A Brief Introduction to the Basics of Aluminum Profiles
Many industries use aluminum for different applications due to its lightness, durability, and resistance to rust. To talk about aluminum profiles, it is important to distinguish between anodized profiles and standard profiles.
This difference is very important, and the choice of alloy for aluminum anodizing is crucial to achieve the desired results in different applications.
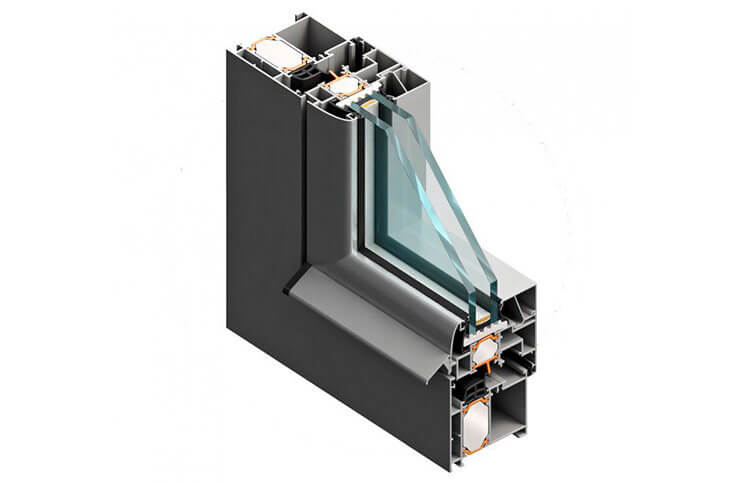
1.Understanding Aluminum Profiles
These are extruded aluminum profiles that are commonly used in different fields such as automotive, construction, aerospace, etc.
These profiles include standard profiles and anodized profiles. Standard aluminum profiles are usually raw or untreated, while anodized profiles are electrochemically treated to improve their characteristics.
The anodizing process involves an electrolytic treatment that increases the thickness of the natural oxide layer on the metal surface. As a result, the process not only provides better appearance, but also significantly improves its corrosion and wear resistance.
This allows them to last longer than standard alternatives. In addition to this, by improving durability, they can last longer than matching products of standard size.
The enhanced surface layer can also be dyed in different colors, which has both aesthetic and functional advantages. Therefore, anodized aluminum profiles are ideal for applications that require a combination of strength, durability, and visual appeal.
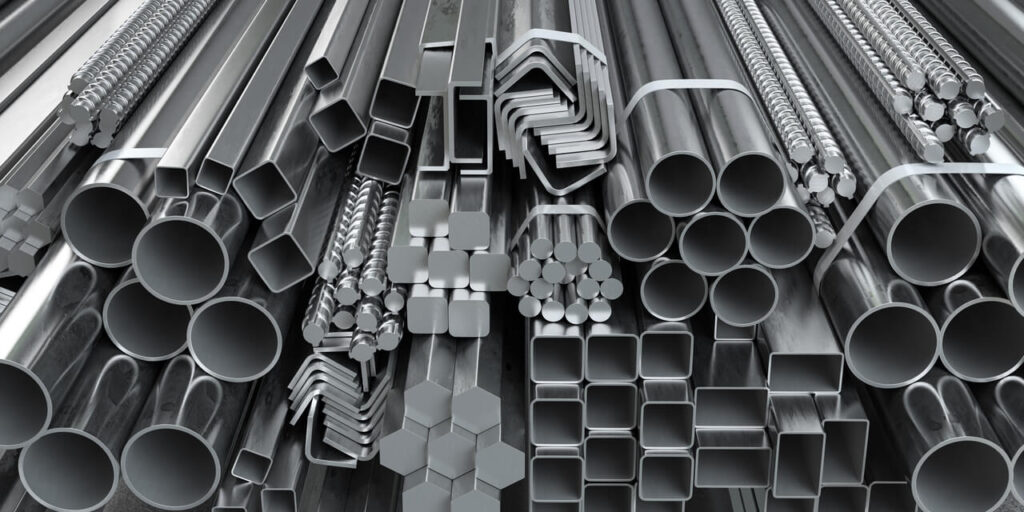
2.Aluminum Anodizing Process
Anodizing is a controlled aluminum oxidation process that is carried out in an electrolytic cell. During the anodizing process, the aluminum profile is immersed in an acidic electrolyte and an electric current is passed through the solution. The aluminum acts as an anode, attracting oxygen ions and forming a thick and stable oxide layer on its surface.
This porous oxide layer can be dyed or sealed, thereby enhancing the aesthetics and protective properties of the aluminum. The oxide layer thickness can be controlled by adjusting the time and conditions of the anodizing process to suit different applications.
Therefore, for decorative purposes, thinner oxide layers are usually used, while thicker oxide layers provide additional protection and are suitable for industrial use.
Due to its higher durability, corrosion resistance and customizable appearance, anodized aluminum is widely used in construction, automotive industry, consumer electronics, etc. The service life of aluminum is extended in this process, which also enhances the visual appeal of aluminum products, making it popular in different industries.
3.Advantages of Anodized Aluminum Profiles
Anodized aluminum profiles have several advantages over standard profiles. For example, they have higher corrosion resistance because the anodized layer allows the profiles to be used outdoors and in harsh conditions.
The aluminum anodizing process creates a protective barrier that limits the reaction between the underlying metal and environmental factors, thus extending the life of the profile.
Secondly, anodized aluminum profiles have enhanced wear resistance. The hard oxide on their surface lasts longer than raw aluminum, reducing the possibility of mechanical damage such as scratches and dents.
This is why this type of profile is suitable for use in high-traffic areas or where longevity is important.
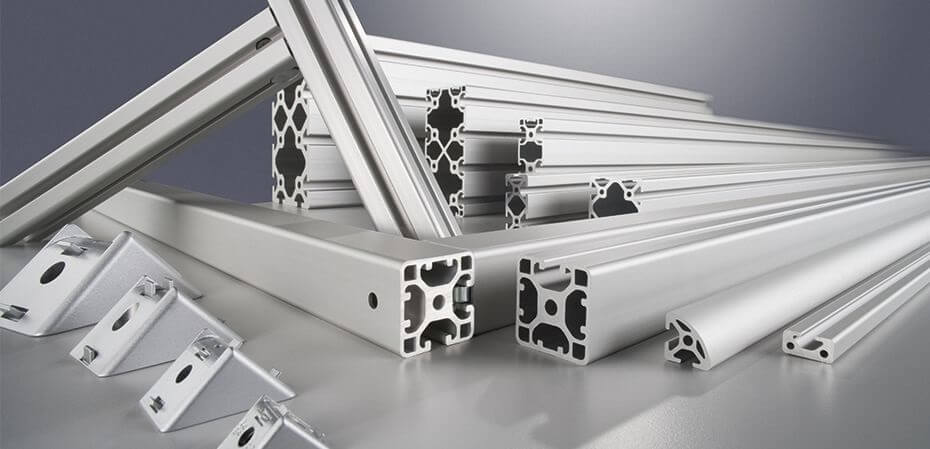
4.The difference between anodized aluminum profiles and standard aluminum profiles
Surface properties and performance characteristics distinguish anodized aluminum profiles from standard aluminum profiles. Standard aluminum is untreated and therefore prone to corrosion and wear, so further coatings or processes may be required to extend its life.
In contrast, anodized aluminum profiles have a naturally occurring protective layer that provides better resistance to corrosion and wear. This gives them an advantage over other materials in situations where long-term efficiency and low maintenance are required.
In addition, they can be dyed and sealed, allowing for more aesthetic diversity in design.
5.Choosing the right anodizing alloy
The success of aluminum anodizing depends on the correct choice of alloy. Different mixtures react differently to anodizing, which affects the final appearance and performance of the anodized profile. 6061, 6063, and 7075 are among the alloys used for anodizing.
One of the reliable alloys is 6061, which is a versatile alloy. It is best suited for structural applications that require high strength and corrosion resistance.
However, another alloy that has very good extrudability and surface finish is 6063. This makes it ideal for architectural and decorative purposes.
The most commonly used aluminum alloy in the aviation industry is 7075. It is preferred for military and aerospace applications due to its high strength properties.
Although anodizing is not done as frequently as 6061 or 6063, it can still be anodized to enhance its corrosion resistance and surface hardness.
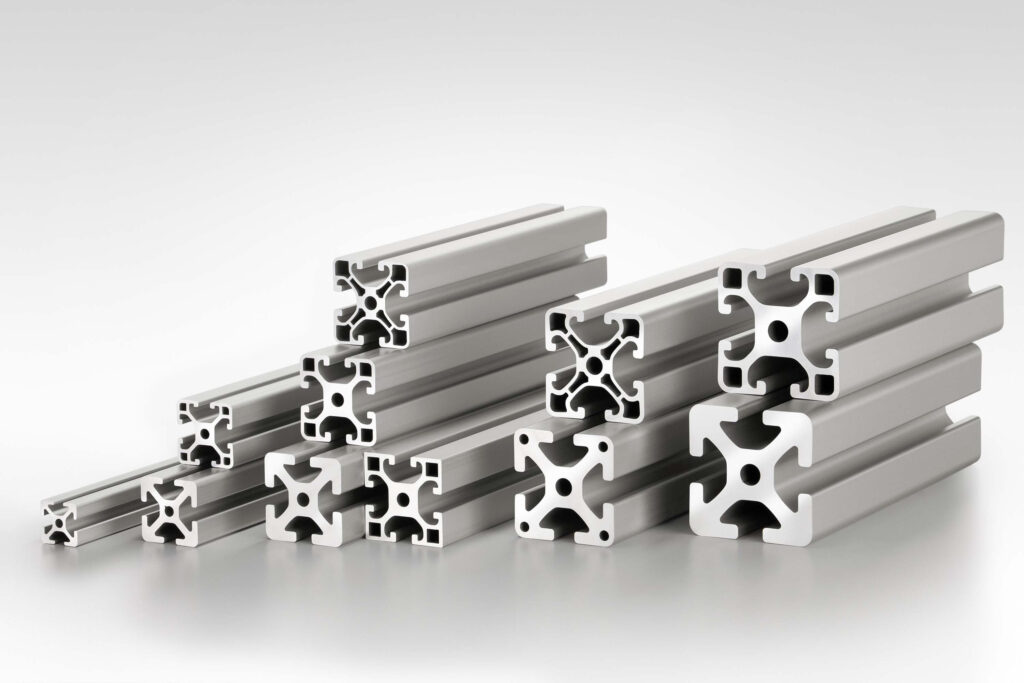
6.Applications of Anodized Aluminum Profiles
Anodized aluminum profiles are used in various fields due to their improved properties. They are widely used as door and window frames as well as curtain walls in the construction industry, where durability and aesthetics are key properties that must be met.
The anodizing process provides a wide range of colors and textures; therefore, architects can realize their design ideas.
Anodized aluminum profiles can also be used in the automotive field for interiors, body panels, and engine components. These parts are resistant to corrosion and wear, so they can withstand the rigors of the interior of the vehicle while maintaining their appearance and functionality.
The aerospace industry is not far behind in the use of anodized aluminum extrusions. This is due to its lightweight properties, ensuring that it can be used in a variety of aircraft components, such as structural parts and even interior accessories.
The protective oxide layer makes these parts reliable no matter what environment they are exposed to.
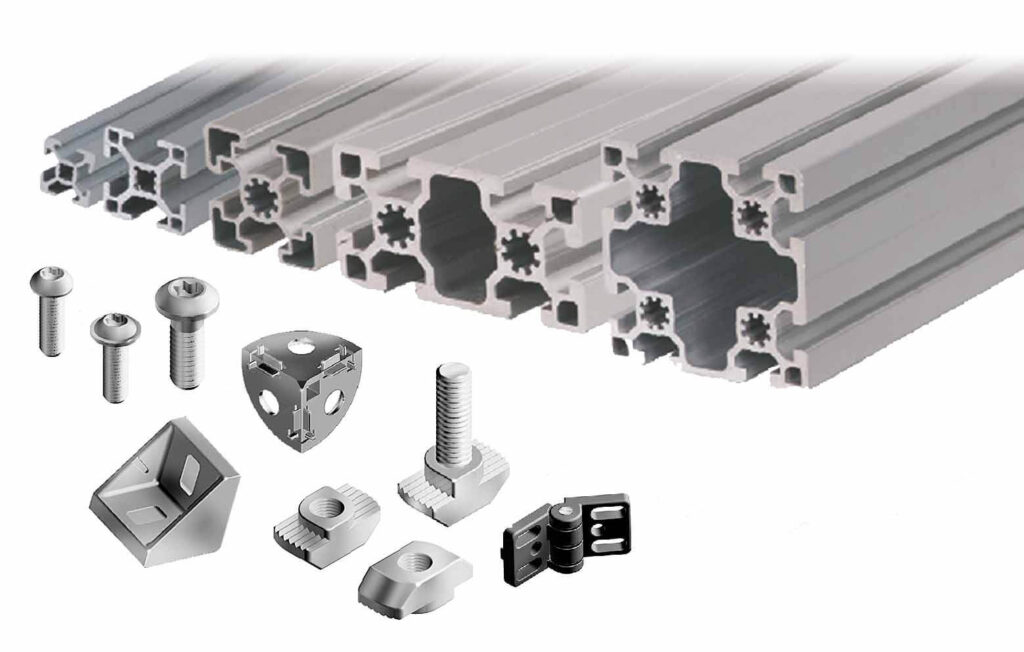
7.Conclusion: Make the Right Choice
Depending on the specific application, you have to choose between anodized and standard aluminum extrusions. Anodized aluminum extrusions are the first choice for projects that require long-term durability, corrosion resistance, and good looks.
At the same time, anodizing improves the natural characteristics of aluminum, extending the life of the extrusion through a protective layer.
On the other hand, for applications that may require additional coatings or treatments to achieve the desired performance, standard aluminum extrusions are sufficient.
Understanding the differences between these two extrusions and choosing the right anodizing alloy can greatly affect the success of your project.
In conclusion, you should decide whether to use anodized extrusions or regular aluminum extrusions based on the needs of your application. Weighing up the benefits of anodized profiles, how they differ from standard profiles, and the alloys suitable for anodizing can guide you in making a decision that guarantees good performance and longevity of the aluminum profile used.