Uncovering the Secrets to High-Quality CNC Machined Titanium Products
Are you ready to enter the world of titanium CNC machining? If you are an engineer, designer, or manufacturer looking to master CNC machining methods such as rolling machining, you have come to the right place.
In this article, I will guide you through the complexities of titanium CNC machining, providing valuable insights, best practices, and practical applications. Together, we will unlock the potential of titanium in CNC machining. Let’s get started!
1.Titanium CNC Machining Basics
1) What is CNC Machining?
Short for Computer Numerical Control Machining, CNC machining is a precise and automated manufacturing process that has revolutionized the production industry. It allows us to create complex parts with extreme precision. Let’s take a deeper look at this remarkable technology.
2) Why Titanium?
Titanium is a metal known for its exceptional properties, making it a popular choice across a wide range of industries. Titanium’s light weight, high strength, and corrosion resistance have solidified its place in fields such as aerospace, medical, and automotive manufacturing. To further understand why titanium is a great choice for CNC machining, let’s explore its unique properties and benefits.
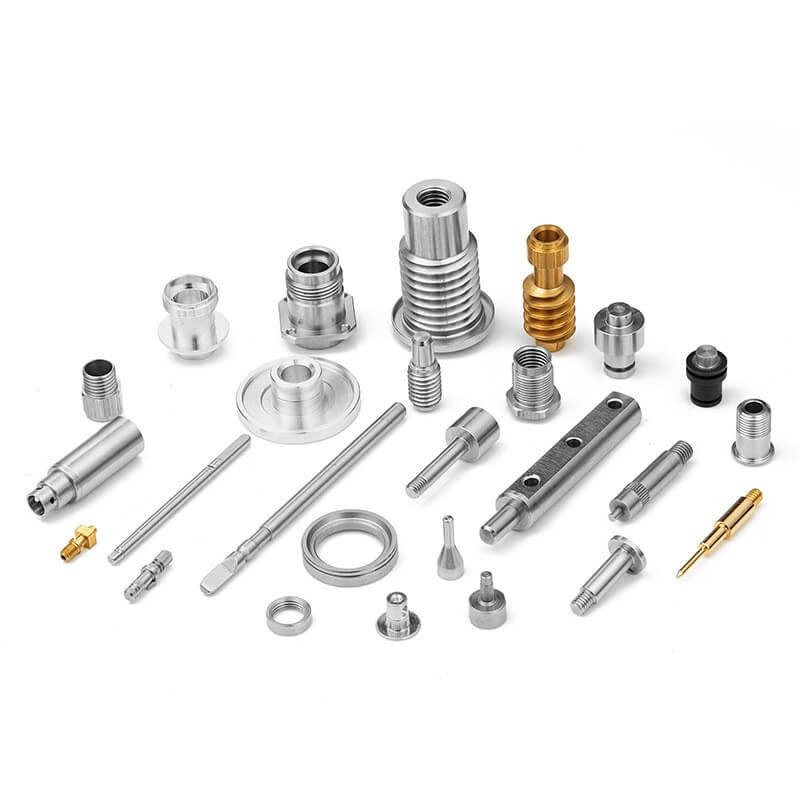
2.Titanium CNC Machining Process
1) Basic Steps of CNC Machining
CNC machining follows a clearly defined process that ensures precision and efficiency. Here, we will break down each step to give you a comprehensive understanding of the entire process:
Step 1: Design and CAD Modeling
- Description: The CNC machining process begins by creating a 3D model of the desired component using computer-aided design (CAD) software.
- Importance: This step lays the foundation for the entire process and allows engineers and designers to visually see the final product.
Step 2: Tool Path Planning
- Description: Specialized CAM (computer-aided manufacturing) software generates tool paths for precise cutting, ensuring that every detail of the design is accurately executed.
- Importance: Tool path planning is essential to achieving the desired results because it guides the CNC machine throughout the machining process.
Step 3: Material Fixturing
- Description: Properly fixing the titanium workpiece is essential to prevent movement during machining.
- Importance: Secure fixturing ensures that the workpiece remains stable and prevents errors during machining.
Step 4: CNC Machining
- Description: This is the heart of the process, where the CNC machine precisely shapes the titanium workpiece according to the tool path instructions.
- Importance: Precision and attention to detail in this step are essential to achieve high-quality results.
Step 5: Quality Control
- Description: After machining, a thorough inspection is performed to ensure that the product meets specifications and quality standards.
- Importance: Quality control helps identify any deviations from the expected results and ensures the integrity of the final product.
2) Tool and Material Selection
When CNC machining titanium alloys, it is essential to select the appropriate cutting tools and understand the material properties. The following factors must be considered:
① Cutting Tools
- Description: Titanium-specific cutting tools are essential for efficient and effective machining.
- Importance: The choice of cutting tools directly affects the quality of the final product. Selecting the right tool ensures smoother operation and extends tool life.
② Cutting Speed and Feed
- Description: Optimizing cutting speed and feed rate is essential to achieve the best results in CNC machining titanium.
- Importance: Properly balanced cutting speeds and feeds are essential for efficient chip formation and preventing tool wear.
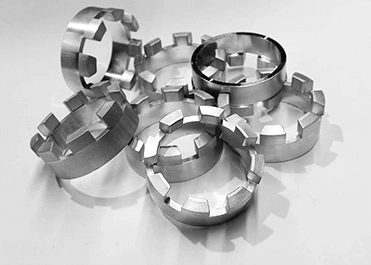
3.Best Practices for Titanium CNC Machining
1) Optimizing Cutting Parameters and Coolants
To achieve perfection in CNC machining of titanium alloys, it is necessary to delve into optimizing various parameters. Let’s explore these aspects in more detail:
① Cutting Speeds and Feed Rates
- Description: Adjusting cutting speeds (measured in surface feet per minute (SFM)) and feed rates (measured in inches per minute (IPM)) requires a delicate balance. Too high a speed or feed rate can cause tool wear and overheating, while too low a speed or feed rate can result in inefficient machining.
- Importance: Fine-tuning these parameters is critical. Specific tool manufacturers provide data on recommended speeds and feeds, which should be used as a starting point and then adjusted based on your specific setup and material conditions.
② Coolant Selection
- Description: Coolant plays a vital role in controlling the heat generated during machining. Options include water-soluble coolants, oils, and compressed air. The choice depends on factors such as workpiece size, tool type and machine capabilities.
- Importance: The right coolant not only dissipates heat, but also prevents thermal expansion and workpiece deformation. The right choice can minimize heat-related problems and extend tool life.
4.Avoid Common Pitfalls
Let’s explore the common pitfalls of CNC machining titanium alloys and how to effectively solve them:
1) Chip Management
- Description: Titanium alloys produce tightly curled chips, which can affect the process if not handled properly. Proper chip evacuation systems, chip breakers and tool geometry should be used.
- Importance: Efficient chip management ensures that chips are not cut again, which avoids poor surface finish and tool wear. It also prevents workpiece contamination.
2) Tool Wear and Replacement
- Description: Monitoring tool wear is essential to maintaining machining quality. Tools need to be checked regularly for signs of wear, chipping or dulling. Some tool wear is normal, but excessive wear can lead to poor results.
- Importance: Timely tool replacement prevents surface defects, maintains machining quality and reduces the risk of tool breakage. Understanding the tool lifecycle is essential for efficient and cost-effective operations.
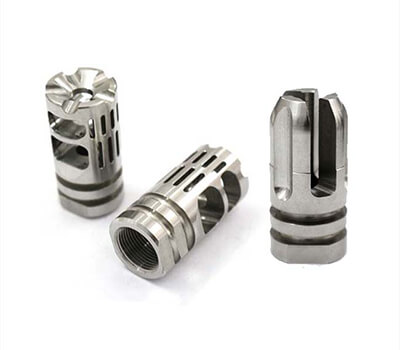
5.Practical Applications of CNC Machining Titanium Alloys
1) Aerospace
Every ounce counts in the aerospace industry, and CNC machining of titanium has been a game-changer. Titanium’s superior properties make it a top choice for applications that require high-strength materials without adding excessive weight. Examples include aircraft landing gear, engine components, and structural parts.
2) Medical
Titanium’s biocompatibility, corrosion resistance, and strength make it ideal for the medical field. CNC machining is used to create complex implants, surgical instruments, and prosthetic components, improving patient outcomes and reducing the risk of complications.
3) Automotive
Titanium is making inroads into the automotive industry, primarily for high-performance and luxury vehicles. CNC machining is used to produce lightweight yet strong components, such as exhaust systems, suspension components, and engine parts. Reducing vehicle weight is essential to improving fuel efficiency and overall performance.