Thermoplastic Injection Molding: Processes, Materials and Applications
As a mature manufacturing process, thermoplastic injection molding plays a key role in meeting the industry’s demand for efficient and precise methods of manufacturing plastic parts. It can transform thermoplastic polymers into durable parts of various shapes and sizes, and is widely used in many industries such as automotive, medical, electronics, packaging, etc. This guide will analyze thermoplastic injection molding in depth and give you a comprehensive understanding of the charm of thermoplastic injection molding technology.
1.What is Thermoplastic Injection Molding?
Thermoplastic injection molding is a process where a thermoplastic polymer is melted, injected into a mold, and cooled to form a solid shape. It is a key method for producing a variety of plastic parts, from simple household items to complex automotive components.
2.Thermoplastic Injection Molding Steps
1.Material Selection
Select appropriate thermoplastic polymers such as polyethylene, polycarbonate, etc. according to the function, aesthetics and service life of the parts.
2.Material Preparation
Dry the original plastic pellets to remove moisture and then load them into the injection molding machine hopper.
3.Melting
Heat the plastic pellets in the barrel to turn them into a molten state, and precisely control the temperature to achieve the desired viscosity and flow characteristics.
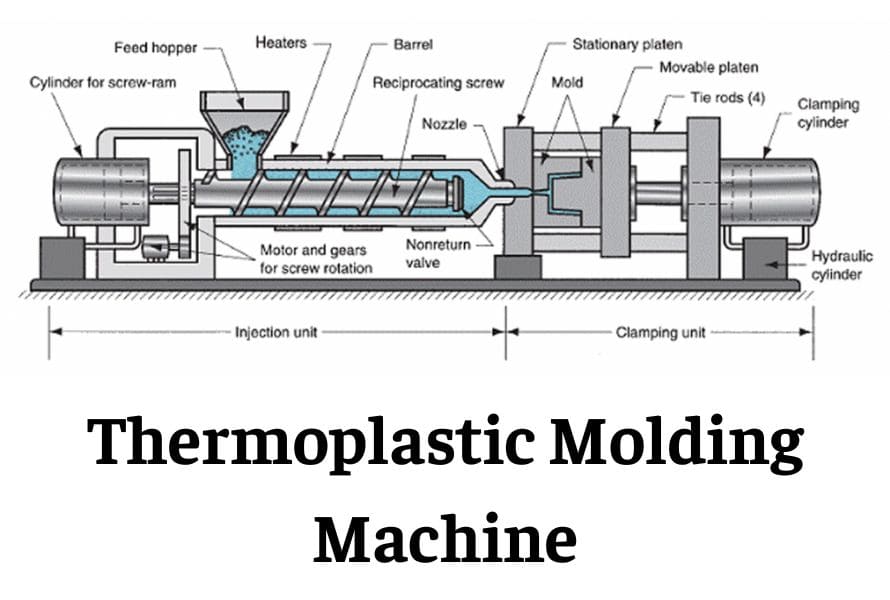
4.Injection
Push the molten plastic into the mold cavity under high pressure, and carefully calibrate the injection pressure and speed to ensure the shape and surface finish of the parts.
5.Cooling and Solidification
The plastic cools and solidifies in the mold. The cooling time is affected by the thickness and thermal properties of the thermoplastic and is critical to the integrity of the part.
6.Ejection
Use the ejector pin to eject the cooled part from the mold, and precisely control the ejection time and force to ensure the quality of the finished product.
7.Post-processing
Includes trimming excess material, polishing surface finish and painting to enhance the appearance and function of the parts.
3.Machine tools for thermoplastic injection molding
Key components of thermoplastic injection molding machines:
Clamping unit: responsible for firmly holding the two halves of the mold together during the injection molding process, applying enough force to offset the high pressure of the molten plastic.
Injection unit: plastic material is melted here and injected into the mold cavity, consisting of a heated barrel and a reciprocating screw.
Pressure holding and cooling system: maintain the pressure of the molten plastic in the mold so that it fully occupies the cavity and solidifies into the desired shape. Effective cooling can shorten the cycle time and improve the quality of parts.
Ejection process: the finished part is pushed out of the mold cavity using an ejector pin, and precision and timing are critical.
Mold tools: made of steel or aluminum, determine the shape, surface texture and size of the final product.
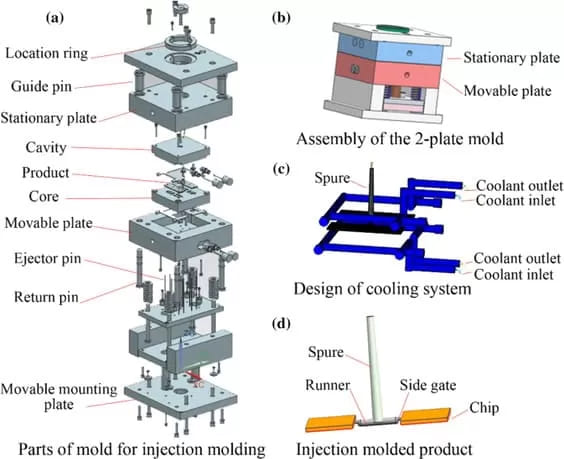
Mold type tools
Double-plate mold: the most common type of mold, suitable for simple parts, cost-effective and easy to manufacture.
Three-plate mold: used for parts that require a more complex gate system, which can achieve automatic separation of the part from the runner system.
Stack mold: increase mold output and is suitable for mass production.
Tandem molds: Two molds in one machine that can be opened and closed independently, increasing production flexibility.
Series molds: Different parts of a product or different products are produced in one cycle, ensuring that the cavity is filled evenly.
Overmolding: Molding a layer of material over a previously molded part.
Insert molding: Molding a metal or other non-plastic part into a plastic.
Hot runner molds: Have a heated runner system that reduces waste and cycle time, but has higher maintenance and initial costs.
Cold runner molds: The runners and gates cool and solidify with the part, then are ejected and recyclable.
Swing-out molds: For parts with threads, have a swing-out mechanism.
L-shaped molds: Suitable for parts with vertical undercuts or protrusions.
Collapsible core molds: For complex parts with internal undercuts or threads.
Gas-assisted injection molds: For hollow or partially hollow parts, gas is injected to form the internal cavity.
In-mold decoration and labeling molds: Labels or decorations are embedded in the part during the molding process.
4.Thermoplastic Injection Molding Machine Parameters
1.Melt temperature: usually 200°C to 300°C, affecting the viscosity and surface finish of the plastic.
2.Mold temperature: usually between 20°C and 120°C, affecting the cooling rate and crystallinity, reducing defects such as warping or shrinkage.
3.Injection pressure: usually between 500 and 1500 bar, ensuring that the molten plastic is pushed into every part of the mold, replicating complex details and achieving high-quality surface finish.
4.Holding pressure: slightly lower than the injection pressure, compensating for material shrinkage when the plastic cools, maintaining part size and integrity.
5.Injection speed: varies according to the complexity of the part, affecting the filling pattern and appearance.
6.Cooling time: a few seconds to a few minutes, depending on the thickness of the part and the thermoplastic material, determining the cycle time and dimensional stability.
7.Back pressure: 5 to 20 bar, improving color dispersion and removing air from the material.
8.Screw speed: 100 to 200 RPM, affects the quality of the plastic melt.
9.Ejection speed and force: precisely controlled to prevent deformation or damage to the finished part.
10.Dwell time: minimized to prevent thermal degradation and maintain the mechanical properties of the material.
11.Clamp force: several tons to several thousand tons, offset high injection pressure and prevent mold flash.
12.Injection volume: precisely calibrated amount of plastic injected into the mold, determines the weight and volume of the finished product.
13.Nozzle temperature: usually similar to the melt temperature, to maintain plastic fluidity and consistency.
5.Commonly used materials for thermoplastic injection molding
1.Acrylonitrile Butadiene Styrene (ABS): Strong toughness, good impact resistance, high dimensional stability, used in automotive parts, consumer electronics and toys.
2.Polyethylene (PE): Flexible, chemically resistant, available in a variety of densities, used in containers, pipes, and household items.
3.Polycarbonate (PC): It has high impact strength, good transparency and remarkable heat resistance. It is used for eyeglass lenses, bulletproof glass and medical equipment.
4.Polypropylene (PP): It has good chemical resistance, elasticity and fatigue resistance and is used in automobile parts, packaging and textiles.
5.Polyamide (nylon): High strength, high temperature resistance, and excellent wear resistance. Used in automotive parts, mechanical parts, and consumer products.
6.Polyvinyl chloride (PVC): Durable, chemically resistant and flame retardant, used in water pipes, medical pipes and outdoor furniture.
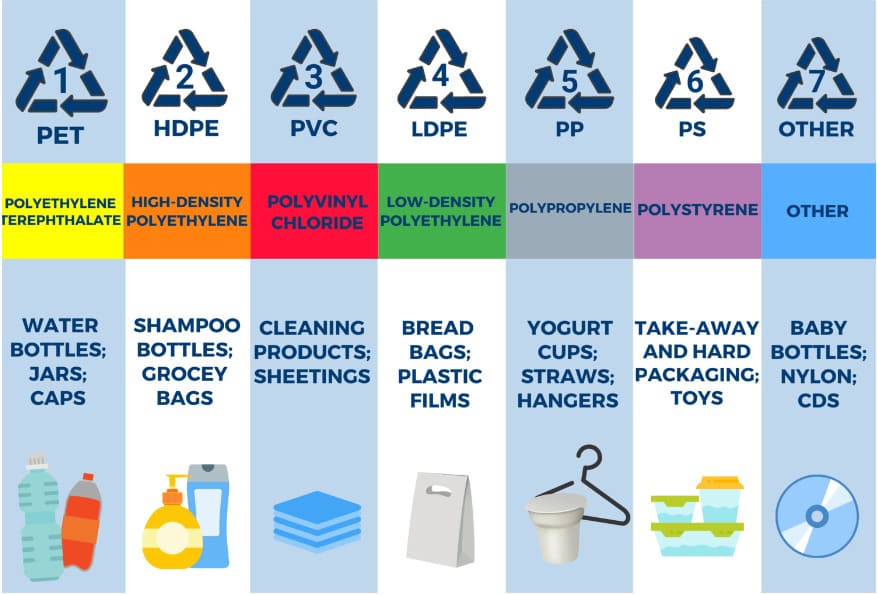
7.Polyethylene terephthalate (PET): Transparent, high strength, safe for food contact, used in beverage bottles, packaging and synthetic fibers.
8.Acrylic (PMMA): High optical transparency, weathering and UV resistance, used for signs, lamps and window panels.
9.Polystyrene (PS): Light weight, cost-effective, high definition, used in disposable cutlery, CD cases and insulation.
10.Thermoplastic polyurethane (TPU): Elastic, oil- and abrasion-resistant, used in footwear, medical devices and automotive parts.
11.Polyoxymethylene (POM): High stiffness, low friction, good dimensional stability, used in precision parts, electrical components and consumer products.
12.Polybutylene terephthalate (PBT): It has good electrical properties, strong heat resistance and chemical resistance, and is used in electrical components and automotive parts.
13.High Impact Polystyrene (HIPS): High impact resistance, easy to process, used in model building, signage and product housing.
14.Thermoplastic elastomers (TPE): Combine plastic and rubber properties to make them flexible and stretchable and used in seals, gaskets and soft-touch components.
15.Polyphenylene ether (PPO): High heat resistance, dimensional stability and good electrical insulation properties, used in automobile parts, electrical components and appliances.
16.Liquid crystal polymer (LCP): It has high mechanical strength, high temperature resistance, and good chemical resistance. It is used in high-performance electrical connectors and microwave cookware.
17.Polyetherimide (PEI): High heat resistance, strength and flame retardancy, used in aerospace, medical applications and electrical appliances.
18.Polyetheretherketone (PEEK): Excellent temperature resistance, chemical resistance and mechanical properties, used in aerospace, automotive and medical implants.
19.Polyphenylene sulfide (PPS): It has high temperature resistance, chemical resistance and dimensional stability. It is used in automotive parts, electrical components and coatings.
20.Styrene Acrylonitrile (SAN): Transparent, rigid and chemically resistant, used in food containers, kitchenware and bathroom accessories.
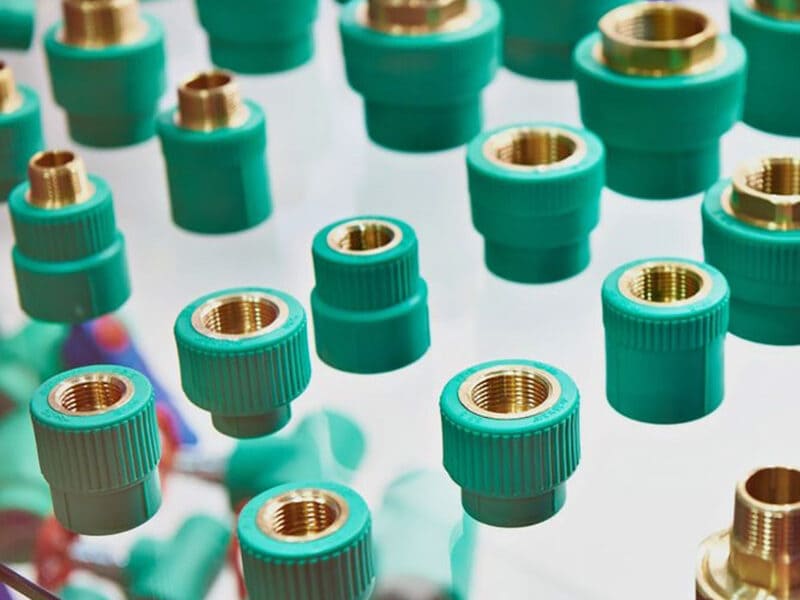
21.Ethylene vinyl acetate (EVA): Flexible, tough and transparent, recyclable, used in foam products, footwear and packaging films.
22.Polyurethane (PU): Wide range of hardness and flexibility, good durability, used in foam seats, wheels and tires, and car interiors.
23.Polyphenylsulfone (PPSU): High heat resistance, toughness and steam sterilization stability, used in medical devices, aircraft interiors and piping.
24.Polyimide (PI): Excellent heat resistance, electrical insulation properties and chemical resistance, used in high temperature electrical insulation, aerospace and semiconductor manufacturing.
25.Polyethylene naphthalate (PEN): Has better barrier, heat and chemical resistance than PET and is used in high-quality packaging and electronics.
26.Polybutylene (PB): Flexible, heat-resistant and pressure-resistant, used in piping systems and floor heating.
27.Polymethylpentene (PMP): Transparent and heat-resistant, used in laboratory equipment and microwave cookware.
28.Polysulfone (PSU): High temperature resistance, high strength, high transparency, used in medical devices, water films and electrical components.
6.Applications of Thermoplastic Injection Molding
Automotive industry
dashboard components, bumpers, door panels, under-hood components, etc.
Medical industry
disposable syringes, surgical instruments, medical device housings, diagnostic equipment components, etc.
Consumer electronics
smartphones, remote controls, computer component housings, battery housings and connectors, etc.
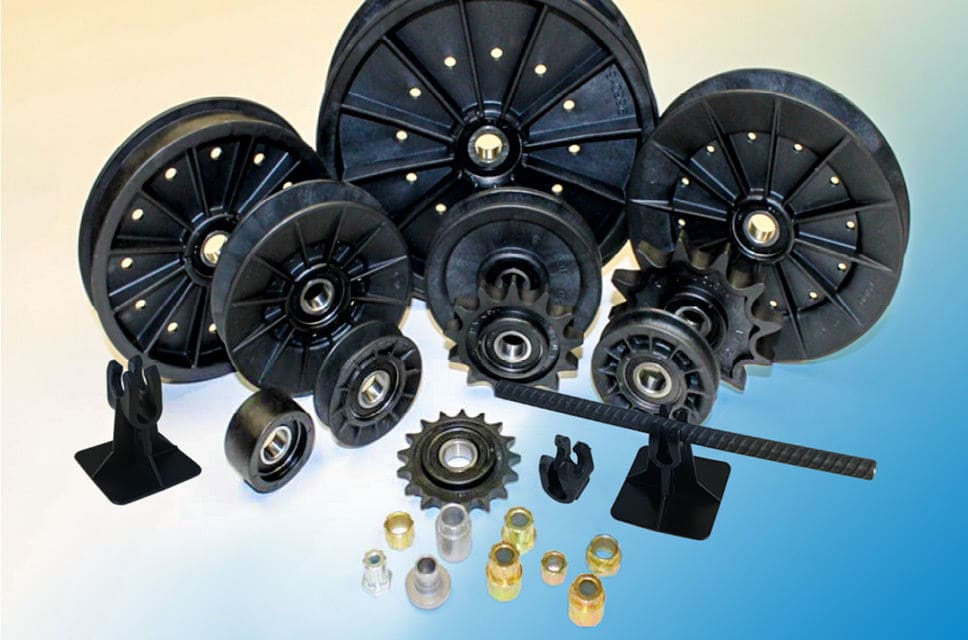
Packaging industry
food and beverage containers, bottle caps and closures, cosmetic packaging and medicine bottles, etc.
Construction industry
pipe fittings, pipe components, electrical boxes, insulation materials and window frames, etc.
Toys and entertainment
action figures, puzzles, board game components, outdoor equipment, etc.
Household items
kitchen utensils, containers and utensils, storage boxes and cleaning tools, etc.
7.Common Problems and Solutions for Thermoplastic Injection Molding
(I) Common Problems
Short Shot: The mold is not completely filled.
Flash Formation: A thin layer of excess plastic appears on the edge of the part.
Warping: The part deforms as it cools.
Dents: Small depressions or dents on the surface of the molded part.
Burn marks: The part turns black or brown.
(II) Solutions
Regular maintenance: Keep the injection molding machine and mold in optimal condition.
Optimize material use: Select the right material and test different materials to meet product requirements.
Monitor and control process parameters: Carefully monitor parameters such as temperature, pressure, and injection speed, and adjust as needed.
Quality Control: Implement strict quality control measures to detect and resolve defects early.
8.Comparison between Thermoplastic Injection Molding and Other Molding Technologies
(I) Differences between Thermosetting Plastics and Thermoplastic Plastic Injection Molding
Thermoplastic materials: plastic when heated, solidified when cooled, reversible process, recyclable, suitable for mass production that requires flexibility, impact resistance or transparency.
Thermosetting materials: irreversible chemical changes occur after heating and molding, cannot be re-melted or molded, suitable for products that require high temperature resistance, chemical exposure or electrical insulation.
(II) Comparison with other molding technologies
Blow molding: used to make hollow objects, thermoplastic injection molding is suitable for making solid parts, with higher design accuracy and complexity.
Compression molding: mainly used for thermosetting plastics, thermoplastic injection molding injects molten plastic into the mold cavity under high pressure, providing more details and complexity.
Rotational molding: used for large hollow parts, thermoplastic injection molding is more suitable for large-scale, complex and tight tolerance parts.
Conclusion
Thermoplastic injection molding technology has an irreplaceable position in modern manufacturing, providing enterprises with efficient and high-quality plastic parts manufacturing solutions. When choosing thermoplastic injection molding, enterprises should fully consider material properties, application requirements, cost-effectiveness, and comparison with other molding technologies to ensure that they choose the manufacturing method that best suits their projects.