Swiss CNC machining: the epitome of precision manufacturing
Swiss CNC machining, also known as Swiss lathe or core-type lathe, is unique in the field of mechanical machining with its unique structure and design. As a synonym for precision manufacturing, Swiss CNC machining is not only known for its high precision and high efficiency, but also has shown its strong application potential in many fields such as aerospace, medical equipment, automobiles, and watchmaking.
This article will delve into the working principles, steps, advantages, challenges, processing materials, precautions and application areas of Swiss CNC machining.
1.What is a Swiss CNC lathe?
Swiss CNC lathes, also known as Swiss CNC automatic lathes, Swiss screw machines or Swiss lathes, were originally developed for the Swiss watchmaking industry. In the 1870s, the first Swiss-type machines appeared, and around the 1960s the machines began to be used in other industries, with the first CNC Swiss being released in the 1970s. With the development of machines and tools, the design of Swiss lathes has been greatly improved, and they have gradually been widely used in parts processing and production in various fields.
The working principle of the Swiss CNC lathe is to fix the workpiece on the spindle and rotate and cut the workpiece by controlling the movement of the spindle and the tool. Swiss machine tools usually adopt a multi-spindle design, which can complete multiple processes such as turning, milling, and drilling at the same time, which greatly improves production efficiency and processing accuracy. In addition, Swiss machine tools move the spindle longitudinally during processing and are particularly good at processing slender shaft parts and complex, high-precision small parts, which gives it unparalleled advantages in the field of precision manufacturing.
2.Swiss CNC machining process
Swiss CNC machining is a precision metal processing method that is widely used in aviation, automotive, mold and other industries. The following are the specific steps of processing:
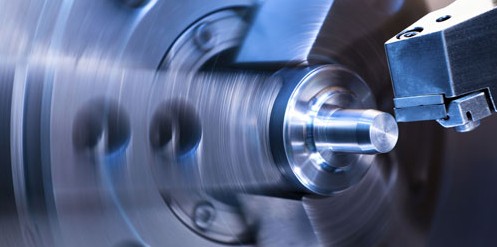
(1) Analyze drawings
First, a detailed analysis of the parts to be processed is required to determine the processing technology and technical requirements.
(2) Programming
Based on the analysis results, CNC programming software (CAD/CAM) is used for programming to generate tool paths.
(3) Tool setting
Before actual processing, the tool needs to be accurately calibrated to ensure processing accuracy. Knife setting can be done by trial cutting or using an external tool setting instrument.
(4) Processing parameter setting
According to the programming results and machine tool performance, set processing parameters, such as spindle speed, feed speed, etc.
(5) Program transmission
Transfer the programmed program to the control system of the CNC lathe.
(6) Workpiece clamping
Correctly install the workpiece to be processed on the lathe and clamp it.
(7) Processing start
After confirming that all parameters are correct, start the CNC lathe and execute the processing program.
(8) Processing monitoring
During the processing process, the operating status and processing effect of the machine tool are monitored to ensure processing quality.
(9) Processing completed
After the machining program is completed, the workpiece is removed from the lathe and necessary subsequent processing is performed.
(10) Quality inspection
Conduct quality inspection on processed parts to confirm whether they meet the drawing requirements.
3.Advantages of Swiss CNC machining
(1) High precision and efficiency
Swiss CNC machining is known for its high precision and efficiency. The machine tool’s high spindle speed and rapid traverse speed make the machining process faster while ensuring the accuracy of fine tolerances and complex geometries of parts. This processing method is particularly suitable for industries such as medical and aviation that require extremely high precision of parts.
(2) Strong adaptability
Swiss lathes can process stainless steel, titanium alloys, brass and other materials to meet the special needs of different industries. In addition, its modular design allows the machine tool to be adjusted and expanded according to production needs, enhancing production flexibility.
(3) High degree of automation
CNC machining technology relies on computer control, achieving a high degree of automation, reducing human intervention and operating errors, and improving production efficiency and product quality. Automation also enables machine tools to run continuously, reducing production downtime and improving overall processing efficiency.
(4) Reduce secondary processing
The Swiss lathe’s multi-functional tools and extensive milling and turning capabilities enable a variety of machining operations to be completed in one clamping, reducing the need for secondary processing and further shortening the production cycle.
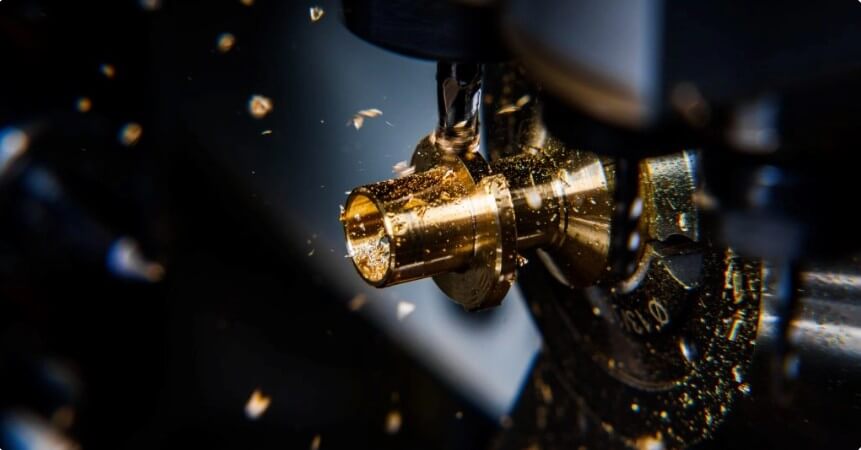
4.Challenges of Swiss CNC machining
(1) Operational complexity
The multiple functions and high speeds of Swiss lathes bring operational complexity. Multiple slides, spindles and cutting tools need to be programmed separately and operated simultaneously, which places high technical requirements on operators and programmers.
(2) High maintenance requirements
Due to the compact structure of machine tools, tool replacement and maintenance are cumbersome. In addition, efficiently operating machine tools also have high requirements for the working environment, requiring stable power supply and appropriate temperature and humidity conditions to ensure the normal operation of the equipment and extend its service life.
(3) Cost issue
Although Swiss lathes have many advantages, their high acquisition costs and high maintenance technical requirements make the initial investment large, which may be a considerable burden for small and medium-sized enterprises.
5.Swiss CNC machining materials
Swiss CNC machining can process a wide range of materials, including but not limited to the following:

(1) Stainless steel
It has good corrosion resistance and high strength and is suitable for medical equipment, food processing and marine equipment manufacturing.
(2) Titanium alloy
With its extremely high strength-to-weight ratio and excellent heat resistance, it is widely used in aerospace and high-performance sports equipment.
(3) Aluminum alloy
Due to its lightweight, corrosion-resistant and easy-to-machine characteristics, aluminum alloys are commonly used materials in CNC machining, especially in the aerospace and automotive industries.
(4) Brass
Brass is an alloy of copper and zinc that is stable but not strong enough. Typical applications include medical devices, consumer products, electrical hardware and contacts.
(5) Copper and copper alloys
It has good electrical and thermal conductivity and is commonly used in electronic and electrical applications.
(6) Alloy steel
Including various tool steels and alloy steels, which are often used to manufacture cutting tools, molds and mechanical structural components due to their excellent hardness and wear resistance.
(7) Platinum and iridium alloys
These precious metals are also important in specific applications because of their unique physical and chemical properties.
(8) Nylon
Nylon is used to make ultra-precision parts. It can make things like bushings, gears, and insulators because nylon slides easily, is lightweight, and doesn’t rust.
(9) Nickel
Nickel is mainly used in Swiss CNC projects to make parts that are not prone to corrosion, resistant to high heat, and conduct electricity well. For example, nickel parts in aircraft and electronics.
(10) Carbon steel
Carbon steel is used to make parts that need to be strong and affordable. It produces products such as automotive fasteners, shafts, gun parts and large machine parts.
Choosing the right material is crucial to ensuring processing quality and efficiency. Material properties, such as hardness, toughness, heat resistance and corrosion resistance, will directly affect tool selection during machining, cutting parameters and final product performance.
6.Precautions for achieving high precision in Swiss CNC machining
(1) Equipment selection and maintenance
Choose high-precision and high-rigidity CNC machine tools, and perform regular maintenance and upkeep to ensure the basic accuracy and stability of the machine tool.
(2) Tool selection and management
Select appropriate tools according to the processing materials and requirements, ensure the sharpness and durability of the tools, and regularly inspect and replace severely worn tools.
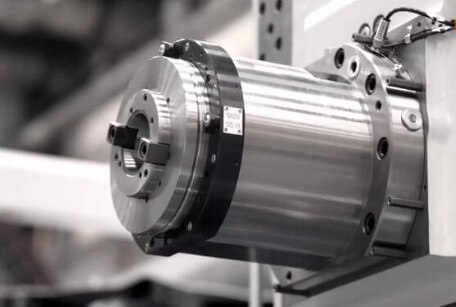
(3) Fixture and positioning
Reasonably designed fixtures and positioning devices reduce positioning errors and clamping deformations, ensuring the stability and accuracy of the workpiece during processing.
(4) Process parameter optimization
According to the characteristics of materials, cutting tools and machine tools, process parameters such as cutting speed, feed rate and cutting depth are reasonably selected, and process parameters are optimized through experiments.
(5) Temperature control
Control temperature changes during processing to avoid the impact of thermal deformation on processing accuracy, and use coolant or a constant temperature device to keep the temperature of the machine tool and workpiece stable.
7.Swiss CNC machining application fields
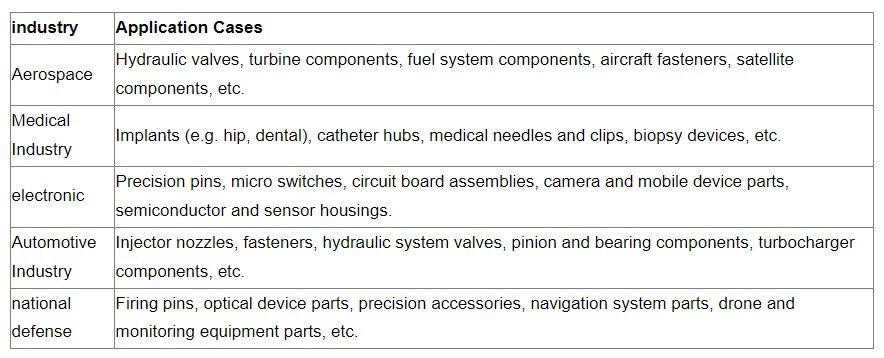
(1) Medical device manufacturing
Due to their high precision and stability, Swiss machine tools are very suitable for processing precision parts in medical devices, such as artificial joints, bone implants, etc. These parts often require tight tolerances and fine surface finishes, and Swiss CNC machines can meet these requirements.
(2) Watch and clock industry
Swiss CNC machining plays an important role in watch manufacturing and is used to process tiny parts in watches, such as gears, shafts, etc. These parts require extremely high precision and surface finish, and Swiss CNC machines can perform these machining tasks with precision.
(3) Aerospace
In the aerospace field, Swiss CNC machine tools are used to process aircraft engine parts, aircraft structural parts, etc. These parts are often made from high-performance materials and have complex geometries that can be machined with precision using Swiss CNC machines.
(4) Automobile manufacturing industry
Swiss CNC machining is used in the automobile manufacturing industry to process engine parts, transmission system parts, etc. Through CNC programming, high-precision and high-efficiency parts processing can be achieved, improving the quality and production efficiency of automobile manufacturing.
(5) Electronic industry
In the manufacture of electronic products, Swiss CNC machine tools can be used to process electronic equipment housings, connectors, conductive plates, etc. These parts usually require high precision and complex shapes, and Swiss CNC processing can meet these requirements.
(6) Precision instruments
Swiss CNC machining is also widely used in the manufacturing of precision instruments, such as measuring equipment, laboratory equipment, etc. The precision parts in these devices often require high-precision machining, and Swiss CNC machine tools can provide the required accuracy and stability.
8.Summary
To sum up, Swiss CNC machining plays an important role in many fields because of its high precision and efficiency, meeting the market’s demand for high-quality, high-precision parts. Promoted the development of modern manufacturing.