Types of Grooving Tools: How to Cut Grooves on a CNC Lathe?
Grooving tools are an essential part of CNC lathes. They are used to cut grooves in the workpiece, forming channels or grooves for various purposes. They play a vital role in the parts of a woodworking lathe and its functions.
Whether you are an experienced machinist or a beginner, understanding the different types of groove tools and how to use them is essential to achieve accurate and efficient results.
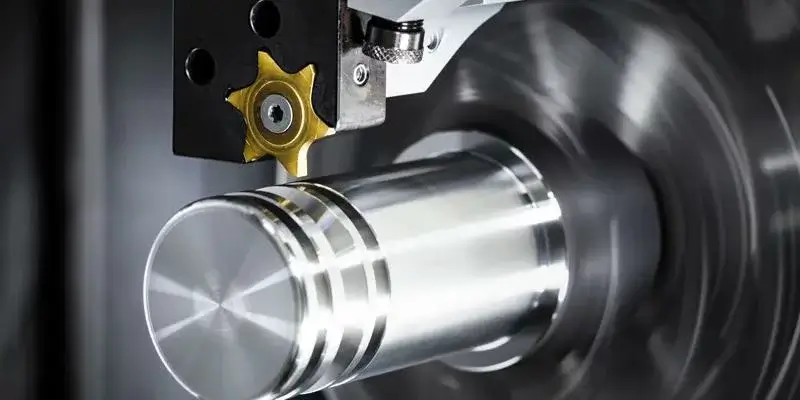
1.Types of Grooving Tools
1) Single Point Grooving Tools
As the name suggests, this tool has only one cutting edge and is used to process grooves of varying widths and depths. It is versatile and can be used for both internal and external grooving operations. Single Point Grooving Tools are usually made of high-speed steel or carbide, ensuring their durability and lifespan.
2) Parting Tools
This tool is specifically designed to cut workpieces from larger stock. It is usually used to create deep grooves or to separate parts from bar or rod stock. Parting tools have narrow cutting edges that allow for precise and clean cuts. They are available in various sizes and materials, depending on the specific application.
3) Indexable Grooving Tools
These tools consist of a tool holder and an insert that can be rotated or indexed to present a new cutting edge. Indexable Grooving Tools are popular in high-volume production environments because they allow for quick and easy tool changes. They are available in different geometries and coatings to accommodate a variety of materials and cutting conditions.
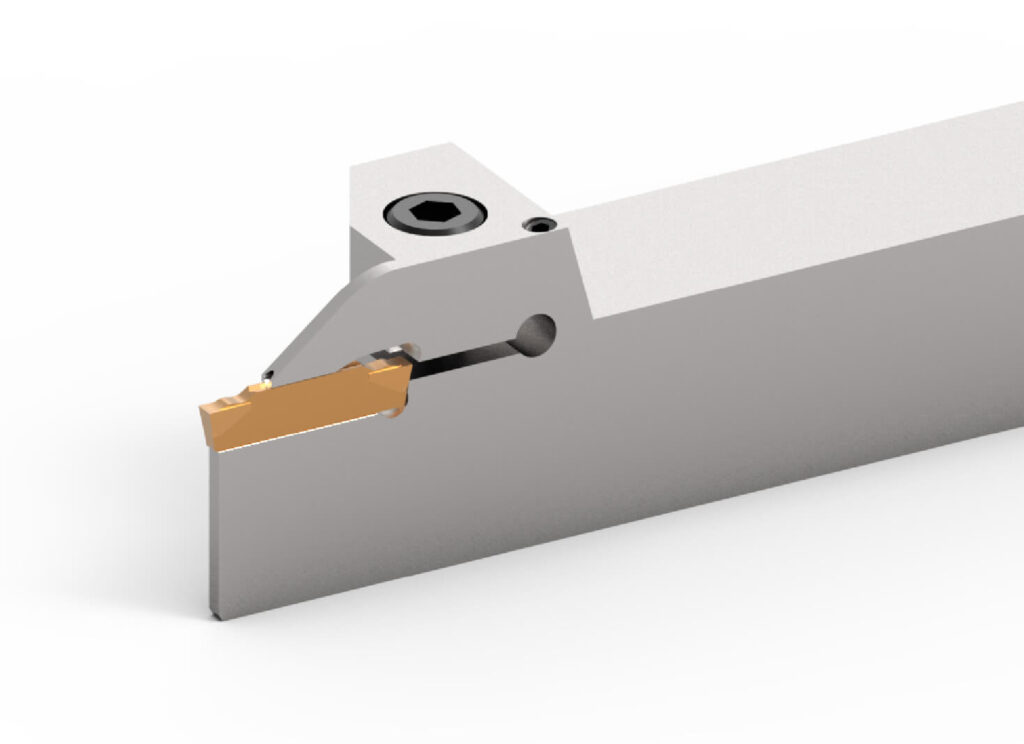
2.Considerations for Cutting Grooves
1) Choosing the Right Grooving Tool
The choice of tool is often determined by the material being machined, the desired groove size, and the specific application requirements. Therefore, it is important to consult the tool manufacturer’s recommendations and guidelines to ensure optimal performance.
2) Setting Up the CNC Lathe
This includes mounting the tool in the tool holder, adjusting the tool height and orientation, and setting cutting parameters such as feed rate and cutting speed. The machine manufacturer’s instructions and guidelines must be followed to ensure safe and accurate operation.
3) Monitoring and Adjusting Cutting Conditions
During the grooving process, it is important to monitor the cutting conditions and make adjustments as needed. This includes checking the tool for excessive wear or chipping, adjusting cutting parameters, and ensuring proper chip evacuation. Regular maintenance and inspection of the grooving tool is also essential to ensure its life and performance.
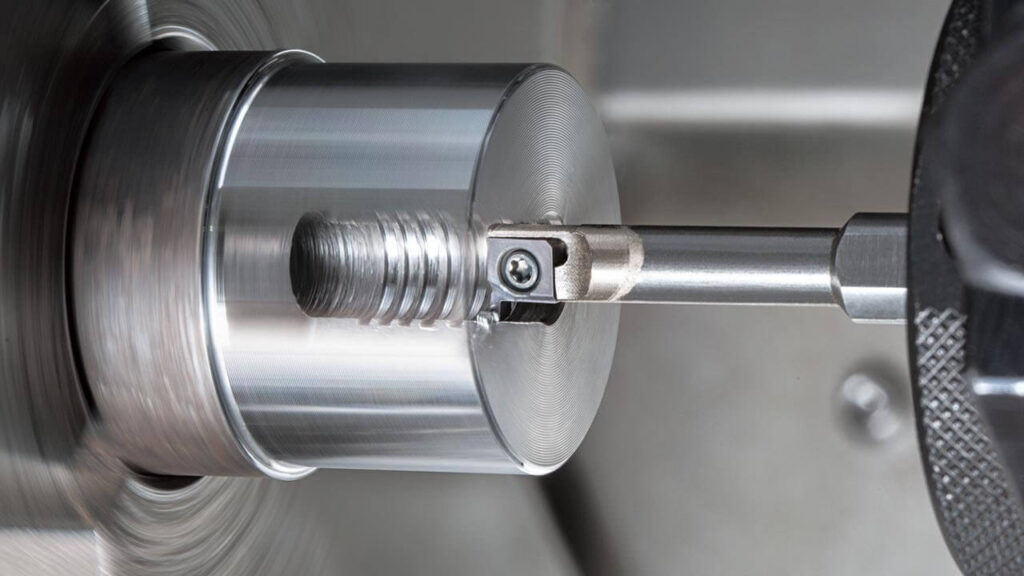
In summary, slotting tools are essential for slotting on CNC lathes. Understanding the different types of slotting tools and how to use them is essential to achieving accurate and efficient results. Whether it is a single point slotting tool, a parting tool, or an indexable slotting tool, selecting the right tool and setting up the machine correctly are the keys to a successful slotting operation.
By following the manufacturer’s recommendations and guidelines, monitoring cutting conditions, and performing regular maintenance, machinists can ensure optimal performance and extend the life of their slotting tools.