The Best Guide to Tool Steels: Types, Properties and Uses
In the field of CNC machining, choosing the right tool material is crucial. Tool steel stands out among many materials due to its unique properties, making it an ideal choice for cutting and processing materials. This article will deeply interpret its types, properties and uses, helping you to accurately choose tools that meet your needs in CNC machining.
1、What is tool steel?
Tool steel is composed of different types of strong carbon and alloy steels. It has high hardness, wear resistance, bending resistance and other characteristics. It is particularly suitable for making reamers, drills, machine molds and hand tools. It can maintain a sharp edge even at high temperatures, thanks to its composition containing carbide-forming elements such as chromium, vanadium, molybdenum, tungsten, as well as elements such as cobalt and nickel. It is widely used in tasks such as metal stamping, forming, shaping, cutting and plastic forming.
2、Composition of tool steel
Tool steel is made of metals such as chromium, molybdenum, tungsten, and vanadium mixed with iron, and contains a large amount of carbon to enhance strength and form hard carbides. The addition of nickel and cobalt makes the steel stronger at high temperatures, while the addition of chromium, molybdenum, tungsten, and vanadium makes it hard and wear-resistant.
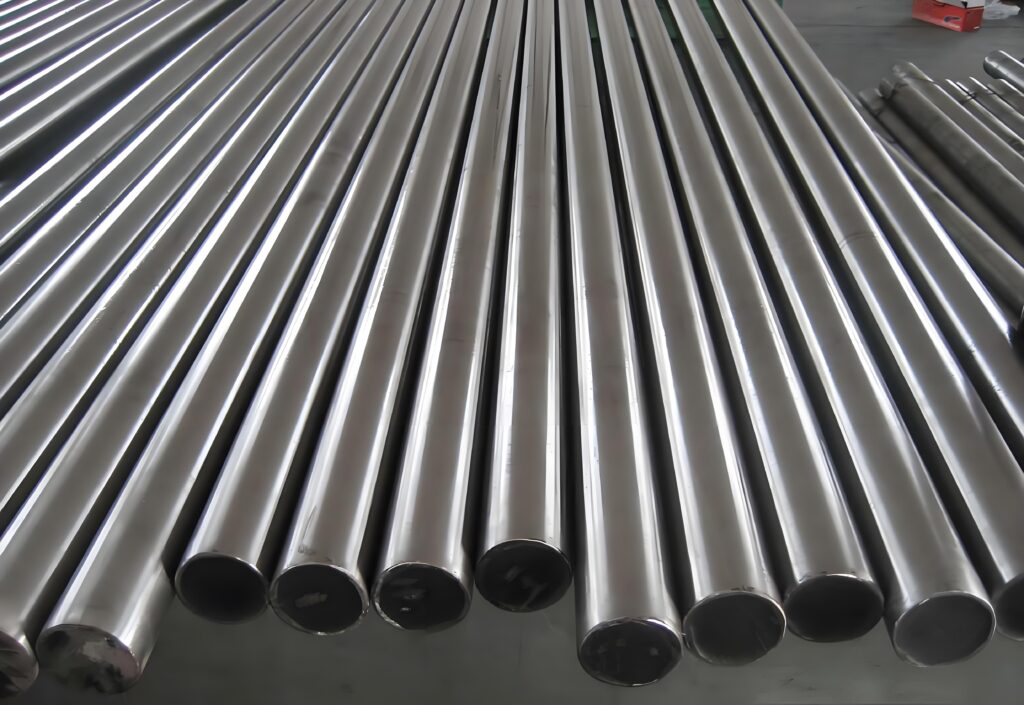
3、Main types of tool steel
Ⅰ.High-speed steel (M, T grade)
Type
High-speed steel (HSS) is divided into M type (molybdenum-based) and T type (tungsten-based). M type high-speed steel has a shorter hardening range, lower hardening temperature, slightly lower hardness than T type high-speed steel, but more durable. The most common one is M2 high-speed steel. T type high-speed steel is harder and more wear-resistant because it contains tungsten and vanadium.
Features
High-speed steel can withstand high temperatures while maintaining hardness. It is called high-speed steel because it can achieve better tool speed and feed rate than ordinary high-carbon steel.
Main uses
Commonly used in the manufacture of drill bits, tool bits, electric saw blades, milling cutters, gear cutters, etc.
Ⅱ.Water-hardening tool steel (W grade)
Composition and characteristics
High carbon content, need to be quenched in water. Low alloy content, cheap price, often used in basic applications.
Performance limitations
Cannot withstand high temperatures, easy to break, water quenching easily leads to warping and cracking.
Application fields
Usually used to manufacture blades, cold heading dies, lathe tools, embossing tools, reamers and industrial cutting tools, etc.
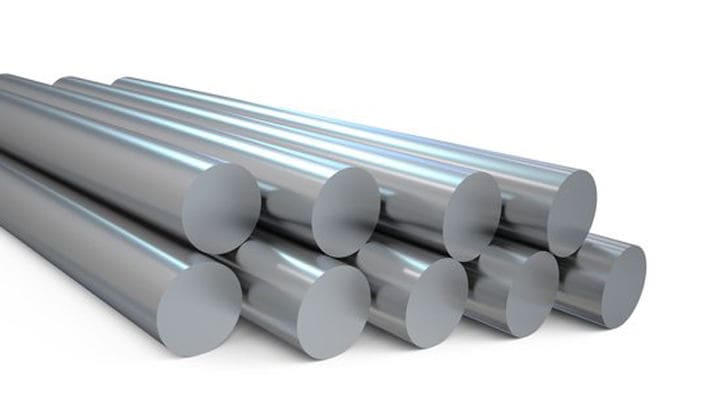
Ⅲ.Cold work tool steel (A, O, D grades)
Features
Medium hardness, strong wear resistance and easy hardening, used to manufacture large parts or parts that need to maintain shape after hardening, divided into three groups: air hardening (A grade), oil hardening (O grade) and high carbon chromium (D grade).
Air quenching or A grade
It has good hardening ability and a lower hardening temperature range, small deformation, easy processing, good toughness and wear resistance. Commonly used in casting, cams, mold bending, rods and blanking, etc.
Oil hardening or O grade
It is oil-quenched during the production process. Its high strength and wear resistance make it suitable for a variety of jobs, such as main engraving rollers, thread cutting rollers, punches, bushings and sleeves, etc.
High carbon chromium or D grade
Contains 11-13% chromium, carbon content 1.4-2.5%, low corrosion resistance but good wear resistance, can be oil or air hardened and has small deformation, used to manufacture tools, plastic injection molds, etc.
Ⅳ.Hot working tool steel (H grade)
Composition and properties
Usually contains a large amount of different metals, but the carbon content is not high, and the heat resistance is good. The most commonly used is H13 type.
Application range
Suitable for manufacturing materials such as metals and glass that require high temperature processing. It is often used in the manufacture of cold heading mold shells and hot extrusion processes of magnesium or aluminum.
Types
Molybdenum-based: contains a large amount of molybdenum, has strong wear resistance, is stable at high temperatures, and is suitable for extreme conditions such as metal milling cutters or molds.
Tungsten-based: contains 9-18% tungsten and 2-4% chromium, has good heat resistance but is brittle, and needs to be preheated before use.
Chromium-based: contains 3-5% chromium and may contain less than 5% of other alloying elements. It is often used in plastic injection mold manufacturing, hot forging and hot working punches.
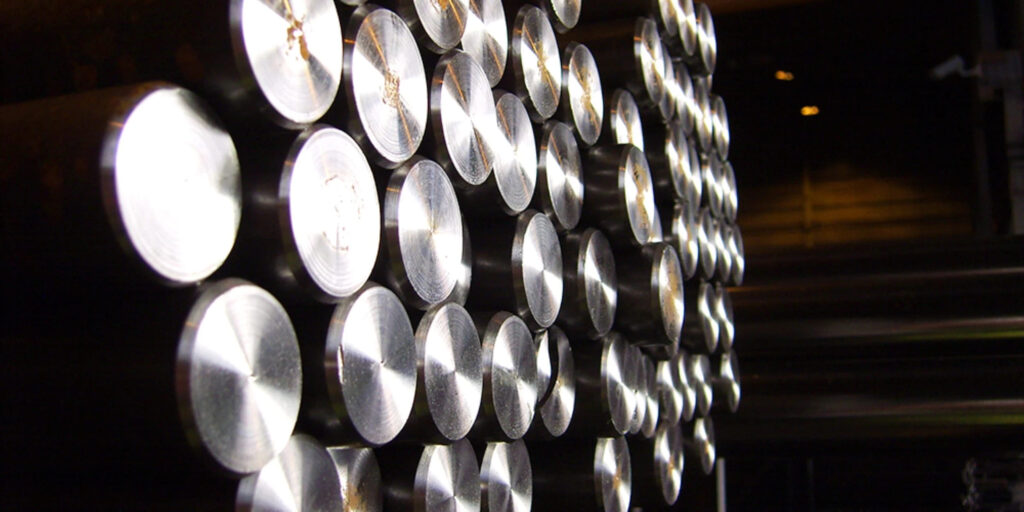
Ⅴ.Impact-resistant tool steel (S grade)
Performance characteristics
Designed to handle stress at low temperatures and has good thermal hardness. Known for its strong impact toughness, it has poor wear resistance and cannot handle high temperatures, with an ultimate temperature of 537°C.
Application fields
Used in blacksmith chisels, boiler shop tools, tool chuck jaws, chucks, clutch parts, jackhammer parts, hot and cold forging dies, hot and cold shear blades and chipper knives, etc.
Ⅵ.Mold steel (P grade)
Features
Mold steel used to make plastic parts, suitable for mold and mold manufacturing processes such as cold stamping, hot forging, die casting and plastic injection molding.
Performance
It has strong comprehensive toughness, corrosion resistance, hardness and wear resistance, high impact strength and is easy to polish. Commonly used models include P20 and 420 (highly refined, high-quality stainless steel).
Ⅶ.Special purpose tool steel (Grade F, L)
Classification and characteristics
It is more expensive than the general W grade and is divided into two categories: low alloy (L type) and carbon tungsten based (F type). Has special composition and qualities for specific uses that ordinary W-steel cannot handle.
L type
Suitable for applications requiring high toughness and wear resistance, such as bearings, clutch plates, rollers, wrenches, cams and chucks.
Type F
Water hardened and much more wear resistant than Type W. Ideal for applications requiring high wear resistance but not high temperature or impact resistance, such as scissors, broaches, polishing tools, reamers and plug gauges.
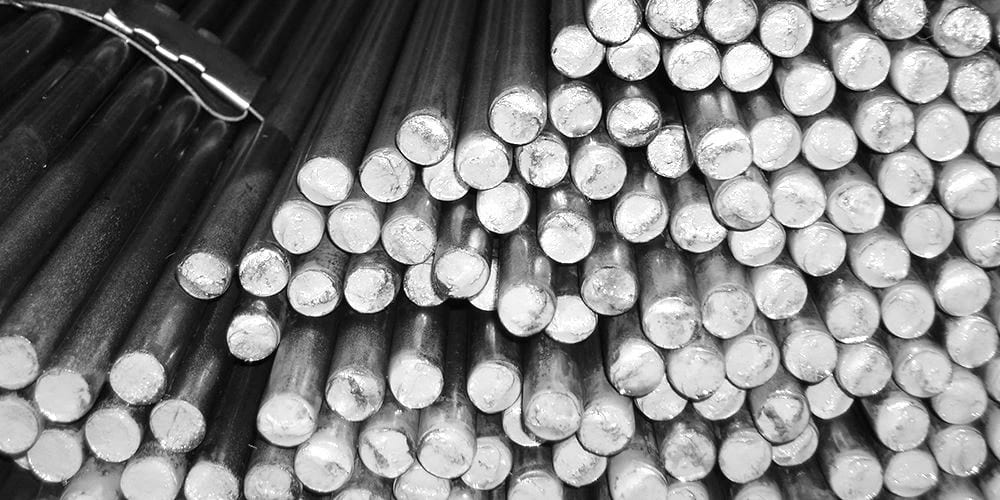
4、Manufacturing method of tool steel
1.Electric Arc Furnace (EAF)
The Electric Arc Furnace (EAF) process is one of the common methods for manufacturing tool steel. It involves melting recycled scrap steel along with alloy components in an electric arc furnace. To prevent oxidation, the molten mixture is treated with chemicals and poured into large ladles. After removing impurities during the refining stage, the steel can be poured into large molds to form ingots.
2.Electroslag Refining (ESR)
The progressive melting process can produce ingots with smooth surfaces and no holes or defects, resulting in high-quality steel with minimal defects.
3.Powder Metallurgy
The use of powdered metal to manufacture tool steel has enhanced hardenability and machinability, and is suitable for high-carbon tool steels and aerospace components, etc.
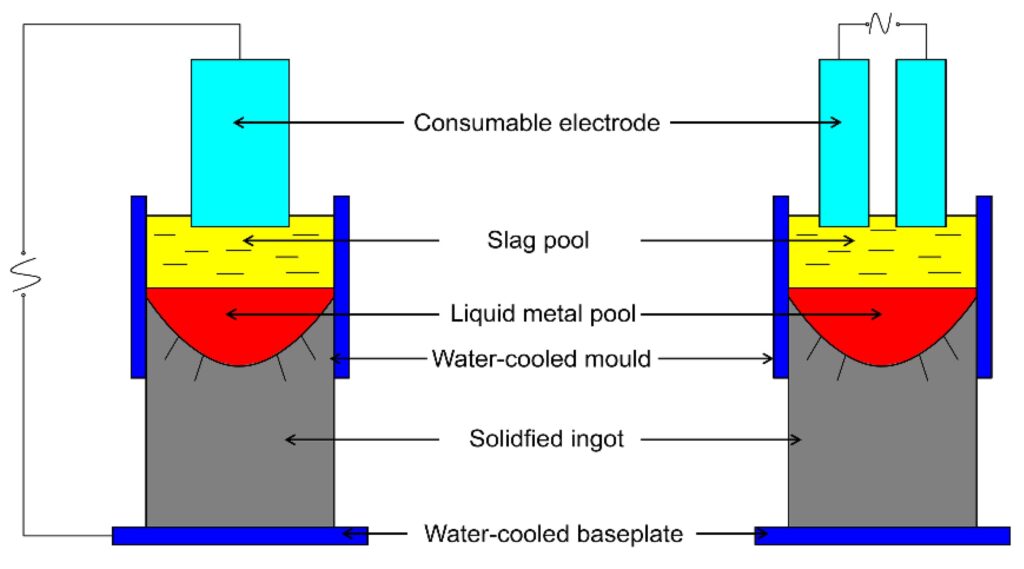
5、Common steps in tool steel manufacturing
1.Annealing
The annealing process involves heating the steel to a specific temperature and holding it for a period of time before cooling. This helps change the molecular structure of the steel, making it less brittle and more machinable.
2.Hot or cold drawing
Hot drawing is performed at high temperatures and allows tool steels to achieve tighter tolerances and unique shapes; cold drawing is usually limited to a single pass of light drawing to prevent the stock from breaking.
6、Main properties of tool steel
1.Wear resistance
Work wear resistance is one of its important properties, which can resist wear during use and extend the service life of the tool. Wear resistance can be increased by adding alloying elements.
2.Heat resistance
Tool steel maintains its performance stability at high temperatures without softening or deformation. Different types have different degrees of heat resistance.
3.Toughness
Toughness measures the steel’s ability to resist fracture. Tool steel needs to have a certain toughness to prevent brittle fracture during use, and adding alloying elements can improve toughness.
4.Hardness
Hardness measures the degree to which steel resists deformation. The Rockwell C test is often used to determine the hardness of tool steel.
The hardness of quenched cold-worked tool steel is usually around 58/64 HRC (Rockwell hardness C), most of the hardness is between 60/62 HRC, and some of the hardness is sometimes as high as 66 HRC.
7、Tool Steel Performance Comparison
O1
Oil-quenched tool steel, easy to machine.
Good wear resistance and toughness.
Best hardness response at low temperatures, high dimensional stability during hardening.
Up to HRC 65.
W1
Water-quenched tool steel.
Excellent wear resistance, good toughness.
Up to HRC 68.
A2
Air-quenched tool steel.
Higher heat and wear resistance than O1.
High dimensional stability, less distortion.
Up to HRC 63.
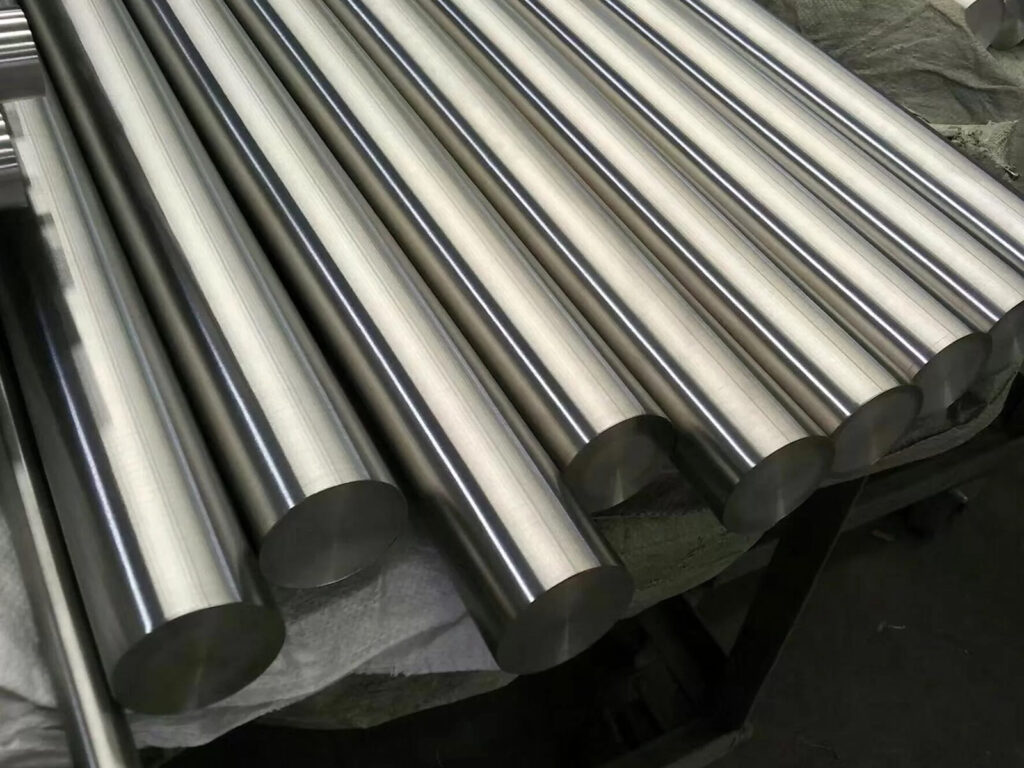
D2
High carbon, high chromium tool steel.
Ideal grade for maximum production, with excellent toughness and wear resistance, high compressive strength.
Up to HRC 65.
S7
Impact-resistant tool steel.
High strength and ductility, suitable for moderately high temperature environments.
Up to HRC 61.
P20
Special tool steel.
Suitable for machining die castings and plastic molds.
Up to HRC 32.
13
Hot work tool steel.
High resistance to thermal fatigue cracking, high hardenability, good wear resistance, good toughness.
Maximum HRC is 54.
M2
High speed tool steel.
Excellent wear resistance, good toughness.
Maximum HRC is 65.
8、What should be considered when selecting tool steel types for processing?
1.Performance
Choose the right type of tool steel for your specific tool or product.
2.Toughness
Consider fracture resistance, taking all the desired characteristics and job requirements into account. Alloy content and manufacturing process affect toughness, and hardness and toughness affect each other.
3.Wear resistance
Increased alloy content generally means higher wear resistance due to increased carbide content in the steel. Carbides are formed by alloys such as vanadium, tungsten, molybdenum and chromium combined with carbon, which enhances wear resistance but reduces toughness.
4.Compressive strength
Compressive strength measures the force an object can withstand before deforming or breaking. Elements such as molybdenum and tungsten increase compressive strength, and the higher the hardness, the better the compressive strength.
5.Processing speed
High-speed steel is best used for high-speed machining because it still provides greater wear resistance and extreme temperatures at high speeds.
6.Cost
Price is a key factor when choosing. Avoid skimping on material selection, as premature tool failure may lead to more costs.
9、Conclusion
In CNC machining, tool steel is an ideal tool material due to its unique properties. Understanding its types, manufacturing methods, properties and applications can enable us to make more accurate choices and provide strong guarantees for machining.
If you need an experienced CNC machining manufacturer, Xavier is your best choice. The Xavier team is well-equipped and can provide high-quality CNC machining solutions to meet your personalized machining needs. Please feel free to contact us.