Introduction to Different Types of Chips in CNC Milling
CNC milling is a widely used machining process that involves the use of rotating tools to remove material from a workpiece. Milling of machined parts is also popular.
As the tool moves across the workpiece, it generates chips or swarf, which are small pieces of material removed during the milling process. For example, milling automotive parts and milling parts in Fort Wayne and other milled parts. These chips can vary in size, shape, and thickness depending on various factors such as cutting speed, feed rate, and the material being machined.
Understanding the different types of chips formed during CNC milling is crucial for the following reasons. First, it helps evaluate the efficiency and effectiveness of the milling process. Second, it provides valuable insights into the cutting conditions and tool performance. Lastly, it helps identify potential issues such as tool wear or improper cutting parameters.
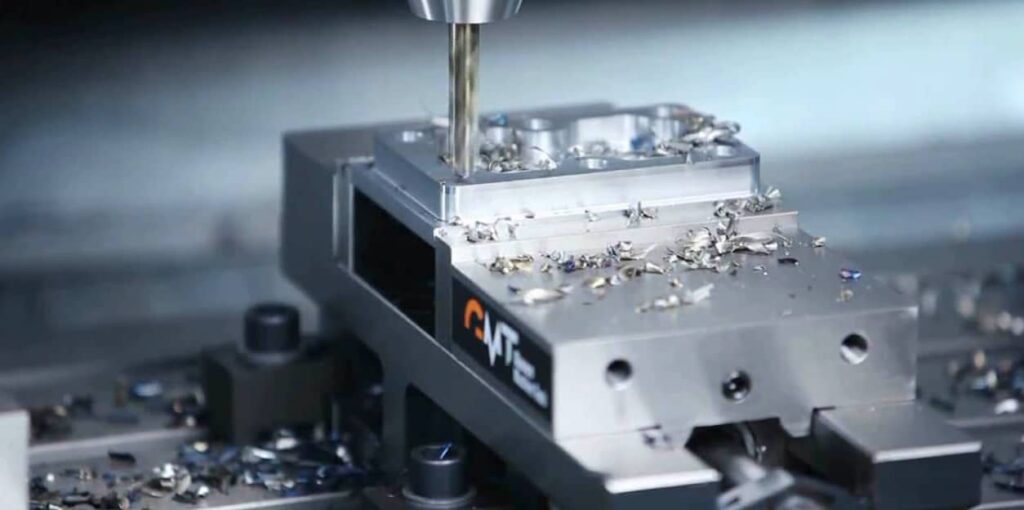
1.Continuous Chips
One of the most common types of chips formed during CNC milling is the continuous chip. As the name suggests, this type of chip is formed in a continuous manner with a smooth, continuous shape. Continuous chips are usually associated with ductile materials such as aluminum or copper.
These materials have a high degree of plasticity, which allows the chips to flow smoothly along the cutting edge of the tool. The formation of continuous chips indicates that the cutting conditions are optimal, resulting in a high-quality surface finish.
On the other hand, discontinuous chips are also formed when machining brittle materials such as cast iron or ceramics. Unlike continuous chips, discontinuous chips have a segmented or broken appearance.
This is because brittle materials tend to fracture rather than deform plastically. The formation of discontinuous chips indicates that the cutting conditions may need to be adjusted to prevent tool breakage or poor surface finish.
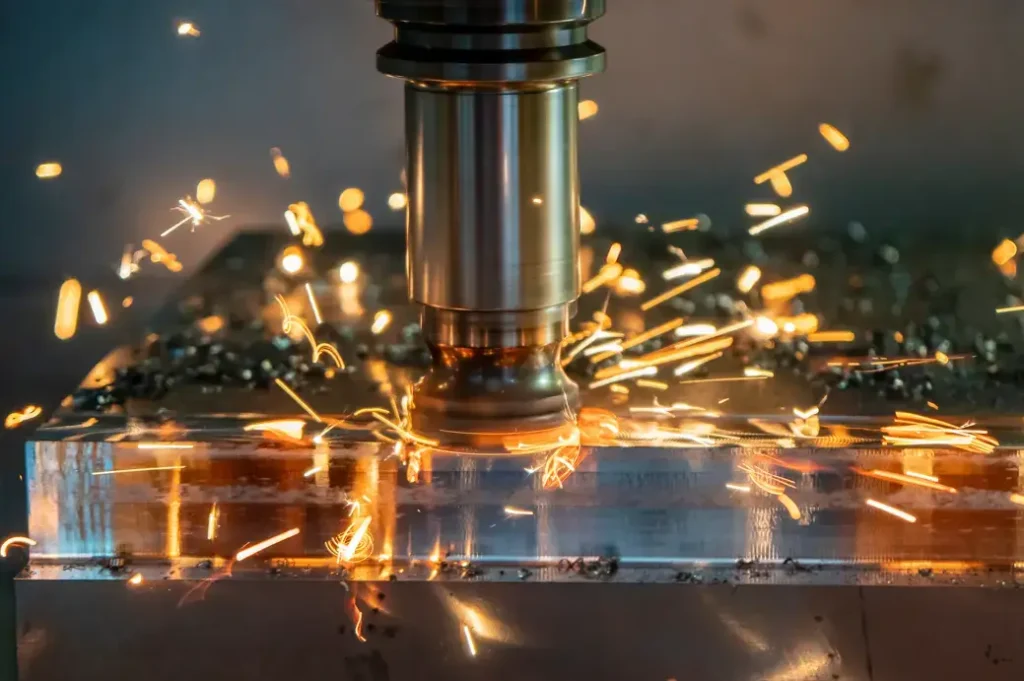
2.Built-up Edge (BUE)
Another type of chip that may form during CNC milling is built-up edge (BUE). Built-up edge occurs when the material being machined adheres to the cutting tool and forms a layer on its surface.
This layer may become unstable and eventually break away from the tool, resulting in a poor surface finish or tool wear. Built-up edge is often observed when machining materials that have a tendency to work harden, such as stainless steel or titanium. To prevent the formation of built-up edge, appropriate cutting parameters and tool coatings should be used.
In addition to the types of chips mentioned above, variations in chip thickness can occur during CNC milling. Thin chips are often associated with low cutting speeds or high feed rates. These chips are more likely to break and can cause issues such as chip jamming or poor chip evacuation.
On the other hand, thick chips form when cutting speeds are high or feed rates are low. Thick chips can put excessive stress on the cutting tool, causing tool wear or breakage.
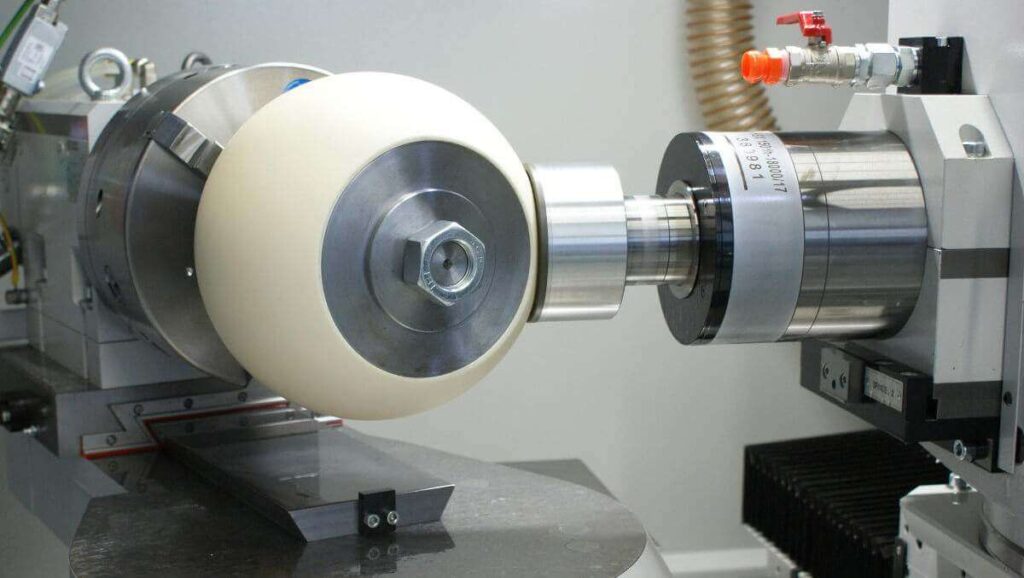
In summary, understanding the different types of chips formed during CNC milling is critical to optimizing the machining process.
Continuous chips indicate optimal cutting conditions and a high surface finish, while discontinuous chips may require adjustment to prevent tool breakage. The formation of built-up edge can lead to poor surface finish or tool wear, necessitating the use of appropriate cutting parameters and tool coatings.
Finally, variations in chip thickness can affect chip evacuation and tool life. By carefully analyzing the chips formed during CNC milling, manufacturers can improve their machining processes and achieve better results.