Basic Introduction of Electroless Nickel Plating
Electroless nickel plating is a widely used technology in many industries such as automotive, aerospace, electronics and manufacturing. It is mainly a process that deposits a layer of nickel on a substrate without the aid of an electric current. Compared with traditional electroplating methods, this process has many advantages, such as uniform coating thickness, excellent corrosion resistance, and the ability to coat complex shapes and sizes. In order to ensure the success of electroless nickel plating, there are several key factors that need to be considered, which we will introduce in detail in this article.
Key factors for the success of electroless nickel plating
Choosing an Electroless Nickel Plating Solution
Electroless nickel plating solutions come in different types such as low-phosphorus, medium-phosphorus, and high-phosphorus solutions. Each type has unique properties that make it suitable for specific applications. For example, low-phosphorus solutions are often used for decorative purposes, while high-phosphorus solutions are favored for their excellent corrosion resistance.
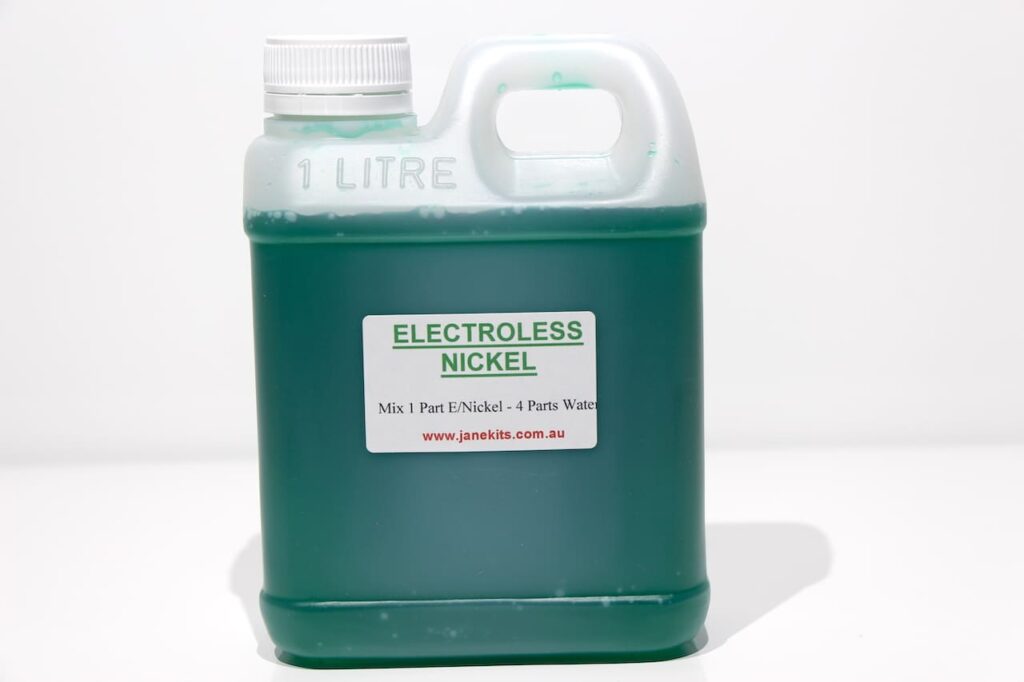
Preparation of the Substrate Before Plating
The substrate surface needs to be thoroughly cleaned to ensure that it is free of any contaminants such as oil, grease, or oxides. This can be achieved through a variety of methods, including mechanical cleaning, chemical cleaning, or a combination of both. Proper surface preparation is also essential to ensure good adhesion between the substrate and the electroless nickel coating.
Substrate Activation
Activation involves the use of a suitable chemical solution to create a catalytic surface for the nickel to be deposited. This step is especially important for substrates that are not catalytic in themselves, such as aluminum or stainless steel. Without proper activation, the electroless nickel may not adhere properly to the substrate, resulting in a poor coating.
Temperature and pH Control
The plating solution needs to be maintained at specific temperature and pH levels to ensure optimal plating performance. Temperature affects the deposition rate, while pH affects the stability and composition of the plating solution. Deviations from the recommended temperature and pH ranges may result in changes in coating thickness, adhesion, and overall quality.
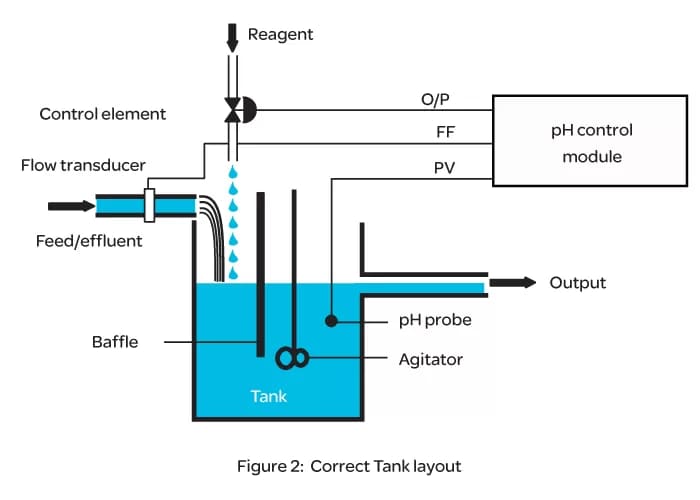
Stirring the Bath
Stirring the bath is important to ensure that the coating is evenly distributed. Agitation helps prevent stagnant areas from forming, which can lead to bath depletion or contamination. This can be accomplished mechanically, such as stirring or air agitation, or using specialized equipment, such as ultrasonic agitation.
Post-plating Treatment
Appropriate post-plating treatment is performed to enhance the performance of the electroless nickel coating. This may include heat treatment, passivation, or additional surface treatment processes. Heat treatment can increase the hardness and wear resistance of the coating, while passivation helps enhance its corrosion resistance. Surface treatment processes such as polishing or grinding can be used to achieve the desired surface texture or appearance.
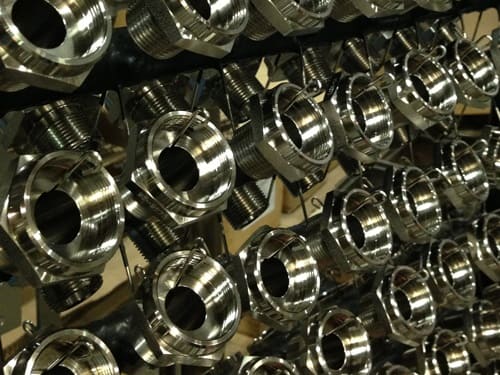
summary
successful electroless nickel plating requires careful consideration of several key factors. These include selection of the correct plating solution, proper substrate preparation and activation, temperature and pH control, agitation of the plating solution, and appropriate post-plating treatment. By considering these factors, manufacturers can obtain a high-quality electroless nickel coating that meets the specific requirements of their application.