Basics of Swiss Machining and Its Applications
Swiss machining, also known as Swiss turning, is a high-precision CNC machining process performed on special lathes designed to produce small, intricate parts. Swiss lathes can run to extremely tight tolerances and with shorter cycle times than conventional lathes, making them ideal for mass-producing complex parts. Let’s dive into the basics of this cutting-edge turning process.
1.What is Swiss machining
Swiss lathes were originally designed by Swiss watchmaker Jakob Schweizer to produce extremely small parts for the watchmaking industry. The first Swiss-style lathes were developed in the 1870s, but became popular in other industries in the 1960s due to their high accuracy and small margin of error.
In a CNC Swiss machine, a sliding headstock pushes a portion of the metal blank into a guide bushing. The rest of the workpiece is securely held in a chuck behind the guide bushing and is not directly exposed to the machining area.
When one portion of the workpiece is machined, the bar moves forward along the z-axis to allow another portion to be machined. This segmented approach allows for fast, close turning of parts because it eliminates part deflection under strong cutting forces and improves accuracy.
Most Swiss-type lathes today use one or two main spindles and one or two subspindles. The main spindle is used for most machining operations. The subspindle is located behind the part and its operations typically include picking up the part as it is cut off and performing various secondary operations, such as drilling or tapping on a side that was inaccessible before the workpiece was separated.
Once these operations are complete, the secondary spindle ejects the finished part into a bin, eliminating the need for the operator to manually change each part, as is typically the case with standard CNC lathes.
In terms of materials, Swiss lathes are typically used to machine metals (carbon steel, aluminum, stainless steel, brass, etc.) and sometimes plastics (nylon, polycarbonate, etc.), and less often wood.
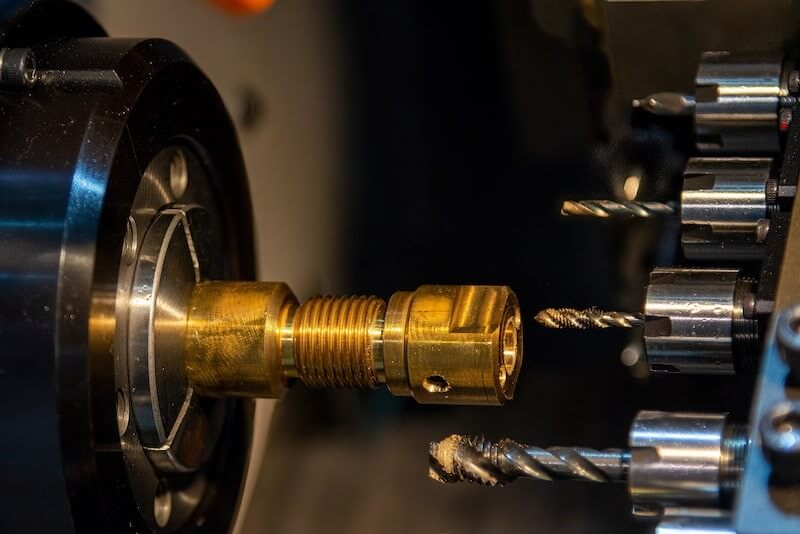
2.Swiss Turning vs. Conventional Turning
Swiss-type lathes are generally more flexible, efficient, and precise than conventional lathes. We will cover some of the key differences between the two:
1) Headstock
A conventional lathe has a fixed headstock that clamps the workpiece at one or both ends (using a tailstock). Swiss machines, on the other hand, have a moving headstock that allows the workpiece to be repositioned along the z-axis during machining.
Machining Process
Swiss machining uses a segmented approach where specific portions of the workpiece are machined as the workpiece passes through a guide bushing. Segmented operations improve consistency, producing precision CNC turned parts with desired tolerances.
A conventional lathe processes one operation at a time, changing cutting tools after the previous step is completed. It is generally slower than Swiss machining, which is segmented, but can complete the entire workpiece in one go compared to Swiss machining, which feeds bar stock through a guide bushing.
2) Guide Bushing
A conventional lathe holds the workpiece in the spindle chuck. Longer workpieces with an aspect ratio greater than 4:1 are more likely to have part deflection due to overhang. Swiss-type lathes use guide bushings to support the workpiece. Machining is done near the guide bushing, so overhang and part deflection are not an issue. Additionally, Swiss-type lathes can complete deeper cuts in a single pass, rather than multiple shallow cuts as with conventional lathes, because the guide bushings provide good support for the workpiece.
However, there are also sliding headstock CNC lathes without guide bushings. This allows for faster setups and improved workpiece concentricity, but these benefits are generally only applicable to shorter workpieces with a low length-to-diameter ratio.
3) Cycle Time
Swiss-type machines are able to perform multiple machining operations with a single setup, thus significantly reducing cycle time for complex geometries compared to conventional machining. Swiss-type machines have 7 to 13 axes, compared to 2 to 5 axes on conventional machines. Automatic barfeeding on Swiss lathes reduces machine downtime and increases productivity because there is no need to manually change workpieces.
4) Coolant
Swiss-type machines use oil as a coolant, while conventional lathes use water. Although oil has a lower heat capacity than water, its high lubricity reduces friction and minimizes overall heat generation. In addition, oil helps reduce tool wear and prevents rust.
5) Post-processing
Parts made on conventional lathes often require additional finishing operations, depending on the level of complexity. Swiss lathes produce parts that are extremely fine and precise, thus reducing the need for secondary finishing operations, or in many cases eliminating them entirely.
6) Cost
Due to their advanced design and more tooling options, Swiss lathes are generally more expensive than conventional lathes. But the difference is not as great as one might think, as there are Swiss CNC machines on the market that don’t cost much more than conventional lathes. When used specifically to produce large quantities of complex parts, Swiss lathes become a more economical choice in the long run, despite the difference in upfront costs.
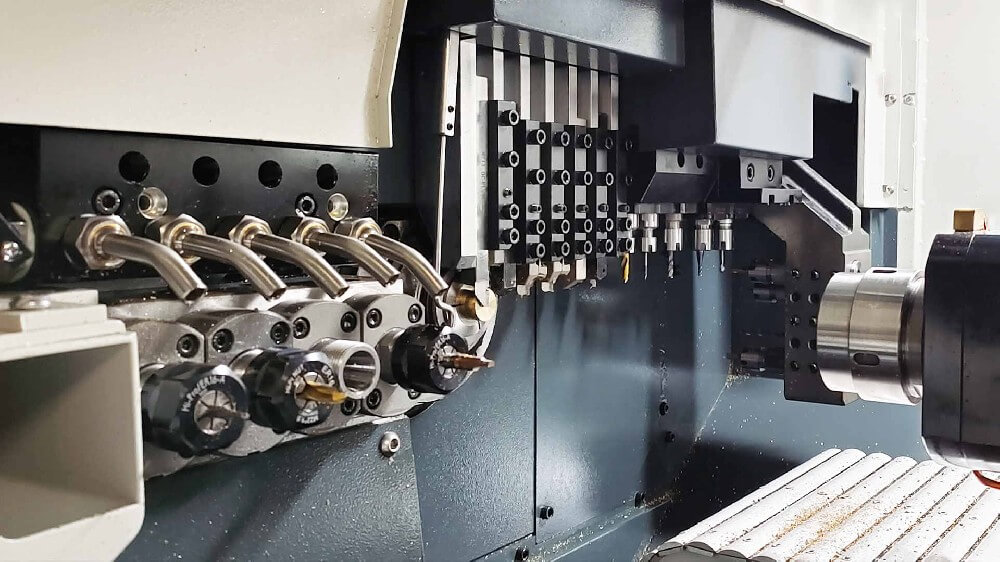
3.Benefits of Using a Swiss-Type Lathe
Fast production speeds and precision make Swiss lathes superior to their counterparts in many ways:
High Precision – Swiss lathes are known for their extreme precision and tight tolerances, which are often required in industries such as medical, aerospace, or complex electronic components.
1) High Repeatability
Swiss machines consistently produce high-quality parts, which is critical for industries where every micron counts.
2) Complex Part Production
With their unique guide bushing system, Swiss lathes can process slender parts and intricate details more efficiently than conventional lathes.
3) Simultaneous Operations
Many Swiss CNC lathes are equipped with multiple toolpaths that can perform operations such as turning, drilling, and milling simultaneously. This can reduce cycle times for complex parts.
4) Fewer Secondary Operations
With the ability to perform multiple operations in a single machining cycle, parts often come off Swiss machines finished or nearly finished, reducing the need for secondary operations.
5) Reduced Deflection
The design of Swiss lathes, in which the workpiece is supported very close to the cutting tool by guide bushings, significantly reduces deflection, resulting in better surface finishes and consistent dimensions on slender parts.
6) Higher RPMs
Swiss lathes can often run at higher RPMs without vibration, resulting in shorter machining times and improved surface finishes.
7) Automation
Swiss turning centers are able to highly automate most, if not all, of the machining process. Automatic barfeed, the number of available tools, multiple axes of motion, and CAM programming combine to allow for precision machining of complex parts without human intervention.
4.Limitations of Swiss CNC Machining
Despite the obvious advantages of Swiss CNC machining, it also has some limitations.
1) Barstock
Barstock is typically limited in size to between 2 mm and 38 mm and requires a consistent diameter as it passes through the guide bushing (screw machine quality barstock). Some machines can handle slightly smaller or larger barstock, but this is uncommon. Sometimes, one end of the barstock is chamfered (usually if its diameter is > 10 mm) to allow the gripper to grip securely.
2) Tooling Cost
Specialized tooling for Swiss machines can be expensive. Additionally, tool size and geometry can be limited due to the close proximity of multiple tools.
3) Heat Dissipation
Swiss lathes use oil as a lubricant compared to conventional lathes that use water. The downside is that oil is less effective at dissipating heat, which can cause problems during long runs
4) Setup Time
Calibrating and changing the number of cutting tools increases the amount of preparation required before starting a project. Swiss machines also require programming, which can be time-consuming, and proper employee training is required to maximize the benefits of Swiss automatic lathes.
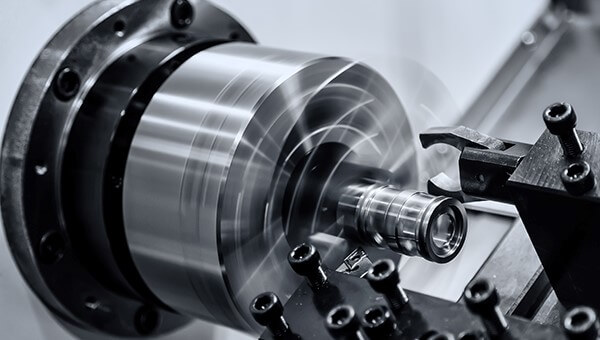
5.Applications of Swiss Machining
Swiss machines are versatile and ideal for parts manufacturing in several industries.
1) Watchmaking
Swiss lathes were originally developed for the watchmaking industry to manufacture miniature, high-precision mechanical parts.
Aerospace – The aerospace industry uses lightweight precision parts with very tight tolerances during assembly. Swiss machines are well suited for this purpose and are known for machining small, complex parts.
2) Medical Devices
The high standards in the medical field have greatly benefited from the capabilities of Swiss lathes in manufacturing medical devices, surgical screws, and implants.
3) Electronics
The manufacturing of electronic components has become increasingly difficult as they become smaller and more advanced. The increasing demand for small parts such as pins, sensors, and connectors makes using Swiss-type CNC lathes a good choice.
4) Automotive
Swiss machines are used in the automotive industry to manufacture fuel injectors, sensors, and valves.
5) Musical instruments
The musical instrument industry benefits greatly from Swiss machining technology’s precision in creating complex parts that ensure optimal function and sound quality. Examples include long, thin parts for woodwind and brass instruments, tuners and tailpieces for guitars, and rods and tensioners for drums. This high level of consistency and accuracy is essential to meet professional standards and provide a consistent sound.