Understanding the Importance of Accuracy in CNC Machining
CNC machining is a widely used manufacturing process that involves the use of computer-controlled machines to create precise and accurate parts. Precision is an important aspect of CNC machining because it determines the quality and functionality of the final product. Sawing machining is often used to remove large pieces of material without paying much attention to tolerances. Parts like those on the hoover washing machine parts list and hotpoint washing machine parts list are more focused on this aspect.
In this article, we will take a deeper look at the importance of precision in CNC machining and explore the concepts of precision and tolerance.
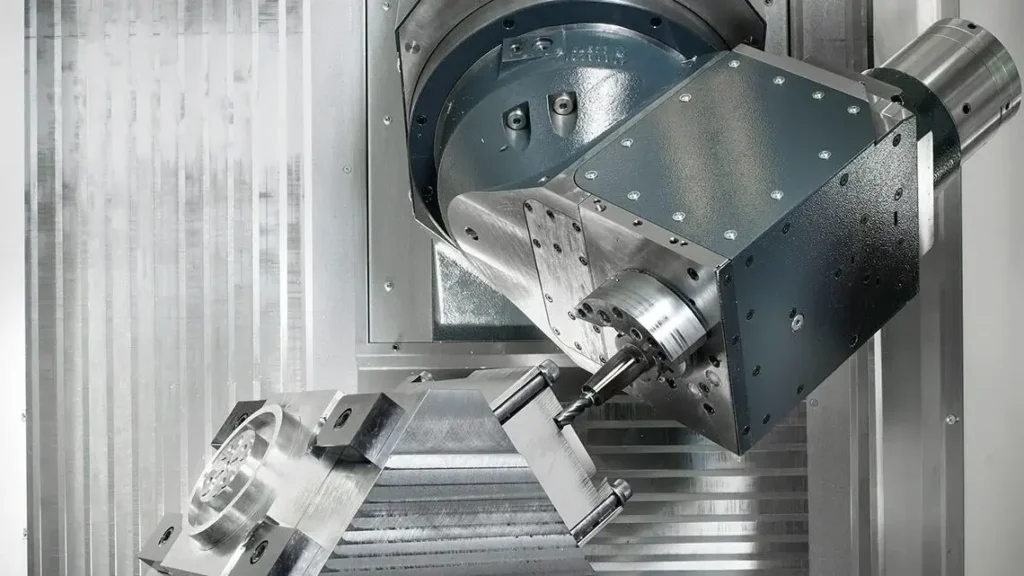
1.The concepts of precision and tolerance
Accuracy refers to how close a measurement or result is to the true or desired value. In CNC machining, accuracy is essential to ensure that the dimensions and specifications of the parts being produced are within the required tolerances. Tolerances are the allowable variations in dimensions, and they play a significant role in determining the accuracy requirements for a particular part. For example, in the aerospace or medical industries where precision is critical, tolerances are often very tight, requiring CNC machining to be very precise. Also included are parts on the hoover washing machine parts list and hotpoint washing machine parts list.
2.The importance of accuracy
The importance of accuracy in CNC machining cannot be overstated. Inaccurate parts can cause a range of problems, including poor fit, functionality issues, and even safety hazards. For example, in the automotive industry, small deviations in engine component dimensions can lead to performance degradation or even catastrophic failure. Therefore, manufacturers must ensure that their CNC machines can consistently produce accurate parts to ensure safe use.
Precision is another crucial aspect of CNC machining. While accuracy refers to how close a measurement is to the desired value, precision refers to the level of consistency and repeatability in producing the same measurement. In other words, precision is about minimizing variations in the dimensions of the parts being produced. Achieving high precision in CNC machining requires not only accurate machines but also careful calibration and maintenance.
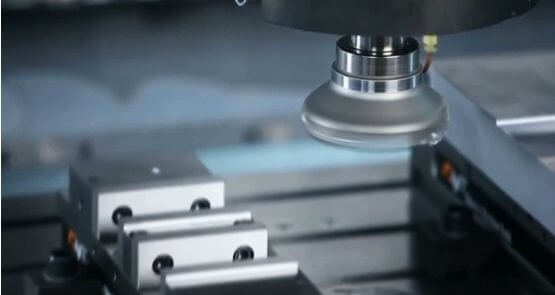
To ensure accuracy and precision in CNC machining, manufacturers employ various techniques and strategies. One common approach is to use high-quality machines and tools that are designed to minimize errors and deviations. Additionally, regular calibration and maintenance of the machines are essential to keep them operating at their optimal performance levels. This includes checking and adjusting the machine’s settings, such as spindle speed, feed rate, and tool offsets.
Furthermore, the selection of appropriate cutting parameters, such as cutting speed and depth of cut, can significantly impact the accuracy and precision of CNC machining. Manufacturers must carefully analyze the material properties, part geometry, and desired surface finish to determine the optimal cutting parameters. This requires a deep understanding of the machining process and the ability to make informed decisions based on the specific requirements of each part.
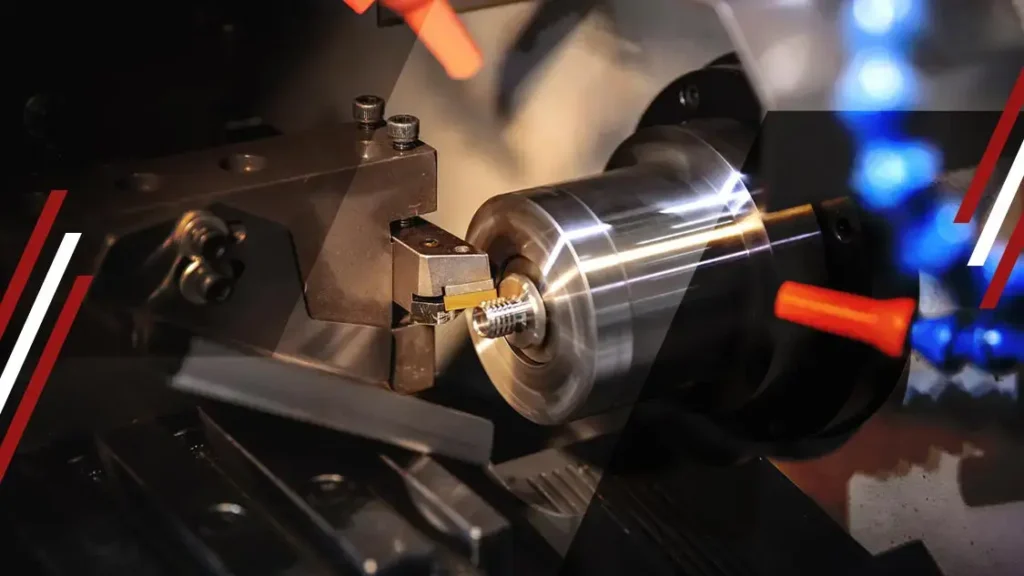
In conclusion, accuracy, precision, and tolerances are critical aspects of CNC machining. Achieving high levels of accuracy and precision is essential to ensure that the parts being produced meet the required specifications and tolerances. Inaccurate or imprecise parts can lead to functional issues, poor fit, and safety hazards. Therefore, manufacturers must invest in high-quality machines, proper calibration, and maintenance, as well as careful selection of cutting parameters to achieve the desired accuracy and precision in CNC machining. By prioritizing accuracy, manufacturers can produce high-quality parts that meet the stringent requirements of various industries.