Thermoforming Plastic Best Practices: Process, Benefits, Applications
As an important processing technology, thermoforming plastic plays a key role in modern manufacturing. Thermoforming can transform thermoplastic sheets into products of various shapes to meet different functional and design requirements. This article will explore the working principle, advantages and disadvantages of thermoforming in depth to help users better understand this technology.
1.What is thermoforming
Thermoforming plastic is a plastic manufacturing process that heats a thermoplastic sheet to its softening point, stretches it onto a mold to form the desired shape, and then cools it to solidify and trim it to its final shape. It is versatile, cost-effective, and can produce both thin and thick products.
2.How thermoforming plastic works
The three typical heating methods used in thermoforming plastic include convection heating, radiation heating, and direct contact heating. Convection heating raises the temperature by circulating hot air around the thermoplastic sheet; radiation heating uses infrared radiation to directly heat the sheet; and direct contact heating transfers heat by bringing the sheet into direct contact with a heated surface. These methods allow the sheet to reach the desired temperature and become pliable for forming on or in a mold.
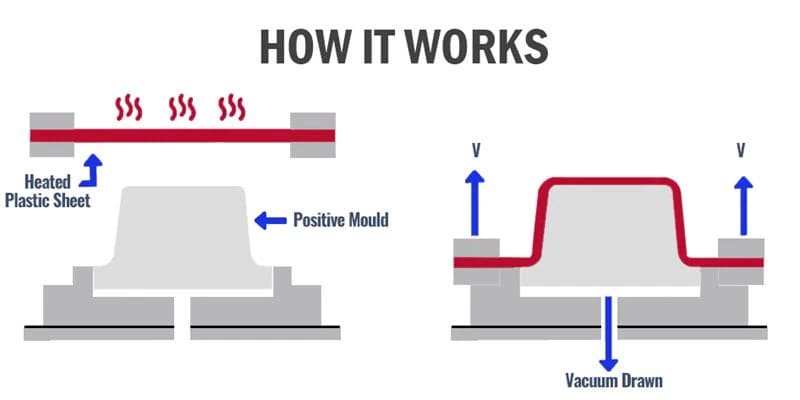
3.Common processes for thermoforming plastic
1.Vacuum forming
It is cost-effective and suitable for packaging, automotive parts, consumer products and other fields. It can process materials such as polystyrene (PS), polyethylene (PE), polypropylene (PP), PVC, PET, PETG, etc.
2.Pressure forming
It is suitable for automotive parts, aerospace parts, industrial applications and other fields. It can process materials such as ABS, polycarbonate (PC), polypropylene (PP), PVC, etc.
3.Mechanical forming
It is suitable for automotive parts, heavy applications, industrial parts and other fields. It can process materials such as ABS, polycarbonate (PC), polypropylene (PP), PVC, etc.
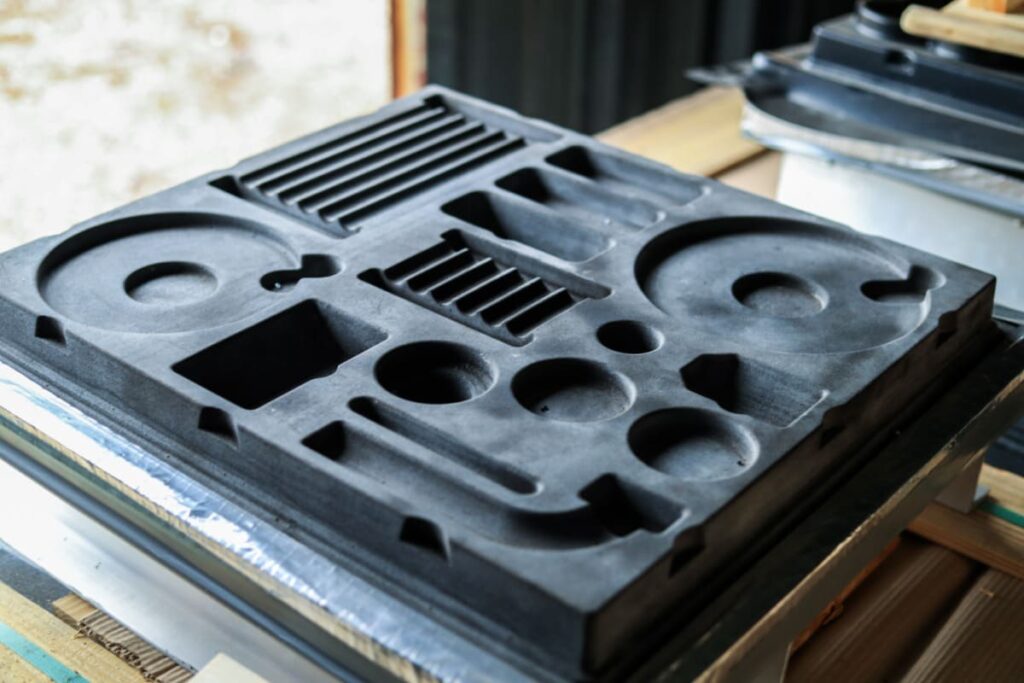
4.Double-piece forming
It is suitable for automotive parts, industrial housings, medical equipment and other fields. It can process materials such as ABS, polycarbonate (PC), polyethylene (PE), polypropylene (PP), etc.
5.Compression molding
It is suitable for thin-walled containers, consumer product packaging, electronic product housings and other fields. It can process materials such as PS, PET, PVC, polypropylene (PP), ABS, etc.
6.Drape molding
Applicable to display racks, signs, artworks and decorations, etc., and can process materials such as acrylic (PMMA), PETG, PVC, etc.
7.Strip heating
Applicable to automotive interior panels, aircraft parts, home appliance parts, etc., and can process materials such as ABS, polycarbonate (PC), polypropylene (PP), PVC, etc.
4.Uses of Thermoforming plastic
1.Packaging Industry
Thermoforming plastic is widely used in the packaging field and is used to make various packaging solutions such as trays, clamshell packaging, blister packaging, etc., providing product protection, visibility and customization options for food, electronic products, cosmetics and medical supplies.
2.Automotive Industry
Thermoforming plastic plays an important role in the manufacture of automotive interior and exterior parts, and can produce components such as dashboards, door panels, console elements, body panels, spoilers, grilles and wheel arch linings, with the advantages of reducing weight, improving design flexibility and saving costs.
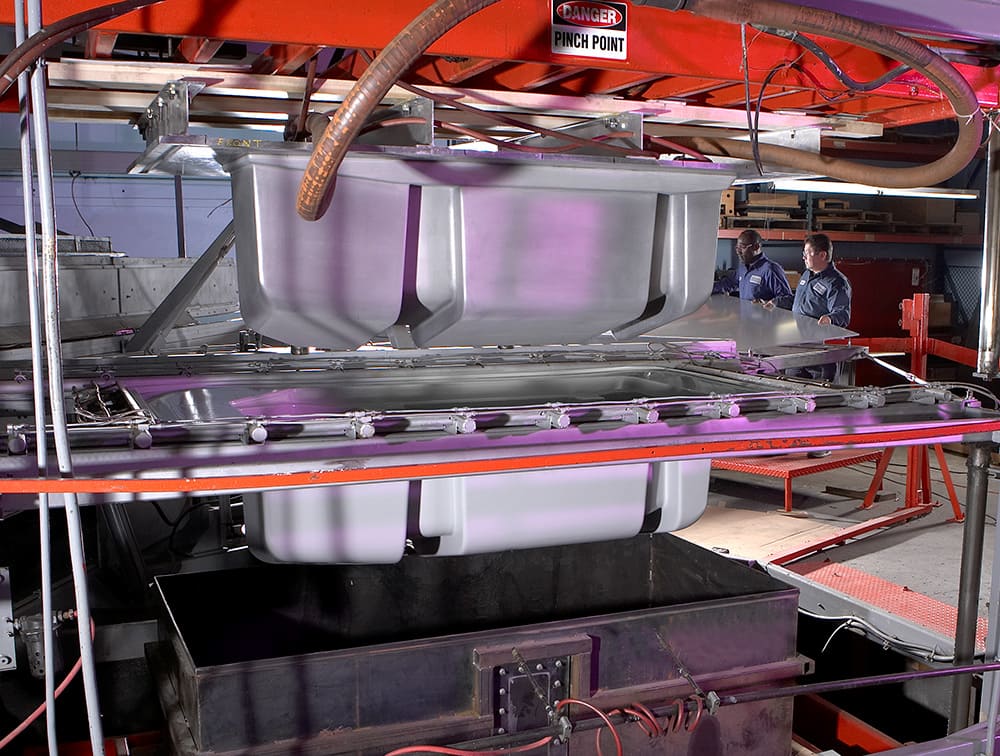
3.Consumer Products
It is used to produce consumer products such as electrical housings, electronic product housings, point-of-sale displays and product housings, with durability, aesthetics and brand elements.
4.Aerospace Industry
The manufacture of lightweight components such as interior panels, seat backs and tray tables helps reduce the total weight of aircraft and improve fuel efficiency and performance.
5.Healthcare Industry
It is widely used in the healthcare field to produce medical device components, surgical trays, pharmaceutical packaging and patient care products, with sterilizability, hygiene and precise customization.
6.Industrial Manufacturing
In the fields of machinery, electronics and construction, it is used to manufacture protective covers, equipment housings, electrical component housings and industrial pallets.
5.Advantages of Thermoforming plastic
1.Cost-effective
Particularly suitable for mass production, the initial tool cost is relatively low, the equipment is simple and the setup time is short.
2.Strong design flexibility
Complex shapes, details and different wall thicknesses can be produced, suitable for deep drawing, undercutting and textured surfaces.
3.Good material versatility
Can be used with a variety of thermoplastic materials, and the appropriate material can be selected according to the product characteristics.
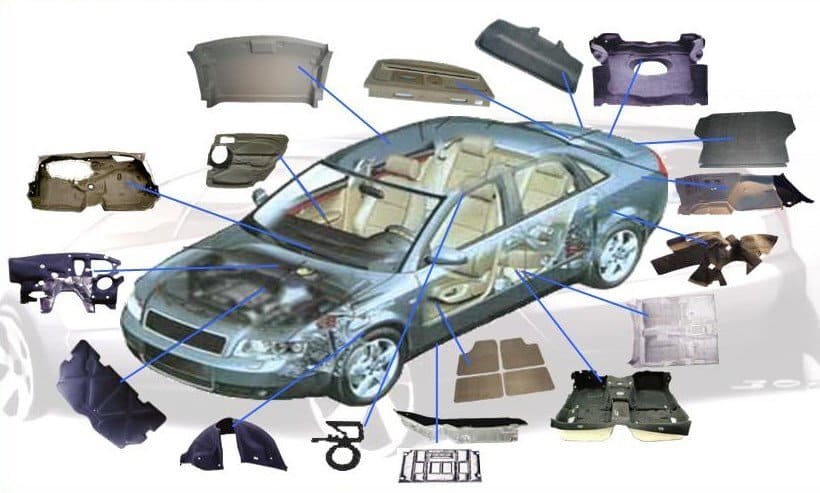
4.Fast turnaround
The heating and cooling stages are relatively fast, and the production cycle is short, which can quickly achieve from design to finished product.
5.Strong scalability
Can adapt to small and large batches, and the mold cost is usually lower than other processes.
6.High material efficiency
Can reduce material waste, and excess materials can usually be recycled.
7.Many surface treatment options
Including gloss, matte, texture and pattern, etc., to enhance the beauty of the product.
6.Disadvantages of Thermoforming plastic
1.Limited material selection
Compared with processes such as injection molding, there may be limitations, and some advanced engineering-grade plastics are not suitable for thermoforming plastic.
2.Large thickness variation
Can cause wall thickness variations in deep drawing or complex parts, affecting product structural integrity and performance.
3.High cost of complex design molds
As part complexity increases, mold requirements become more complex and costs increase.
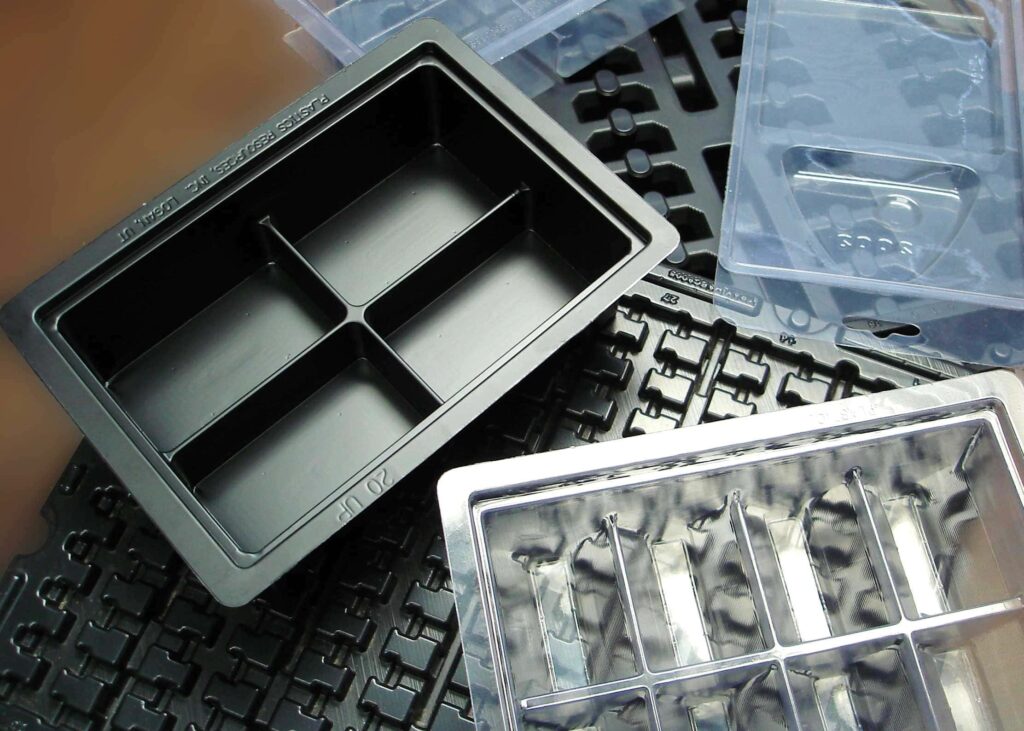
4.Limited part size
Usually more suitable for the production of medium to large parts, and very large parts may be challenging.
5.Limited precision
Compared with processes such as CNC machining or injection molding, there may be limitations in achieving extremely tight tolerances and complex features.
6.Surface defects
Minor surface defects such as flow lines, mesh structures or texture changes may occur, and some applications may require additional finishing operations.
7. Commonly used thermoforming plastic materials
1.Polystyrene (PS)
Low price, high transparency, easy processing, widely used in packaging applications, disposable food containers and consumer products.
2.Polyethylene (PE)
Available in various forms, such as low-density polyethylene (LDPE) and high-density polyethylene (HDPE), with impact resistance, moisture resistance and chemical resistance, used in packaging, automotive parts and industrial applications.
3.Polypropylene (PP)
High strength, chemical resistance and heat resistance, used in packaging, automotive parts and consumer products, can be processed by thin and thick thermoforming technology.
4.Polyvinyl chloride (PVC)
Durable and versatile, with chemical resistance and weather resistance, used in packaging, automotive parts, building materials and medical products.
5.Acrylonitrile butadiene styrene (ABS)
Rigid and impact-resistant, commonly used in automotive parts, electronic housings and consumer products, providing a balance of strength, toughness and surface finish.
6.Polycarbonate (PC)
Transparent and strong, strong impact resistance, used in automotive lighting, medical equipment and electronic components.
7.Polyethylene terephthalate (PET)
Transparent and lightweight, known for its excellent clarity and barrier properties, used in packaging applications, especially in the food and beverage industry, and also in blister packaging and clamshell packaging.
8.Polyethylene terephthalate glycol (PETG)
A modified form of PET with higher impact resistance and flexibility, used in applications requiring durability and clarity, such as medical packaging, electronic product housings and point-of-sale displays.
9.Polyvinylidene chloride (PVDC)
Known for its excellent oxygen and moisture barrier properties, used as a coating in thermoformed packaging to extend the shelf life of products and protect them from external factors.
10.Polylactic acid (PLA)
Biodegradable, renewable thermoplastic derived from plants, used in environmentally friendly applications such as disposable packaging, food containers and compostable products.
11.Polyamide (PA)
Commonly known as nylon, it has excellent strength, toughness and chemical resistance, and is used in thermoforming plastic applications requiring high mechanical properties, such as automotive components, industrial parts and electrical housings.
12.Ethylene Vinyl Acetate (EVA)
Flexible and resilient, with cushioning and shock-absorbing properties, used in applications such as footwear, protective pads, and medical products.
13.Polymethyl Methacrylate (PMMA)
Also known as acrylic, a transparent material with excellent optical clarity and weather resistance, used in applications where aesthetics and visual appeal are important, such as signage, display cases, and lighting.
8.Summary
Thermoforming plastic is a manufacturing process with broad application prospects and plays an important role in multiple industries. It has the advantages of high cost-effectiveness, flexible design, and strong material versatility. In practical applications, it is necessary to comprehensively consider the advantages and disadvantages of thermoforming according to specific project requirements and select a suitable manufacturing method.