Titanium CNC Machining: Tips, Challenges, and Grades Guide
Titanium CNC machining is one of the most common machining methods. That’s because titanium is an excellent CNC machining material. It is resistant to high temperatures and chemical corrosion. In addition, it is lightweight and has a variety of other properties that make it unique and popular with manufacturers.
CNC machined titanium parts are also very durable, but can be challenging to machine due to the high tensile strength of titanium alloys.
In this article, we will provide a lot of information about titanium CNC machining, how to choose the right cutting tools to machine titanium alloys, and useful tips to ensure successful machining.
1.Why choose titanium for CNC machining parts?
The main advantages of titanium CNC machining as a manufacturing material include its excellent biocompatibility, high corrosion resistance, and the highest strength-to-weight ratio of all metals. This metal also has excellent ductility and good machinability.
Other reasons to choose titanium for CNC machining parts include:
- Durability: Titanium has high durability and is ideal for manufacturing CNC machined parts that work in harsh or extreme working conditions.
- Non-magnetic: This metal is not magnetic. It also has excellent oxidation resistance, so it can resist corrosion.
- Non-toxic: Titanium is corrosion-resistant, highly biocompatible, and non-toxic, making it ideal for use in the medical industry.
These properties of titanium allow it to be used in a variety of industries, including aerospace, medical, and automotive industries.
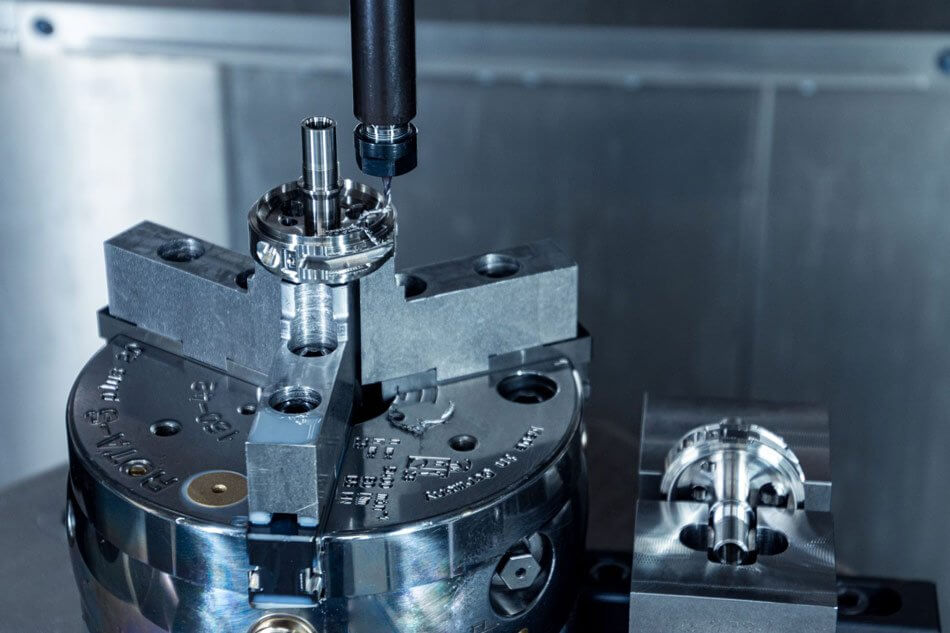
2.Challenges to Consider When CNC Machining Titanium
Although CNC titanium is a high-quality material with a wide range of uses, manufacturers often encounter challenges when machining it.
These challenges include:
1) High Chemical Reactivity and Wear
When machining titanium alloys, certain gases react with titanium alloys, causing problems such as surface oxidation and embrittlement, which weaken the strength of the parts and reduce their corrosion resistance.
In addition, this metal has a low elastic modulus and high strength, so it becomes sticky when machining. Titanium metal is sticky and may adhere to CNC cutting tools, causing tool failure and damage. In addition to tool damage, wear can also damage the surface finish of titanium metal.
2) Heat Buildup and Cutting Forces
Keeping the temperature low when machining titanium alloys is one of the most difficult challenges. The reason is that titanium alloys have low thermal conductivity, which causes heat to build up in the metal workpiece where the tool moves quickly. If not dealt with, this will wear faster and can negatively affect the quality of the cut surface, especially when machining harder titanium alloys.
For these harder titanium alloys, using higher chip loads and lower rotational speeds on your CNC machine is essential. High-pressure coolant can also help your cutting tools work more efficiently and produce higher-quality titanium parts.
In addition, titanium alloys require large cutting forces, making them difficult to cut. These cutting forces often lead to tool wear, part failure, and high vibration, which can affect product quality and surface finish.
3) Residual and Hardening Stress
Due to the crystal structure of titanium alloys, they are not very flexible, which can cause problems during machining. The crystal structure of titanium alloys can increase cutting forces during machining, reduce machining difficulty, and increase the possibility of residual tension. These tensions can cause the workpiece to distort, crack, or have a shortened service life.
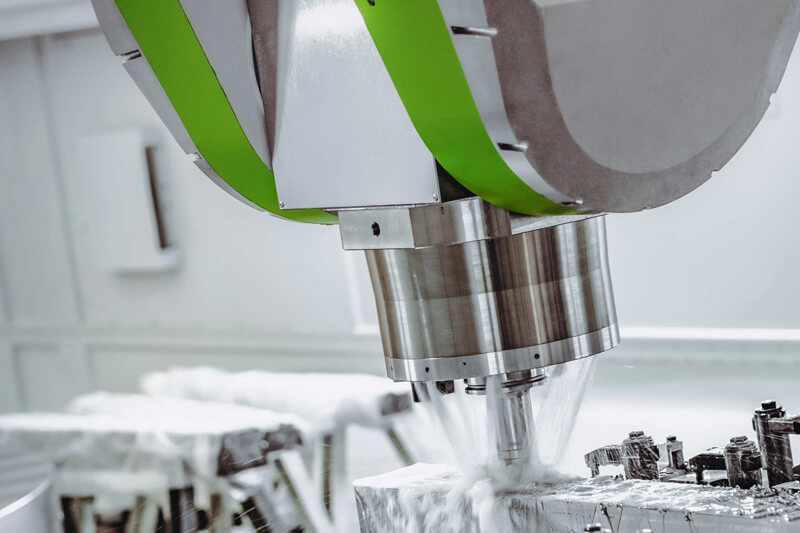
3.Practical Tips for Titanium CNC Machining
Due to the difficulty of titanium machining, many machine shops are reluctant to use this cutting-edge material. Yet, many manufacturers choose to use titanium to produce high-quality parts because of its superior qualities. Fortunately, skilled CNC machinists and toolmakers have developed useful tips for machining titanium.
1) Secure the Part
Anything you can do to reduce vibration will make titanium machining easier, as titanium is prone to tool chatter. To prevent workpiece deflection, secure the part.
In addition, use a top-of-the-line CNC machine with an extremely rigid tool arrangement. To minimize tool deflection, you may even consider a shorter cutting tool.
2) Choose the Right Cutting Tool
Due to the growing demand for titanium, toolmakers are developing new strategies to improve titanium machinability. Cutting tools with titanium carbonitride (TiCN) or heat-resistant titanium aluminum nitride (TiAlN) coatings can extend tool life.
Overall, machinists should select high-quality titanium-specific tools and regularly inspect and replace worn equipment. Also, consider using smaller diameter tools with more cutting edges to ensure that workpiece removal rates remain stable while limiting heat buildup.
3) Consider Cutting Parameters
Temperature control must be carefully controlled when machining titanium alloys. Applying a steady stream of high-pressure coolant to the cutting area is one of the most direct ways to keep the workpiece and tool cool. If the chips are blown away from the cutting area, they will not stick to the machining tool.
In addition, feed rate, spindle speed and chip load must be considered when machining titanium alloys. This requires limiting the pressure on the tool and equipment and avoiding staying in one place too long. Another cutting strategy, such as increasing the axial depth of cut while reducing radial engagement, may also be worth investigating to improve cutting efficiency and reduce machining temperatures.
4) Use high-pressure cooling systems to prevent overheating
Titanium CNC machining requires a very small portion of the tool radius to be in contact, very sharp, and very small feeds per tooth. However, this can cause heat that is difficult to remove from the work area. If left unchecked, it will eventually damage our cutting tools, and the thermal effects can make it challenging to maintain tolerances. Therefore, use the best possible coolant settings when cutting titanium alloys.
High-pressure cooling systems are an effective aid. The spindle may also be essential, depending on the application. Increasing the coolant concentration may also be beneficial when machining titanium alloys.
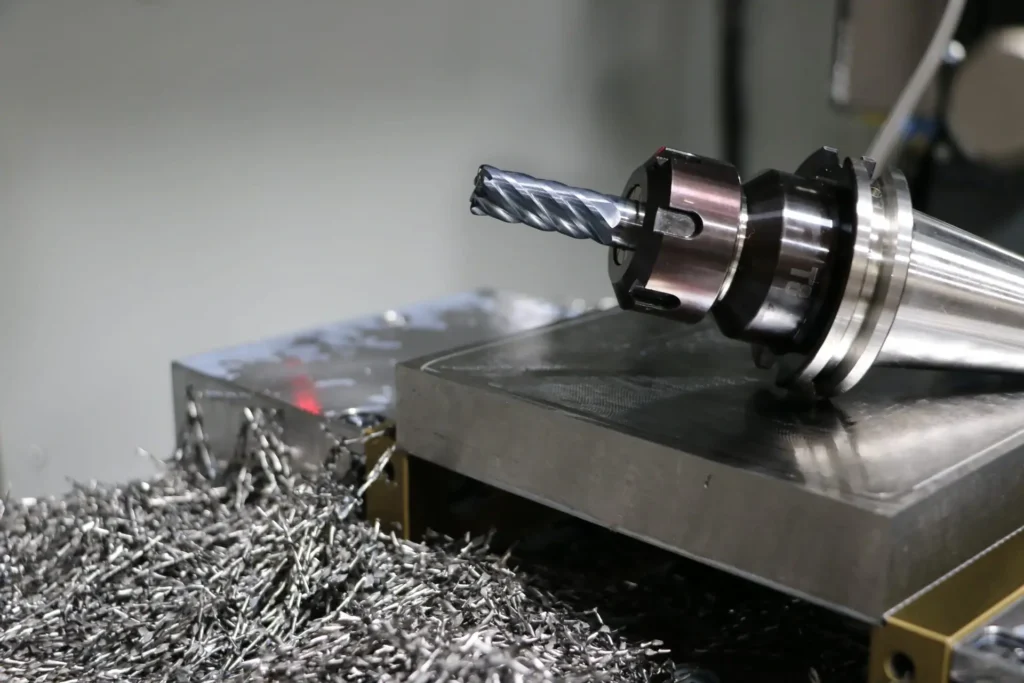
4.Different Titanium Alloy Grades for CNC Machining
There are various grades of titanium and titanium alloys, each with its ideal uses, advantages, and disadvantages. Let’s look at these grades in detail.
1) Grade 1 (Pure Titanium, Low Oxygen Content)
Of the most commonly used types of titanium alloys, this titanium alloy is the softest and most ductile. Grade 1 titanium alloys have excellent machinability, impact toughness, corrosion resistance, and formability.
On the downside, it has lower strength compared to other grades of titanium alloys. This grade of titanium alloy is suitable for medical, automotive, and aerospace industries.
2) Grade 2 (Pure Titanium, Standard Oxygen Content)
This is also known as workhorse titanium. It has high corrosion resistance, strength, formability, weldability, ductility, and low strength. Grade 2 titanium can be used in the medical and aerospace industries for the production of aircraft engines.
3) Grade 3 (Pure Titanium, Moderate Oxygen Content)
While this titanium is less commercially popular than Grades 1 and 2, it has good mechanical properties. It has high corrosion resistance as well as machinability and strength. It is used in the medical, marine, and aerospace industries.
4) Grade 4 (Pure Titanium, High Oxygen Content)
This grade of titanium has high strength and corrosion resistance. However, it is not easily machined and usually requires large amounts of coolant and feed rates. Grade 4 titanium can be used in cryogenic vessels, CPI equipment, airframe components, heat exchangers, etc.
Grades 1-4 above are all pure titanium, and the next section describes different grades of titanium alloys.
5) Grade 5 (Ti6Al4V)
Grade 5 titanium alloy contains 4% vanadium and 6% aluminum. It is not as strong as the other alloys, but has high corrosion resistance and formability. It is ideal for power generation, offshore and marine applications, and critical airframe structures.
6) Grade 6 (Ti 5 Al-2.5Sn)
This titanium alloy has good stability, strength, and weldability, especially at high temperatures, and can be used in the production of airframes and jet engines.
7) Grade 7 (Ti-0.15Pd)
This grade of titanium alloy is similar to Grade 2, the only difference being the addition of palladium to improve its corrosion resistance. Grade 7 titanium alloy has excellent formability and weldability. It is well suited for the production of chemical processing equipment.
8) Grade 11 (Ti-0.15Pd)
Grade 11 titanium is very similar to Grade 7. However, it is more ductile and less tolerant of other impurities. It is weaker than Grade 7 and can be used in the marine and chlorate manufacturing industries.
9) Grade 12 (Ti0.3Mo0.8Ni)
Grade 12 titanium alloy is expensive, has 0.8% nickel and 0.3% molybdenum, and has excellent weldability, high temperature strength, and corrosion resistance. It can be used for housings and heat exchangers, marine and aircraft parts, etc.
10) Grade 23 (T6Al4V-ELI)
Grade 23 titanium alloy, also known as ultra-low interstitial titanium alloy or TAV-EIL, has similar properties to grade 5 titanium alloy, but is purer. Grade 23 titanium alloy has good fracture toughness and biocompatibility, but relatively poor machinability. Grade 23 titanium alloy can be used to produce orthopedic pins, screws, surgical nails and orthodontic appliances.
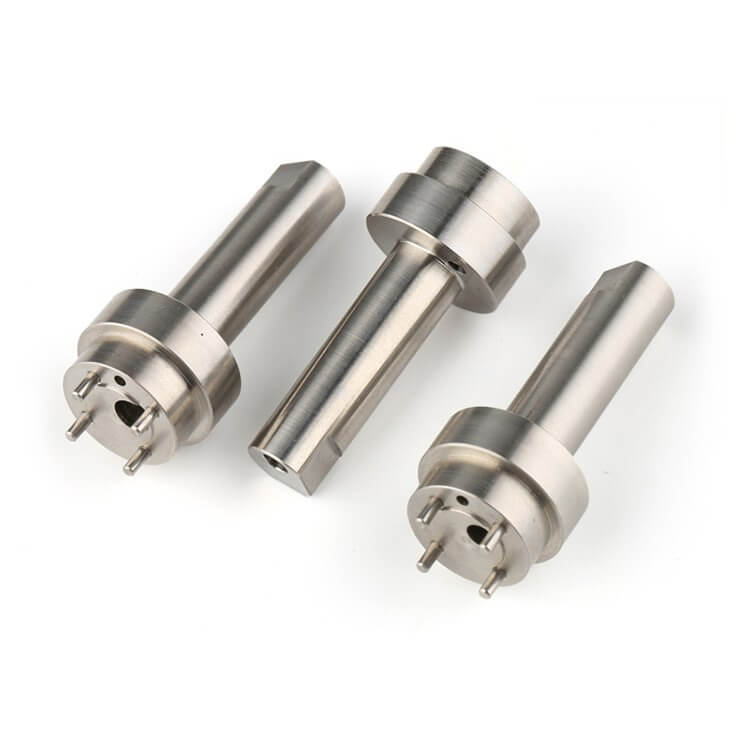
5.How to choose the right titanium CNC machining tool?
It is usually a bad idea to use any cutting tool when machining titanium alloy with CNC. Here is how to choose the right cutting tool for milling titanium alloy or using other CNC machining techniques.
1) Consider the number of cutting edges of the cutting tool
You must increase the number of cutting edges of the end mill to shorten the product processing cycle. For titanium alloys, the more teeth there are, the less chatter. For example, a 10-flute end mill, while suitable for chip loads in most materials, is very suitable for titanium alloys. This is mainly due to the need to reduce radial engagement.
2) Avoid interrupted cuts and keep the cutting edge sharp
Due to its low Young’s modulus, titanium is both strong and resilient. This means that in order to efficiently and frictionlessly remove chips from the surface, we need a sharp tool.
Avoid interrupted cuts whenever possible, as they can hammer chips into a sharp tool, which can cause premature tool failure.
3) Consider cutting tool coatings
Coatings can greatly improve a tool’s ability to withstand the heat generated by titanium. TiAlN (titanium aluminum nitride) is a suitable coating to consider. It has lubricity and resists built-up edge, galling, and chip welding, and is particularly suited to the temperatures during machining.
4) Try high-feed milling cutters when CNC machining titanium
High-feed milling cutters are suitable for maintaining low engagement when machining titanium alloys in both the axial and radial directions. These tools are built to perform this task effectively.
6.Surface treatment of titanium CNC machined parts
A range of surface treatment techniques, including titanium polishing, can enhance the functionality and aesthetics of CNC machined titanium products.
These surface treatments include:
- Polishing
- Anodizing
- Chrome Plating
- Powder Coating
- PVD Coating
- Brushing
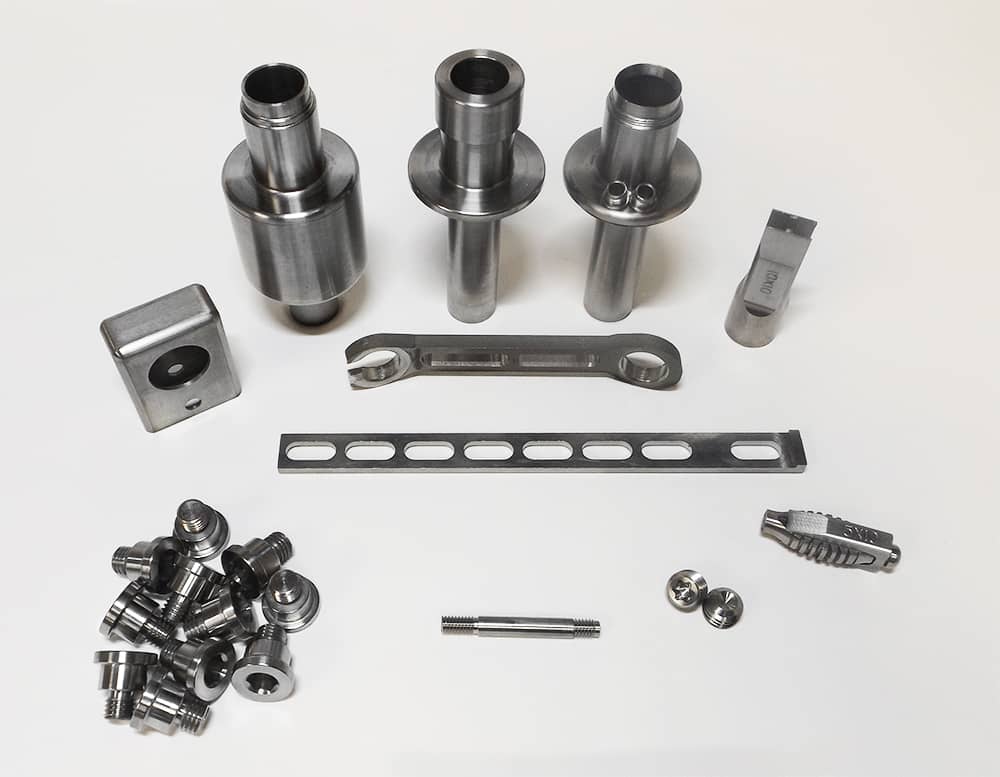
7.Applications of Titanium CNC Machining Parts
Titanium machined parts are durable, corrosion resistant, and aesthetically pleasing. These properties make them suitable for a variety of industries.
1) Marine/Navy Industry
Titanium has a higher corrosion resistance than most natural metals. This corrosion resistance makes it an ideal material for the production of propeller shafts, underwater robots, rigging equipment, ball valves, marine heat exchangers, fire protection system pipes, pumps, exhaust pipe bushings, and shipboard cooling systems.
2) Aerospace
Titanium is a highly sought-after material in the aerospace industry due to its many excellent properties. These properties include a high strength-to-weight ratio, excellent corrosion resistance, and the ability to survive extreme heat environments.
Titanium parts in the aerospace industry include seat components, turbine components, shafts, valves, housing and filter components, and oxygen generation system components.
3) Automotive
In the automotive field, the titanium vs. aluminum debate has been raging, with aluminum having the upper hand due to its availability and cost-effectiveness. Despite this, titanium is still used in the production of automotive parts.
The main uses of titanium and its alloys in the automotive sector are in the production of valves for internal combustion engines, valve springs, retainers, automotive fender brackets, suspension nuts, engine piston pins, suspension springs, brake caliper pistons, engine rocker arms and connecting rods.
4) Medical and Dental
Titanium has a variety of applications in the medical industry due to its high corrosion resistance, low electrical conductivity and physiological pH.
Titanium parts used in the medical industry include tapered, straight or self-tapping bone screws, dental implant screws, skull screws for cranial fixation systems, spinal fixation rods, connectors and plates, orthopedic pins, etc.
8.Conclusion
Titanium and its alloys require careful processing to achieve optimal part production. It is a very different metal from similar metals such as steel and brass. It requires the use of the right tools, expertise and patience.
If you are looking for an experienced CNC machining manufacturer, Xavier is your ideal choice. The Xavier team is well-equipped to provide high-quality CNC machining solutions. If you need more information or to discuss your machining needs with us, please feel free to contact us.