We care about
your anodizing solutions
Proactively coordinate quality vectors vis-a-vis supply chains
quickly engage client-centric comprehensive services.
Our qualifications:
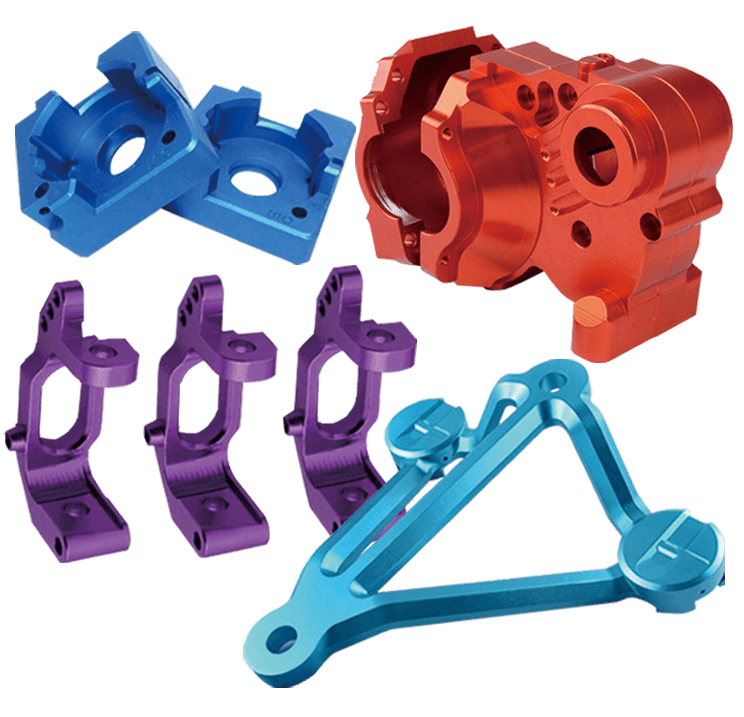
Surface finishes
Aluminum anodizing services
We offer anodizing type II and III, which are ideal surface finishes for aluminum parts. Anodizing strengthens aluminum parts and is available in several colors, depending on the type.
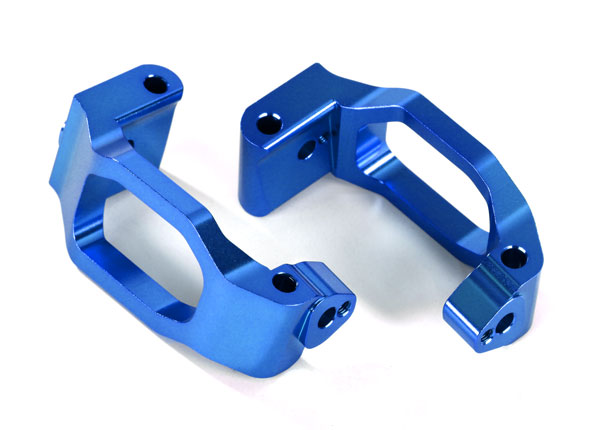
Part surface treatment
Anodized aluminium and aluminium alloys
Anodic oxidation is the process of forming decorative and protective films on the surfaces of aluminum and its alloys. In principle, the process of forming an oxide film on aluminum is actually an electrochemical reaction in which an electric current is applied at a sufficient voltage to a suitable electrolyte to form a porous oxide film on the surface of aluminum. Anodizing, unless otherwise specified, usually means anodizing sulfuric acid.
Oxidation type of aluminum alloy CNC machining parts
Types | description | Xavier |
Type I | chromic acid anodizing,Conventional oxide file was formed in chromium acid tank | |
Type IB | chromic acid anodizing,Low voltage process,22±2V | |
Type IC | Anodic oxidation of non-chromic acid, using a non-chromic acid formula to generate class I and IB oxide films | |
Type II | Anodic oxidation of non-chromic,Conventional oxide film foemed in sulfuric acid tank | √ |
Type IIB | Sulfuric acid anodized film ,Conventional oxide film produced using a non-chromic acid formulation | √ |
Type III | hard anodizing | √ |
Classes | description | Xavier |
Class 1 | Non-staining | √ |
Class 2 | staining | √ |
Critical items
Non standard requests
* We supply a range of standard colors. If you need a particular RAL or Pantone color code, please contact sales@xavier-parts.com
**As a standard our anodizing thickness will follow ISO 7599: ISO class AA10 (for clear) and ISO class AA15. If your parts require different standards, please contact sales@xavier-parts.com
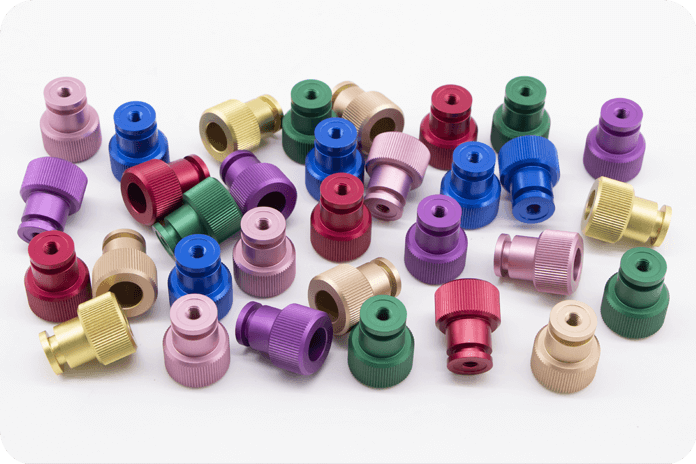
Xavier in its anodized
capacity
◆ substrate: aluminum and aluminum alloy
◆ Reference Standard M I L-A-8625F
◆ Film thickness range:
Coating type | I、IB、IC、IIB | II | III |
Thickness range(um) | 0.5~17.8 | 1.78~25.4 | 12.7~114.3 |
◆ other processes: sandblasting,chemical sanding,chemical polishing,shielding and blocking holes
◆ staining: black, blue, red, golden yellow (customized according to customer requirements)
◆ maximum machining size: 230 * 45 * 110 (c m)
◆ Maximum weight of single piece: 300 (kg)
◆ sealing method: environmental protection: boiling water, nickel salt, cobalt salt, ferrofluorone closed; non-environmental protection: dichromate, nickel salt + dichromate double closed
◆ test method: vortex tester membrane thickness test, paint adhesion test, membrane weight test, corrosion resistance test, light resistance test, wear resistance test, insulation test
◆The hardness of anodic oxidation film is higher than that of aluminum and aluminum alloy. Because the porosity of hard anodic oxidation film is lower than that of ordinary anodic oxidation, the hardness of hard anodic oxidation is relatively high. The hardness range of general reference is as follows.
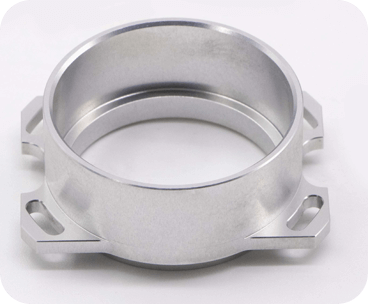
Aluminum and Aluminum alloy
40-160HV
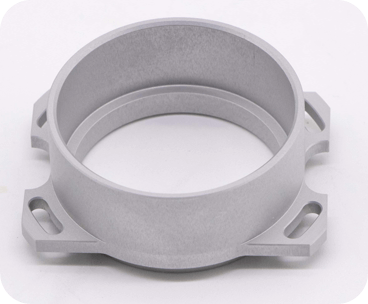
Anodic oxidation
250-300HV
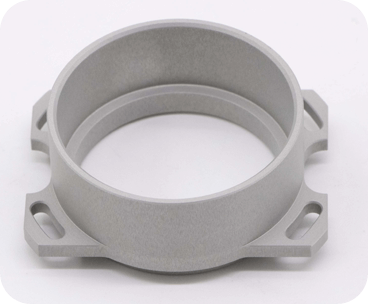
Hard anodizing
350-420HV
Quality
We have high standards for Part surface treatment
We manufacture your custom parts according to strict manufacturing standards and ensure all parts and processes adhere to the Xavier Standard. A thorough verification of these requirements is included in our inspection report that we ship with every order.
-
Standard 1
PO consistent
We ensure that every part after machining is as specified in the PO as customer requirements.
-
Standard 2
Quality check
Prior to MP shipment to ensure that each part meets order specifications and Xavier standards.
-
Standard 3
Require consistent
Ensure conformance of parts and any required documentation prior to dispatching the order.