Tool selection and cutting parameter optimization in precision machining of tire valve stems
The tire valve stem is a key component in the tire system and is responsible for maintaining the stability of the internal air pressure of the tire. Its machining accuracy directly affects the safety and service life of the tire. Therefore, the precision machining of tire valve stems is particularly important.
This paper will discuss in detail the tool selection and cutting parameter optimization in the precision machining of tire valve stems, aiming to improve machining efficiency and product quality.
1.Structure and materials of tire valve stems
The tire valve stem is mainly composed of a rod body, a sealing component and a dust cap. Its structure is relatively simple, but it has high requirements for dimensional accuracy, surface roughness and form and position tolerances. Commonly used materials include stainless steel, aluminum alloy and copper alloy, which have good mechanical properties and corrosion resistance.

2.Analysis of precision CNC machining process of tire valve stems
(1) CNC programming and simulation
In precision CNC machining, CNC programming is one of the key links. Programmers need to select appropriate CNC systems and programming software according to the drawing requirements of the valve stem and write efficient CNC machining programs. In order to improve programming efficiency and accuracy, CAD/CAM software can be used for automatic programming. After programming is completed, CNC simulation is required to verify the feasibility and safety of the processing program.
(2) Processing route planning
The precision CNC processing route of tire valve stems usually includes the following steps:
1) Cutting:
According to the size requirements of the valve stem, select suitable bar stock for cutting.
2) Rough processing:
Remove most of the material through turning, milling and other processes to prepare for subsequent fine processing.
3) Heat treatment:
Appropriate heat treatment is performed on the valve stem to improve its hardness and strength.
4) Fine processing:
Use precision CNC lathes, CNC milling machines and other equipment for high-precision processing to ensure the dimensional accuracy and surface quality of the valve stem.
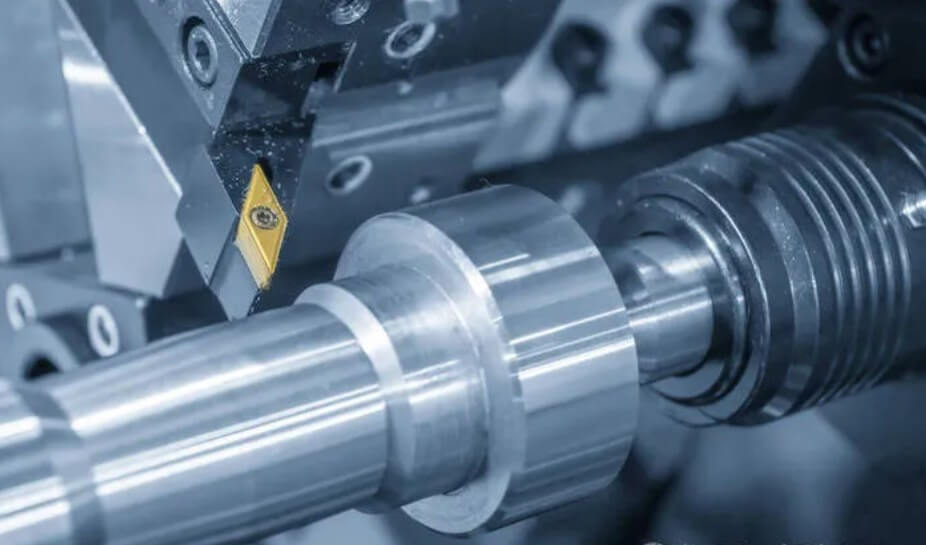
5) Surface treatment:
The valve stem is surface treated, such as nickel plating, chrome plating, etc., to improve its corrosion resistance and aesthetics.
6) Inspection:
Perform a comprehensive inspection on the valve stem after machining to ensure that it meets the design requirements.
3.Characteristics and challenges of tire valve stem machining
Tire valve stems are usually made of high-strength stainless steel or aluminum alloy, and are characterized by slenderness and thin walls. The difficulties in machining are mainly reflected in the following aspects:
(1) High precision requirements:
The dimensional accuracy and surface roughness requirements of the valve stem are extremely high. The general dimensional tolerance is in the micron level, and the surface roughness is required to be below Ra0.8μm.

(2) Easy to deform:
Due to the thin and slender walls of the valve stem, it is very easy to deform during the cutting process due to factors such as cutting force and cutting heat, which affects the machining accuracy.
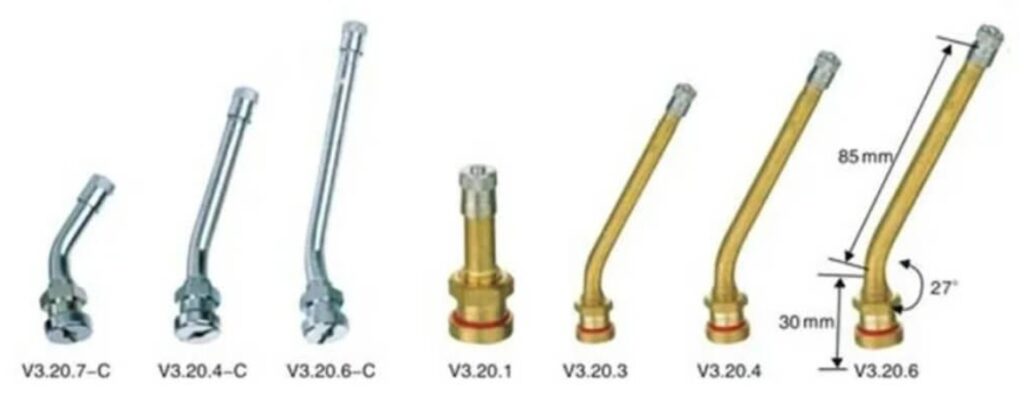
(3) Machining efficiency:
Tire valve stems are mass-produced parts. How to improve machining efficiency while ensuring accuracy is an urgent problem to be solved.
In view of the above characteristics, reasonable tool selection and cutting parameter optimization are particularly important.
4.Tool selection for CNC machining of tire valve stems
(1) Tool material selection
1) High-speed steel tools:
High-speed steel tools have good toughness and wear resistance, and are suitable for rough machining and semi-finishing of valve stems. However, their hardness is relatively low and they are not suitable for high-speed cutting.
2) Carbide tools:
Carbide tools have high hardness and good wear resistance, and are suitable for high-speed cutting. They are widely used in the finishing of tire valve stems. However, their toughness is poor, and care should be taken to avoid impact loads during machining.
3) Ceramic tools:
Ceramic tools have extremely high hardness, good wear resistance and heat resistance, and are suitable for machining high-hardness materials. However, they are prone to chipping during machining, and are suitable for finishing with small cutting amounts.
4) Diamond tools:
Diamond tools have the highest hardness and low friction coefficient, and are suitable for high-precision and high-surface quality machining. However, they are more expensive and easily damaged by impact, and are suitable for the final finishing of valve stems.
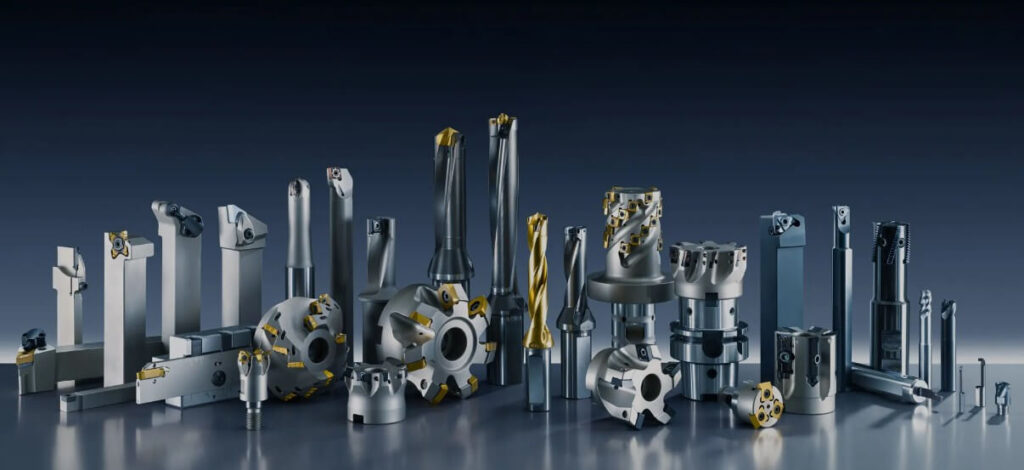
(2) Tool structure selection
1) Integral tool:
Integral tool has simple structure and good rigidity, which is suitable for rough machining and semi-finishing of valve stem.
2) Indexable tool:
The blade of indexable tool can be replaced, which reduces tool change time and improves machining efficiency, and is suitable for mass production.
3) Special structure tool:
In view of the slender characteristics of tire valve stem, tools with internal cooling holes can be selected to effectively reduce cutting heat and deformation.
(3) Tool geometry parameter selection
1) Rake angle:
Properly increasing the rake angle can reduce cutting force and cutting heat, but too large a rake angle will reduce tool strength. Generally, the rake angle is selected to be 15°-25°.
2) Back angle:
The back angle mainly affects tool wear and surface roughness. Generally, the back angle is selected to be 6°-12°.
3) Blade inclination angle:
The blade inclination angle affects the flow direction of chips and the direction of cutting force. Proper selection of the blade inclination angle can reduce the cutting force and avoid interference between the tool and the workpiece.
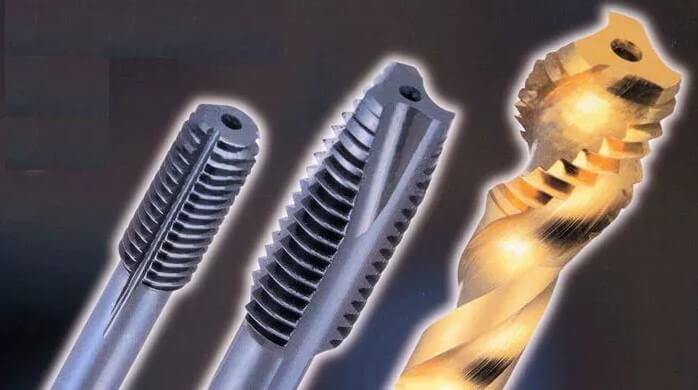
5.Optimization of cutting parameters for CNC machining of tire valve stems
(1) Cutting speed
1) High-speed steel tool:
The cutting speed is generally selected between 20-40m/min.
2) Carbide tool:
The cutting speed is generally selected between 80-200m/min.
3) Ceramic tool:
The cutting speed is generally selected between 200-500m/min.
4) Diamond tool:
The cutting speed is generally selected between 300-1000m/min.
The selection of cutting speed should be based on comprehensive considerations of factors such as tool material, workpiece material, and machining accuracy. Under the premise of ensuring machining accuracy, a higher cutting speed should be selected as much as possible to improve machining efficiency.
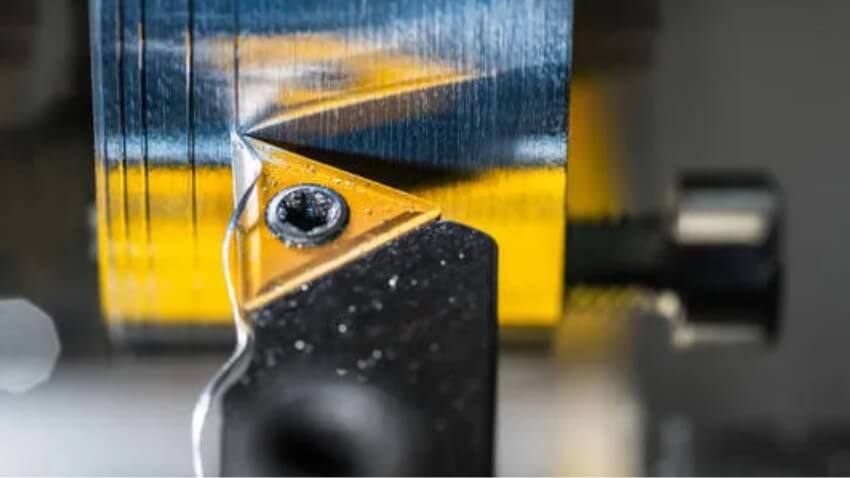
(2) Feed rate
1) Rough machining:
The feed rate is generally selected between 0.1-0.3mm/r.
2) Semi-finishing:
The feed rate is generally selected between 0.05-0.1mm/r.
3) Finishing:
The feed rate is generally selected between 0.01-0.05mm/r.
The selection of feed rate should be based on comprehensive considerations such as processing accuracy, surface roughness, and tool strength. Under the premise of ensuring processing accuracy, a larger feed rate should be selected as much as possible to improve processing efficiency.
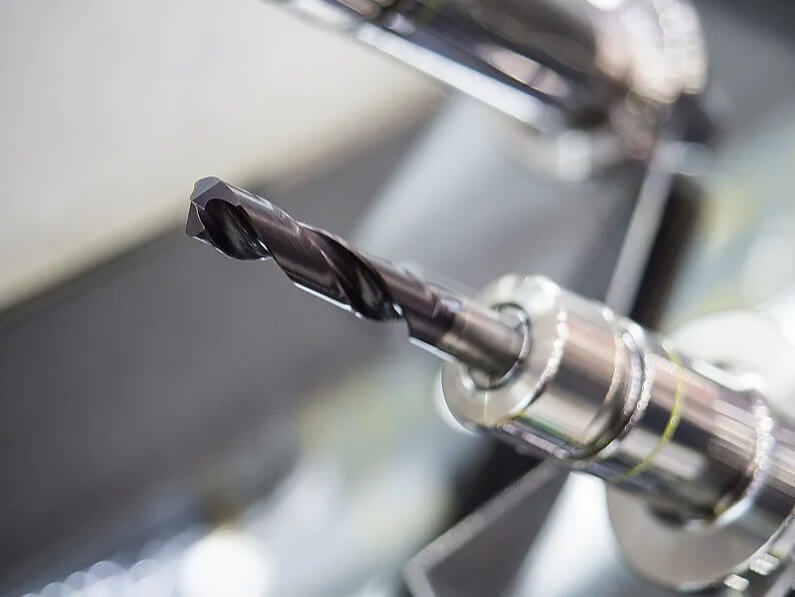
(3) Back cutting amount
1) Roughing:
The back cutting amount is generally selected between 0.5-2mm.
2) Semi-finishing:
The back cutting amount is generally selected between 0.2-0.5mm.
3) Finishing:
The back cutting amount is generally selected between 0.05-0.2mm.
The selection of back cutting amount should be based on comprehensive considerations such as processing accuracy, surface roughness, and tool strength. Under the premise of ensuring processing accuracy, a larger back cutting amount should be selected as much as possible to improve processing efficiency.
(4) Cooling and lubrication
The cutting heat generated during the cutting process will cause deformation of the tire valve stem parts and tool wear, affecting the processing accuracy. Therefore, reasonable cooling and lubrication measures are crucial. Common cooling and lubrication methods are:
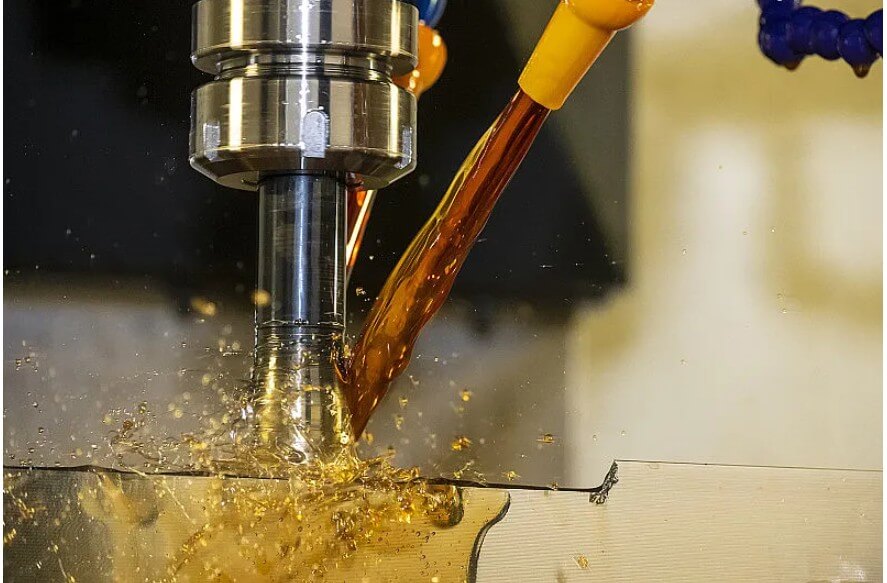
1) Emulsion:
It has good cooling and lubrication properties and is suitable for general cutting processing.
2) Cutting oil:
It has good lubrication properties and is suitable for fine processing and processing of difficult-to-process materials.
3) Internal coolant:
The coolant is directly sprayed into the cutting area through the internal channel of the tool, with significant cooling effect, suitable for high-precision processing.
6.Conclusion
Precision processing of tire valve stems is a key link in the tire manufacturing process. Reasonable tool selection and cutting parameter optimization are important means to improve processing efficiency and product quality. In the actual processing process, the appropriate tool material and structure should be selected according to the specific processing requirements, the cutting parameters should be optimized, and effective cooling and lubrication measures should be taken to achieve the best processing effect.
2 Comments