Exploring the diversity and wide application of turned parts
Turned parts, as an important part of the field of mechanical processing, occupy an important position in modern industry with their rich variety and wide range of uses. Whether it is automobile manufacturing, aerospace, or medical equipment and precision instruments, turned parts play a key role.
The following article will take you to understand the types, uses, quality control and specific applications of turned parts.
1.Basic concepts of turned parts
(1) Definition
Turned parts refer to parts that are made by rotating the workpiece on a lathe and cutting it with a tool. This processing method occupies an extremely important position in the manufacturing industry because turned parts have the characteristics of high precision and high surface quality and are widely used in many fields such as machinery, automobiles, aerospace, etc. Turning can process various metal materials, such as steel, aluminum, copper, etc., as well as some non-metallic materials, such as plastics and wood.
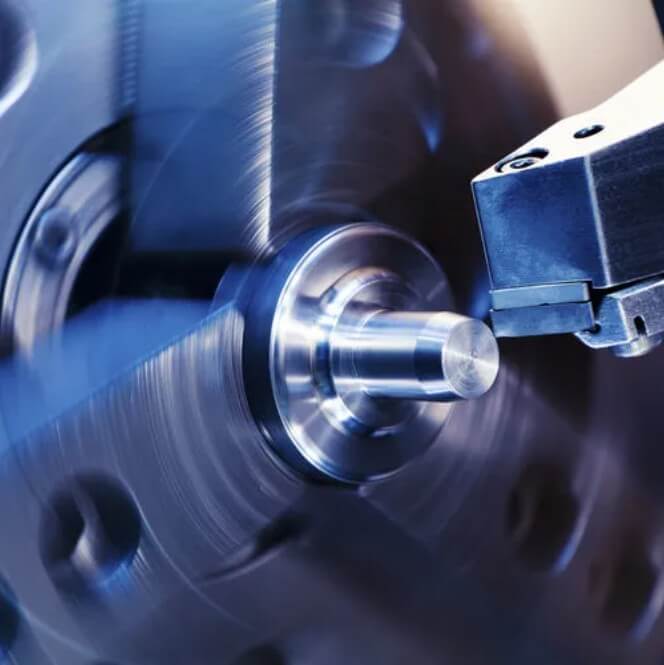
(2) Importance
The precision and surface quality of turned parts directly affect the performance and service life of the final product. For example, in the automotive manufacturing industry, key components such as the piston and cylinder of the engine need to be turned to ensure their dimensional accuracy and surface roughness to meet the requirements of high-precision matching and high-reliability operation. In the aerospace field, the high precision and high stability of turned parts are key factors to ensure flight safety and equipment performance. Therefore, turning technology has an irreplaceable and important position in modern manufacturing.
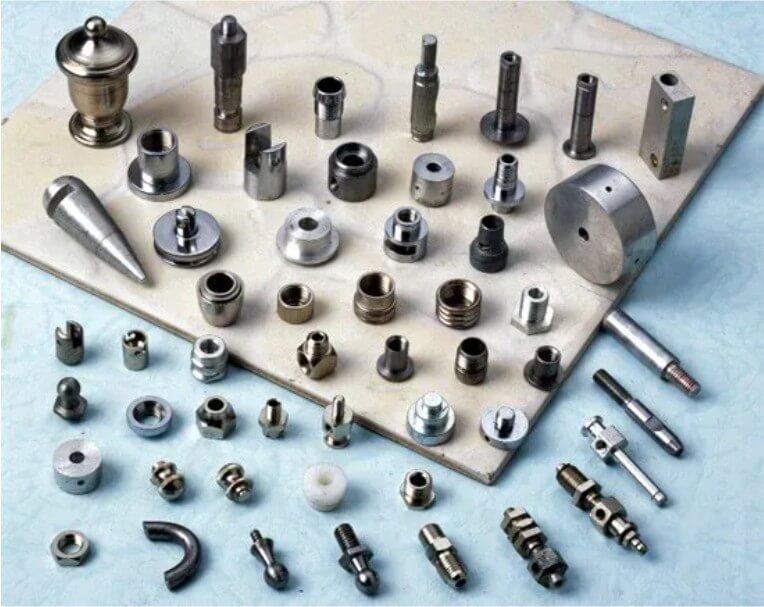
2.Types and uses of turned parts
Turned parts are a common type of parts in mechanical processing. They are processed by lathes and have a variety of shapes, sizes and uses. The following is an overview of the classification of turned parts based on different characteristics.
(1) Classification by material:
1) Metal turned parts: including steel, cast iron, aluminum, copper and their alloys. Steel turned parts are often used in situations where high strength and high hardness are required, such as bearings, gears and shaft parts; aluminum turned parts are widely used in the aviation and automotive industries due to their light weight and good corrosion resistance.
2) Non-metal turned parts: such as plastics, ceramics and composite materials. Plastic turning parts are often used to manufacture precision parts and models, while ceramic turning parts are suitable for applications in special environments due to their high hardness, high temperature resistance and corrosion resistance.
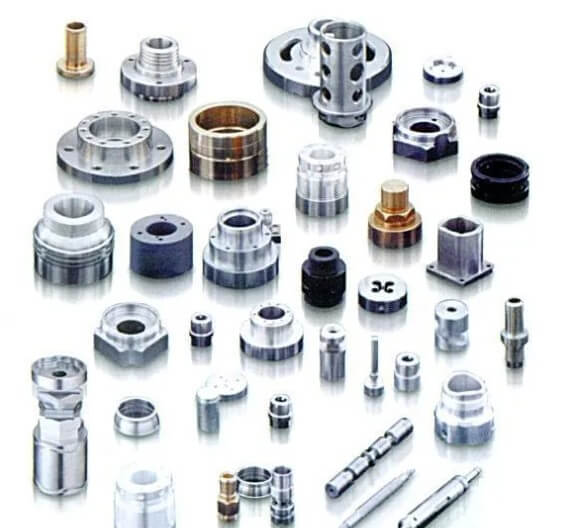
(2) Classification by shape:
1) Shaft turning parts: usually long strips with rotational symmetry, such as transmission shafts, motor shafts, etc.
2) Disc turning parts: flat in shape, often used to manufacture flanges, bearing covers and gears, etc.
3) Sleeve turning parts: with inner and outer circular surfaces, such as bushings, bearing sleeves, etc.
4) Special shape turning parts: parts processed into complex shapes according to specific needs, such as cams, eccentric wheels, etc.
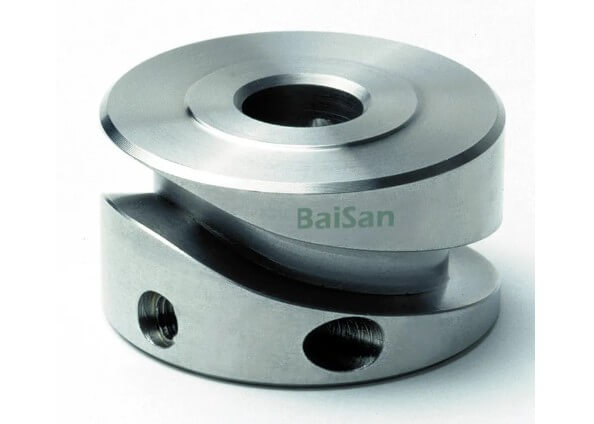
(3) Classification by processing accuracy:
1) Rough turning parts: mainly remove most of the excess, with relatively low accuracy requirements, usually IT11-IT9.
2) Semi-finishing turning parts: further improve accuracy and surface quality on the basis of rough processing, with an accuracy level of generally IT8-IT7.
3) Finished turning parts: meet high precision requirements, low surface roughness, small dimensional tolerance, such as IT6 and above.
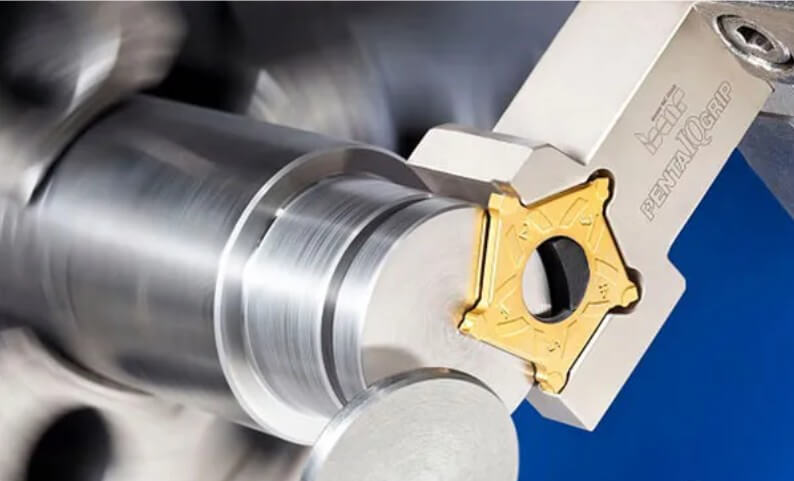
(4) Classification by surface finish:
1) Low finish turning parts: high surface roughness, usually between 12.5-6.3μm, suitable for general mechanical parts.
2) Medium finish turning parts: surface roughness between 3.2-1.6μm, suitable for mechanical parts with higher requirements.
3) High finish turning parts: surface roughness below 0.8μm, commonly used in precision machinery and optical instruments.
(5) Classification by functional use:
1) Transmission parts: such as gears, worm gears, sprockets, etc., used to transmit power and motion.
2) Support parts: such as bearing seats, sleeves, etc., play a supporting and positioning role.
3) Fasteners: such as bolts, nuts, etc., used to connect and fasten other parts.
4) Seals: such as oil seals, sealing rings, etc., used to prevent leakage.
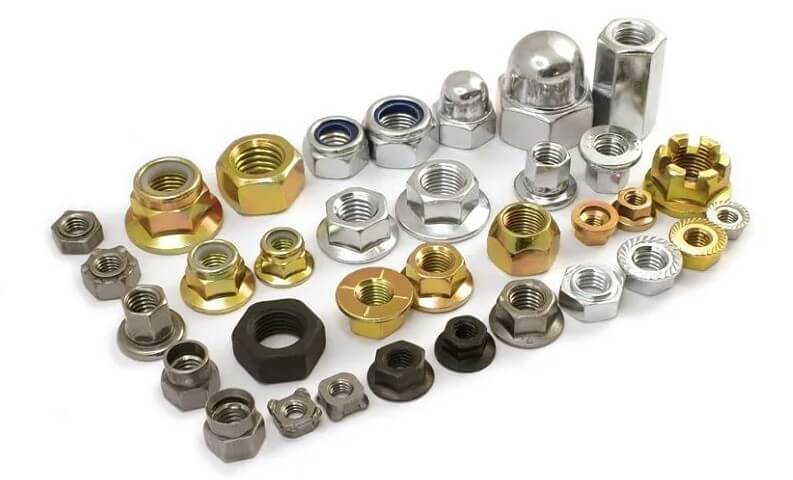
(6) Classification by hardness:
1) Soft turning parts: low hardness, easy to process, such as unhardened steel and non-ferrous metals.
2) Hard turning parts: high hardness, usually above 45HRC, suitable for occasions requiring high wear resistance and high strength, such as tool steel and bearing steel.
(7) Classification by size:
1) Small turning parts: usually less than 50mm in diameter and less than 100mm in length, suitable for precision instruments and electronic equipment.
2) Medium turning parts: between 50-200mm in diameter and between 100-500mm in length, widely used in general machinery manufacturing.
3) Large turning parts: greater than 200mm in diameter and greater than 500mm in length, commonly used in heavy machinery and large equipment manufacturing.
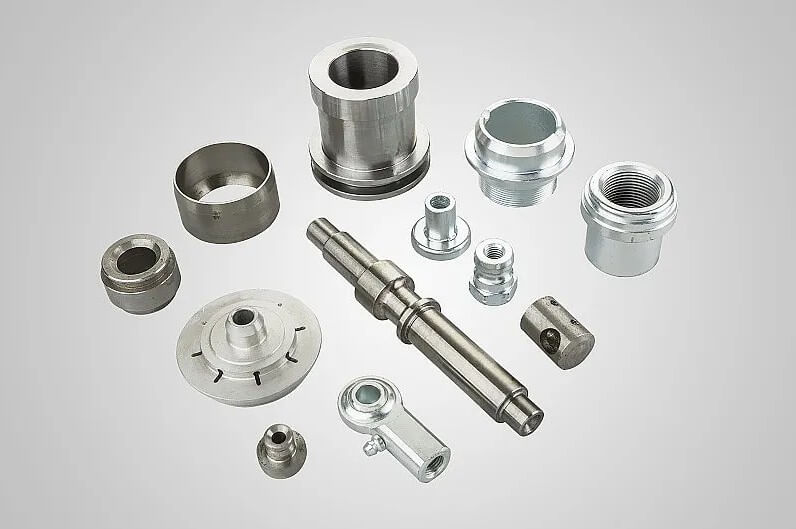
Summary:
There are many types of turning parts, and different types have significant differences in materials, shapes, processing accuracy, surface finish, functional use, hardness and size. These differences enable turned parts to meet various machining and application requirements, thus occupying an important position in modern industry.
3.Quality control of turned parts
(1) Common problems in turning
In turning, common problems include dimensional errors, surface roughness that does not meet requirements, and tool wear. These problems may be caused by a variety of factors, such as improper selection of turning tools, unreasonable cutting parameter settings, and inaccurate machine tool adjustments. For example, if the rake angle of the turning tool is not selected properly, it may lead to increased cutting forces, causing deformation and dimensional errors of the workpiece. In addition, excessive cutting speed or excessive feed rate may also lead to increased tool wear and affect the processing quality.
In addition, the material properties of the workpiece are also important factors affecting the turning quality. For example, certain high-hardness materials may cause severe tool wear, thereby affecting the processing accuracy and surface quality. In response to these problems, effective quality control measures need to be taken to ensure the stable quality of turned parts.
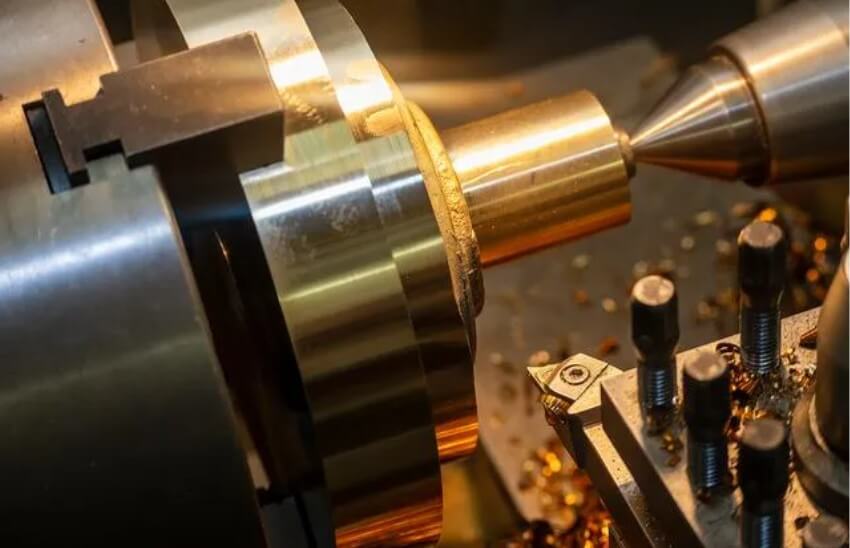
(2) Quality control strategies
In order to improve the quality of turned parts, the following strategies can be adopted:
1) Select the appropriate turning tool:
Select the appropriate turning tool type according to the material and processing requirements of the workpiece. For example, when processing high-hardness materials, you should choose a turning tool with higher wear resistance, such as a carbide turning tool or a ceramic turning tool.
2) Optimize cutting parameters:
Reasonably set the cutting speed, feed rate and cutting depth. For example, when processing high-hardness materials, you should choose a lower cutting speed and feed rate to reduce tool wear.
3) Use coolant:
During the turning process, using a suitable coolant can reduce cutting heat and tool wear and improve processing quality. For example, using oil-based coolant can reduce tool wear and improve surface finish.
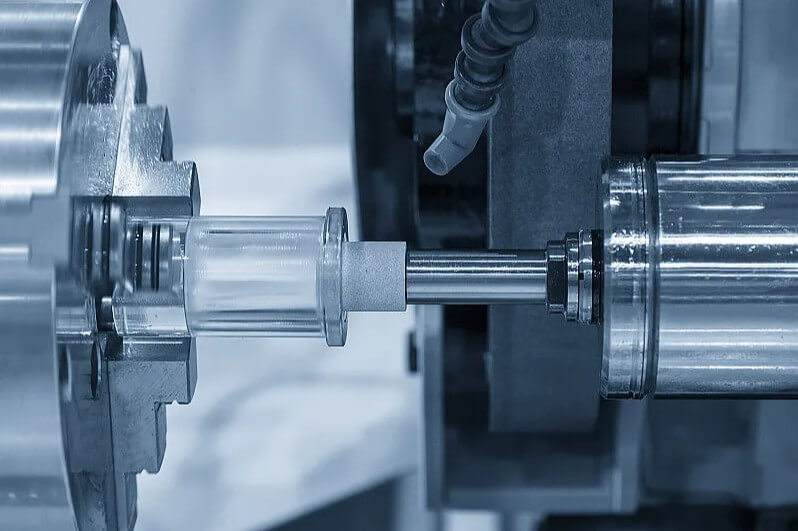
4) Regularly check and replace tools:
Regularly check the wear of the tool and replace the tool with severe wear in time to ensure the processing quality.
5) Real-time monitoring:
During the turning process, using real-time monitoring equipment, such as a dial indicator, can timely detect problems in the processing and make adjustments. For example, by monitoring the size and surface quality of the workpiece, the cutting parameters can be adjusted in time to ensure the stability of the processing quality.
4.Specific applications of turned parts in the industry
As an important product in the field of mechanical processing, turned parts are widely used in many industries. Their diversity and flexibility make them an indispensable part of modern manufacturing. The following are the applications of turned parts in several key areas:
(1) Automobile industry
Turned parts are widely used in the automobile industry, including the manufacture of key components such as engine crankshafts, camshafts, and transmission shafts. The precision of these components directly affects the overall performance of the car, so the high precision of turning processing has become an important link in ensuring the quality of the car.
For example, the outer cylindrical surface of the engine crankshaft is completed by turning, which ensures the strength and wear resistance of the crankshaft, thereby meeting the requirements of high-speed operation of the engine.
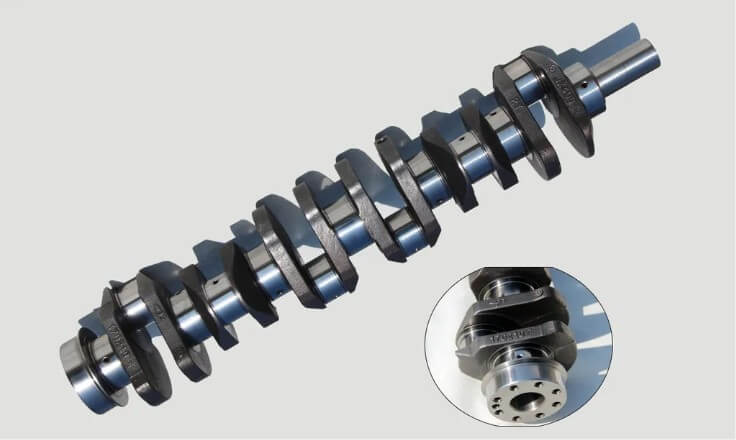
(2) Aerospace field
In the aerospace field, turned seals play a vital role. Since aerospace vehicles operate in extreme environments such as high temperature, high pressure, and strong radiation, turned seals must have excellent high temperature resistance, high pressure resistance, and corrosion resistance.
The combustion chamber and nozzle of the rocket engine, the attitude control system of the spacecraft, and the key components of the satellite communication system all rely on turned seals to ensure stable operation and prevent medium leakage.
(3) Mechanical Manufacturing
The application of turned parts in the field of mechanical manufacturing includes various rotating parts, such as shafts, discs, sleeves, etc. These parts are the basic components of mechanical equipment, and turning can accurately control their size and shape to meet the needs of different mechanical equipment.
For example, the inner holes and end faces of parts such as bearing seats and hydraulic cylinders can achieve high precision and high surface quality through turning, thereby ensuring the operating accuracy and stability of mechanical equipment.
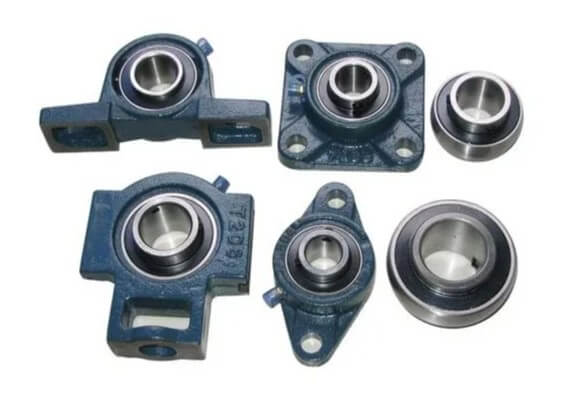
(4) Medical Devices
In the field of medical devices, turned parts are used to manufacture precision medical components, such as surgical instruments and joint replacement parts. These components have extremely high requirements for accuracy and surface finish, and turning can meet their strict manufacturing standards.
Since medical devices are directly related to the health and safety of patients, the application of turned parts in the medical field needs to strictly comply with relevant industry specifications and standards.
(5) Energy Industry
The application of turned parts in the energy industry includes the manufacture of key components such as oil drilling equipment, generator rotors, and wind turbine main shafts. These parts play a core role in energy production, and the high efficiency and precision of turning ensure the reliability and efficiency of energy equipment.
For example, the drill bit of oil drilling equipment is turned to achieve its complex geometry and high hardness to meet the needs of deep well drilling.
5.Summary
In summary, the charm of turning technology lies in its ability to produce a wide variety of turned parts with a wide range of uses to meet the needs of different industries.
7 Comments