Basic Introduction to Titanium Alloy CNC Machining
Titanium Alloy CNC Machining has become the choice of more and more companies. Titanium alloys have been widely used in many key industries due to their unique performance advantages, such as high strength-to-weight ratio, excellent corrosion resistance and good biocompatibility. However, the processing of titanium alloys, especially through computer numerical control (CNC) machining technology, faces a series of special challenges and problems.
Titanium Alloy CNC Machining involves many aspects such as material properties, processing technology, tool selection, cost control, etc., which require in-depth understanding and precise operation to ensure processing quality and efficiency. This article will discuss in detail the common problems about Titanium Alloy CNC Machining and provide corresponding solutions to fully analyze this complex and important processing process for you.
1.Difficulty of Titanium Alloy CNC Machining
Question 1: Is titanium alloy difficult to machine?
Titanium alloys are indeed more difficult to machine than many other metals, mainly due to their low thermal conductivity and high strength. This causes heat to concentrate on the cutting edge, causing problems such as rapid tool wear, increased cutting forces, and surface defects. However, with the right equipment and technology, Titanium Alloy CNC Machining can be carried out effectively.
Question 2: Will titanium alloys bend during machining?
Titanium alloys will bend during machining, which is related to a variety of factors.
Residual stress (such as that generated during the manufacturing process, uneven material removal during machining can cause deformation)
Heat generation (titanium has low thermal conductivity, and concentrated machining heat is prone to thermal expansion and warping, especially in thin sections or complex geometry parts)
Tool pressure (excessive cutting force or improper tool path can introduce mechanical stress and cause workpiece deformation)
Part geometry and fixtures (complex geometry or insufficiently supported parts are prone to warping, and appropriate fixtures and supports are required to maintain dimensional stability).
To reduce the risk of warpage, measures such as pre-processing stress relief processes (such as heat treatment), balanced processing, controlled cutting parameters (low cutting speed, high feed rate, sharp tool and proper cooling technology), appropriate fixtures and intermediate stress relief can be taken.
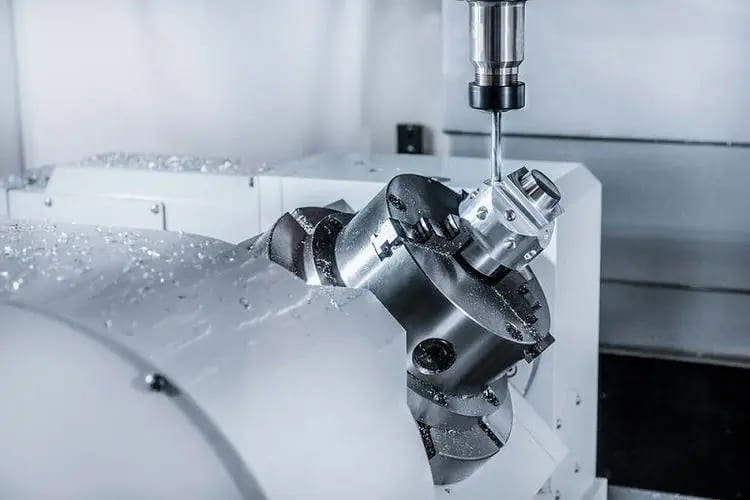
2.Titanium Alloy CNC Machining advantages and application issues
Question 3: What are the advantages of Titanium Alloy CNC Machining?
Titanium Alloy CNC Machining offers several significant advantages.
High strength-to-weight ratio: Its high strength-to-weight ratio makes titanium alloy parts lighter than other metal parts, making it very suitable for aerospace and marine applications that require weight reduction;
Corrosion resistance: Excellent corrosion resistance enables use in harsh environments
Biocompatibility: Good biocompatibility makes it the preferred material for medical implants
Fatigue Resistance: Excellent fatigue resistance ensures long-term component durability
Question 4: What are the applications of Titanium Alloy CNC Machining parts?
Titanium Alloy CNC Machining parts are widely used, mainly in the following fields:
Aerospace: such as aircraft parts, engine parts, satellite parts
Medical: such as implants, surgical instruments, dental prostheses
Automotive: Performance parts, exhaust systems, suspension components
Ships: such as propellers, shafts, underwater equipment
Chemical processing: such as valves, pumps, heat exchangers and many other industries.
3.Questions related to the CNC machining process and challenges of titanium alloys
Question 5: What kind of cutting tools are best for titanium alloys?
Carbide tools are usually the first choice for machining titanium alloys because of their high hardness and wear resistance. Tools with special coatings (such as titanium aluminum nitride TiAlN) can help reduce heat buildup and extend tool life.
High-speed steel (HSS) tools can also be used, especially when high toughness operations are required, but they may wear faster than carbide tools.
Question 6: What are the common machining processes for titanium alloys?
Common machining processes for titanium alloys include milling (creating complex shapes and features), turning (producing precisely sized cylindrical parts), drilling (creating holes of different sizes and depths), and grinding (achieving fine surface finishes and tight tolerances).
Due to the characteristics of titanium alloys, each process requires careful consideration of cutting parameters. CNC machining is favored for its high precision and ability to handle complex geometries. Milling and turning usually use slower cutting speeds and higher feed rates to control heat.
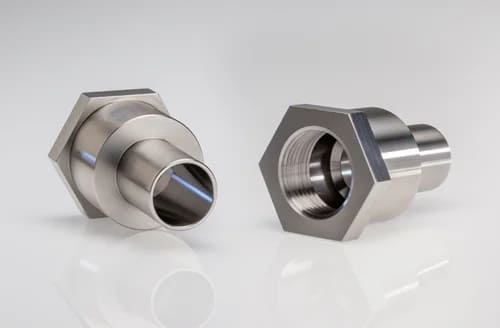
Question 7: What are the best practices for reducing tool wear when machining titanium alloys?
Tips for reducing tool wear in titanium CNC machining include using high-quality cutting tools with the right coating, optimizing cutting parameters to avoid excessive heat generation, implementing proper tool clamping and cooling, and monitoring tool condition to replace worn tools promptly.
Question 8: How important is coolant in titanium machining?
Coolant is critical in titanium machining, helping to reduce heat generation and prevent work hardening, as well as enhancing chip evacuation and preventing chip accumulation. Without adequate cooling, cutting tools will wear quickly and the workpiece may suffer thermal damage.
High-pressure coolant systems or flood cooling methods are often used to keep the cutting zone cool to extend tool life and ensure a high-quality surface finish.
4.Material properties and design-related issues for titanium alloy CNC machining
Question 9: What are the different grades of titanium and their machinability?
Titanium has many grades, such as the common 1, 2, 3, 4, 5 (Ti – 6Al – 4V), 9 (Ti – 3Al – 2.5V), 23 (Ti – 6Al – 4V ELI), and other specialized alloys. Different grades have different properties and machinability. The machinability of commercial pure grades (1 – 4) becomes more challenging as the strength increases, and the alloy grades are more challenging to process due to their high hardness and strength.
Machinability needs to take into account factors such as titanium’s low thermal conductivity, work hardening tendency, and high strength, and requires careful control of machining parameters, tool selection, and cooling strategies. Understanding these differences can help select the right titanium alloy grade for a specific application and predict machining challenges.
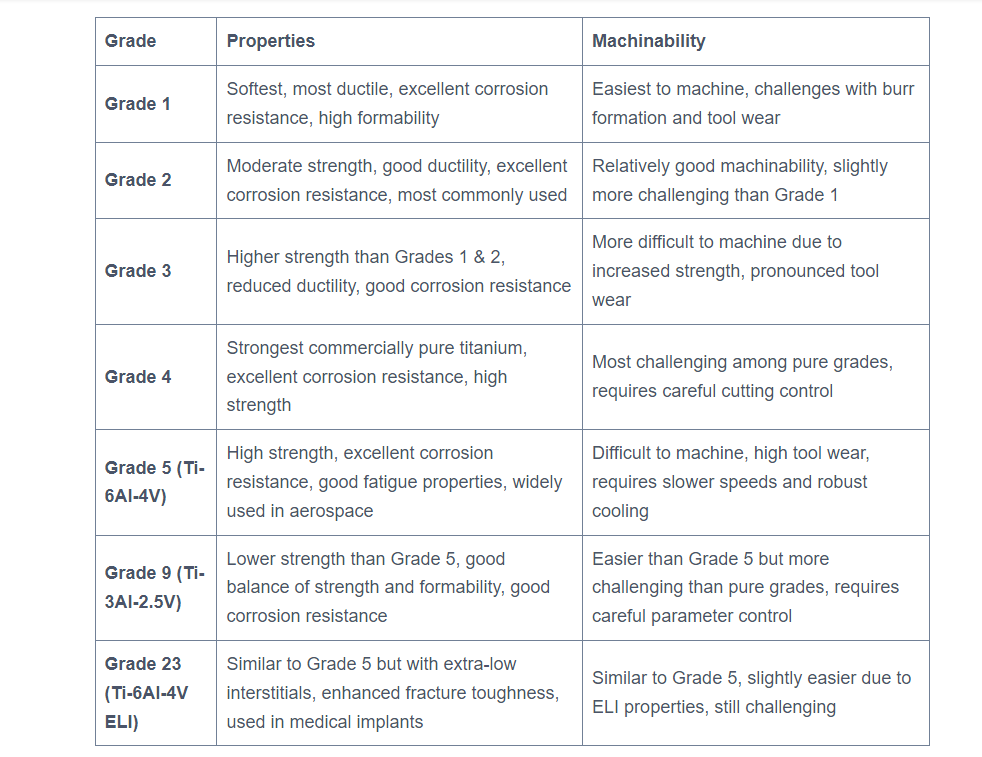
Question 10: How does titanium compare to other metals such as aluminum or steel in CNC machining?
Titanium is generally more difficult to machine than aluminum but easier than steel. Aluminum is softer and conducts heat better, while steel is harder and generates more heat when processed. Titanium has excellent strength, corrosion resistance and a high strength-to-weight ratio, making it suitable for specialized applications, but it is difficult and expensive to process.
Aluminum is easy and fast to process, making it suitable for cost-sensitive applications. Steel is strong and durable, and its machinability varies by grade. The choice of material depends on the specific requirements of the application.
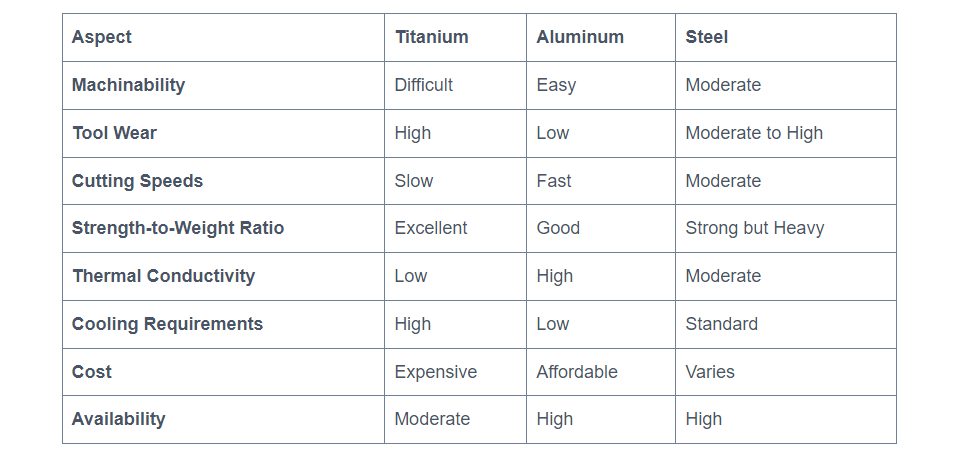
Question 11: How does titanium’s strength-to-weight ratio affect part design?
Titanium’s high strength-to-weight ratio can be used to design lightweight and highly durable parts, which is particularly valuable in weight-sensitive applications such as aerospace and automotive, where it can reduce component weight without sacrificing strength and performance.
Question 12: What factors should be considered in the design of titanium alloy parts?
Designing titanium alloy parts requires considering material properties, avoiding complex geometries to reduce machining difficulty and cost, considering the possibility of wear or seizure (such as threads or mating surfaces), ensuring adequate support during processing to prevent deflection, and choosing tolerances that balance accuracy and manufacturability are also key factors.
5.CNC machining costs and manufacturing-related issues for titanium alloys
Question 13: Is Titanium Alloy CNC Machining expensive?
Titanium Alloy CNC Machining is generally more expensive than machining other metals (such as aluminum or steel). The reasons for the high cost include high material prices, the need for special tools, slow machining speeds, and increased tool wear.
Despite the higher cost, the unique properties of titanium alloys make the investment reasonable in applications with high performance, durability, and weight reduction requirements.
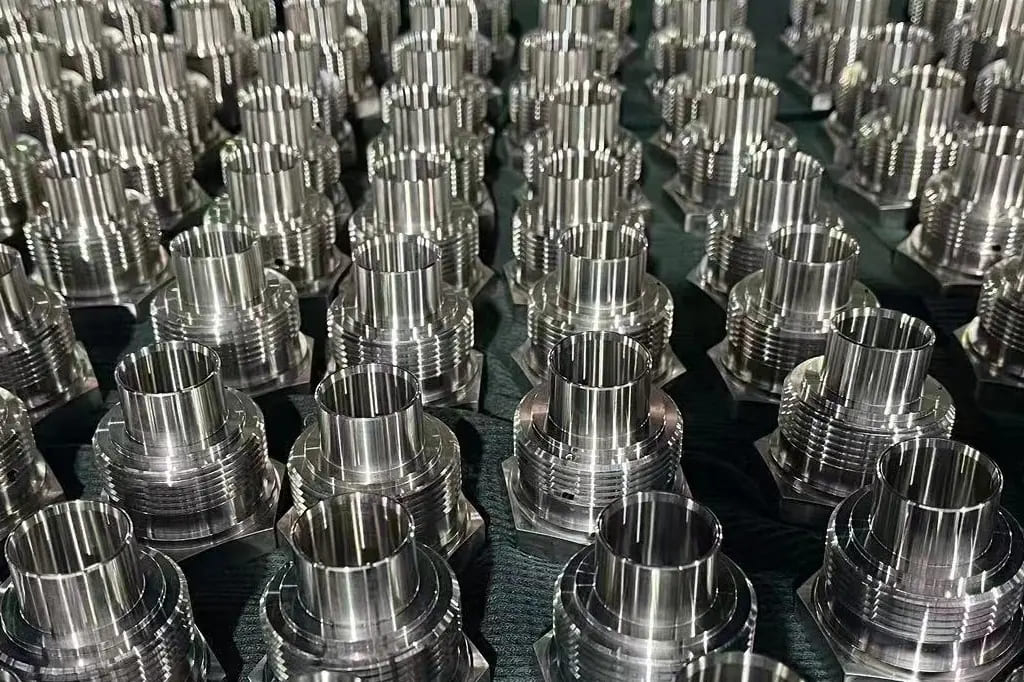
Question 14: What factors affect the cost of Titanium Alloy CNC Machining?
The factors that affect the cost of Titanium Alloy CNC Machining include part design complexity, the grade of titanium alloy used, machining time, tool wear, the need for a special coolant system, and the possibility of increased scrap. The experience and expertise of the machining service provider also affect cost and quality.
Question 15: How to reduce the cost of CNC machining parts of titanium alloys?
To reduce the cost of CNC machining parts of titanium alloys, you can consider optimizing the design for manufacturability, such as simplifying the geometry and reducing unnecessary features; selecting a titanium alloy grade that balances machinability and performance requirements; and working with an experienced CNC machining service provider to improve process efficiency and reduce material waste.
Reliable Titanium Alloy CNC Machining Service Provider – Xavier
If you need an experienced titanium alloy CNC machining manufacturer, Xavier is your best choice. The Xavier team is well-equipped to provide high-quality CNC machining solutions and excels in machining all types of metal alloys, including titanium alloys, to meet your personalized machining needs. If you need more information or to discuss your machining needs with us, please feel free to contact us.