The Basics of Turning Parts
Turning parts is a fundamental process in the manufacturing industry that involves shaping a workpiece by rotating it against a cutting tool. This process is widely used to create cylindrical components with precise dimensions and smooth finishes. Understanding the basics of turning parts is essential for anyone involved in the manufacturing or engineering field.
Key Elements to Look Out For When Manufacturing Turning Parts
One of the key elements in turning parts is the lathe machine. A lathe is a versatile tool that rotates the workpiece on its axis while various cutting tools shape it. Lathes come in different sizes and configurations, ranging from small benchtop models to large industrial machines. The choice of lathe depends on the size and complexity of the parts being produced.
The workpiece, also known as the stock, is the material that is being shaped in the turning process. It can be made of various materials such as metal, wood, or plastic. The workpiece is mounted on the lathe’s spindle, which rotates it at a controlled speed. The cutting tool, which is fixed on a tool post, then moves along the workpiece to remove material and shape it according to the desired specifications.
There are different types of turning operations that can be performed on a lathe. The most common ones include facing, turning, drilling, boring, and threading. Facing involves creating a flat surface at the end of the workpiece, while turning is the process of removing material from the outer diameter to create a cylindrical shape. Drilling and boring are used to create holes in the workpiece, while threading is used to create screw threads.
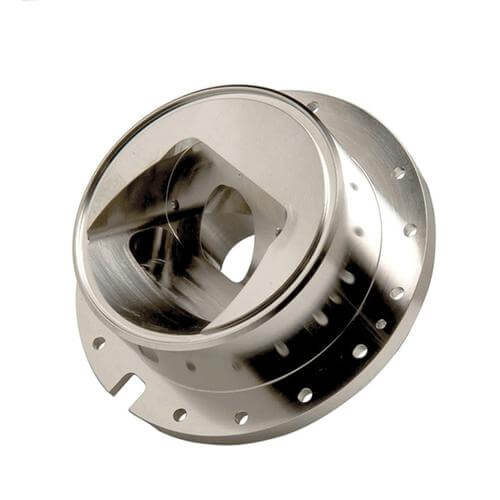
To achieve accurate and precise results, it is crucial to consider the cutting parameters during the turning process. These parameters include the cutting speed, feed rate, and depth of cut. The cutting speed refers to the speed at which the workpiece rotates, while the feed rate determines how fast the cutting tool moves along the workpiece. The depth of cut, on the other hand, determines the amount of material that is removed in each pass.
In addition to the cutting parameters, the choice of cutting tool also plays a significant role in turning parts. Different materials and shapes of cutting tools are used depending on the workpiece material and the desired outcome. High-speed steel (HSS) tools are commonly used for general-purpose turning, while carbide tools are preferred for high-speed and heavy-duty applications.
Safety is an important aspect of turning parts. When operating a lathe, you must follow proper safety procedures and wear appropriate personal protective equipment (PPE). This includes safety glasses, gloves and hearing protection. It is also important to properly secure the workpiece and ensure that the cutting tools are sharp and in good condition to minimize accidents and achieve the best results.
In conclusion, turning parts is a fundamental process in the manufacturing industry that involves shaping a workpiece by rotating it against a cutting tool. Understanding the basics of turning parts, including the use of lathe machines, different types of turning operations, cutting parameters, and safety precautions, is essential for anyone involved in the manufacturing or engineering field. By mastering these fundamentals, manufacturers can produce high-quality cylindrical components with precision and efficiency.