Application of titanium alloy materials
Grade 5 titanium is a titanium alloy composed of titanium, which contains 6% aluminum and 4% vanadium. Ti-6Al-4V has excellent corrosion resistance, making it the first choice in various industries. The reason Apple used grade 15 titanium in the iPhone 15 Pro is likely due to the material’s inherent lightness, strength, and stiffness.
Advantages of titanium alloy
1.Excellent strength to weight ratio
In terms of strength-to-weight ratio, titanium stands out, especially grade 5 titanium. It offers a level of strength comparable to many steel types. At the same time, it weighs almost half as much as its steel counterpart. The aluminum used in previous iPhone models may have been lighter than titanium. But it is obviously lagging behind in terms of strength. iPhone devices require a delicate balance between durability and portability. A higher strength-to-weight ratio ensures the device remains strong and resilient while minimizing weight. The result is an improved overall user experience that makes the device more comfortable to hold and carry without compromising its structural integrity.
2.preservative
All of the above titanium and aluminum exhibit commendable corrosion resistance. Still, titanium offers significant advantages, especially in challenging environments rich in salt water or chlorine. It’s under these conditions that titanium’s corrosion resistance really shines and is significantly better than steel. This is especially true when working with non-stainless steel or steel that has not been specifically treated. Grade 5 titanium is also highly flexible. While aluminum may be too flexible and steel may be too hard, titanium balances these properties. As a result, iPhone 15 Pro is more resistant to deformation and bending. Grade 5 titanium’s superior corrosion resistance significantly extends the lifespan of devices like iPhone 15 Pro. By withstanding harsh environmental factors, Grade 5 titanium can help ensure equipment remains resilient over time. This corrosion resistance is critical for mobile devices as it helps protect internal components, extending the lifespan and overall durability of the device.
3.aesthetic appeal
Grade 5 titanium gives the device a premium, high-end look. Its natural luster and polished finish create a stylish and luxurious feel. As a result, it improves the overall look and perceived quality of the iPhone 15 Pro models. This premium look and feel is consistent with Apple’s commitment to creating visually stunning and sophisticated devices. The use of Grade 5 titanium expands color and finish options for the iPhone 15 Pro series. Options such as Space Black/Space Grey, Blue, Silver and Titanium Gray offer customers a diverse aesthetic to suit their personal preferences. These options increase the visual appeal of the device and enable users to choose a finish that matches their style and taste.
4.Thermal properties
The thermal expansion rate of grade 5 titanium is very close to that of glass. This feature is very important when integrated into devices such as smartphones. For example, the iPhone’s screen is mostly made of glass. Using metals that have similar thermal expansion to glass can help reduce the risk of temperature-affected deterioration. This compatibility helps maintain device stability and overall performance. Cooling capabilities are especially important for mobile devices. It helps prevent overheating and maintain optimal performance, even under demanding conditions. Additionally, grade 5 titanium is heat treatable. This property makes it particularly suitable for a variety of manufacturing applications. It is easy to weld and fabricate, and has an impressive combination of high strength and corrosion resistance.
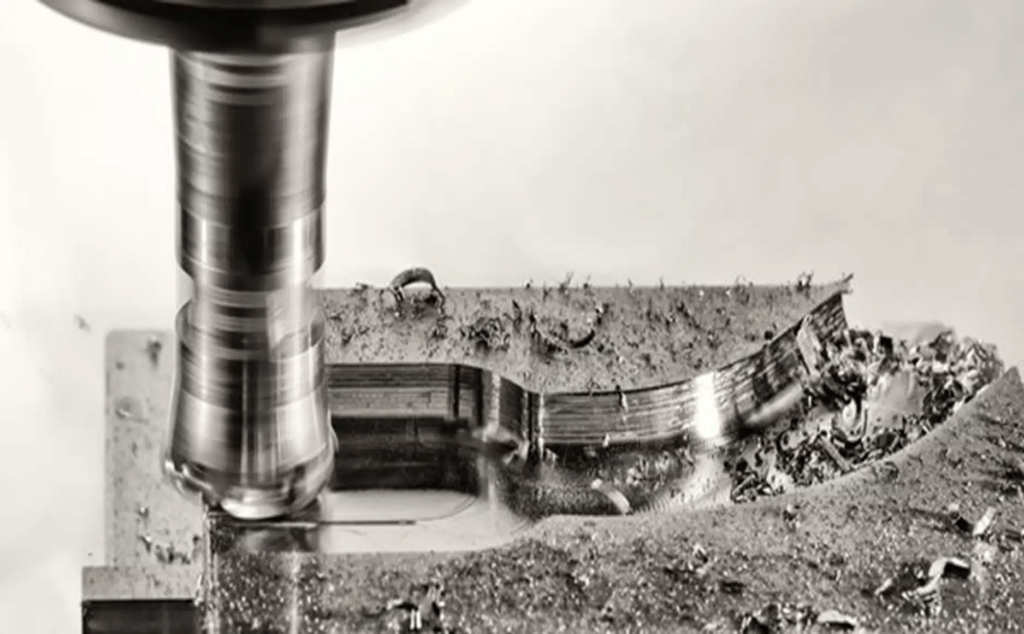
Titanium Machining Challenges and Solutions
The iPhone 15 Pro made of titanium brings many benefits to users, but machining titanium effectively can be quite difficult. How difficult is it? How do manufacturers overcome the challenges involved? You’ll find the answers in this section.
Difficulties caused by material properties:
1.Low thermal conductivity
As a thermal insulator, titanium faces challenges during processing due to its low thermal conductivity. The heat generated during machining processes tends to accumulate in the work area rather than being effectively dissipated. This can lead to high temperatures in excess of 1000°C. This heat buildup can cause wear, chipping, tool dulling, and even breakage. This challenge becomes even more apparent when machining parts that are prone to deformation, such as thin walls or rings. Achieving the required dimensional accuracy in this case can be quite complex. When the tool pushes against the workpiece material, local deformations may exceed the elastic limit.
2.WORk hardening
Titanium alloys are characterized by a hexagonal close-packed (HCP) crystal structure, which limits their slip systems and flexibility. Therefore, they are susceptible to work hardening. This process increases the material’s hardness and strength through plastic deformation. It causes accelerated tool wear, increased cutting forces and reduced machinability.
Additionally, work hardening can introduce residual stresses within machined components. Residual stress is the internal pressure that remains after external loads are removed. Therefore, it may cause problems such as deformation, cracking, and reduced fatigue life.
3.Chemical reactivity
Titanium alloys readily react with nitrogen, hydrogen, oxygen and carbon at high temperatures. This reaction can lead to surface oxidation and potential contamination of machined parts. The results can have a negative impact on the corrosion resistance, fatigue strength and biocompatibility of titanium alloys. In addition, titanium alloys tend to stick to the tool surface, forming built-up edges. Therefore, it can lead to issues such as chipping, wear, and tool failure.
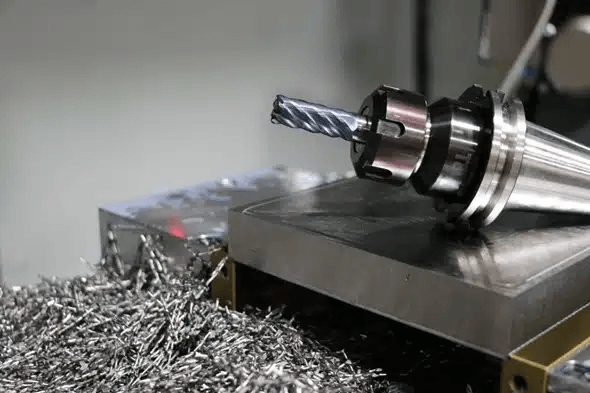
Difficulties during processing:
- Generate high heat
Titanium alloys are known for their strength but present considerable challenges when it comes to processing. They require high cutting forces for adequate machining. Due to the low thermal conductivity of titanium alloys, maintaining proper cooling temperatures during processing is very challenging. This can lead to several problems, including vibration, accelerated tool wear, and the production of defective parts. Additionally, these alloys have poor thermal conductivity, leading to heat buildup in the tool and workpiece. This can also lead to swelling, distortion, and even the risk of fire. - Vibration and tremor
The elasticity of titanium alloys creates challenges in the cutting process. Elastic deformation of the workpiece causes vibrations and increases friction, which generates additional heat. This complicates the existing heat dissipation problems of titanium alloys. In addition to its low elastic modulus, titanium also exhibits relatively large elongation at break values. It can stretch to more than 150% of its original length before breaking. As a result, titanium tends to produce extended thin chips that damage cutting tools and leave marks on the workpiece surface.
3.Slow material removal rate
The challenges posed by slow material removal rates in titanium alloys stem primarily from their unique properties. These alloys are known for their high strength, which makes them inherently more difficult to machine. Additionally, their low thermal conductivity complicates the dissipation of heat generated during machining, potentially affecting tool life and part quality. In addition, titanium alloys tend to produce long and thin chips, which is also a reason for the slow material removal rate. It reduces machining efficiency and tool wear, requiring precise machining techniques and specialized tools to maintain productivity.
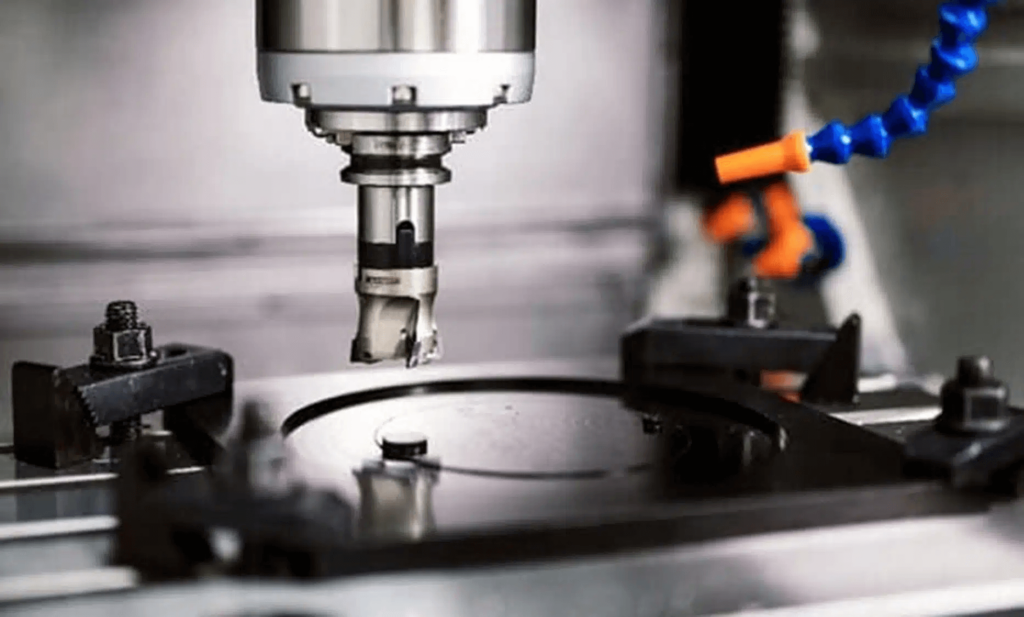
To meet the growing demand for titanium, machinists are actively devising innovative ways to enhance the machinability of this metal. Here are some practical tips for getting the best results:
- Use cutting tools with durable materials and geometries
Choosing high-quality titanium-specific tools that can handle the challenges of this demanding material can significantly improve titanium machining performance. Making sure your tools are in top condition is crucial. In addition, regular inspection and timely replacement of worn equipment helps maintain efficiency and accuracy. Additionally, choosing a tool with a smaller diameter and more cutting edges is a smart strategy. This helps maintain a stable workpiece removal rate and also helps manage the heat generated during the process. Smaller, more numerous cutting edges distribute the cutting load efficiently. This reduces the risk of overheating and tool wear, which can be particularly problematic when working with titanium alloys. - Keep the blade sharp
During machining, titanium molecules in the workpiece tend to accumulate in front of the cutting insert. Under the combined influence of high pressure and high temperature, these molecules are effectively “welded” to the blade. This creates what is called built-up edge. Therefore, it is important to use specialized insert materials and geometries when machining titanium alloys. In order to optimize the machining process, it is crucial to maintain a sharp cutting edge on the tool. Dull tools cause heat to concentrate and wear out quickly, increasing the likelihood of tool failure. Keeping your blades sharp helps minimize the heat generated during machining. This extends the life of the tool and helps achieve more precise cuts. - Use large tool nose radius or chamfer cutting
Enhance tip geometry by using a larger radius or chamfered cutting edge. Doing this will help you maximize the number of blades involved in the cut. This method effectively reduces cutting forces and minimizes local heat. When milling titanium alloys, cutting speed and radial depth of cut affect tool life. During titanium alloy machining, insert groove wear usually occurs locally along the cutting depth direction. As a result, it causes wear on the back and front of the blade. This wear usually occurs due to the hardened layer left behind from previous machining. In addition, chemical reactions and diffusion between the tool and workpiece materials at temperatures exceeding 800°C can also lead to the formation of groove wear. Therefore, adjusting these parameters and optimizing the tool geometry can go a long way in extending tool life. It also helps maintain efficiency when working with titanium. - Optimize feed speed and cutting speed
During titanium machining, you must carefully calibrate feed rates, spindle speeds, and chip loads. This practice helps manage the stress placed on tools and machinery and prevents staying in a single location for too long. A helpful strategy is to explore alternative cutting methods. You can increase axial depth of cut while reducing radial engagement. Such adjustments can improve cutting efficiency and reduce heat generated during machining. This way, you can achieve a more efficient and controlled titanium machining operation.
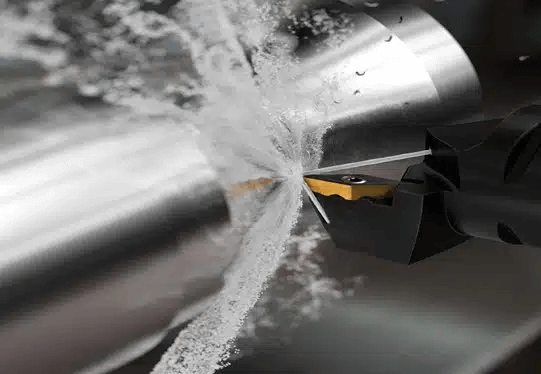
- Ensure consistent, aggressive, and deep cuts
Consistent, aggressive, and deep cuts reduce contact time between tool and workpiece, minimizing the potential for work hardening. Removing material quickly and efficiently also helps manage the heat generated during the process. Therefore, these cutting methods can extend tool life. The combination of consistent, aggressive and deep cuts optimizes the machining process in titanium alloys. It helps you strike a balance between efficiency, precision and tool life. - Utilize high-pressure coolant systems
Temperature control is crucial during titanium machining. High-pressure coolant is fired directly into the cutting area, keeping the workpiece and tool cool while preventing chips from sticking. It also ensures thermal stability and helps avoid workpiece surface degeneration and tool damage caused by excessive temperatures. Increasing coolant concentration has also proven beneficial in maintaining tolerances and extending tool life during titanium machining. - Apply appropriate coating to tools
The success of titanium machining depends on the use of coated high-frequency steel tools. Tools with coatings such as titanium carbonitride (TiCN) or heat-resistant titanium aluminum nitride (TiAlN) provide the durability needed for long-term use. These specialized tools are designed to withstand the high temperatures and forces associated with titanium machining. When working with challenging materials like titanium, their ability to maintain their sharpness over time is critical.