The Ultimate Guide to Swiss CNC Machining
Since its development in 1870, Swiss machining has been a mainstay of the CNC industry. Although Swiss machining was originally developed for watch production, it is also used in other industries, especially in the medical field for the machining of bone screws.
Swiss machining is a manufacturing technique that uses specialized tools to cut and design materials into complex parts, slender or precision components. It is ideal for producing parts that require extremely high precision machining, and therefore has applications in various industries such as medical, automotive, hydraulics, aerospace, firearms, and electronics.
So, what are the benefits of using Swiss CNC machining compared to other types of machining? What are the applications of this manufacturing technique? Read on as we provide you with the answers to these questions and other important information about Swiss machining.
1. What is Swiss Machining?
CNC Swiss machining is one of the best ways to manufacture precision parts. Swiss machines have a sliding headstock that works in conjunction with a guide bushing. The purpose of this guide bushing is to provide stability to the bar stock along all axes, including the longitudinal axis. With stability guaranteed, it becomes easier to machine complex slots, threads, holes, and multiple diameters on the workpiece.
These CNC components of Swiss turning centers make the entire machining process highly automated. It ensures that all machined parts precisely meet tight tolerance requirements.
Now that we have a general idea of what Swiss machining means, when would you adopt this manufacturing technology?
• When the best quality finish is important: Swiss machining is ideal when you need to achieve a high quality finish. The quality of finish achieved through this machining eliminates the need for secondary finish applications.
• When high accuracy and high volume are essential: The accuracy of CNC machines is extremely high. This makes this technology ideal for use in situations where accuracy and precision are critical. In addition, combining the accuracy of advanced machines with the precision of skilled operators allows for the manufacture of high volumes of precision parts.
• When producing highly complex parts: With Swiss machines, it becomes easier to machine complex geometries of tiny diameter parts. It also achieves this through a high level of Swiss precision machining.
• When cost-effectiveness is a factor: As manufacturing volumes increase, the CNC Swiss machining process becomes less expensive. This makes it an ideal manufacturing technology for mass production of precision parts.
• When components require turning and milling functions: With Swiss CNC machining, multiple setups are not required. Let me explain that using this technique, a number of milled features can be given to a part during the turning process, including hexagonal edges, flats, and slots, which eliminate the need for milling.

2. What materials can be used in CNC Swiss machining?
There is a wide variety of materials that manufacturers use for Swiss-type lathes. They use these materials for a variety of reasons, including cost-effectiveness, corrosion resistance, conductivity, and more. Let’s take a look at the most commonly used materials for CNC Swiss-type machining.
1) Brass
This material is non-magnetic, non-sparking, and low-cost. Engineers use this material for CNC Swiss machining because of its structural integrity, corrosion resistance, and excellent conductivity. In addition, it produces parts with tight tolerances and high strength.
2) Tool Steel and Carbon for Swiss-Type Lathes
The versatility, strength, and alloy properties of carbon steel make it a preferred material for CNC Swiss-type lathe manufacturing. The combination of this material and Swiss lathes is ideal for producing brackets, bushings, sockets, screws, shafts, and connectors in a cost-effective manner.
3) Stainless Steel
Using stainless steel for this manufacturing technique gives the parts durability and corrosion resistance. This makes stainless steel an ideal material for manufacturing complex parts for the automotive, aerospace, military, and medical industries.
4) Bronze
Swiss machined bronze materials create durable parts that are wear-resistant and corrosion-resistant. These properties make bronze ideal for the consumer, electrical, industrial, and aviation industries.
5) Aluminum
This is the most commonly used material for CNC Swiss machining because it is the most cost-effective. Aluminum has properties that make it ideal for this technology, including corrosion resistance, light weight, high-precision machining, and excellent electrical conductivity.
6) Plastics
This material is also well suited to this manufacturing technique, especially rigid materials. Turning this material can produce fittings, screws, sleeves, housings, insulators, and custom bushings for a variety of industries.
7) Other materials include
1. Titanium: This is an ideal material for CNC Swiss machining due to its high ductility.
2. Copper alloys: Copper and copper alloys have excellent electrical conductivity, spark-free, corrosion-resistant, and non-magnetic properties, making them ideal for CNC Swiss machining parts.
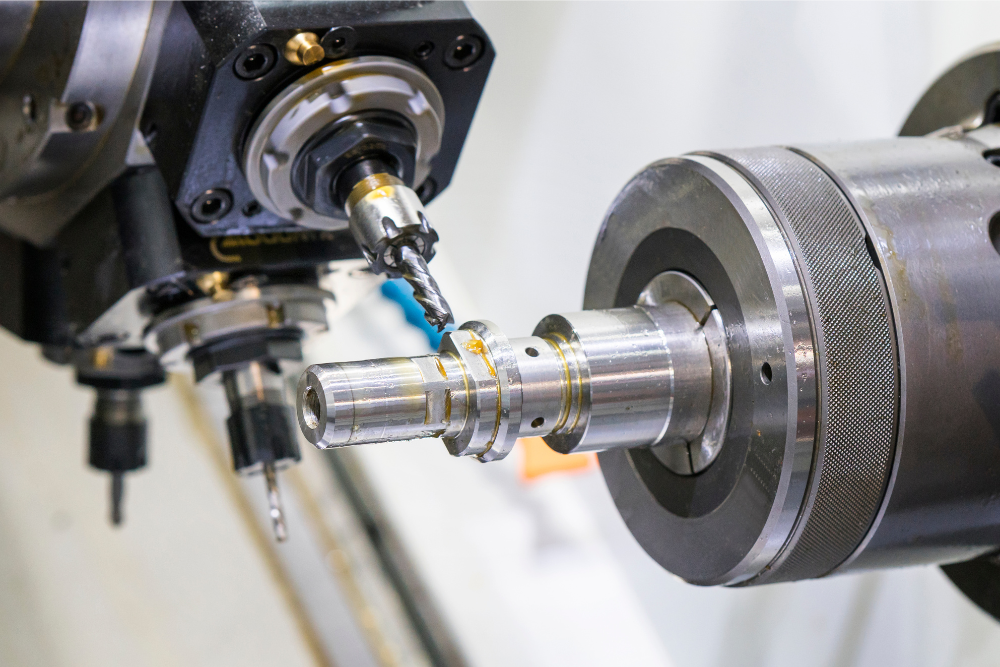
3. What are the benefits of Swiss machining?
Manufacturers can gain many benefits using Swiss machining technology. Here are the main benefits of this manufacturing technology:
• Short setup time: Since CNC Swiss machine parts combine milling and turning functions, it saves setup time for traditional turning while significantly reducing cycle time. This is mainly because there are fewer setups and manufacturers only need to set up one operation instead of multiple operations.
• Simplified machining process: Since CNC Swiss machines can perform multiple functions including sawing, drilling and milling, there is no need for secondary operations. Thus simplifying the entire machining process.
• High-volume production and shorter lead times: Due to the speed of Swiss-type lathes, lead times are shorter. This machine speed can produce parts in large quantities in a short period of time and at a lower cost.
• Low labor requirements: Through automated processes, Swiss CNC machines can run unmanned for hours at a time. This reduces labor costs for large-scale production while giving engineers time to focus on other details.
• Tight tolerances: Unlike traditional lathes, Swiss lathes hold the machined parts in place near the tool holder or machining area. This helps the machine maintain tight tolerances when designing or cutting small parts.
• High precision: Swiss-type machines do not produce multiple sections of bar stock at the same time. This helps increase precision while reducing the likelihood of errors with CNC Swiss-type machines.
4. What are some applications for Swiss machined parts?
Although originally developed for the manufacture of screws used in the watchmaking industry, including pocket watch production, the entire process is now used in a variety of industries. These industries include:
• Medical Industry: This industry often requires parts with high precision machining and accuracy, so it is not surprising that CNC Swiss machined parts are used. Swiss machined parts manufacturers use Swiss screw machines to create orthopedic bone screws, implants, and surgical screws.
• Aerospace Industry: Swiss machined parts are also used in the aerospace industry. Manufacturers machine flying metals such as aluminum alloys, alloy steels, and titanium to produce fasteners, flanges, fans, and other aircraft components.
• Defense Industry: With CNC Swiss turning, engineers can manufacture military products and parts that require extremely precise parts such as firing pins, cover pins, and rifles.
• Oilfield and Energy Industry: With CNC Swiss turning, engineers manufacture parts for the oil and gas industry. They use this technology to manufacture oilfield parts for tracking production and monitoring pipelines on offshore drilling platforms.
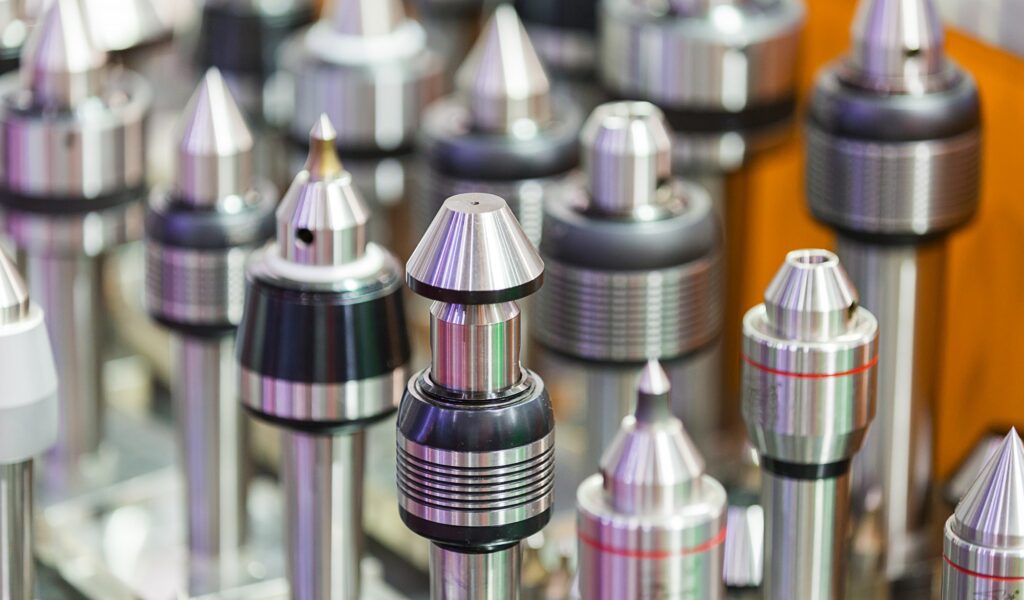
5. Conclusion
If you are looking for a cost-effective way to machine high-precision products and parts, then using a Swiss-type machine is one of the best options. If you are looking for a trusted and reliable contract manufacturer that provides Swiss machining services with fast turnaround times and the right quality certifications, contact Xavier Machining today.