have been widely used in aerospace, automobile manufacturing, medical equipment and other fields due to their excellent corrosion resistance and mechanical properties. However, the high hardness, high toughness and poor thermal conductivity of stainless steel make it face many challenges in the turning process, such as severe tool wear and low processing efficiency.
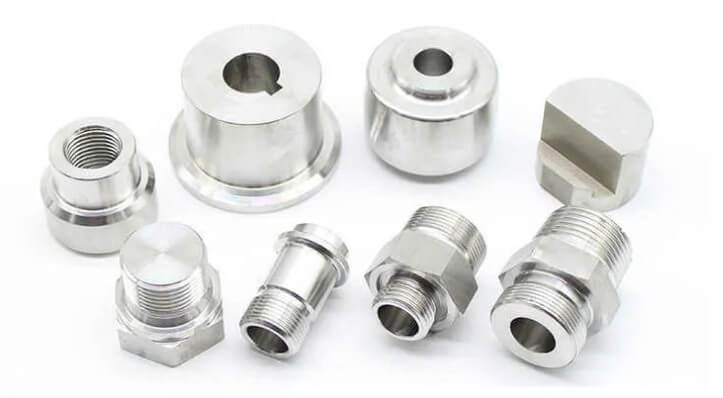
(1) Material properties
The advantages of stainless steel turned parts are mainly reflected in the following aspects:
1) Corrosion resistance:
Stainless steel contains chromium, which can form a dense oxide film on the surface to prevent the invasion of corrosive media. This allows stainless steel turned parts to maintain stable performance in harsh environments.
2) High temperature resistance:
Stainless steel materials can maintain stable mechanical properties in high temperature environments and are not prone to oxidation and deformation. This allows stainless steel turned parts to continue to work normally under high temperature conditions.
3) High strength:
Stainless steel materials have high strength and hardness and can withstand large loads and impacts. This allows stainless steel turned parts to maintain stable performance under heavy load conditions.
4) Good machinability:
Although stainless steel materials are difficult to process, high-precision and high-efficiency processing can be achieved by selecting appropriate tools and processing techniques.
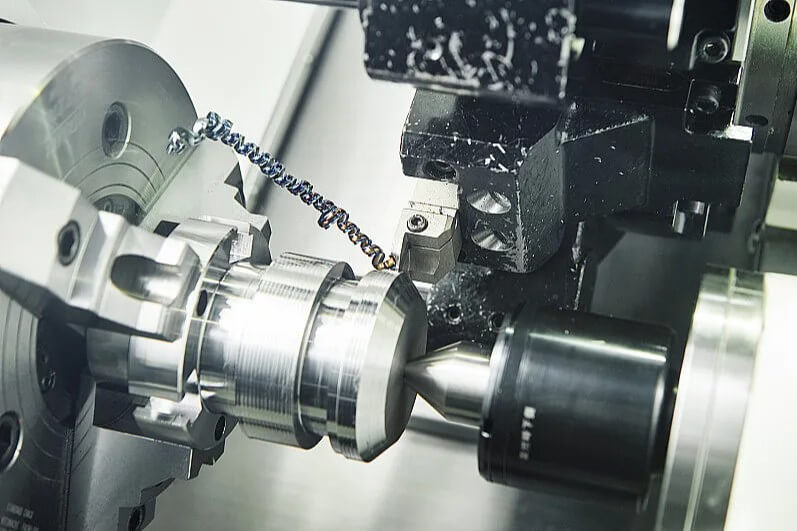
(2) Machining difficulties
The main difficulties in stainless steel turning include:
1) Severe tool wear:
Due to the high hardness and high toughness of stainless steel, the tool is prone to severe wear during cutting, affecting tool life and processing efficiency.
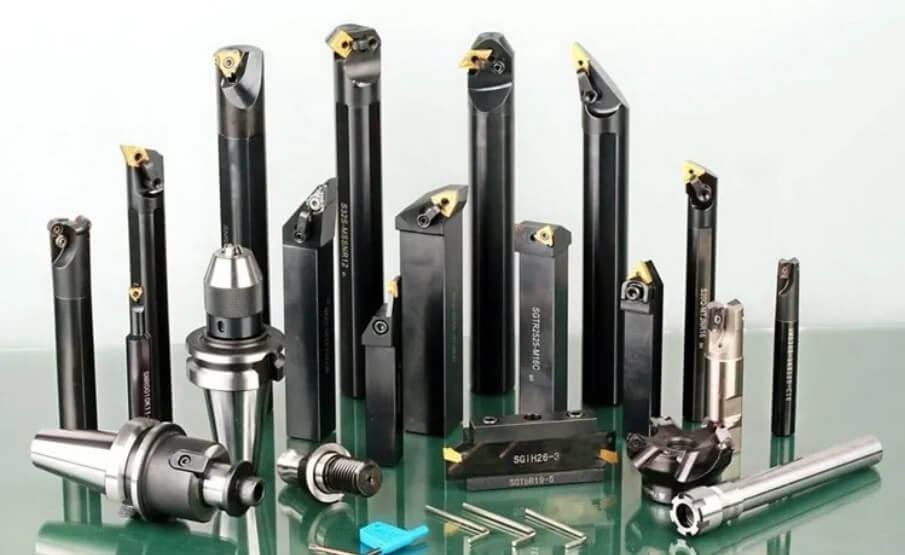
2) High cutting temperature:
Poor thermal conductivity causes the large amount of heat generated during cutting to be unable to be dissipated in time, and the high cutting temperature further exacerbates tool wear.
3) Poor surface quality:
Stainless steel materials are prone to work hardening, and chips are easy to adhere to the tool to form “tool tumors”, affecting the surface quality.
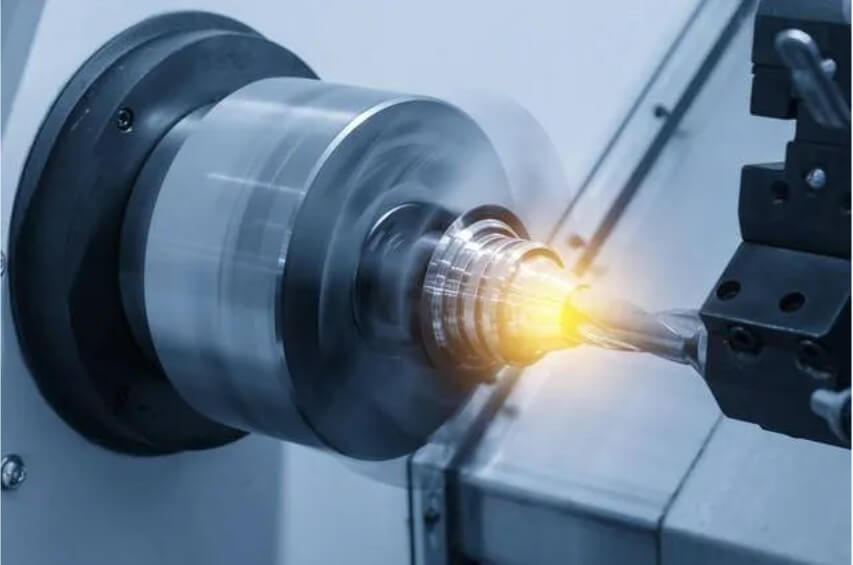
2.Tool wear and life management for stainless steel turning
Based on the above-mentioned processing difficulties, the following are some suggestions for extending tool life:
(1) Tool wear mechanism
During stainless steel turning, the main causes of tool wear include mechanical wear, thermal wear and chemical wear. Mechanical wear is the loss of tool material due to friction between the tool and the workpiece. Thermal wear is the softening or oxidation of tool material due to the high temperature generated during cutting. Chemical wear is the loss of tool material due to chemical reactions between the tool and the workpiece material.
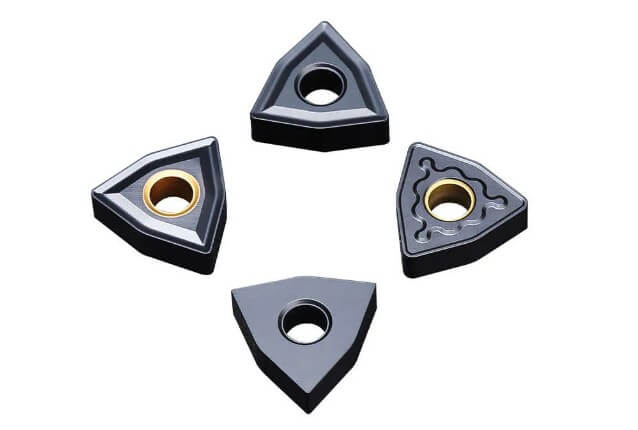
(2) Tool life extension strategy
1) Select appropriate tool material and geometric parameters:
According to the characteristics of stainless steel materials, select tool materials with good wear resistance and high hardness, such as cemented carbide, ceramics and cubic boron nitride. At the same time, reasonably design the geometric parameters of the tool to improve the cutting performance and durability of the tool.
2) Optimize cutting process parameters:
Reasonably select cutting speed, feed rate and cutting depth to reduce tool wear. For example, selecting a lower cutting speed and a larger feed rate can reduce tool wear and increase tool life.
3) Reasonable use of cutting fluid:
Select appropriate cutting fluid and reasonably control the flow and pressure of the cutting fluid to improve cooling and lubrication effects and reduce tool wear. For example, using oil-based cutting fluid can improve lubrication effect and reduce tool wear; using water-based cutting fluid can improve cooling effect and reduce cutting heat.
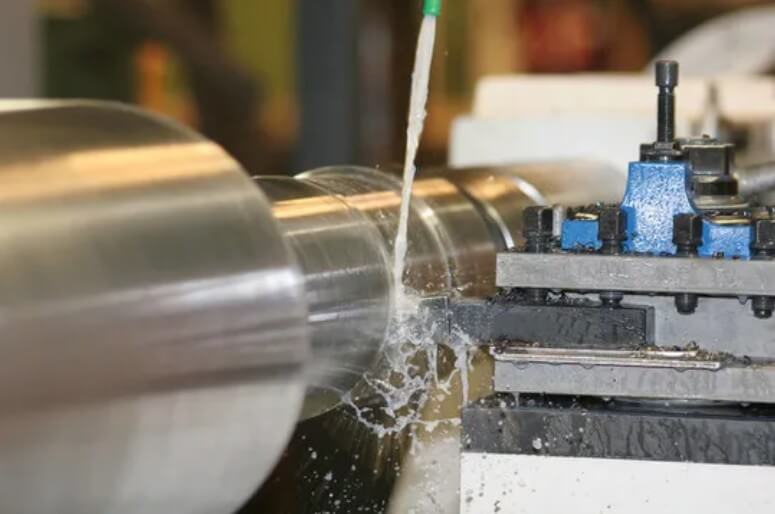
4) Regular inspection and sharpening of tools:
Regularly check the wear of the tool and sharpen it in time to keep the tool sharp and improve processing efficiency and quality. For example, when the blade wear of the tool is 0.2-0.3mm, the tool needs to be removed and sharpened. When sharpening, choose an alumina grinding wheel and re-grind according to the geometric angle of the tool.
3.Tool selection and optimization for stainless steel turning
Selecting appropriate tool materials and optimizing tool geometric parameters are the key to ensuring the processing efficiency and quality of stainless steel turned parts. The following will discuss these two aspects in detail:
(1) Tool material selection
The selection of tool material is directly related to the durability and processing efficiency of the tool. The ideal tool material for cutting stainless steel should have high hardness, good wear resistance and anti-adhesion.
1) Carbide tools:
Carbide tools are widely used in stainless steel turning due to their high hardness and good wear resistance. Commonly used carbide grades include YG6, YG6X, YT5, etc., which are suitable for rough machining; while YT15, YT30, YW, YW2 and other grades are suitable for semi-finishing and finishing. It is worth noting that when machining austenitic stainless steel such as 1Gr18Ni9Ti, YT-type carbide should be avoided, because the titanium element in stainless steel will react with the titanium in YT-type carbide, resulting in increased tool wear.
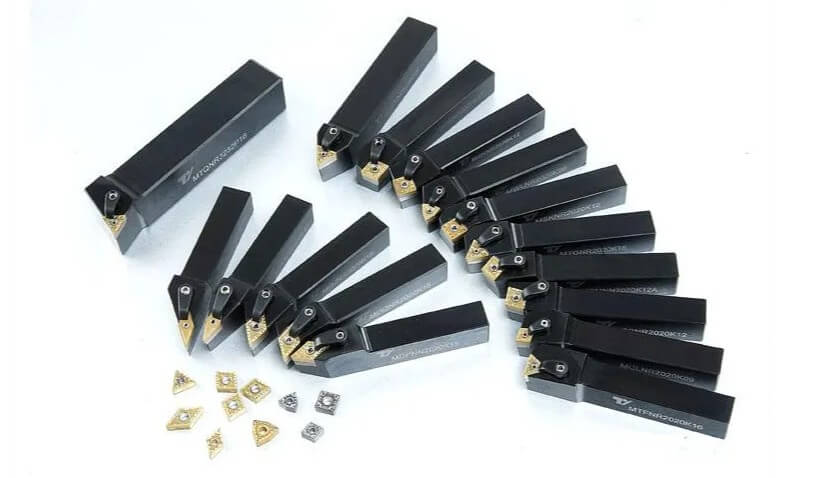
2) Ceramic tools:
Ceramic tools have extremely high hardness and wear resistance and are suitable for high-speed cutting of stainless steel. Ceramic tools can still maintain good cutting performance at high temperatures and are suitable for machining high-hardness stainless steel materials.
3) Coated tools:
Cubic boron nitride (CBN) tools have extremely high hardness and thermal stability, and are suitable for high-precision and high-efficiency turning. CBN tools can maintain high hardness at high temperatures and are suitable for processing high-hardness materials.
(2) Tool geometry optimization
The reasonable selection of tool geometry has an important influence on cutting force, cutting heat, tool durability and processing surface quality.
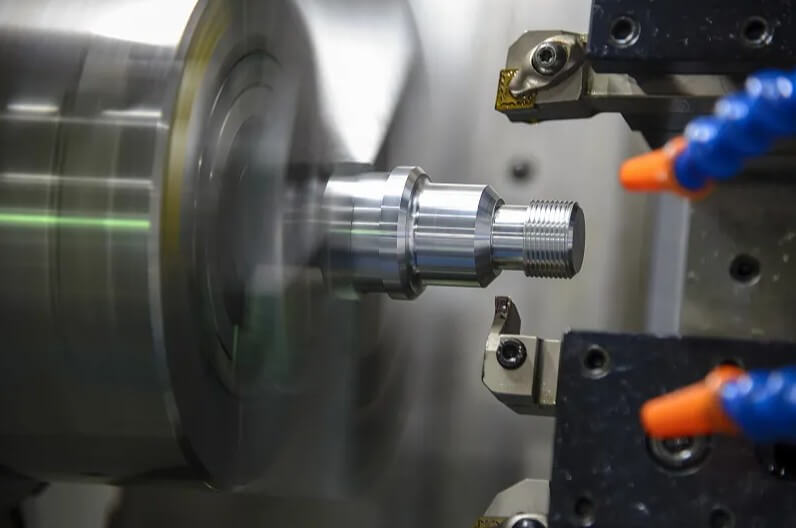
1) Rake angle:
The rake angle determines the sharpness of the tool. When turning stainless steel, a smaller rake angle (10°~15°) should be selected for rough machining to enhance the strength of the tool tip; a larger rake angle (20°~30°) should be selected for fine machining to reduce cutting force and cutting heat.
2) Back angle:
The back angle affects the wear of the tool back face. When the cutting thickness is small, the back angle should be larger, otherwise it should be smaller. Under normal circumstances, the back angle for rough machining is 5°~7°, and the back angle for fine machining is 7°~10°.
3) Main rake angle:
The main rake angle affects the distribution of cutting force and the durability of the tool. When machining stainless steel, the main rake angle is generally selected to be 30°~45°. For workpieces with a larger aspect ratio, the main rake angle can be selected to be 90°.
4) Secondary rake angle:
The secondary rake angle affects the finish of the machined surface. The secondary rake angle is 3°~10° for rough machining and 15°~20° for fine machining.
5) Blade inclination angle:
The blade inclination angle affects the discharge of chips and the strength of the tool. Usually, the blade inclination angle is 0°~5° to ensure smooth discharge of chips.
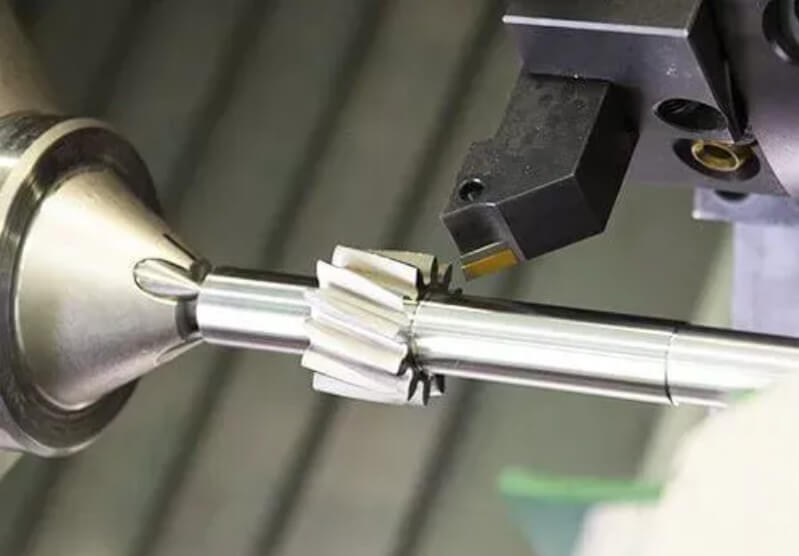
4.Surface treatment technology of stainless steel turned parts
Stainless steel turned parts are widely used in modern industry due to their corrosion resistance and aesthetics. However, the surface after turning often needs further treatment to achieve higher performance and aesthetic requirements. The following are several key technologies for the surface treatment of stainless steel turned parts:
(1) Surface polishing:
Polishing is a common surface treatment method for stainless steel turned parts. It removes small surface defects and burrs through mechanical friction. Polishing can be divided into rough polishing and fine polishing. Rough polishing uses coarse abrasives to quickly remove large surface defects, while fine polishing uses fine abrasives to make the surface smooth like a mirror. Polishing can not only improve the aesthetics, but also improve the wear resistance and corrosion resistance of parts.
(2) Electrolytic polishing technology:
Electrolytic polishing is an electrochemical process that applies an electric current in an electrolyte to preferentially dissolve the microscopic protrusions on the surface of stainless steel, thereby obtaining a highly smooth surface. Compared with mechanical polishing, electrolytic polishing can more effectively reduce surface roughness without changing the dimensional accuracy of the workpiece, and is particularly suitable for workpieces with complex shapes.
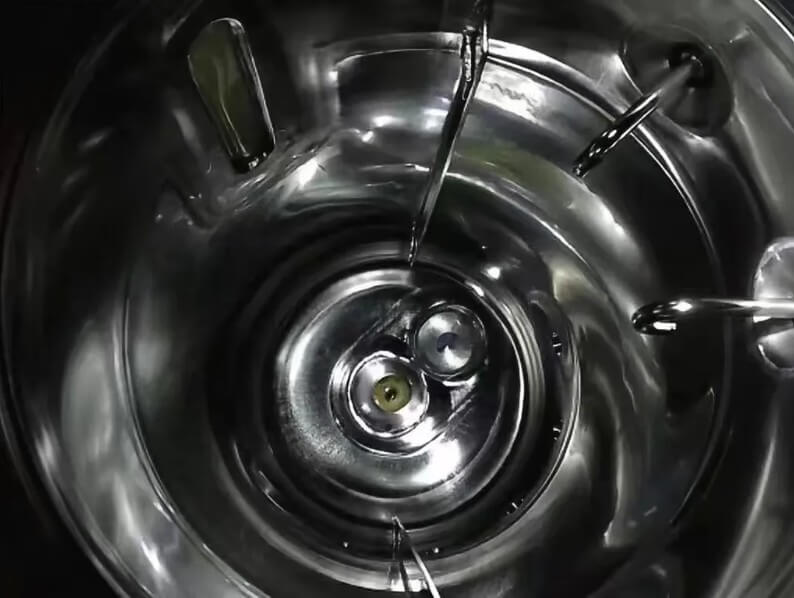
(3) Surface passivation treatment:
Passivation treatment is to form a dense oxide film on the surface of stainless steel by chemical methods to improve its corrosion resistance. It is usually treated with solutions such as nitric acid or chromic acid. After treatment, the corrosion resistance of the stainless steel surface is significantly enhanced, which is suitable for occasions with extremely high corrosion protection requirements, such as medical devices and food processing equipment.
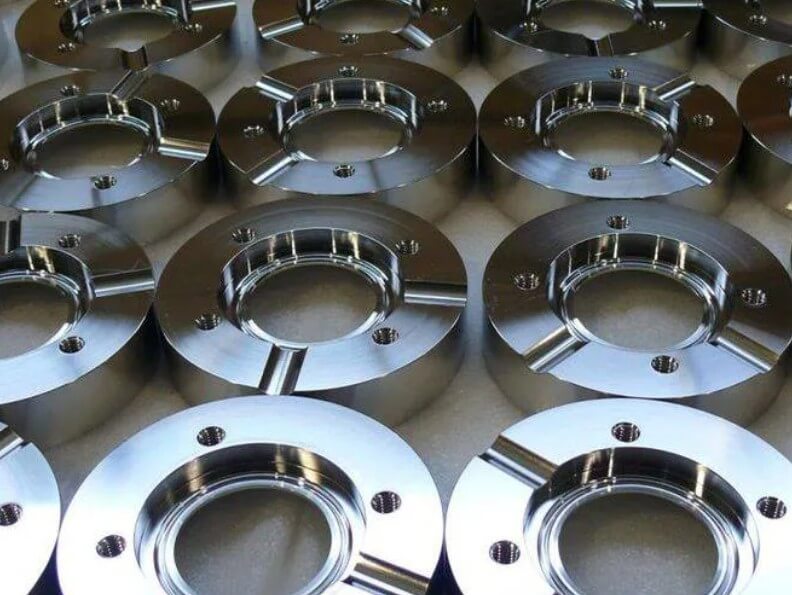
(4) Coating technology:
To meet special needs, one or more layers of coating can be applied to the surface of stainless steel turned parts. Common coating materials include ceramics, titanium nitride, etc. These coatings can not only improve the hardness and wear resistance of the surface, but also increase the resistance to high-temperature oxidation. Coating technology is widely used in the fields of aerospace and automobile manufacturing.
Through the above surface treatment technology, the performance and service life of stainless steel turning parts can be significantly improved to meet the needs of different industrial applications.
5.Application fields of stainless steel turned parts
Stainless steel turned parts are widely used in many industries due to their excellent corrosion resistance, high strength and good surface finish. The following are the main application fields of stainless steel turned parts:
(1) Medical device field:
Stainless steel turned parts are used to manufacture high-precision medical devices such as surgical knife handles, dental tools, artificial joints, etc. These parts need to be antibacterial, corrosion-resistant and highly stable, and stainless steel turned parts can just meet these stringent requirements.
(2) Food processing industry:
In the food processing industry, stainless steel turned parts are used to manufacture key equipment such as food mixers, filling machines, and cutting machines. Stainless steel is easy to clean and meets food hygiene standards, which can ensure the safety of food during processing.
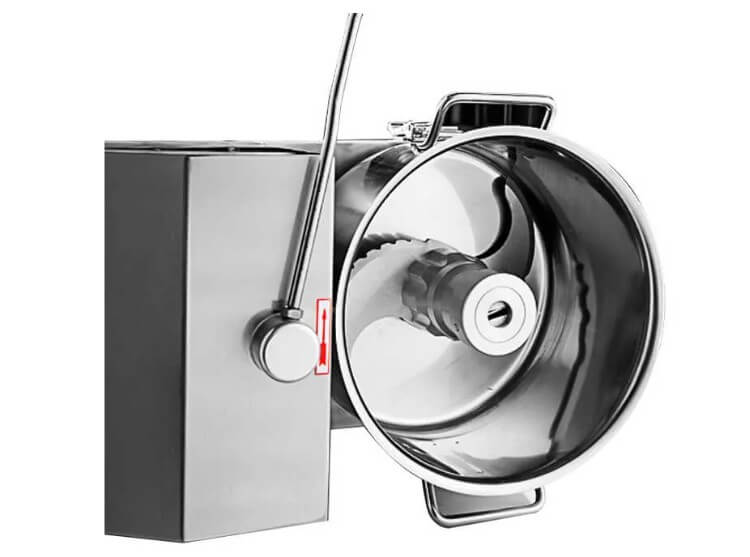
(3) Aerospace:
The aerospace field has extremely high requirements for material performance. Stainless steel turned parts are used to manufacture structural parts of aircraft and rockets. Its light weight and high strength meet the design requirements of aerospace vehicles and ensure flight safety.
(4) Automobile manufacturing:
Stainless steel turned parts are mainly used in automobile manufacturing to produce exhaust pipes, brake system parts, steering systems, etc. These parts work under high temperature and high pressure environments. The high temperature oxidation resistance and corrosion resistance of stainless steel ensure their long-term stable operation.
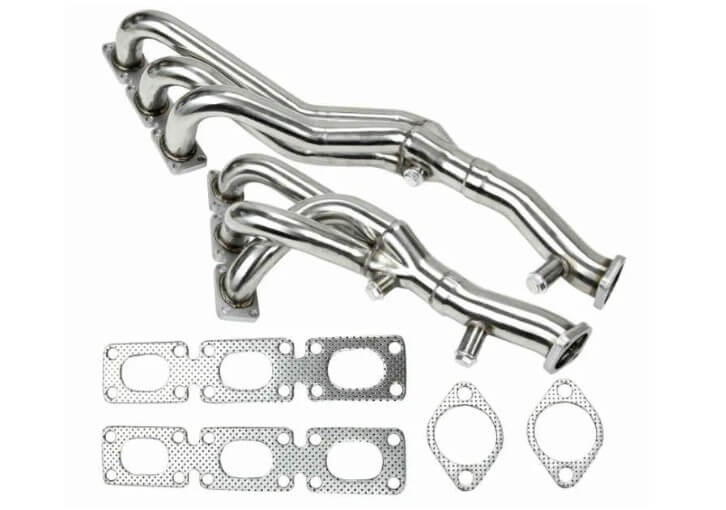
(5) Electronics industry:
Stainless steel turned parts are used in the electronics industry to make precision electronic components, such as connectors, shielding covers, etc. Its excellent conductivity and anti-interference ability ensure the normal operation of electronic equipment.
6.Summary
In summary, mastering the processing skills of high-precision stainless steel turned parts is crucial to improving product quality and production efficiency. By reasonably selecting tools, extending tool life, optimizing cutting parameters, and adopting advanced surface treatment technology, the processing difficulties of stainless steel materials can be effectively overcome, providing high-quality parts for the development of the manufacturing industry.