Machining Guide for CNC Turned Parts
Manufacturing processes have come a long way since the beginning of the Industrial Revolution, which heralded the use of technology for mass production. Methods, equipment, and tools have been developed, used, and improved to increase efficiency. Among these were mechanical turned parts for the medical sector. Each turning parts manufacturer is also constantly updating turned parts meaning.
CNC turning is one of the cutting-edge technologies that has significantly improved the efficiency, speed, and quality of manufactured products. This production method uses deductive computer programming machining techniques to efficiently manufacture high-performance products. It is widely used in a variety of industries such as automotive, oil and gas, and aerospace, especially for customizing specialized parts.
This guide is designed to provide you with all the information you need to fully understand how CNC turned parts work, customization considerations, and other processes. It also includes the various applications of this manufacturing method in multiple industries.
1.Understanding CNC Turned Parts
An ongoing challenge facing manufacturers is the ability to efficiently manufacture products with complex shapes and geometries. This is one of the advantages of CNC turned parts, making them popular with many engineers and specifiers.
Computer numerical control or CNC machines are at the heart of CNC turned parts. CNC machines hold material within a clamped chuck and then use preprogrammed motions to spin it onto a stationary cutting tool or drill to remove portions of the material, creating the designed shape.
CNC turned parts can be made from a wide range of materials, including plastics, metals, and composites. But more importantly, because the machine’s motions follow computer-generated routes and are not subject to human error, its cutting precision and accuracy are exceptional.
This high level of precision is a major advantage of CNC turned parts over other manufacturing processes, especially those that require a lot of human input. Additionally, its ability to achieve dimensional accuracy with tight tolerances makes it a suitable manufacturing technology for industries with tight margins of error, such as aerospace and automotive.
However, you need to have a deep understanding of how CNC turned parts work and the process to fully utilize their capabilities, including functional materials, tools, and CNC machining programs and settings.
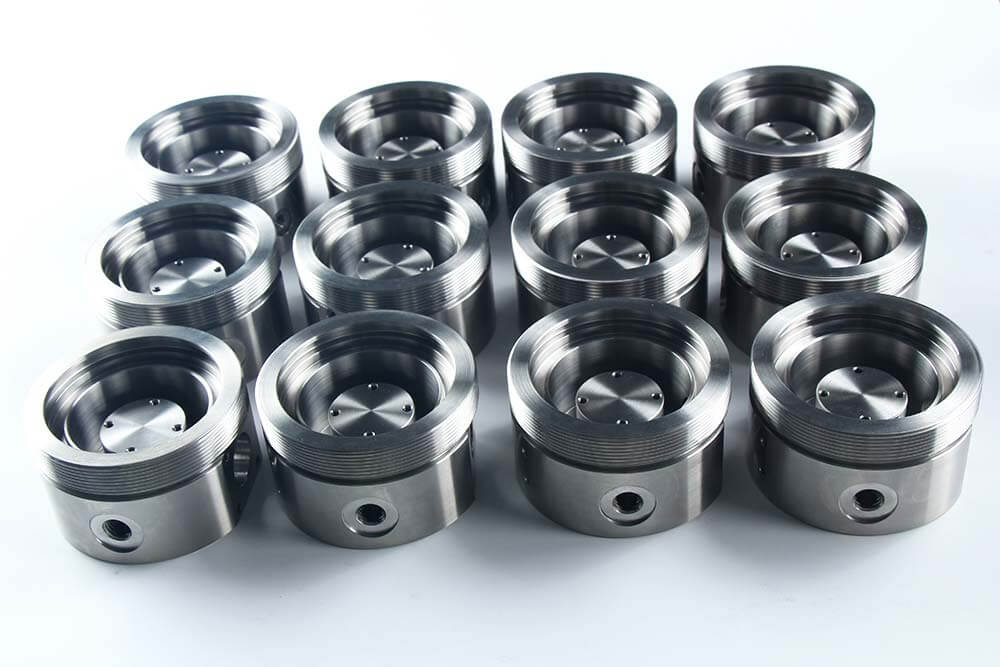
2.Material Selection for CNC Turned Parts
The versatility of CNC turned parts includes their ability to work with a wide range of materials, including precious metals, fibers, and plastics. However, the unique characteristics of individual materials determine their suitability and limitations when used for CNC turned parts.
Understanding these material limitations is essential to choosing the right material when using CNC machining in your projects. Here are some of the most popular materials that CNC machine tool manufacturers in different industries often use.
1) Explore Stainless Steel
Stainless steel has always been a preferred manufacturing material for different purposes, chief among which is its corrosion resistance. Other attractive properties of stainless steel include its high durability, strength, and thermal properties, which make it suitable for applications where the ability to withstand extreme temperatures is crucial.
However, the aesthetic appeal that manufacturers seek in decorative materials is what makes it attractive to manufacturers as a suitable material for CNC machined parts.
2) Benefits of Brass
An attractive property of brass is its high machinability, making it easy to handle during machining processes such as CNC machining. However, it also has other interesting properties such as high corrosion resistance, thermal and electrical conductivity, and an aesthetic appearance that make it suitable for decorative manufacturing. Considering its corrosion resistance and high electrical conductivity, it is also suitable for plumbing products and electrical components.
3) Steel Properties
Steel’s high tensile strength and durability are two of its properties that make it widely suitable for a variety of CNC machined parts. For example, in the design phase of mold design and other projects, designers often specify steel during the material selection phase of the design because of its versatility and ability to withstand high tensile stresses.
Depending on the grade of steel selected, it can also withstand load forces and pressure if heat treated, making it a suitable material for CNC turned parts for machine components and accessories.
4) Advantages of Aluminum
Aluminum is one of the few materials that is lightweight, yet very strong and can easily support structural loads and forces. Its anti-corrosion properties make it an ideal material for wet areas. Therefore, manufacturers and designers rely on these advantages when recommending the use of aluminum for CNC machined parts.
5) Unique Properties of Titanium
As the most precious metal on earth, titanium is widely recommended for its ability to resist corrosion and maintain structural integrity under extreme temperatures and pressures. In addition, titanium is lightweight, making it suitable for use in mechanical parts for manufacturing aerospace industry components.
3.CNC Turned Parts vs. CNC Milled Parts: Identifying the Difference
Manufacturers and designers often struggle with whether to use CNC milling or CNC turned parts for production because of the high precision of their computerized processes.
However, understanding the differences between the two machine processes, including their limitations, can help quickly identify and select the best machine process for each project. The movement of the components and tools is a significant difference between them.
The material moves in CNC turned parts, while the cutting tool is held stationary by a clamping mechanism. While the material is in place, the cutting tool travels according to the computer-generated CNC milling manufacturing strokes.
Therefore, CNC milling may be better suited for large pieces of material than CNC turning, as larger materials may be difficult to turn. In addition, the complexity of the design may be another important consideration in choosing one of the two CNC-based programs.
The CNC milling method is generally better suited for complex designs that require a large number of operations because the cutting tool can easily move along the material. Meanwhile, CNC turning is particularly well suited for round materials. Therefore, CNC milling is often used to produce parts with complex geometries, such as gears.
However, sometimes they are used together to complete custom designs, focusing on factors such as accuracy, measurement, and shape complexity.
Whether CNC turning or milling is used often depends on the complexity of the part and the materials used. For example, CNC turning is often used for cylindrical or round items, while CNC milling is better suited for parts with complex geometries, such as gears or brackets.
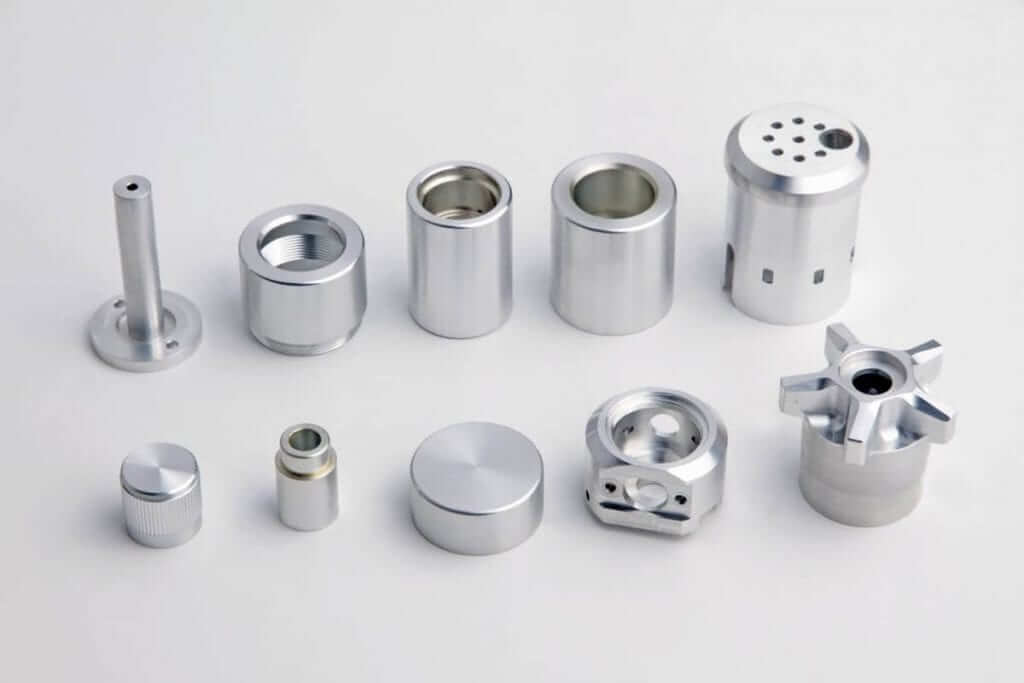
4.Key Industries Using CNC Turned Parts
The high precision of CNC turned parts and the ability to process a variety of materials, including metals, alloys, and plastics, are favored by many manufacturers and industries.
The following are the major industries where CNC turned parts help achieve high-quality and innovative products.
1) Medical Industry
In the medical field, medical procedures require the use of special tools with intricate design details and a narrow margin of error, and CNC turned parts help to manufacture some of the most complex mechanisms and devices used to save lives. These devices include implants, surgical instruments, and equipment.
2) Aerospace Industry
Passenger safety is a top priority in the aerospace industry, and strict design and manufacturing error tolerances can easily ensure passenger safety.
However, CNC turned parts are a staple of every aerospace manufacturing project. CNC turning is used to manufacture aerospace components such as landing gear, rotors, blades, and engine parts.
3) Transportation Sector
When safely moving people and cargo to their destinations, transportation equipment relies on high-precision CNC turning to create some of the most complex components, including bearings, shafts, and axles.
4) Oil and Gas Industry
This industry is another heavy user of CNC turned parts, producing pipe fittings such as valves, pump components, and unique studs and bolts. CNC turning’s ability to produce design accuracy using corrosion-resistant materials continues to be favored by the industry.
5.Customization Possibilities of CNC Turned Parts
Sometimes, CNC turned parts need to be customized to meet specific project requirements. These requirements are often not standard, and using traditional mechanisms or equipment can become challenging. Fortunately, CNC turned parts are versatile and easily customized to meet the desired project requirements.
CNC turning is particularly useful in industries such as mold making and automotive, where multiple custom pieces must be manufactured to meet safety, functional, or aesthetic standards. Components such as gears, engine parts, and brake calipers are some of the CNC turned parts used in automobiles for specific purposes.
More importantly, the precision required for these parts is high, requiring a precise method like CNC turning to achieve this level of accuracy.
Another industry that relies heavily on the high precision of CNC turned parts is the furniture and accessories industry. The designs in this industry are becoming more ergonomic, requiring high precision and fine details, including backrests, door handles, and custom-designed chair legs.
In addition, musical instruments and their accessories contain a large number of details because these details are necessary to make them function, especially instruments such as drums, guitars, and saxophones.
Before using CNC turned parts for your project, specific parameters are crucial, especially from a design perspective, so that manufacturers can achieve the expected level of detail and quality.
The following are some of the most critical information that manufacturers should have before producing CNC turned parts.
- Necessary design inputs: Design inputs are essential to achieve the desired functionality, geometry, and aesthetics of CNC turned parts. These inputs include drawings (2D and 3D), specification files, and data sheets containing features and dimensions. Manufacturers use these inputs to efficiently produce turned parts to meet specifications and select the appropriate tooling to realize the design.
- Material Preferences: While CNC uses a variety of materials to realize project designs, not all materials are suitable for most CNC projects. Therefore, the appropriate materials must be agreed upon and recommended during the design phase. These material preferences should be documented and presented to the manufacturer during production to ensure that the product is of high quality and meets the design specifications.
- Adherence to Quality and Tolerance Requirements: Tolerances and quality levels are not the same for every project. Since it costs more to achieve high quality within tight error tolerances, adhering to the quality specified by the design means that you will not spend more or less than the required budget.
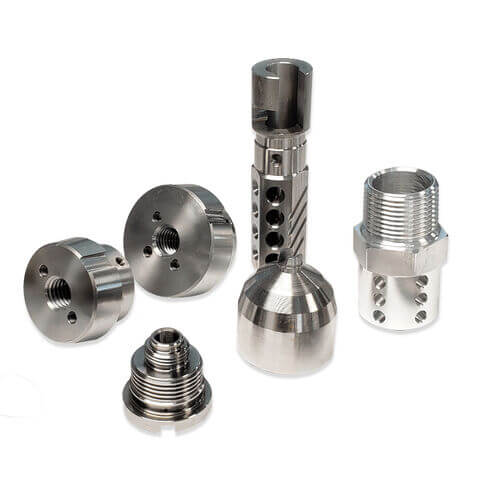
6.Surface Finishing Techniques for CNC Turned Parts
Functionality versus aesthetics often leads to economical failure for most products. Therefore, many manufacturers consider the surface finish of the product to be as important as functionality.
However, there are several ways to achieve an aesthetically pleasing surface finish; choosing the most appropriate method depends on the quality required for the design.
Listed below are some of the most common surface finishing processes for CNC turned products.
1) Painting
Painting is probably the most popular surface treatment method for CNC turned parts. The reason is that painting is easy to operate, with a variety of colors and qualities, which can suit almost any type of budget.
Painting is widely used on a variety of materials, which is why painting has become a standard method for finishing CNC turned parts. Simply clean the surface of the part to make it free of dirt, apply a primer, and then spray or brush the final desired paint color on the surface of the material.
2) Electroplating Method
Here, the surface of the material needs to be transferred from the source and placed on the target CNC part through an electric current. The material is usually a thin layer of metal with a shiny appearance, which makes the CNC turned part look more attractive. The thin layer also acts as an anti-corrosion layer for the part.
3) Polishing Process
Grinding the surface of the machined part is another way to show its beauty. Abrasive materials with a fine surface are often used to remove roughness and spatter from the surface of CNC turned parts, presenting a more beautiful material surface.
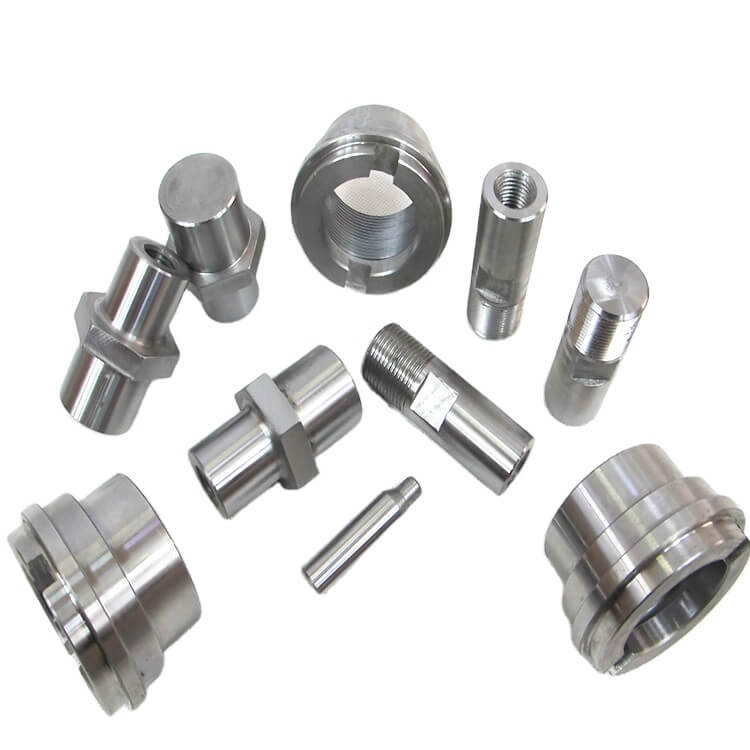
7.Finding Reliable CNC Turned Parts Manufacturers in China
China is a manufacturing hub, so it’s only natural that it’s the top destination for anyone looking to buy specialty manufacturing tools like rapid prototyping and CNC turned parts.
However, the sheer number of CNC turned parts manufacturers can make it difficult to find a reliable one. Still, there are some simple, not-so-obvious steps you can follow to quickly find a reliable manufacturer that fits your needs and budget.
- Do your research and ask for recommendations: Due diligence is one of the quickest ways to find a reliable manufacturer in China. If you have colleagues and friends who are already doing business in China, you can save yourself some research effort by asking for their recommendations.
- Assess expertise and capabilities: A manufacturer’s expertise and capabilities indicate their reliability. Understanding the technical level and success rate of their previous work will tell you if the manufacturer is reliable. This information is usually available on their website.
- Verify quality control measures and certifications: A commitment to high-quality manufacturing is another way to verify a manufacturer’s reliability. This shows that the system works and they are trustworthy, especially if they have industry-recognized certifications like ISO 9001.