Basic Introduction to Face Milling
As one of the important technologies in CNC machining, face milling plays a vital role in surface flattening of workpieces and various machining scenarios. Next, we will explore various aspects of face milling in depth, including its definition, working principle and other related knowledge, to provide you with a comprehensive technical guide.
1.What is face milling
Face milling is a machining technique used to flatten and smooth the surface of a workpiece. Machinists can use a machining center or milling machine to perform this process. The main difference from traditional milling technology is that in face milling, the milling machine or machining center is perpendicular to the workpiece, that is, the top of the machine mills the workpiece.
It can be divided into manual and automatic. The automatic has a more constant feed rate and can reduce the risk of failure or miscutting compared to manual.
Face milling uses a variety of milling cutters such as end mills, shell mills and fly cutters. The machine tool rotates the tool counterclockwise to move the workpiece over the tool teeth.
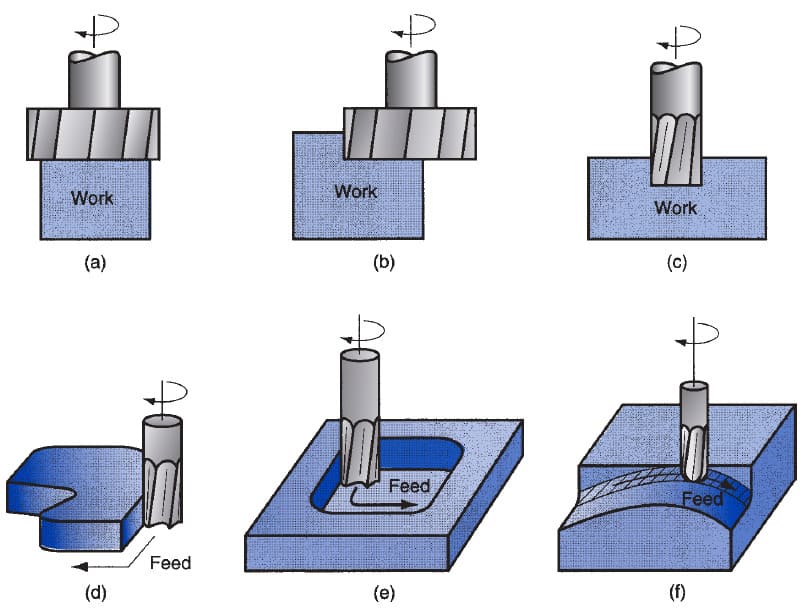
2.How face milling works
(i) Workpiece positioning
Before face milling, make sure the workpiece is clamped firmly on the machine table to prevent it from slipping.
(ii) Spindle positioning
Place the milling machine perpendicular to the workpiece so that the top of the milling machine can act on the material.
(iii) Adjust feed rate and torque
Adjust the feed rate and the speed at which the machine moves the tool (spindle rotation) to ensure that the machine cuts in the correct position.
(iv) Machining
After the machine is set up, the CNC machining code entered by the computer does all the work to machine the desired shape and size on the workpiece.
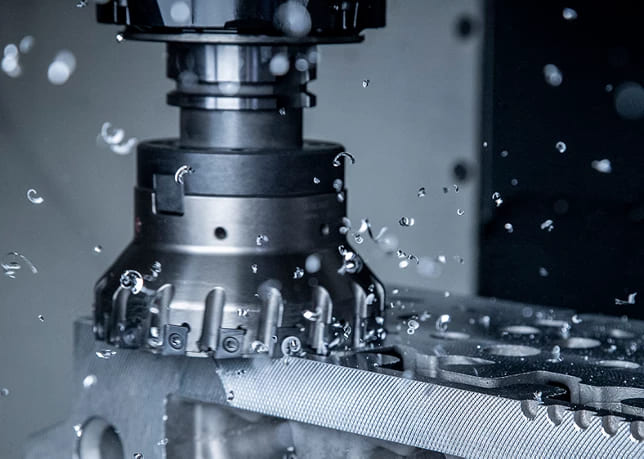
3.Choose the right face milling cutter
(I) Shell milling cutter
Shell milling cutters are the preferred cutter for face milling. They have multiple teeth and a blade with a labeled insert. They are very suitable for producing a consistent surface finish and can control the amount of material removed each time. They are suitable for processing a variety of materials. However, depending on the thickness of the material, the insert may need to be replaced frequently.
(II) End milling cutter
End milling cutters have cutting edges and are suitable for complex processing on workpieces, but are not suitable for processing large pieces of material. They are not strong and have a limited selection of materials that can be processed.
(III) Flying cutters
Flying cutters have only one cutting edge and one blade. They consume relatively low power and run at a low speed, but they can produce fine surfaces. When selecting a tool, you also need to consider factors such as the angle at which the tool enters the workpiece, the coordination between the spindle and the machine tool, and the processing mode.
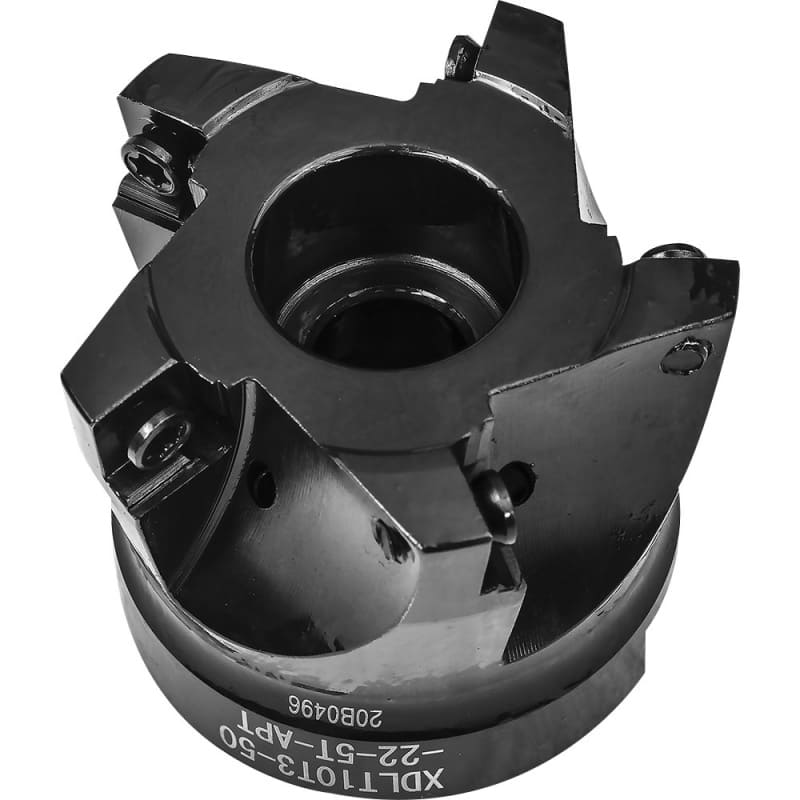
4.Types of face milling operations
(i) General face milling
Face milling cutters with a lead angle of 45° are suitable for general face milling. The tool diameter should be larger than the workpiece (at least 20% and up to 50%), and the entry point should be in the center, while considering the machine’s rotary size and horsepower.
(ii) Heavy-duty milling
Heavy-duty face processing requires a lot of material and a large machining center. A face milling cutter with a lead angle of 60° is the best choice. This process generates a lot of heat and chips, so you need to pay attention to protecting and cleaning the workspace.
(iii) High-feed milling
High-feed milling involves workpieces with high cutting speeds and feed rates. Face milling cutters with a small lead angle are the best choice. The lead angle is generally around 10°.
(iv) Finishing with wiper blades
A beautiful surface finish design can be achieved using scraper blades and standard blades. Scraper blades are mainly used for surface finishing, and their necessity depends on the type of standard blade used.
5.Tips for optimizing face milling process
(I) Choose the right tool
Ensure that the tool is suitable for the face milling process, provide optimal production efficiency, and make the work smoother.
(II) Set specific parameters
Set dedicated parameters for face milling to distinguish it from other machining programs and improve machining accuracy.
(III) Ensure the parameters are correct
The face milling program involves technical parameters such as cutting depth, feed per tooth, and feed per revolution. Ensure that each parameter is correct to avoid wasting material.
(IV) Keep the tool sharp
Use sharp tools to avoid slowing down the machining process and tool breakage to ensure machining efficiency and quality.
6.Application and advantages of face milling
The surface has the advantages of high efficiency in removing excess material, favorable chip formation, and high working speed. It is often used in the preliminary (rough) cutting stage of machining and can also be used for the final machining of the plane. In addition, by applying appropriate working parameters and cylindrical milling cutters, it can also be used to process components with holes. Correct planning can improve work efficiency and the final quality of the obtained surface.
Finally
Face milling technology is an integral part of modern manufacturing, providing high-quality surface finishes for a wide range of materials through precise control and efficient machining.
If you need an experienced CNC machining manufacturer, Xavier is your best choice. The Xavier team is well-equipped to provide high-quality CNC machining solutions to meet your personalized machining needs. For more information or to discuss your machining needs with us, please feel free to contact us.