Turning of aluminum parts: a comprehensive analysis from process to practice
In the modern manufacturing industry, turning of aluminum parts has become an indispensable part with its high efficiency and precision. Turning of aluminum parts not only involves complex machining steps, but also requires careful control of machining parameters, as well as a good understanding of the problems encountered in the machining process and the corresponding solutions, as long as this can ensure the quality and performance of the final product.
This article will be through three parts of the turning of aluminum parts related to the content of a comprehensive introduction. The first part is a basic introduction to the characteristics of aluminum and the advantages of these characteristics for turning; the second part of the aluminum parts of the turning process for the fine control, including process analysis and process parameters selection, optimization; the third part of the turning process for the wear and tear caused by the solution, including aluminum wear and tool wear in two cases.
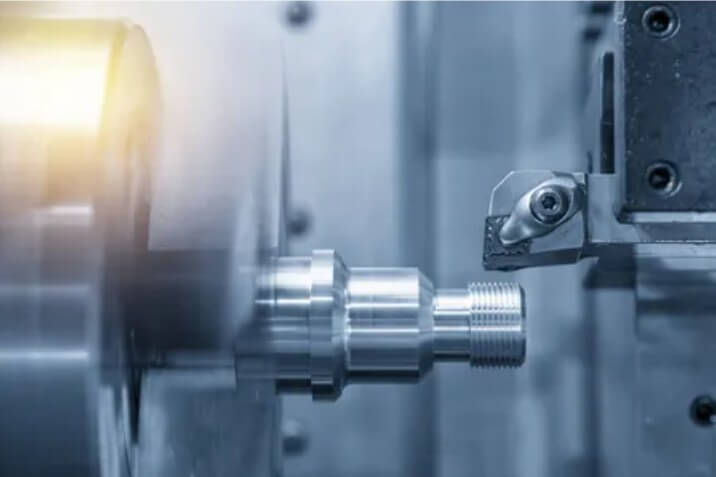
1.Characteristics of aluminum and its influence on turning process
Aluminum, with the element symbol Al and atomic number 13, is a silver-white light metal. It is ductile, electrically and thermally conductive. Aluminum is abundant in the earth’s crust, accounting for about 8%, ranking first among the metallic elements. Here are some properties of aluminum:
(1) Lightweight:
The density of aluminum is only 2.7g/cm³, about one-third that of steel. This characteristic makes aluminum in the turning process can reduce the cutting force and machine load, improve machining efficiency, while reducing the weight of the workpiece, suitable for the manufacture of lightweight parts.
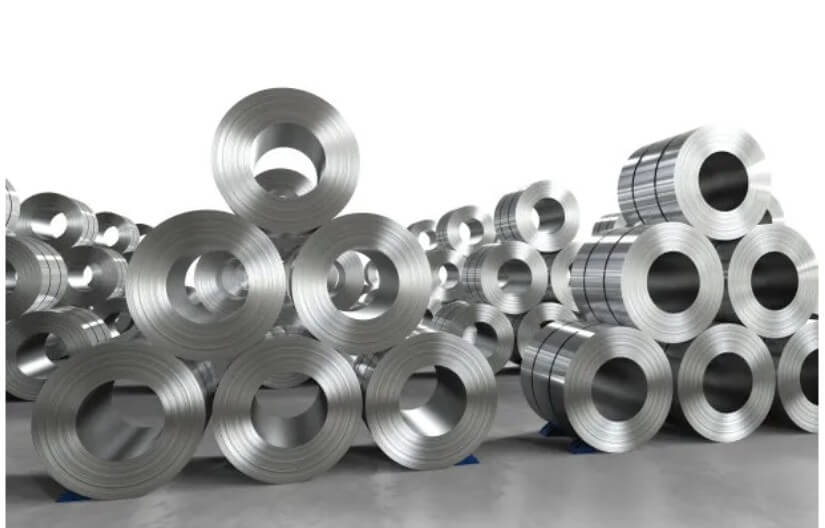
(2) Good thermal conductivity:
Aluminum’s thermal conductivity is about 50-60% of copper, which is conducive to the rapid dispersion of heat in the turning process, reduce tool wear, improve machining accuracy and surface finish.
(3) excellent machinability:
Aluminum is soft, easy to cut, small deformation during processing, suitable for high-speed turning. Aluminum machinability makes it possible to quickly form in the turning process, reducing processing time and cost.
(4) Non-magnetic:
Aluminum is a non-magnetic material, not affected by magnetic fields in turning, suitable for precision machining and electronic industrial applications.
(5) Corrosion resistance:
Aluminum has good corrosion resistance in most environments, and the surface of the turned parts can form a dense layer of oxide film to protect the substrate from corrosion and extend the service life of the parts.
(6) good recyclability:
Aluminum has a very high recyclability, turning processing of aluminum chips can be recycled and reused to reduce resource waste and environmental pollution, in line with the requirements of green manufacturing.
2.Turning of aluminum parts: process analysis
Turning of aluminum parts is an important process in metal processing, which is widely used in aerospace, automotive and machinery manufacturing due to its high efficiency and precision. The following is an analysis of the turning of aluminum parts.
(1) Parts drawing analysis and preparation
According to the part drawings, clarify the design requirements, geometry, dimensions and features. Ensure that the understanding of the drawings is accurate, to provide an accurate basis for subsequent processing.
(2) Machine tools and workpiece preparation
Select the appropriate machine tool equipment and fix the workpiece on the lathe. Ensure that the workpiece material meets the process requirements and the machine parameters are set reasonably to ensure machining accuracy and efficiency.
(3) Tool selection and installation
According to the machining requirements of the parts, select the appropriate type and size of the turning tool, and use the fixture to install the turning tool on the lathe. Tool selection needs to be determined according to the hardness, shape and surface quality of the machined material.
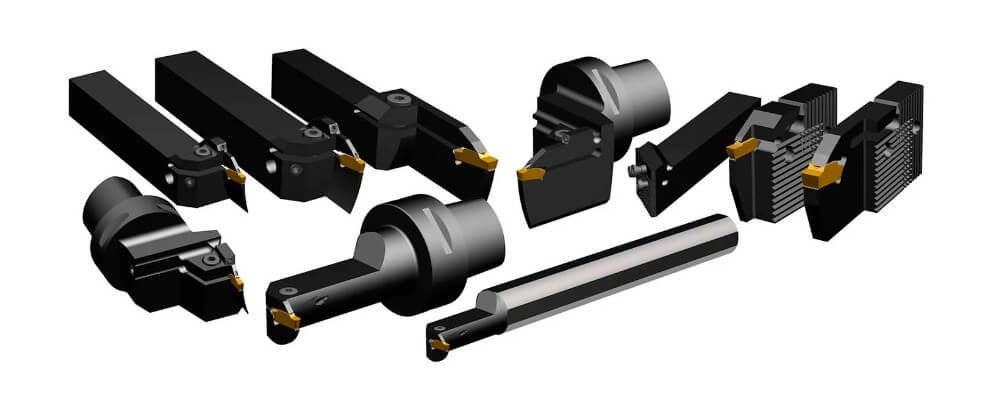
(4) Rough turning
Use rough turning process to remove the excess material on the workpiece, so that the shape and size of the workpiece gradually close to the target value. This stage should pay attention to cutting efficiency and material removal, while avoiding excessive cutting leading to deformation or damage of the workpiece.
(5) Fine turning
On the basis of rough turning, use smaller depth of cut and higher speed for fine machining to achieve the required dimensional accuracy and surface roughness. The finishing turning stage should focus on machining accuracy and surface quality.
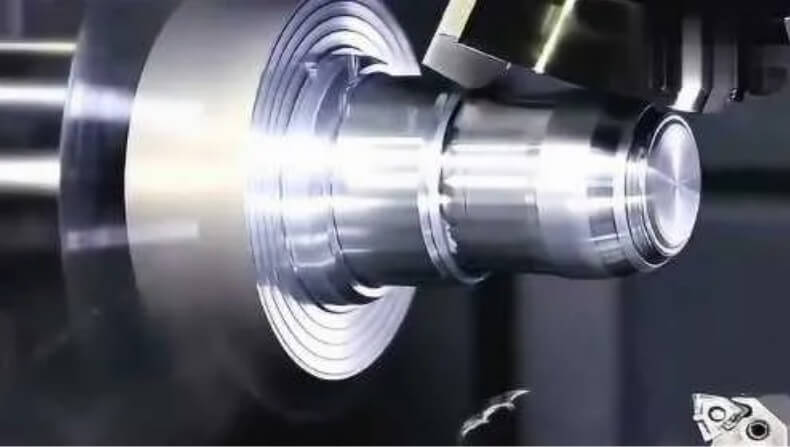
(6) Real-time monitoring and adjustment
Use measuring instruments to monitor the size and surface quality of the workpiece in real time. According to the real-time monitoring results, timely adjust the machine tool and tool parameters to maintain machining accuracy.
(7) Cutting threads and surface treatment
If necessary, thread cutting can be performed with a thread turning tool during the turning process of aluminum parts. After completing the turning, surface treatment, such as grinding, polishing or coating, is performed on the workpiece as needed to improve the surface quality and protect the workpiece.
(8) Quality inspection and finishing
Quality inspection is carried out on the machined workpiece, including inspection of size, geometric accuracy and surface quality. Finally, clean and organize the parts to ensure the quality and reliability of the parts.
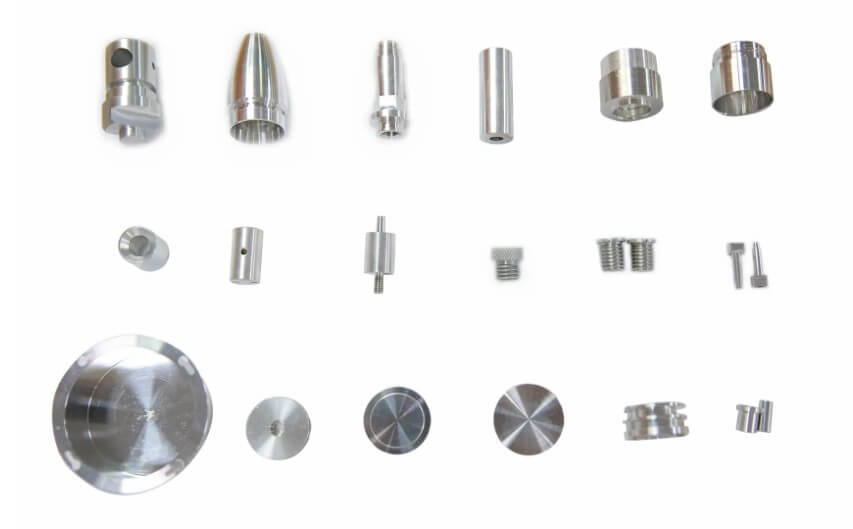
3.Turning of aluminum parts: selection and optimization of machining parameters
Aluminum parts are widely used in modern manufacturing due to their lightweight and high strength properties. Because of this, it is necessary to put forward higher requirements for the selection and optimization of turning parameters of aluminum parts. The optimization strategy of turning parameters for aluminum parts is discussed below in terms of cutting speed, feed, depth of cut, tool geometry and cooling.
(1) Cutting speed
Cutting speed is one of the most important parameters in turning. Turning of aluminum parts usually adopts a higher cutting speed to improve processing efficiency. The cutting speed of high-speed steel tools is generally in the range of 100-200 m/min, and carbide tools can reach 200-500 m/min.
(2) Feed
The choice of feed needs to be considered comprehensively machining efficiency and surface quality. Larger feed can improve machining efficiency, but may lead to increased surface roughness. The feed amount for turning of aluminum parts is generally selected between 0.1-0.3 mm/revolution.
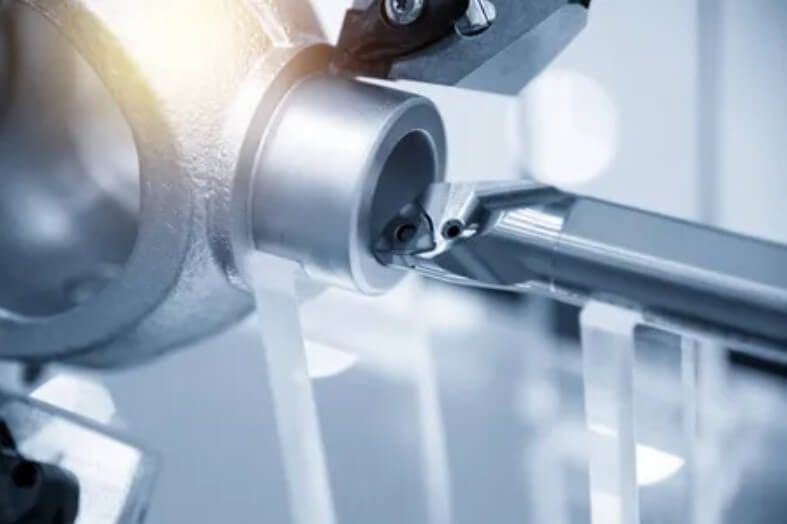
(3) Cutting depth
The depth of cut should be selected according to the workpiece allowance and machine power. When rough turning, the depth of cut can be larger, usually between 2-5 mm; when fine turning, the depth of cut should be smaller, usually between 0.1-0.5 mm.
(4) tool geometry parameters
The geometric parameters of the tool, such as the front angle, back angle and camber angle, have a significant impact on the cutting performance. Turning of aluminum parts usually choose a larger front angle to improve cutting efficiency and tool life. The rear angle is generally selected between 6°-12° to maintain the strength and sharpness of the cutting edge.
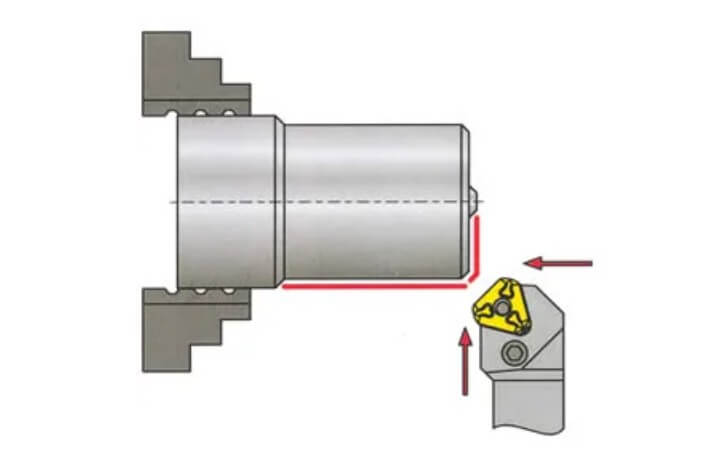
(5) Cutting fluid
Cutting fluid plays a cooling, lubrication and cleaning role in the turning process, which can improve cutting performance, extend tool life and improve processing quality. The cutting fluid commonly used in the turning of aluminum parts includes water-based coolant and oil-based cutting fluid.
Summary:
In summary, the process and parameter selection and optimization of the turning process of aluminum parts have an important impact on processing efficiency and workpiece quality. In the actual machining process, it must be operated and managed in strict accordance with the design requirements to ensure the quality of the workpiece and machining efficiency.
4.Common problems and solutions in the turning of aluminum parts
Aluminum parts are widely used because of their lightweight and high strength. However, in the process of turning, various problems are often encountered, affecting processing efficiency and part quality. The following are common problems and their solutions in the turning process of aluminum parts.
(1) Poor surface finish
1) Reason: improper cutting parameters, tool wear, cutting temperature is too high.
2) Solutions: optimize cutting speed, feed and depth of cut, use good wear-resistant tool materials and coatings, check and replace tools regularly, use effective coolant to control the cutting temperature.
(2) Burr
1) Reason: the surface of aluminum parts is soft, easy to produce burrs when cutting.
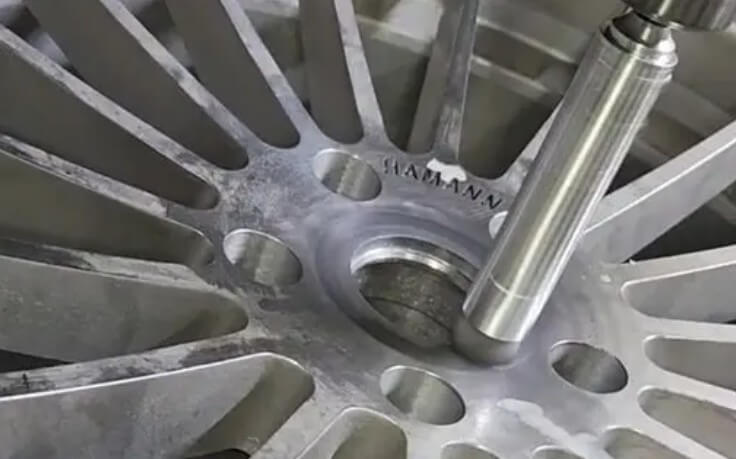
2) Solution: Reduce the feed volume appropriately, choose sharp tools, increase the angle of the back angle of the tool, use appropriate coolant to reduce friction and heat.
(3) Burns
1) Reason: cutting temperature is too high, high thermal conductivity of aluminum parts, easy to produce high temperature in the local.
2) Solution: Use high speed cutting, reduce the depth of cut and feed, use adequate coolant to reduce the cutting temperature.
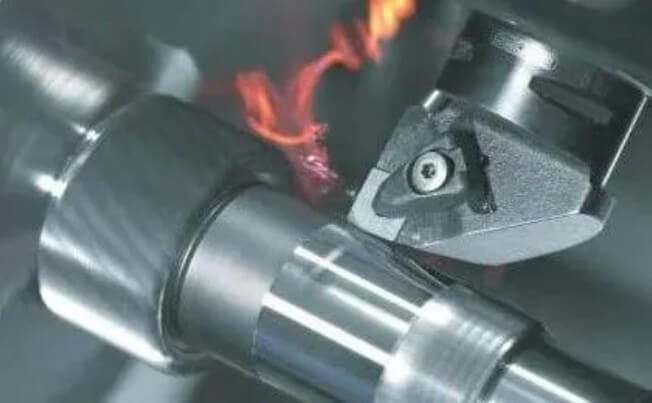
(4) Deformation
1) Reason: Aluminum parts with good plasticity, cutting force and heat-affected areas can easily lead to deformation.
2) Solution: Reasonable selection of fixtures to ensure that the workpiece clamping stability, the use of symmetrical cutting to balance the cutting force, control the cutting temperature to reduce thermal deformation.
(5) vibration pattern problem
1) Reason: machine tool spindle runout, tool clamping is not firm, cutting force is too large.
2) Countermeasures: regular inspection and adjustment of the machine tool spindle to ensure its accuracy; the use of high rigidity of the toolholder and clamping mechanism; adjust the cutting parameters, reduce the cutting force, to avoid self-excited vibration.
(6) surface hardening problems
1) Reason: the cutting temperature is too high, the surface of the aluminum parts of the cold hardening.
2) Countermeasures: control the cutting speed, to avoid high temperature; selection of cutting tool materials with good thermal conductivity, such as diamond tools; the use of adequate cutting fluid for cooling.
(7) cutter mark problem
1) Reason: unreasonable tool geometry parameters, cutting edge is not sharp.
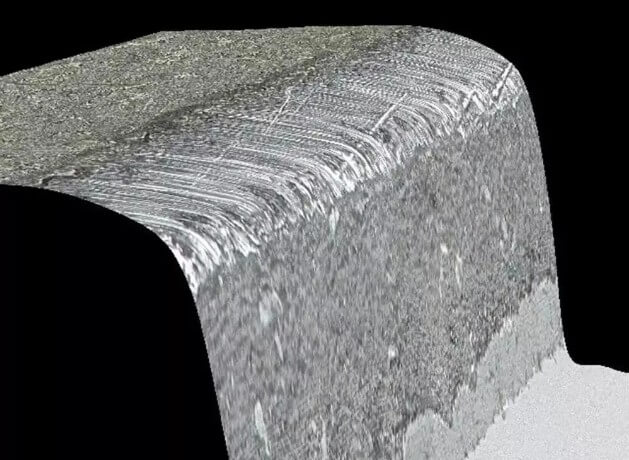
2) Countermeasures: Optimize the front angle, back angle and tilt angle of the tool to ensure that the cutting edge is sharp; Regularly sharpen the tool to maintain its good cutting condition; For aluminum parts with high precision requirements, several times of fine turning can be carried out.
(8) Surface discoloration
1) Reason: the cutting temperature is too high, resulting in oxidation of the surface of aluminum parts.
2) Countermeasures: control the cutting temperature, use efficient cutting fluid for cooling; choose the appropriate cutting speed to avoid excessive cutting heat; keep the tool clean and reduce chip adhesion.
5.Causes and solutions for tool wear during turning of aluminum parts
Tool wear and breakage are common problems in the turning process of aluminum parts. Specific solutions to these problems are presented below:
(1) Wear of rear tool face
1) Problem: the rear face wear is mainly due to the friction between the tool and the workpiece material during the cutting process, and the wear usually starts from the edge line and gradually develops downwards.
2) Solution: Appropriately reduce the cutting speed, while increasing the feed to reduce friction and extend tool life.
(2) Crescent pit wear
1) Problem: Crescent puddle wear is caused by the chemical reaction resulting from the contact between the chips and the front face of the tool.
2) Solution: Reduce the cutting speed and select inserts with the correct groove type and more wear-resistant coatings to slow down the formation of crescent pits.
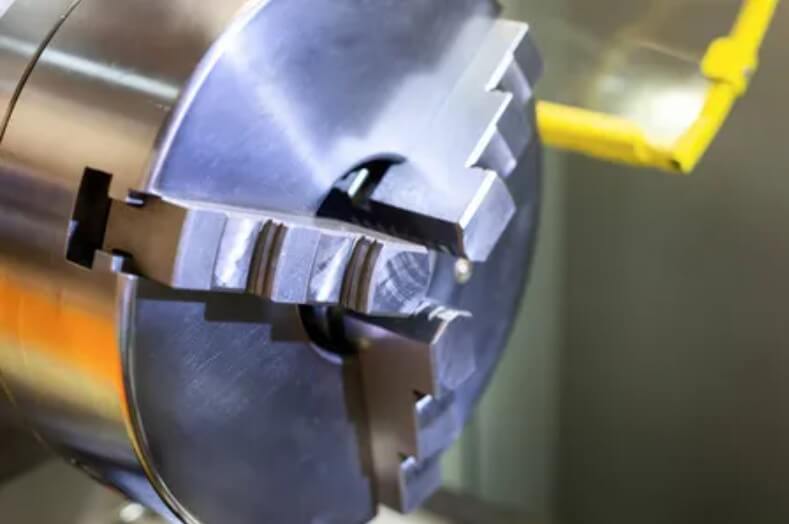
(3) Plastic Deformation
1) Problem: Plastic deformation of the cutting edge occurs at high temperatures and high cutting forces, resulting in the depression or collapse of the cutting edge.
2) Solution: Use cutting tool materials with high thermal hardness and apply coatings to the insert to enhance its resistance to plastic deformation.
(4) Coating Flaking
1) Problem: When machining bonded materials, the adhesion load causes the coating to separate, exposing the underlying layer or substrate.
2) Solution: Increase cutting speed and select inserts with thinner coatings to minimize the risk of coating flaking.
(5) Cracking and chipping
1) Problem: Rapid temperature fluctuations and mechanical stresses cause cracks or minor damage to the cutting edge of the tool.
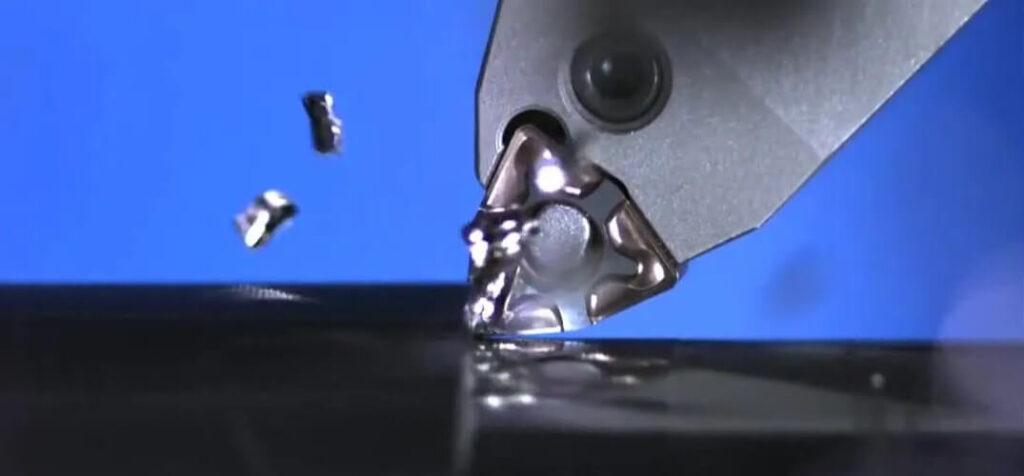
2) Solution: Use a blade material with higher toughness and rational use of coolant to avoid rapid temperature changes.
(6) Groove wear
1) Problem: Excessive localized damage at the maximum depth of cut, possibly due to chemical wear, adhesive wear or thermal wear.
2)Solution: For machining hardened materials, select a smaller main deflection angle and adjust the depth of cut.
(7) Fracture
1) Problem: Excessive load on the cutting edge causes the tool to break, making it impossible to continue using it.
2) Solution: Regularly check tool wear, select the correct cutting parameters, and ensure clamping stability.
(8) Chip Tumor Accumulation
1) Problem: Material accumulates on the front tool face, forming chip tumors, leading to increased cutting forces and coating damage.
2) Solution: Increase the cutting speed and use a sharper cutting edge when processing softer, more viscous materials.
5.Summary
Turning of aluminum parts is a complex system engineering project that requires close cooperation and meticulous management of all links.Through in-depth discussion and practical application of the processing steps, processing parameters, common problems and solutions, you can continuously improve the level and quality of turning of aluminum parts.