Turning centers: Evolution
The natural descendant of the manual lathe, turning centers are an important machine tool used in the manufacturing industry. These versatile machines play a key role in precisely machining raw materials into finished products. While the general principles of turning centers have remained the same over time, significant advancements and innovations have been introduced in the past decade. Let’s explore the evolution of turning centers and highlight the key innovations that have revolutionized their capabilities.
1.History of Turning Centers
Turning centers have a long and fascinating history that dates back to ancient civilizations. Ancient Egyptians utilized rudimentary wooden lathes to shape and polish materials. In the Middle Ages, efficiency improved significantly with the introduction of pedal-driven lathes. However, it was during the Industrial Revolution that turning centers went through a transformational phase. Steam-powered and electric machines replaced manual operations, increasing productivity and driving innovation in the turning process.
In the 18th and 19th centuries, as the Industrial Revolution gained momentum, the first powered turning centers came into being. The introduction of steam lathes and electric machine tools marked a pivotal moment, allowing materials to be shaped faster and more efficiently. This technological advancement laid the foundation for subsequent innovations and the eventual incorporation of digital technology into turning centers.
Recently, the convergence of numerically controlled (NC) machine tools with digital technology has marked a turning point, evolving into sophisticated computer numerical control (CNC) technology. With their computer-controlled precision and efficiency, CNC lathes have become the method of choice for companies seeking accurate and cost-effective production processes to meet the growing demand for complex precision parts across industries.
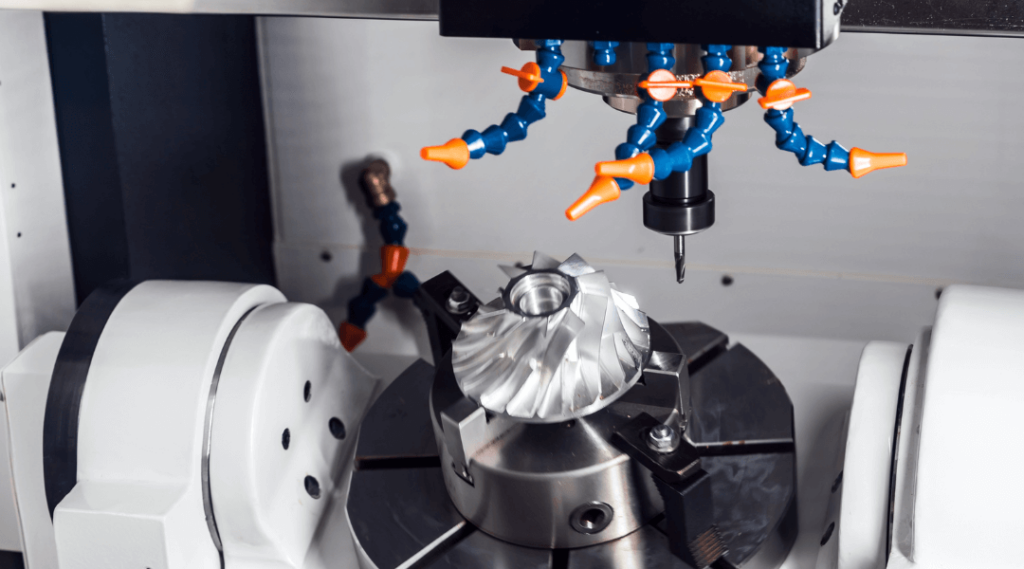
2.Key Turning Center Advancements and Innovations
The turning center industry has seen some major advancements and innovations over the past decade, revolutionizing its functionality and expanding its capabilities. Let’s take a look at some of them:
1) Multi-axis Capability
Traditional lathes typically have two axes of motion, while modern turning centers are equipped with multiple axes, often five or more. This provides greater flexibility and the ability to perform complex machining operations without repositioning the workpiece.
2) Integrated Automation
Today, turning centers often include integrated automation features, such as robotic loaders and unloaders, which can automatically handle material loading and unloading tasks. This reduces the need for human intervention and increases productivity.
3) CNC Technology
Computer numerical control (CNC) technology has made great strides in recent years, allowing for more precise control and monitoring of turning centers. CNC systems can program and perform complex machining operations with a high degree of accuracy and repeatability.
4) Power tooling
Many modern turning centers are equipped with power tooling capabilities. This means that in addition to traditional turning operations, the machine can perform secondary operations such as drilling, milling, and tapping without resetting or transferring the workpiece to another machine.
5) Advanced control systems
These tools now feature advanced control systems that provide operators with intuitive interfaces and real-time monitoring capabilities. This allows for better visualization and control of the machining process, as well as rapid adjustments and optimizations as needed.
6) Improved cutting tools and toolholders
Innovations in cutting tool technology have increased tool life, cutting speeds, and surface finish. In addition, toolholders have been improved to provide greater stability and rigidity, resulting in better machining performance.
7) Energy efficiency
Turning centers are becoming increasingly energy-efficient, with improved designs that reduce power consumption and waste heat. This not only reduces operating costs, but also has a positive impact on the environment.
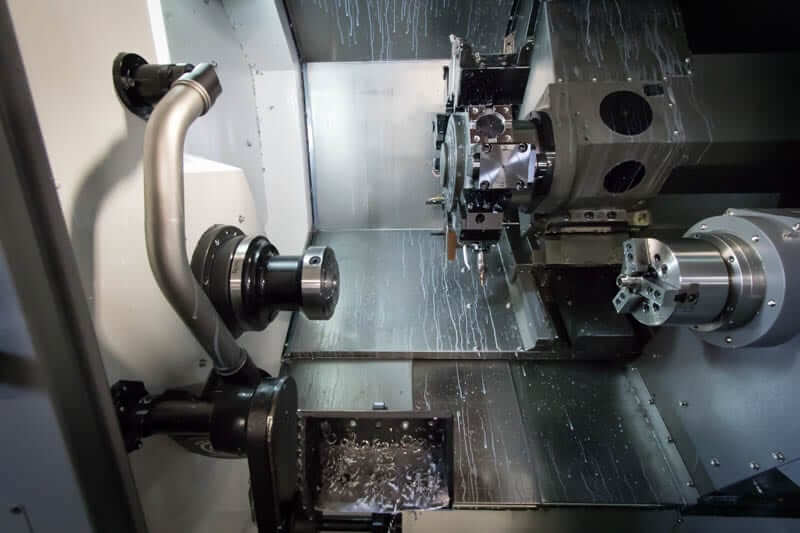
3.Xavier’s Commitment to Precision Machining
In the dynamic landscape of manufacturing, the evolution of turning centers is a testimony to human ingenuity and technological advancement. Looking into the future, it will undoubtedly continue its journey of improvement and innovation. With cutting-edge equipment and a team of experienced professionals, Xavier is the epitome of excellence in precision machining services. Our unwavering commitment to accuracy, quality, and customer satisfaction has made us an industry leader. The evolution of turning centers is an ongoing story, and at Xavier, we are committed to being at the forefront of shaping its next chapter, providing exceptional results for all your machining needs.