Importance of Machining Parts
CNC machining parts are key to all industries because of their high accuracy, repeatability, and precision. These machining parts are prevalent across industries because they are cost-effective for demanding applications. CNC machinists and product engineers manufacture parts using cutting-edge CNC technology, which includes automated machining operations.
This guide discusses machining parts, their compatible machining techniques, benefits, and design principles. You will also learn about the materials used for machining parts, their applications, and helpful tips for choosing the right machining parts manufacturer.
1. What are Machining Parts?
If you look around, you will find different machining parts everywhere. Manufacturers create these parts through a machining process where specialized cutting machines (including milling machines, milling machines, and lathes) use sharp cutting tools to gradually remove excess material from a workpiece bar to form the desired shape.
These digital manufacturing processes include CNC drilling, milling, turning, and grinding, which are used to cut a piece of material into the desired shape or part. Typically, Machining Parts can be manufactured through manual or automated (computer numerical control) machining. However, machinists now use computer-aided design to produce custom Machining Parts.
Additionally, you can make CNC parts from any metal alloy, plastic, or any other material that can be cut without significant degradation.
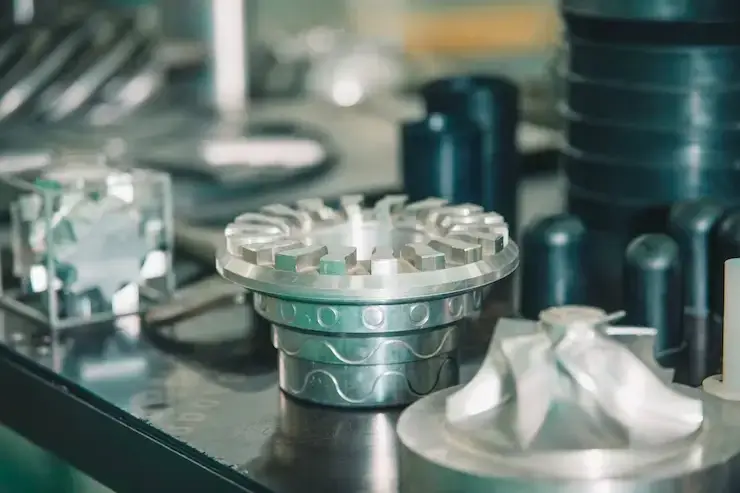
2. Machining Techniques and Processes
Manufacturers and machinists employ different CNC machining processes to produce parts for different purposes. The following are standard manufacturing techniques and methods used to achieve different results:
• Milling: This subtractive manufacturing process involves using a CNC milling machine to remove material from the workpiece to form a CNC part with a contour or flat surface. Common types of milling operations include CNC milling, face milling, and end milling. These machining processes involve the use of a variety of milling machines and cutting tools.
• Turning: This metal cutting process involves rotating a workpiece bar while feeding a cutting tool to remove material and machine cylindrical shapes. CNC turning is a reliable method for machining threads, shafts, and complex features on the outer surface of machining parts.
• Drilling: The drilling process uses a rotating drill bit to drill holes in the workpiece. This is a basic process commonly used in industry to drill holes in machining parts and components, with varying sizes and depths.
• Broaching: This is a process that uses a specialized tool called a broach to cut material in a controlled manner. Machinists use broaches to create splines, keyways, and other complex internal shapes.
• Grinding: Grinding involves using a grinding wheel to cut material from the surface of a machined part to achieve a high degree of precision and a smoother surface.
• Electrospark machining (EDM): This machining technology uses electrical sparks to cut material from a workpiece to form a specified shape. This process can meet the high precision required for machining complex shapes or hard materials.
• Laser cutting: Laser cutting uses a high-powered laser beam to blow, vaporize, or melt material to make precise cuts on a workpiece. This is a technology suitable for cutting plastics, metals, and other materials.
• Ultrasonic machining: This technology uses ultrasonic vibrations and abrasive slurries to remove material from the surface of a workpiece. It is ideal for machining delicate and brittle materials.
3. What are the advantages of machining parts?
CNC parts and components have advantages over 3D printing and injection molding parts. This section discusses the typical advantages of machining parts:
1) Excellent prototypes
CNC machining technology can provide machining parts and prototypes with complex designs and intricate features. These machined prototypes are ideal and affordable because they can be machined in one-off quantities.
In addition, since CNC machining is digital and faster, it is easier to quickly replicate sheet metal parts. Therefore, you can perform necessary testing and evaluation of prototypes before manufacturing the final product.
In addition, the material versatility of machining enables you to order machined prototypes and parts in different metal alloys or composite plastics to check which part performs best after considering all relevant factors.
2) No Minimum Order Quantity
One of the significant advantages of Machining Parts is that you can purchase them without a minimum order quantity. You can easily machine parts from workpiece bar stock, making small batches or one-off parts cost-effective. Therefore, you can easily order the exact number of Machining Parts you need.
CNC machining is almost unique in producing quality parts without minimum order quantity requirements or risk of excess inventory. Therefore, it is ideal for prototyping, small batch production, and small companies.
3) Strength
Machinists make machine parts from solid materials called blanks. These are usually extruded or cast materials. Therefore, machining parts are stronger than other parts such as 3D printed parts. Likewise, molded parts are not as strong as machining parts because molded parts typically have thin walls and limited mechanical properties.
4) Design Freedom
Machine-machining parts allow for unhindered design freedom, allowing for different design features such as shape and size. These parts typically have fine and detailed features, even though they may be thick and strong.
CNC machining remains one of the most versatile manufacturing methods for geometries because it can handle design requirements such as fine details, complex features, or complex geometries. As a result, machining parts have complex design features that meet the needs of a wide range of applications.
5) Faster Delivery Time
CNC machining technology manufactures metal and plastic parts faster than other manufacturing processes such as molding. Although CNC machining parts do not use labor-intensive tools, the production process is highly efficient.
Some CNC machines are equipped with faster machining centers that are equipped with linear guides and have fast machining speeds. In addition, the speed of CNC machining centers and the one-step nature of the machining process can shorten the delivery time of machining parts.
6) Surface Finishing
CNC parts allow for higher surface finishing standards with moderate post-processing operations. Additionally, machining provides superior surface finishes because it leaves no visible layer lines. CNC machining parts and assemblies are compatible with a wide range of surface finishing, allowing your parts to meet design specifications and perform well.
7) Quality
Generally speaking, machining parts are manufactured to very high standards due to the precise control of CNC machines. These precision machining parts typically provide fine surface finishes and tighter tolerances to meet your design requirements. However, customers can indicate the tolerance requirements that the machinist needs to achieve. As a result, it may take longer for the machine operator to machine tight tolerance parts and corresponding features.
8) Easy Modification
Since CNC machining parts are created from digital CAD files, you can easily make digital design changes at any stage of production. This feature is beneficial for R&D and prototyping when product developers and engineers have to make minor modifications to machining parts to make various versions. It helps reduce material waste because machining parts are typically defect-free.
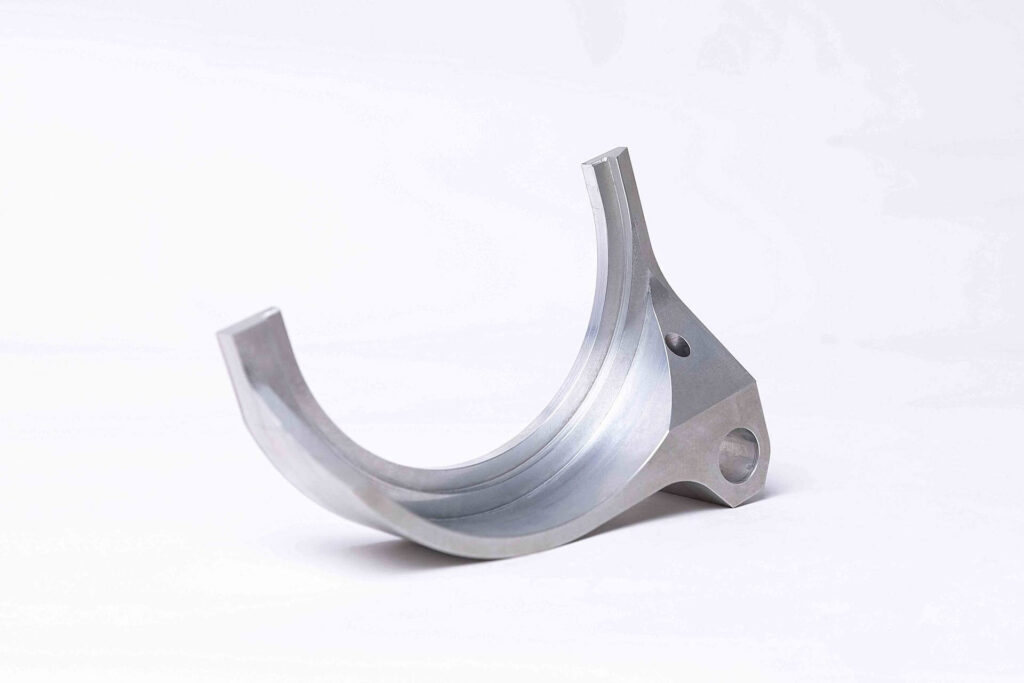
4. Design principles for machining parts
Generally, when machining parts, it is recommended to follow the Design for Manufacturing (DFM) principle. That is, design the part according to the intended manufacturing process.
However, you can easily design Machining Parts by following the following design principles:
1) Wall Thickness
Thin walls are not suitable for machining parts because it affects performance. Therefore, make sure your machined part design does not have thin wall thickness. However, if thin walls are critical to your design, it is better to use injection molding to manufacture the part.
2) Undercut
An undercut is a complex cut that requires the use of standard cutting tools because a part of the part blocks it. They require special machining design considerations and special cutting tools, such as T-shaped machining tools.
However, since these tools have standard sizes, the undercut size must be in whole millimeters to correspond to the cutting tool. Undercuts can vary from 3 to 40 mm, and the undercut depth is exactly twice the width, depending on the machining tool. Nonetheless, if undercuts can be avoided, you can machine parts faster and with less work.
3) Cavities, Holes, and Threads
When drawing the design drawings of machining parts, it is important to remember that cavities and holes depend on the cutting tool. You can machine cavities and grooves into the part to a depth of about four times the width of the cavity. It is important to know that deeper cavities necessarily require rounded corners rather than sharp edges due to the required cutting tool diameter.
In addition, the depth of a hole drilled with a drill should not exceed four times the drill width. Likewise, the diameter of the hole must match the standard drill size as closely as possible. On the other hand, the depth of threads used to integrate fasteners such as screws should not exceed three times the diameter.
4) Scale
The size of CNC Machining Parts is actually limited, as you have to manufacture them within the build envelope of the machine. CNC milled parts must be precisely sized to 400 x 350 x 150 mm, while turned parts should have a maximum size of Ø 500 mm x 1000 mm.
However, it is good to note that larger sizes are achievable with larger machines, but this must be discussed with the machinist before production begins.
5) Protrusions
Making high protrusions is often difficult, as thin walls can damage the part or lead to reduced precision. Therefore, it is important to keep the height of the protrusion to no more than four times its width.
5. Machined Part Materials
CNC machining parts are often made of a variety of materials, such as metal alloys and plastics. However, some materials are easier to machine, while others are complex. Rigid materials are difficult to cut and may cause tool chatter and vibration, which can affect workpiece quality.
On the other hand, very soft materials and materials with very low melting points tend to deform easily when interacting with cutting tools.
The following are typical machined part materials:
• Metals: Titanium, Bronze, Brass, Copper, Aluminum, Stainless Steel (17-4, Inconel 625 and 718), Zinc, Magnesium.
• Plastics: ABS, PC, POM, ABS+PC, PP, PMMA (Acrylic), PS, PEEK, HDPE, DHPE, PPS, Teflon, PAGF30, PCGF30.
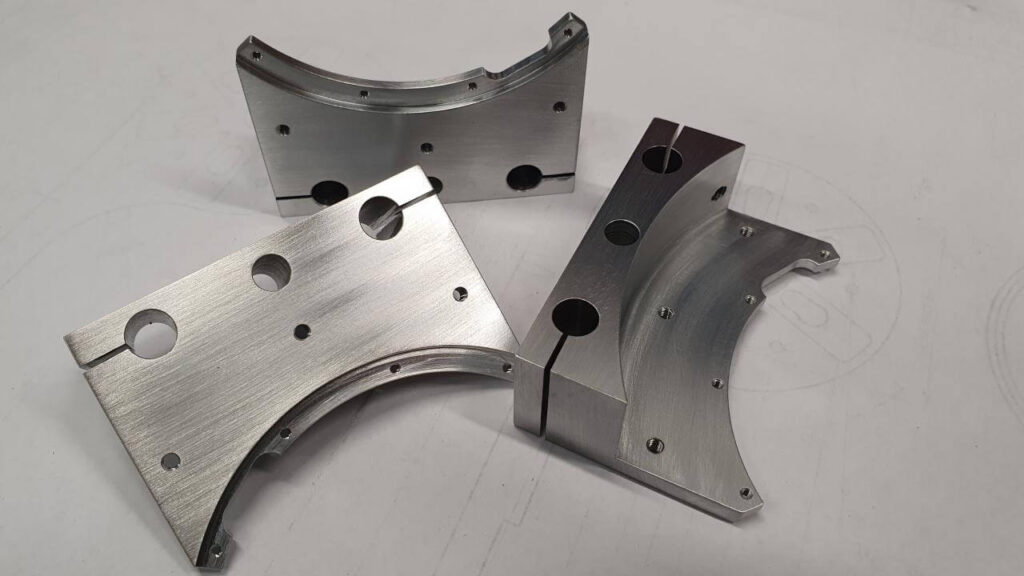
6. Machined Part Surface Finish
A variety of compatible post-processing operations help enhance the surface texture and functionality of machining parts.
The following are some standard machined part surface finishes:
• Post-machining: Post-machining finishing options do not involve surface treatment of the machining parts. It is the precise surface condition of a machined part when it leaves the CNC machine. It is often well suited for many internal non-decorative functional parts.
• Powder coating: The powder coating process involves spraying a powder coating of any preferred color onto the machined part and then baking it. It forms a strong coating on the machined part that improves its wear resistance. This coating is more durable than ordinary paint coatings.
• Anodizing: This electrochemical process improves the corrosion resistance of aluminum machining parts. It forms a scratch- and corrosion-resistant layer on the metal part. The Type II anodizing process provides a corrosion-resistant coating on aluminum machining parts. In contrast, Type III anodizing forms a thicker coating on the machined part that has better wear and chemical resistance.
• Sandblasting: Sandblasting involves spraying abrasives (fine beads) at high speeds onto the surface of the machined part. This process helps remove sharp edges, burrs, and residual material. However, you can modify this process to achieve a certain degree of roughness. However, sandblasting may not be compatible with fine features because the process removes material and affects the geometry of the machined part.
7. Machined Part Tolerances
Manufacturers use modern CNC machines to create machining parts with tighter tolerances. While non-machined parts and prototypes can use looser tolerances, tight tolerances can be critical for machined parts that must interact with other components. The following is a table of CNC machining tolerances:
8. What are the applications of machining parts?
CNC machining parts and components have become indispensable and therefore suitable for a variety of applications across industries. Typical machined components used in different applications include valve bodies, ball joints, rollers, housings, gears, fasteners, brackets, etc.
The following are common industries that use machining parts:
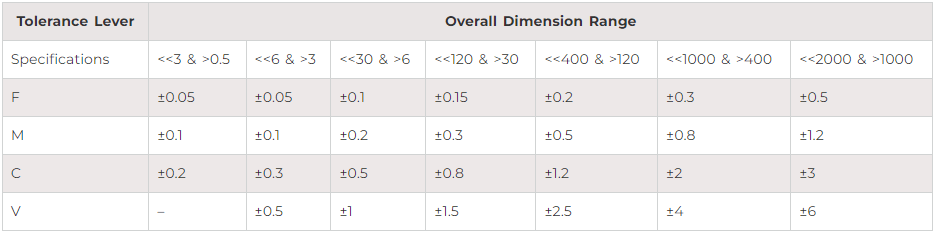
1) Aerospace
Due to the high precision requirements of the aerospace industry, engineers in the aerospace industry rely on machining parts such as engine components, engine brackets, fuel plates, landing gear components, and prototypes. In aerospace machining, there is no room for the slightest deviation as this can lead to catastrophic failure. Therefore, precision machining parts in this field are crucial.
2) Medical
The medical industry has a variety of applications for machining parts and components. Precision machining is suitable for manufacturing stainless steel and titanium alloy machining parts, including implants, surgical instruments, medical devices, and other complex diagnostic equipment.
What’s more, machining techniques such as Swiss screw machining are well suited for machining medical components. Considering the safety and accuracy requirements of various medical procedures, machining medical components generally requires tighter tolerances.
Precision is crucial for implants as they must fit perfectly with the patient’s body. Therefore, CNC machining is the standard method for manufacturing these implants as it provides the required accuracy and helps achieve complex machined part geometries.
3) Automotive
The automotive industry relies on CNC machining to manufacture mechanical parts such as one-off custom parts, lighting components, engine blocks, pistons, gears, and steering systems.
Manufacturers in this field rely on cutting-edge machining methods, including five-axis CNC machining, to manufacture complex automotive machining parts with high precision and efficiency.
4) Consumer Products
Most household appliances and goods contain mechanical parts. In addition, sports equipment may be CNC machined, while consumer electronics use different machined metal and plastic parts because of their excellent conductivity.
Typical examples of machining parts in this application include sockets, laptop housings, electrical insulation materials, connectors, etc.
5) Other applications of CNC machining parts include:
• Military
• Robotics
• Electronics
• Renewable Energy
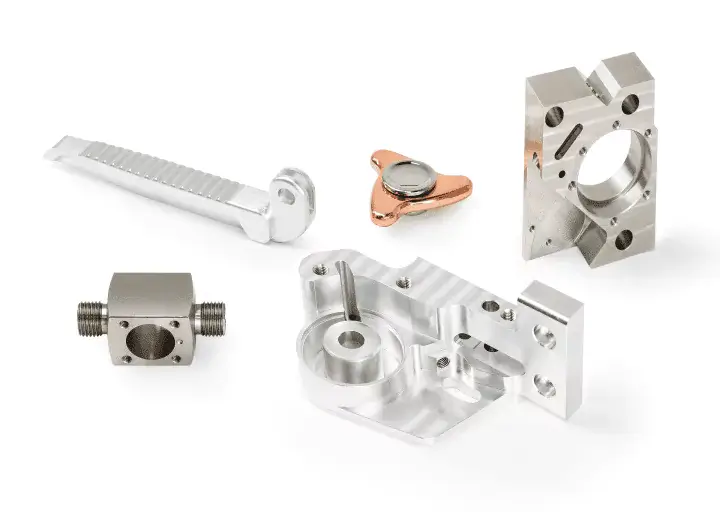
9. How to Choose a Machining Partner for Your machining parts
You need a reliable machining partner to outsource your CNC machining needs for small or large batches of machining parts or prototypes. Working with a third-party CNC machining service provider is often more advantageous than an in-house solution because of the large factory space and the expertise required to operate the machine tools and equipment.
While choosing a reliable machining partner for your machining parts can be quite challenging, here are some helpful factors and practices to consider:
• Certifications: While certifications won’t tell you the scope of a machining company’s capabilities, ISO certifications are useful because they are an important guide to identifying capable machining companies.
• Word of Mouth: It can be helpful to talk to other hardware companies in the area that have worked with machining parts manufacturers to get a sense of their outsourcing experience.
• Required Information: Make sure you ask all the questions you can until you are confident that the manufacturer can handle your project once you have established a relationship with them. However, if they cannot answer your questions convincingly, they may not be the right manufacturing partner.
• Request Quotes: It is recommended to request quotes from different shortlisted machining companies, compare prices, and determine the company that is best suited for your project. This way, your CNC machining costs remain effective.
• Factory Tours: It is important to visit the factory of a potential manufacturing partner to understand how they operate and what machining tools and equipment they have. In some cases, it is feasible to have a manufacturing agent organize visits to multiple factories in a particular region.
Nevertheless, here are some other helpful tips to follow when dealing with outsourced machining parts manufacturers:
• Follow DfM guidelines: Make sure that the digital part design strictly adheres to machining guidelines, including limited depth holes, no thin walls, etc.
• Use common standards: Provide complete technical drawings with digital files to avoid ambiguity, and adopt common standards to prevent any kind of miscommunication.
• Confidentiality agreement: It is best to sign a non-disclosure agreement when outsourcing mechanical parts. This agreement legally prevents the manufacturer from sharing or using your design with any other party.
• Consider shipping time: If you have a tight deadline, it is recommended that you consider the shipping time of the outsourced parts. This is because outsourced parts take longer to arrive than in-house parts.
• Be prepared to pay: Manufacturers usually ask for an advance payment when processing the first order. However, they may allow you to purchase on credit for subsequent projects.
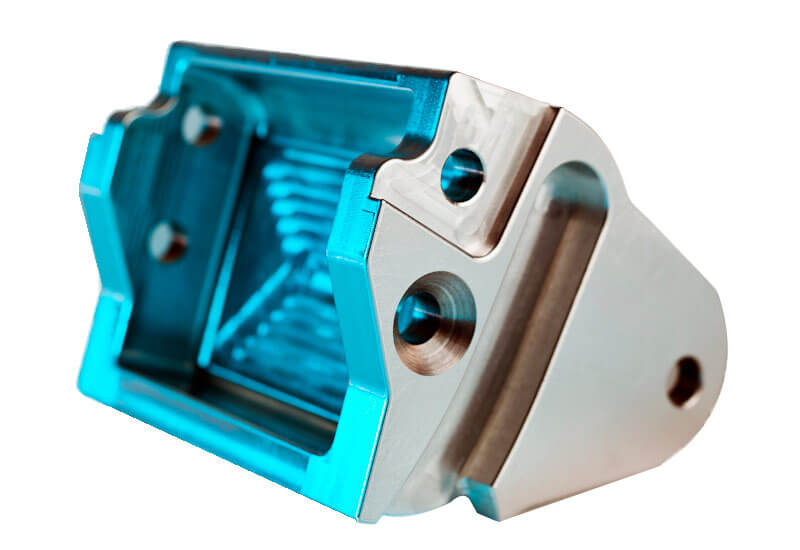
10. Conclusion
Machinery parts are designed in a variety of ways and have a wide range of uses; therefore, it is essential to understand the complexity of successfully realizing the technical drawings and production of the parts. However, by following DfM guidelines, considering material properties, and working with an experienced machining partner, you can easily create quality Machining Parts that meet your requirements.
Xavier Machining is a reliable partner for all CNC machining services to meet your rapid prototyping and machining parts needs. We provide high-quality parts and prototypes at competitive prices with shorter delivery times. Our efficient quality control system helps to bring your products to market faster. We have many years of extensive experience in producing machining parts for different industries. Our machine shop has advanced machinery and is equipped with a quality management system to produce high-quality machining parts with high precision and accuracy. Contact us today and let us help you with your machining parts!