Thread cutting technology in-depth analysis and application guide
Thread cutting is a key technology in mechanical processing, which is mainly used to process internal and external threads on various materials. Threads are widely used in industrial production and daily life, such as fasteners, pipe connections, mechanical transmission, etc. This article will elaborate on the basic principles of thread cutting, cutting methods, tool selection, process parameters, common problems and solutions, processing strategy optimization, cooling and lubrication strategies, etc.
1.Basic principles of thread cutting
Thread cutting is the process of removing material from the workpiece by a tool to form a thread with a specific pitch and shape. The basic elements of a thread include major diameter, minor diameter, intermediate diameter, pitch and tooth angle. During the cutting process, the tool feeds along the axis of rotation of the workpiece, and the workpiece rotates at the same time, forming a continuous spiral line on the surface of the workpiece through the cutting edge of the tool.
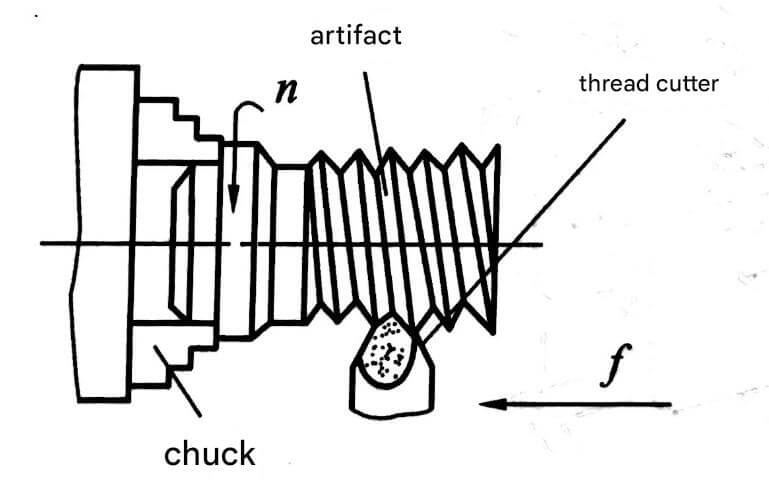
2.Thread cutting method
(1) Thread turning
Thread turning is one of the most commonly used thread processing methods, suitable for processing threads of various specifications and shapes. Thread turning can be performed on ordinary lathes and CNC lathes. By installing a thread turning tool, the thread cutting is achieved by utilizing the lathe’s spindle rotation and the tool’s longitudinal feed motion. The advantages of thread turning are high processing accuracy and a wide range of applications, but the processing efficiency is relatively low.
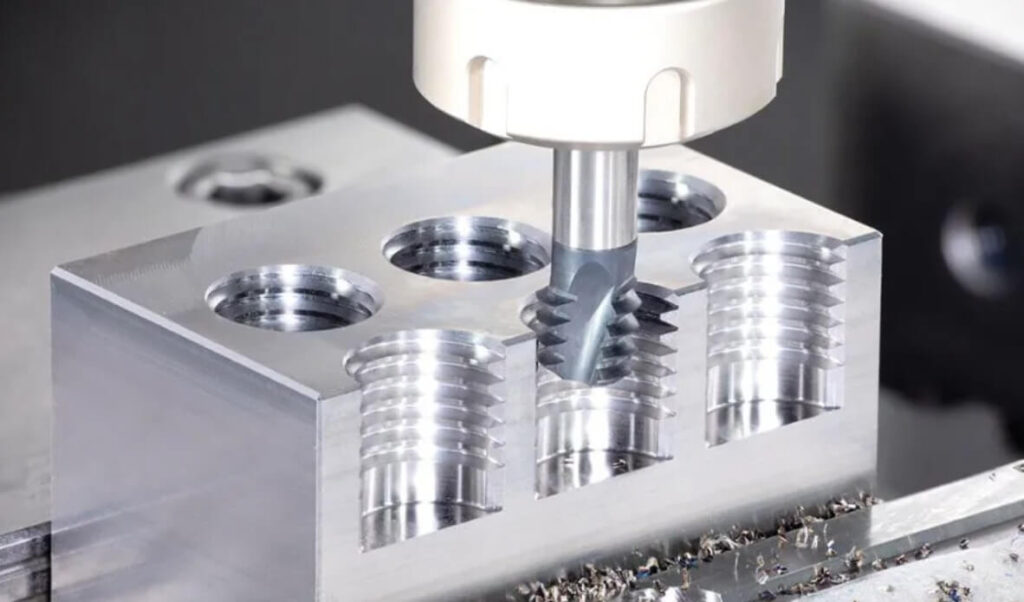
(2) Milling thread
Milling thread is processed by a thread milling cutter on a milling machine or machining center. Milling thread is suitable for processing large diameter threads, special shape threads, and difficult-to-process materials. The processing efficiency of milling thread is high, and the tool wear is uniform, but the processing accuracy is greatly affected by the machine tool accuracy and tool selection.
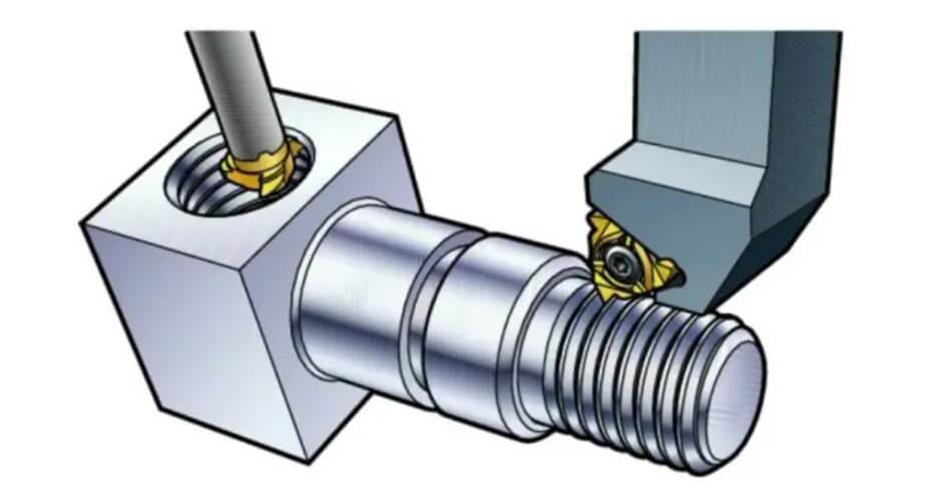
(3) Grinding thread
Grinding thread is mainly used for the processing of high-precision threads, such as precision lead screws, thread gauges, etc. Grinding thread can be performed on a thread grinder, and high-precision thread processing is achieved through the high-speed rotation of the grinding wheel and the low-speed rotation of the workpiece. Grinding thread has high processing accuracy and good surface quality, but the processing cost is relatively high.
(4) Tapping and threading
Tapping is a method of processing internal threads, using a tap to cut threads in a prefabricated hole. Threading is the process of machining external threads, using a die to cut threads on a round bar. These two methods are simple to operate and suitable for small-batch production and maintenance operations, but the processing accuracy and efficiency are low.
3.Selection of thread cutting tools
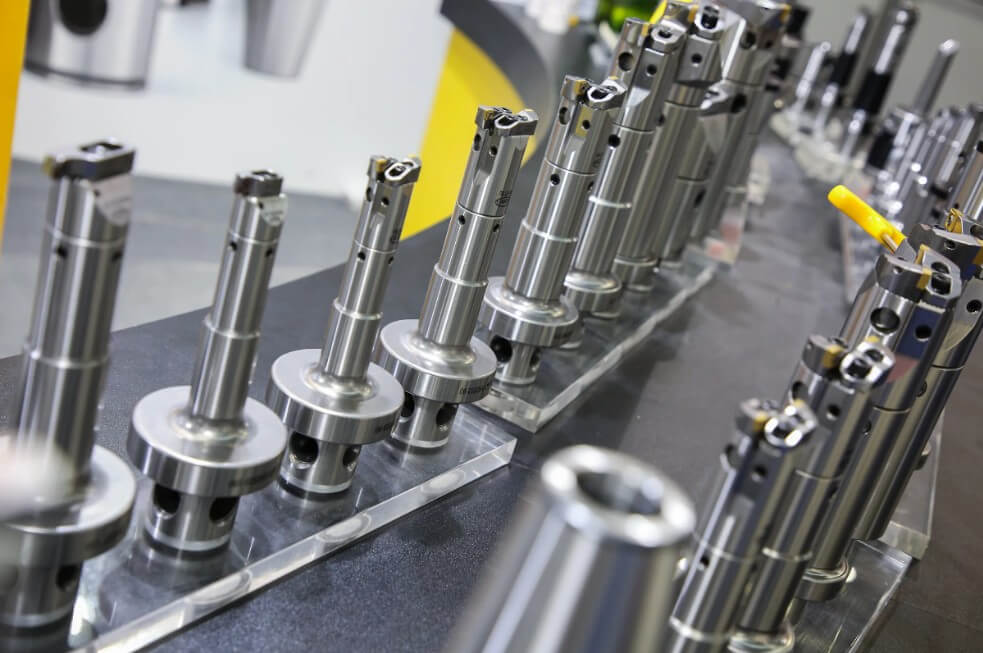
(1) Thread turning tool
Thread turning tool is the main tool for turning threads. It is divided into different types according to the size of the tooth angle, such as 60°, 55°, 29°, etc. Thread turning tools are made of high-speed steel, cemented carbide, etc. Selecting the right tool material and geometric parameters is crucial to improving processing efficiency and thread quality.
(2) Thread milling cutter
Thread milling cutter is used for milling threads. Select the right tool according to the processing material and thread specifications. Thread milling cutters are of two types: integral type and indexable type. Indexable milling cutters have the advantages of easy blade replacement and long tool life.
(3) Taps and die
Tap is used for tapping. Select the right tap according to the thread specifications and materials. Taps can be divided into hand taps and machine taps. Hand taps are suitable for small-batch production and maintenance work, while machine taps are suitable for mass production. Dies are used for threading, and it is also necessary to select the appropriate die according to the thread specifications.
4.Thread cutting process parameters
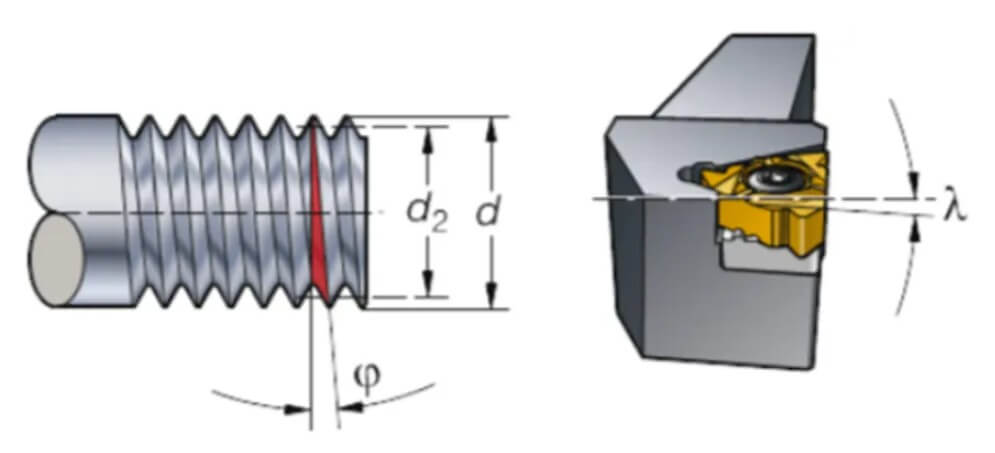
(1) Cutting speed
Cutting speed is an important factor affecting thread processing efficiency and tool life. The selection of cutting speed should be determined based on the workpiece material, tool material and thread specifications. Generally speaking, the cutting speed of high-speed steel tools is lower, while the cutting speed of carbide tools is higher.
(2) Feed rate
Feed rate refers to the distance the tool feeds per revolution, also known as pitch. The selection of feed rate should be determined based on the pitch of the thread and the cutting capacity of the tool. Excessive feed rate will lead to increased tool wear, while too small feed rate will reduce processing efficiency.
(3) Cutting depth
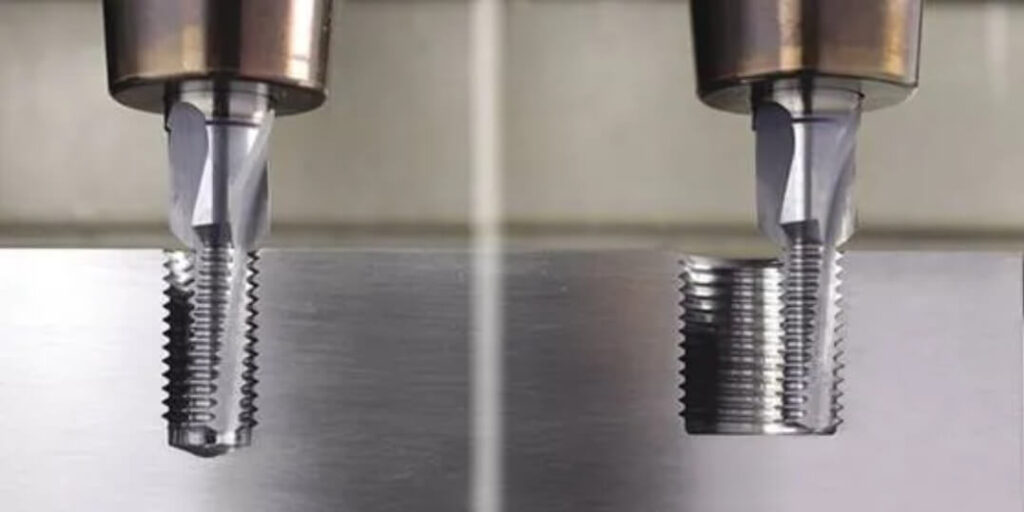
The cutting depth refers to the depth to which the tool cuts into the workpiece each time it cuts. The selection of cutting depth should be determined based on the hardness of the workpiece material and the cutting capacity of the tool. A larger cutting depth can be selected for rough processing, and a smaller cutting depth should be selected for fine processing.
5.Common problems and solutions for thread cutting
(1) Poor thread surface roughness
1) Causes: tool wear, unreasonable cutting parameters, insufficient cooling and lubrication, etc.
2) Solution: Replace worn tools, optimize cutting speed and feed rate, and use cutting fluid to improve cooling and lubrication conditions.
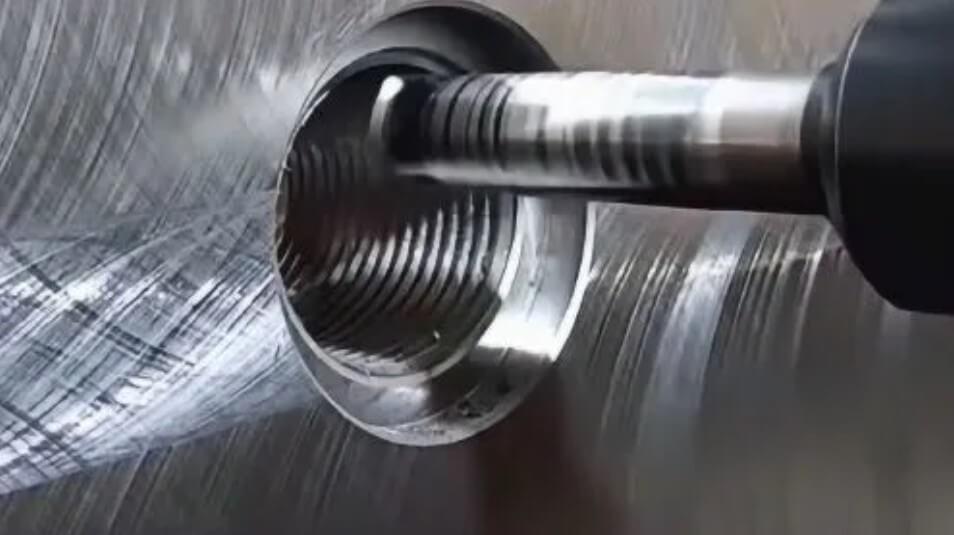
(2) Thread size accuracy exceeds tolerance
1) Causes: inaccurate tool installation, low machine tool accuracy, deformation of workpiece material, etc.
2) Solution: Reinstall the tool, adjust the machine tool accuracy, and control the deformation of the workpiece material.
(3) Incomplete thread profile
1) Causes: tool cutting edge wear, excessive cutting depth, uneven workpiece material hardness, etc.
2) Solution: Replace worn tools, adjust cutting depth, and select workpiece materials with uniform hardness.
(4) Thread chipping
1) Causes: excessive cutting force, blunt tool edge, poor workpiece material toughness, etc.
2) Solution: Reduce cutting force, replace sharp tools, and select workpiece materials with better toughness.
6.Optimization of thread cutting processing strategy
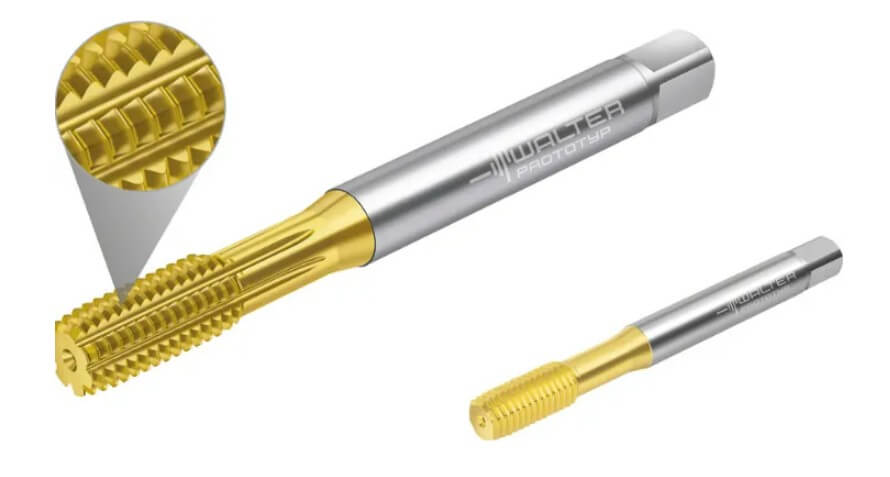
(1) Step-by-step cutting strategy
The step-by-step cutting strategy can improve thread cutting efficiency. The thread cutting process is divided into two stages: roughing and finishing. In the roughing stage, a larger cutting depth and feed speed are used to quickly remove material;
In the finishing stage, a smaller cutting depth and feed speed are used to ensure the accuracy and surface quality of the thread. This strategy can reduce cutting time and improve cutting efficiency.
(2) Multi-blade cutting strategy
The use of multi-blade cutting tools for thread cutting can improve cutting efficiency. For example, using a thread milling cutter for thread processing can achieve multi-blade cutting at the same time, improving cutting efficiency. In addition, multi-blade cutting tools can also achieve thread processing of different pitches and shapes by adjusting cutting parameters, which has high flexibility.
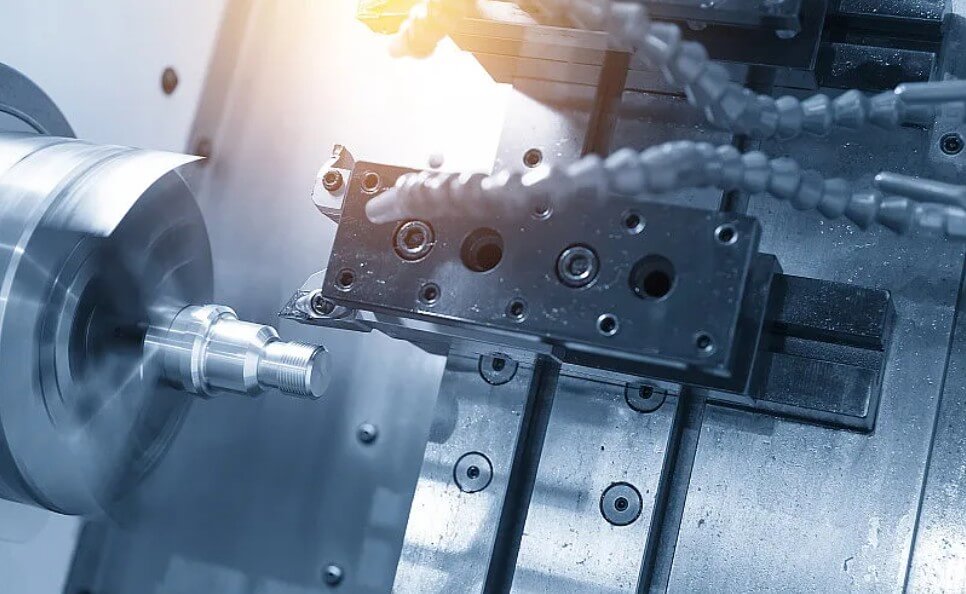
(3) Optimizing tool paths
Optimizing tool paths can reduce idle travel time and improve cutting efficiency. When performing thread cutting, the tool path should be arranged reasonably to avoid unnecessary idle travel.
In addition, the use of advanced cutting methods such as spiral cutting can reduce vibration and impact during the cutting process and improve cutting efficiency.
7.Thread cutting cooling and lubrication strategy
(1) Selecting a suitable cutting fluid
Selecting a suitable cutting fluid can reduce cutting temperature, reduce tool wear, and improve thread cutting efficiency. Common cutting fluids include emulsions, oil-based cutting fluids, synthetic cutting fluids, etc. When selecting cutting fluids, comprehensive consideration should be given to factors such as workpiece materials, tool materials, and cutting parameters.
(2) Reasonable cooling and lubrication methods
A reasonable cooling and lubrication method can give full play to the role of cutting fluids and improve cutting efficiency. Common cooling and lubrication methods include pouring cooling, spray cooling, and internal cooling. When selecting a cooling and lubrication method, comprehensive consideration should be given to factors such as processing requirements and machine tool conditions.
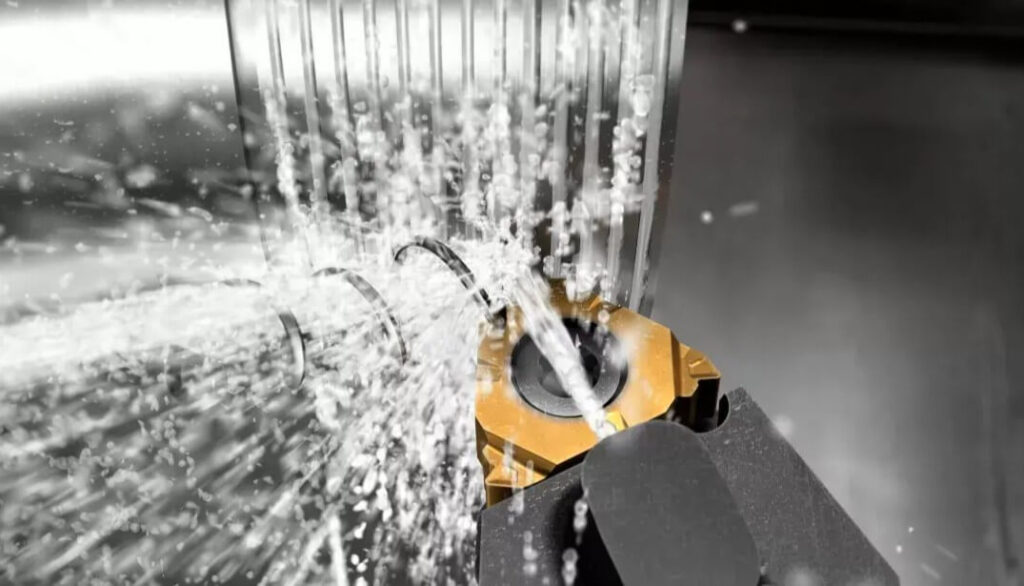
(3) Controlling the flow and pressure of cutting fluid
Controlling the flow and pressure of cutting fluid can ensure cooling and lubrication effects and improve thread cutting efficiency. Excessive or insufficient flow and pressure of cutting fluid will affect the cooling and lubrication effects. Therefore, the flow and pressure of cutting fluid should be reasonably controlled according to factors such as processing requirements and tool materials.
8.Development of CNC thread cutting technology
With the continuous development of CNC technology and tool materials, thread cutting technology is also constantly improving. The widespread use of CNC lathes and machining centers has greatly improved the automation and processing accuracy of thread cutting.
The application of new tool materials such as coated carbide and ceramic tools has further improved the efficiency and tool life of thread cutting. In addition, the online detection technology of thread cutting is also developing continuously, which can realize real-time detection and quality control of thread size.
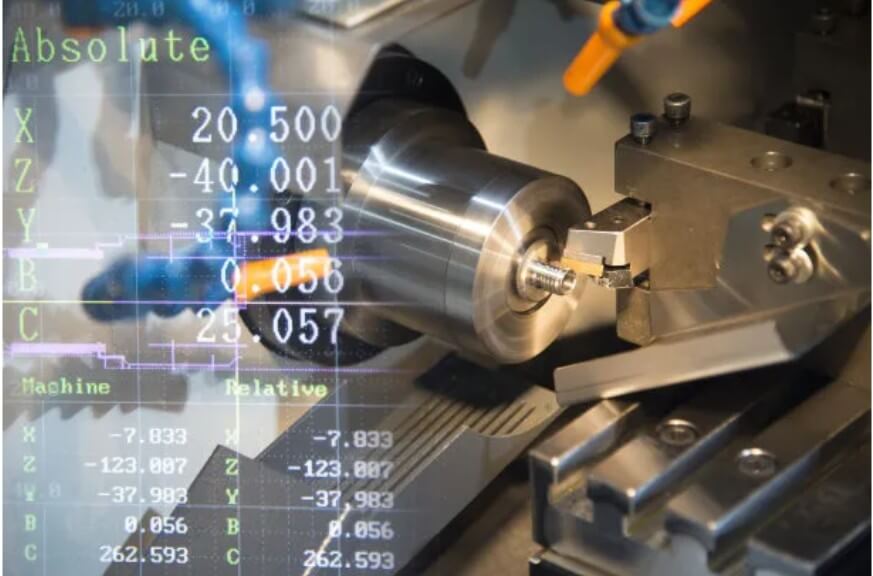
9.Specific applications of threads in different fields
(1) Mechanical fastening connection
1) Bolt connection:
It is used in situations where the connected parts are not too thick and it is easy to process through holes, such as the fixing of machine casing.
2) Stud connection:
It is suitable for situations where the connected parts are thick and need to be frequently disassembled and assembled, such as the connection of vehicle engine parts.
3) Screw connection:
It is directly screwed into the threaded hole of the connected part. It is suitable for situations where a nut cannot be installed on one end, such as the fixing inside electronic equipment.
(2) Transmission application
1) Trapezoidal thread:
It is widely used in the spiral transmission of machine tools and equipment due to its high root strength and good centering.
2) Sawtooth thread:
Suitable for force transmission screws with unidirectional force, such as jacks and screw presses.
3) Rectangular thread:
Although the root strength is low, the transmission efficiency is high and it is used in occasions requiring precision transmission.
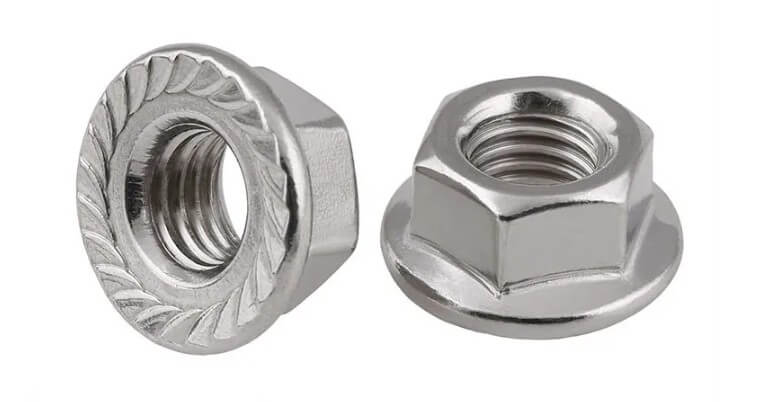
(3) Pipe system connection
Pipe thread:
Used for connecting water, gas, lubrication and other pipeline systems to ensure sealing, such as the connection of domestic natural gas pipelines.
(4) Precision adjustment
Fine pitch thread:
Due to its good self-locking performance, it is often used in mechanisms that require precision adjustment, such as the focusing mechanism of a microscope and the fine-tuning device of an optical instrument.
(5) Electronic equipment:
The small threaded connection in electronic equipment is used to fix circuit boards, housings, etc. to ensure the stability and safety of the equipment. For example, micro screws are often used for internal assembly in electronic products such as mobile phones and computers.
10.Conclusion
Thread cutting is a key technology in mechanical processing. Mastering and applying this technology is of great significance to industrial production. At the same time, the development of CNC thread cutting technology also provides more efficient and precise thread processing solutions for industrial production.