Sump Pump Check Valves: Material Selection and Machining Challenges
In sewage treatment systems, sump pump check valves play a vital role. Their main function is to prevent sewage backflow and ensure the normal operation of the system.
Since sewage contains a variety of chemical components, solid particles and corrosive media, the material selection and machining process of the check valve have a direct impact on its performance, durability and economy.
This article will explore the material selection principles of sump pump check valves, as well as the challenges and solutions faced during the machining process.
1.Sump pump check valve – what is it and how does it work?
(1) Definition
A sump pump check valve is a valve installed on the sewage pump outlet pipe, mainly used to prevent the medium (sewage) from flowing back when the pump stops running. It is an indispensable key component in sewage treatment systems.
(2) Working principle
1) One-way flow:
A check valve is a type of fluid control valve. It is a valve specifically used to control the one-way flow of fluids (liquids or gases).
The sump pump check valve ensures that the medium can only flow in one direction through the automatic opening and closing of the valve disc or valve plate. When the pump is running, the medium pressure pushes the valve disc to open, allowing sewage to pass; when the pump stops, the valve disc automatically closes under the action of gravity or spring to prevent sewage from flowing back.
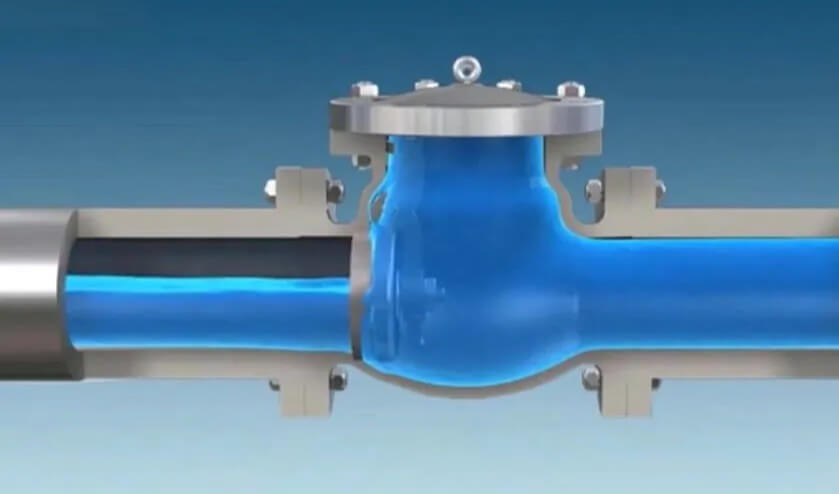
2) Prevent water hammer effect:
The rapid closing of the check valve can effectively reduce the water hammer effect and protect the pipeline and equipment from impact damage.
(3) Main types
1) Spring check valve:
The valve disc is controlled by spring pressure and is suitable for high-pressure sewage systems.
2) Swing check valve:
The valve disc is opened and closed by hinge flipping, which is suitable for large-flow sewage systems.
3) Ball check valve:
The flow direction is controlled by the rolling of the ball, which is suitable for sewage systems containing solid particles.
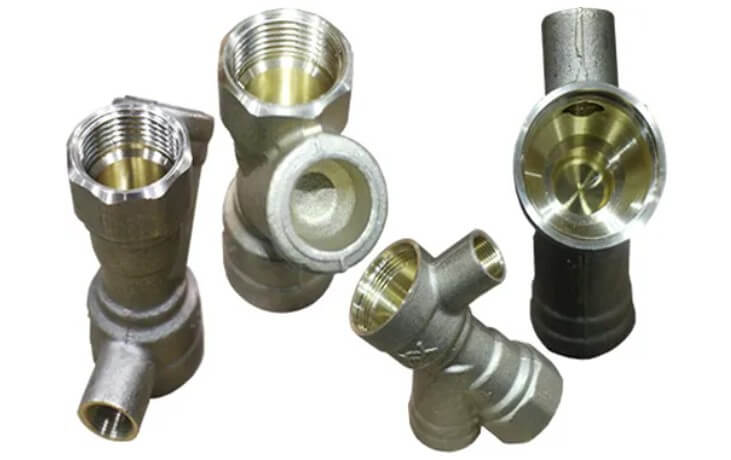
2.Material selection of key components of sump pump check valve
(1) Selection of valve body material
As the main pressure-bearing component of the sump pump check valve, the valve body needs to have good corrosion resistance, mechanical strength and machinability. Common valve body materials include:
1) Gray cast iron (HT200, HT250):
Advantages: low cost, good casting performance, strong shock resistance.
Disadvantages: weak corrosion resistance, not suitable for highly corrosive sewage.
2) Ductile iron (QT400-18, QT500-7):
Advantages: high strength, impact resistance, more corrosion resistant than gray cast iron.
Disadvantages: the quality of graphite spheroidization needs to be controlled during the casting process, otherwise it is easy to affect the mechanical properties.
3) Stainless steel (304, 316):
Advantages: excellent corrosion resistance, suitable for chemical sewage or high acid and alkali environment.
Disadvantages: high price, severe work hardening, high processing cost.
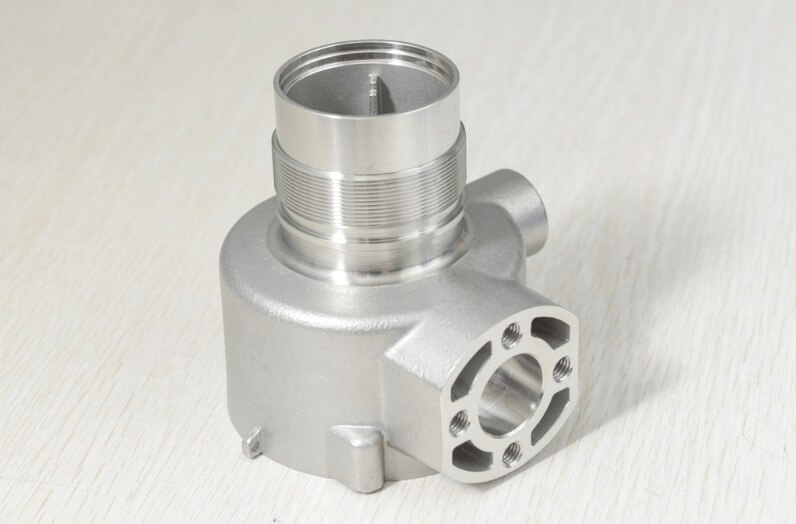
4) Copper alloy (H62, H65):
Advantages: good corrosion resistance, especially suitable for salty sewage environment.
Disadvantages: low mechanical strength, not suitable for high pressure environment.
(2) Selection of valve disc material
The valve disc is in direct contact with sewage, and its sealing performance and wear resistance are crucial. The main materials include:
1) Stainless steel (316, 304):
Suitable for corrosive sewage, high durability.
2) High-strength engineering plastics (nylon, POM):
Lightweight, corrosion-resistant, suitable for medium and low pressure sewage systems.
3) Rubber-coated metal:
Reduce impact noise and improve sealing.
(3) Selection of spring material
The spring is used to control the opening and closing of the valve disc, and its material needs to have good fatigue resistance and corrosion resistance.
1) Stainless steel (304, 316):
Excellent corrosion resistance, but slightly lower elasticity.
2) Alloy steel (50CrVA, 60Si2Mn):
High strength, suitable for high pressure systems, but requires anti-corrosion treatment.
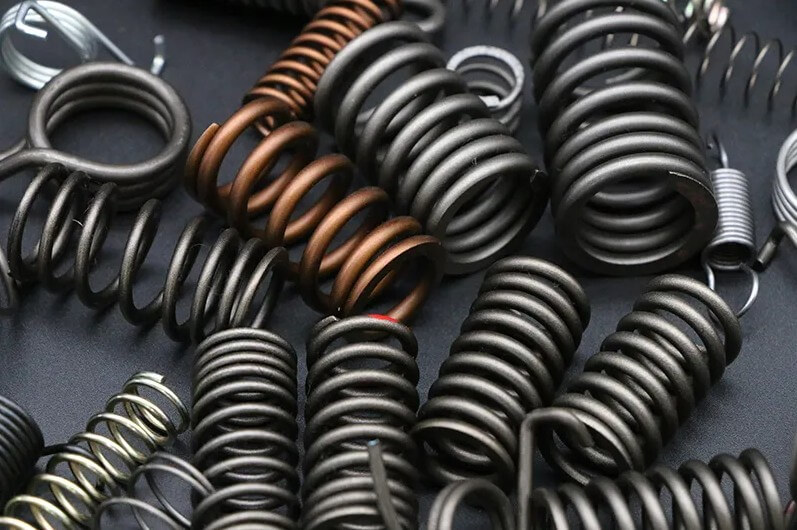
3.Analysis of machining difficulties of different materials
(1) Machining challenges of stainless steel
Stainless steel is difficult to machine due to its high hardness, severe work hardening and poor thermal conductivity. The main problems include:
1) High cutting force and fast tool wear:
Wear-resistant tools (such as coated carbide tools) are required.
2) Severe work hardening:
It is recommended to reduce the cutting speed and use a constant feed rate to reduce secondary cutting.
3) Difficult chip removal:
Use high-pressure coolant to increase the flow rate of the cutting fluid to prevent chip blockage.
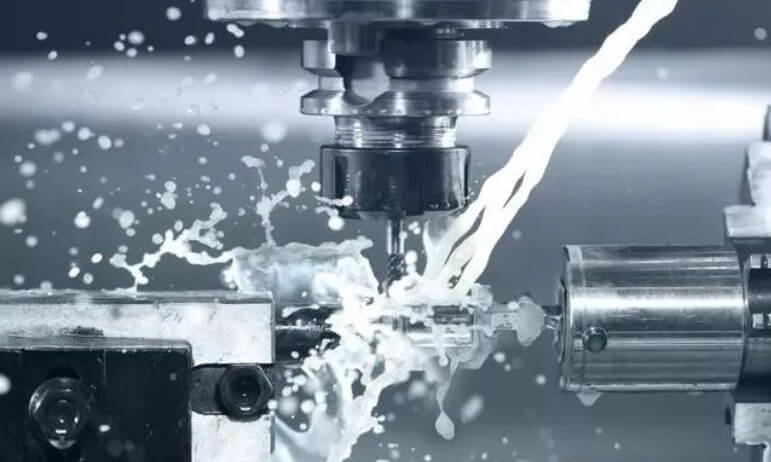
(2) Machining difficulties of ductile iron
The machinability of ductile iron is better than that of stainless steel, but the following problems still exist:
1) Graphite particles affect tool life:
Wear-resistant tools such as CBN (cubic boron nitride) tools are required.
2) Uneven distribution of hard spots:
Use a moderate feed rate to reduce the risk of tool chipping.
(3) Difficulties in processing high-strength alloys
High-strength alloys (such as high manganese steel and wear-resistant alloys) face the following challenges during processing:
1) High cutting force and concentrated heat:
Use water-based coolant to avoid overheating of the workpiece.
2) Tool chipping:
It is recommended to use a small rake angle tool and control the cutting speed.
(4) Challenges in processing rubber and engineering plastics
Rubber is easy to deform and difficult to process precisely: low-speed cutting or freezing processing is required.
Engineering plastics have a large thermal expansion coefficient: the processing environment temperature needs to be controlled to reduce dimensional errors.
4.Effects of materials and surface treatment on the life of sump pump check valves
(1) Surface treatment methods
1) Nitriding treatment (applicable to stainless steel and alloy steel): improve hardness and wear resistance.
2) Chrome plating (applicable to valve disc and valve seat): reduce friction and enhance the corrosion resistance of sump pump check valve.
3) Spraying Teflon (PTFE): applicable to corrosive sewage and reduce scaling.
4) Phosphate treatment (applicable to carbon steel): improve corrosion resistance and lubrication performance.
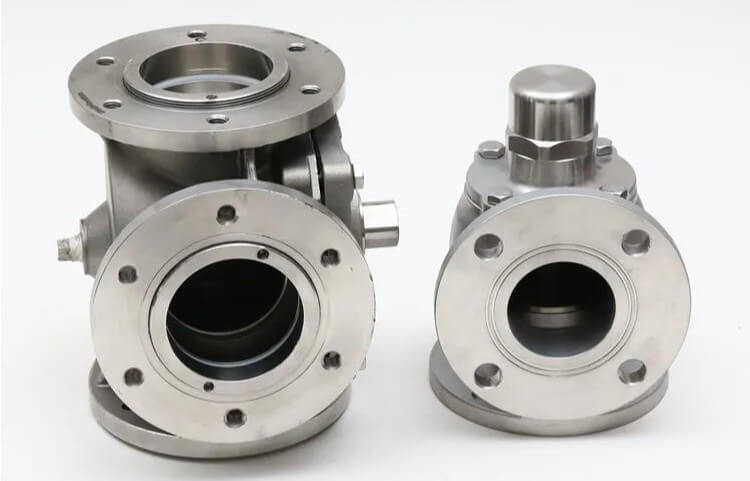
(2) Comparison of material durability in corrosive environments
1) Acidic sewage environment: 316 stainless steel > 304 stainless steel > ductile iron
2) High temperature and high pressure environment: alloy steel > ductile iron > gray cast iron
3) Sewage containing solid particles: high-strength engineering plastics > rubber-coated metal > stainless steel
5.Case analysis of sump pump check valve: practical application of different materials in sewage treatment systems
(1) Case 1: Municipal sewage treatment station
Material: ductile iron valve body + 316 stainless steel disc + 304 stainless steel spring.
Main challenge: Long-term erosion of sediment particles causes wear of the sealing surface.
Improvement plan: Optimize the hardening treatment of the sealing surface to improve wear resistance.
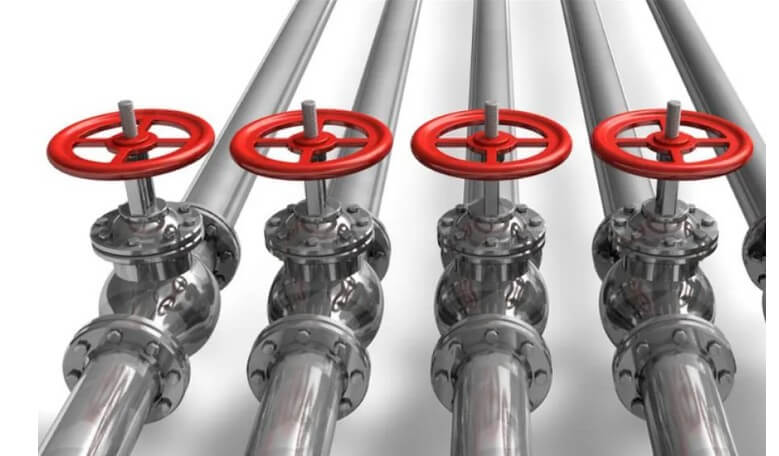
(2) Case 2: Chemical sewage discharge system
Material: 316 stainless steel valve body + rubber-coated disc + alloy steel spring.
Main challenge: High temperature environment causes aging of sealing materials.
Improvement plan: Use high temperature resistant rubber materials and improve the cooling system.
(3) Case 3: Food processing wastewater treatment system
Material: Stainless steel valve body + food grade plastic valve disc + stainless steel spring.
Main challenge: Frequent opening and closing leads to valve disc fatigue failure.
Improvement plan: Optimize the valve disc structure and reduce stress concentration.
6.Conclusion
The material selection of the sump pump check valve directly affects its durability and operating stability, and the challenges of different materials in the machining process also require corresponding technical optimization solutions.
Reasonable selection of valve body, valve disc and spring materials, combined with appropriate surface treatment technology, can greatly improve the service life and working efficiency of the sump pump check valve, thereby increasing the sewage discharge speed.