Casting: A common method for producing aluminum parts by pouring molten aluminum into a mold
Aluminum is a versatile and widely used material in various industries, thanks to its lightweight, durability, and excellent thermal and electrical conductivity. When it comes to manufacturing aluminum parts, there are several different methods available. One of the most common methods is casting, which involves pouring molten aluminum into a mold.
Production methods of aluminum parts
Casting is a widely used method for producing aluminum parts due to its cost-effectiveness and versatility. It allows for the creation of complex shapes and intricate designs that may be difficult or impossible to achieve with other manufacturing processes. The process begins with the creation of a mold, which can be made from various materials such as steel, sand, or plaster. The mold is then filled with molten aluminum, which is allowed to cool and solidify. Once the aluminum has solidified, the mold is removed, leaving behind the desired aluminum part.
There are several different types of casting methods that can be used to produce aluminum parts. One common method is sand casting, which involves creating a mold by compacting sand around a pattern of the desired part. The molten aluminum is then poured into the mold, and once it has solidified, the sand is removed to reveal the finished part. Sand casting is a versatile method that can be used to produce parts of various sizes and complexities.
Another casting method is investment casting, also known as lost wax casting. The method involves creating a wax pattern of the desired part, which is then coated with ceramic material. After the ceramic-coated model is heated, the wax melts and flows out, leaving a cavity in the shape of the part. Molten aluminum is then poured into the mold cavity, and once solidified, the ceramic shell is broken open to reveal the finished part. Investment casting is often used to produce parts with intricate details and high dimensional accuracy, ensuring an extremely high level of detail and precision.
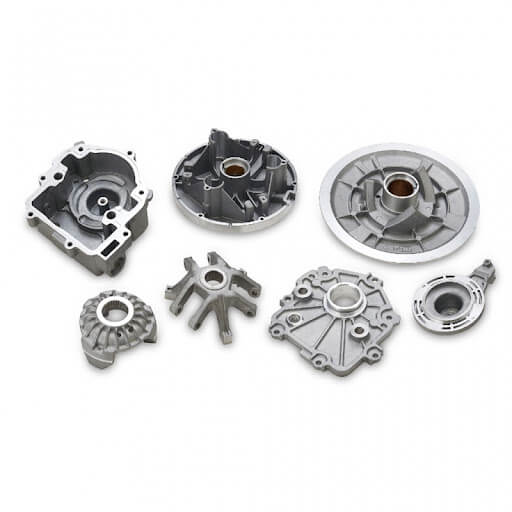
Die casting is another popular method for producing aluminum parts. This method involves injecting molten aluminum into a steel mold, known as a die, under high pressure. The molten aluminum quickly solidifies, and the die is opened to remove the finished part. Die casting is a highly efficient method that allows for the production of large quantities of parts with excellent dimensional accuracy and surface finish. It is commonly used in the automotive and electronics industries.
In addition to these casting methods, there are also other ways to produce aluminum parts. For example, extrusion involves forcing heated aluminum through a shaped die to create long, continuous profiles with a consistent cross-section. This method is often used for producing aluminum bars, rods, and tubes. Another method is forging, which involves shaping heated aluminum by applying compressive forces. Forging is commonly used for producing high-strength aluminum parts such as aircraft components.
In conclusion, there are several different methods available for producing aluminum parts. Casting, including sand casting, investment casting, and die casting, is a common method that allows for the creation of complex shapes and intricate designs. Other methods such as extrusion and forging are also used for producing aluminum parts with specific characteristics. Each method has its own advantages and limitations, and the choice of method depends on factors such as the desired part design, quantity, and cost considerations.