The Art of Custom Metal Machining: Techniques and Tips
The fascinating world of custom metal fabrication, which transforms raw materials into complex structures and functional parts for industries ranging from aerospace to construction, is similarly fascinating with DIY machining.
Advances in technology have revolutionized the way metal machining processes are performed, making them more efficient, precise, and environmentally friendly.
In this blog post, we will explore the various technologies and processes involved in metal machining and how they contribute to the creation of high-quality, custom products.
You will gain insight into the importance of choosing the right metal fabricator, the cutting-edge technologies that shape the industry, and the safety precautions necessary for a seamless manufacturing process.
Let’s create a sustainable future together with our high-quality metal machining solutions.
1.Learn about Metal Machining
Metalworking is a complex and varied process that involves shaping, cutting, and joining a variety of metals to create custom products.
This process is an integral part of numerous industries, and each technique requires specific knowledge and expertise.
From sheet metal to bar metal, the fabrication process transforms raw materials into functional components for a variety of applications, including metal machining projects.
The metal machining industry includes machine shops that are responsible for performing a variety of operations, including but not limited to:
1. Joints
2. Cuts
3. Bends
4. Forms
These shops play a vital role in the execution of metal machining projects. Companies often outsource metal machining services to save costs, gain expertise, and increase efficiency.
Anyone involved in the industry or seeking metal machining services will benefit from a basic understanding of these processes.
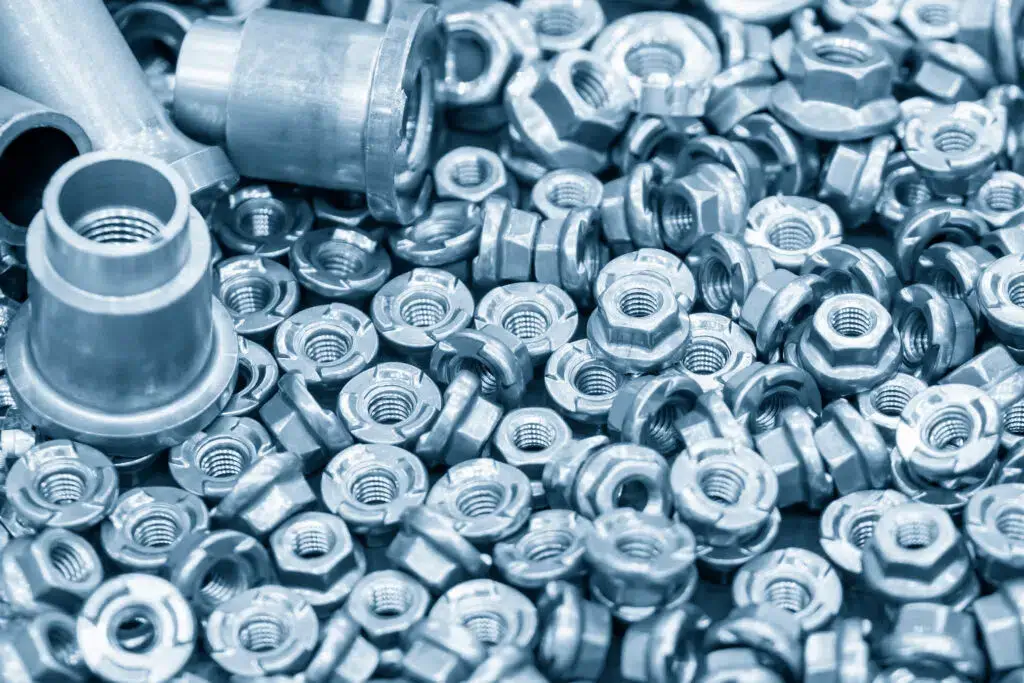
2.Custom Metal Machining Explained
Custom metal machining allows for unique, high-quality products to be tailored to specific requirements and industry standards. The process offers flexibility in design and material selection, unlike other manufacturing processes.
Custom fabrication services, such as cutting, bending, and welding, are designed to meet specific size and shape requirements, ensuring precision and customer satisfaction.
The use of cutting-edge technology in custom metal machining optimizes the entire process, resulting in shorter turnaround times, improved quality control, and greater cost-effectiveness when working with sheet metal and other materials.
High-quality metal parts are produced by adhering to precise specifications, striving for accuracy at every stage of production, and maintaining precise measurements.
3.Metal Machining Technologies
Metal machining includes a range of basic processes, with cutting metal being a fundamental step in achieving precision and complex shapes. Technologies such as laser cutting are indispensable in this area.
However, metalworking is not limited to cutting and includes a variety of key techniques such as:
1. Bending
2. Folding
3. Forging
4. Casting
5. Machining
6. Extruding
7. Drawing
8. Punching
9. Stamping
10. Shearing
11. Welding
Each process has its own unique purpose in the manufacturing process and helps produce a high-quality metal product.
In the next section, we will review some of the different metal machining techniques and their role in shaping metal into the desired results.
These techniques are essential to metal machining projects and ensure accuracy, efficiency, and excellent results.
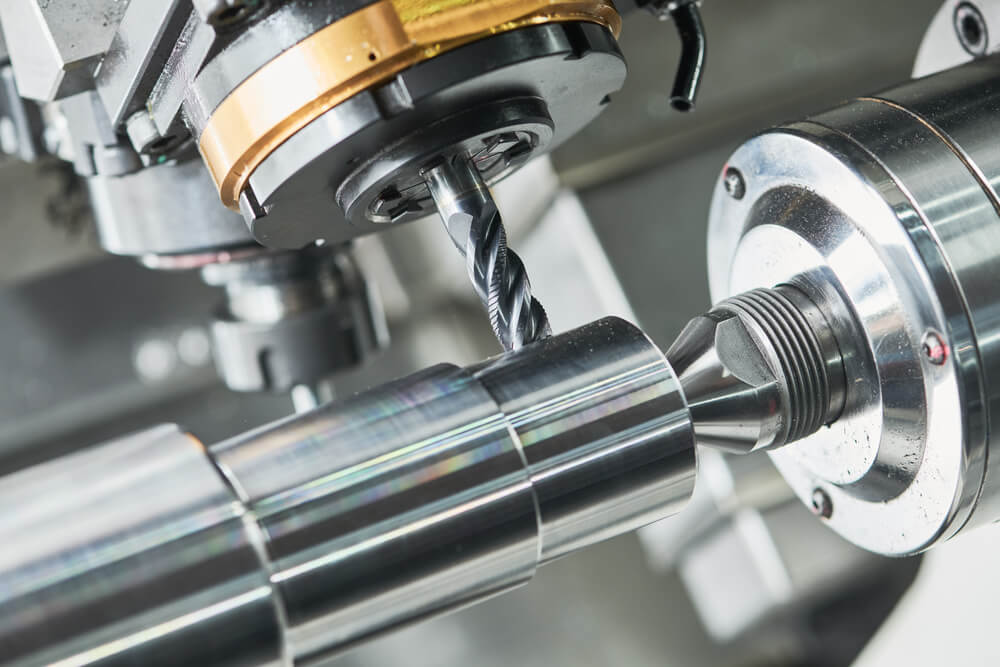
1) Bending and Folding Techniques
Bending and folding techniques manipulate sheet metal to form the desired shapes and angles and require skill and the proper tools to perform successfully.
Folding is a metal machining process that involves manipulating metal to form angles and is often used to shape sheet metal. More than 25% of all processes in the metal preparation phase involve folding, especially when working with flat sheet metal.
Successful bending in metal machining requires repeated practice and following the correct techniques, which are essential to achieve precise and efficient results.
The ability to perform bending and bending operations is a critical skill for any fabricator or custom metal fabricator.
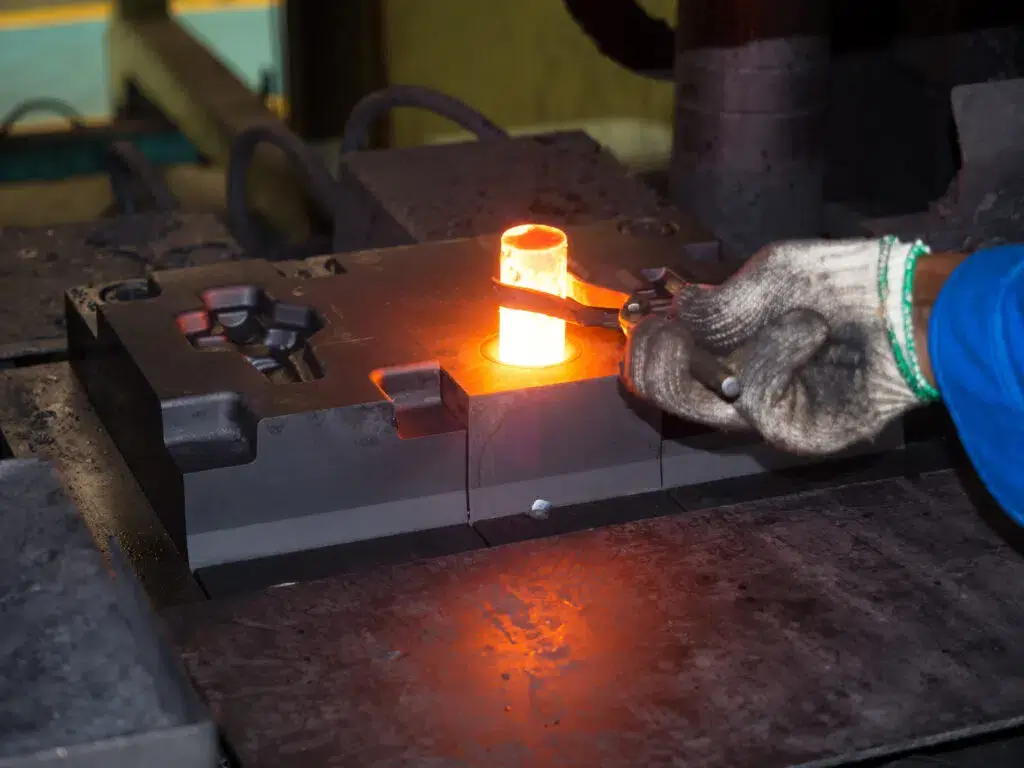
2) Forging and Casting: Shaping Metal Using Heat
Forging and casting involve shaping metal using heat and force. Forging involves shaping metal using compressive forces, usually by hammering or die striking. Casting is a manufacturing method where molten metal is poured into a mold or die.
Once cooled and hardened, it takes on the desired shape. Both techniques are essential in the metal manufacturing process, and each has unique uses and distinct advantages.
Forging has a long history. Blacksmiths have used it as a metal manufacturing technique for centuries.
While blacksmiths and fabricators still use hand forging to complete intricate and creative work, modern technological advances have led to the development of die casting and permanent mold casting, which are more efficient and better suited for mass production.
3) Machining: Precision and Control
Machining is a subtractive process that involves removing unwanted material. This helps create precise shapes and forms. The process utilizes tools such as drills, lathes, and milling machines to achieve the desired shape and finish.
Machining offers many advantages in metal machining, such as precision and accuracy, repeatability, and cost-effectiveness. Additionally, machining can produce parts with complex shapes and tight tolerances.
Safety measures are essential when machining. These measures include wearing necessary protective gear, using appropriate tools and techniques, and following all safety instructions.
Additionally, it is imperative to ensure that the work area is clean and free of any clutter. These precautions help maintain a safe work environment and ensure that metal machining projects are completed successfully.
4) Extrusion and Drawing: Creating Unique Shapes
Extrusion and drawing processes allow metal to be formed into unique shapes. Extrusion involves passing metal through a die to form cylindrical items, such as wire or pipe, while a tapered die is used to pull the stretched metal into a thinner shape.
Both techniques play an important role in metal machining to create complex and unique shapes.
Extruded steel fabrication is a process where metal is pushed or pulled through a die to obtain the desired shape. This is a very precise process that produces consistent results.
Drawing, on the other hand, determines the shape, size, and quality of the finished product, guaranteeing customer satisfaction with the process.
The versatility and precision of these techniques help create high-quality metal products.
5) Punching, coining, and shearing
Punching, coining, and shearing techniques produce different effects in metal:
1. Punching uses a turret and die to create holes in metal.
2. Punching involves using a press or hammer to create indentations rather than holes in a metal panel or sheet to form shapes, letters, or images.
3. Shearing uses pressure to break metal, making one long, straight cut with two tools positioned above and below the metal.
These techniques play an important role in a variety of metal machining projects, allowing for precise shaping and manipulation of metal parts. Mastering these techniques is essential for modern metal fabricators, as they contribute to the overall success and quality of metal machining work.
6) Welding: Joining Metal Pieces Together
Welding is the process of joining metal pieces together using heat and pressure. There are a variety of welding techniques to choose from, including:
1. Stick or arc welding
2. MIG welding
3. TIG welding
4. Flux-cored arc welding
Welding is a critical component in any metal machining process, as it enables the creation of complex structures and functional components.
It takes a skilled welder to perform TIG welding, a complex process that works well for most metal products and complex projects.
Welding techniques such as MIG and flux-cored arc welding offer portability and efficiency to metal machining.
Mastering these welding techniques is essential for any metal fabricator as it helps in the successful completion of metal machining projects.
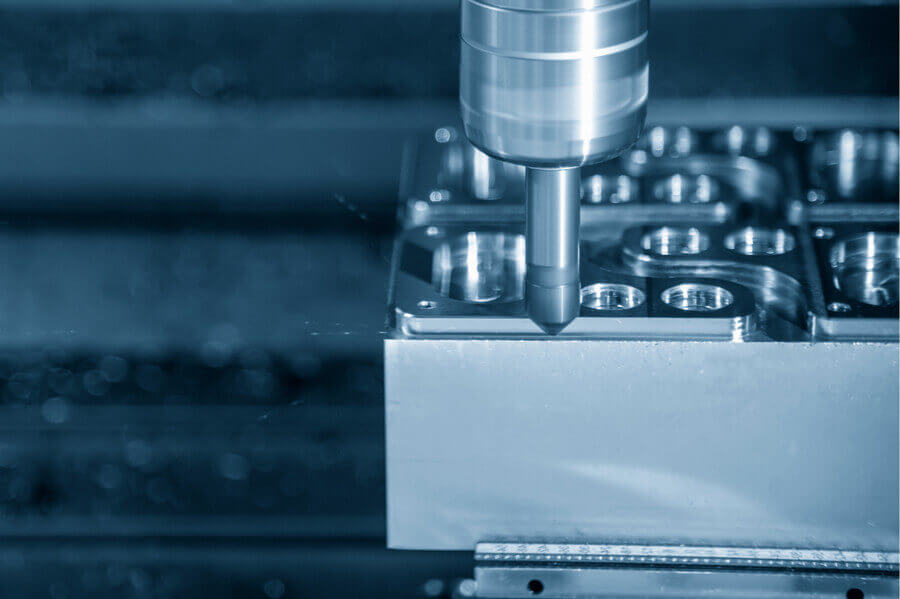
4.Tips for Selecting the Right Metal Fabricator
The success of a metal machining project depends on selecting the right metal fabricator. Factors to consider include:
1. Experience
2. Industry Served
3. Resources
4. Precision
5. Type of Production
6. Materials in Stock
Getting quotes from various businesses and gathering testimonials from other customers can provide insight into a metal fabricator’s production volume and customer service levels.
An informed decision requires evaluating the experience, resources, and industry knowledge of a potential metal fabricator. Ensuring that the metal fabricator selected meets your specific requirements and industry standards will help in the success of your metal machining project.
Companies like Xavier employ skilled fabrication and fabrication professionals to provide reliable, quality metal machining services, delivering products and services that exceed industry quality standards.
5.Shape the Future with Xavier
In summary, metal machining is a diverse and complex process that plays a vital role in many industries.
The various technologies and processes involved in metal machining, such as cutting, bending, forging, casting, machining, extrusion, drawing, punching, stamping, shearing, and welding, help to manufacture high-quality customized products according to specific requirements and industry standards.
As the metal machining industry continues to evolve, the focus on cutting-edge technology, efficiency, accuracy, and sustainability will drive its future growth. Embracing these advancements and ensuring the safety of all those involved in the process is essential to the successful completion of metal machining projects.