Introduction to Small Batch CNC Machining
Low-volume CNC machining is a manufacturing process that involves the use of computer numerical control (CNC) machines to produce small quantities of parts or products. This method is ideal for businesses that require limited quantities of items as it offers several advantages over traditional manufacturing processes. For example, automotech tyre machine parts, azkoyen coffee machine parts, b and q washing machine parts, b braun dialysis machine parts, b&q washing machine parts, and back to life machine replacement parts.
In this article, we will explore the different types of low-volume CNC machining and how they can benefit various industries such as automotech tyre machine parts, azkoyen coffee machine parts, b and q washing machine parts, b braun dialysis machine parts, b&q washing machine parts, and back to life machine replacement parts.
Small batch CNC machining type
One of the most common types of small batch CNC machining is milling. Milling involves the use of a rotating cutting tool to remove material from a workpiece, creating a desired shape or form. This process is highly versatile and can be used to produce a wide range of parts, from simple flat surfaces to complex three-dimensional shapes. Milling is particularly useful for industries such as automotive, aerospace, and electronics, where precision and accuracy are crucial.
Another type of low-volume CNC machining is turning. Turning is a process that involves rotating a workpiece while using cutting tools to remove material and form a cylindrical shape. Therefore, this method is often used to produce parts such as shafts, rods, and tubes. And because of its high efficiency, turning can also be used to create simple and complex designs. Therefore, it is widely used in medical, oil and gas, defense and other industries.
In addition to milling and turning, small batch CNC machining also includes processes such as drilling, tapping, and grinding. Drilling involves creating holes in a workpiece using a rotating cutting tool, while tapping is the process of creating internal threads in a hole. These processes are essential for industries that require precise hole placement and threading, such as the automotive and aerospace sectors.
Grinding, on the other hand, is a process that involves using an abrasive wheel to remove material from a workpiece, resulting in a smooth and precise surface finish. This method is commonly used in industries such as tool and die making, where high precision and surface quality are critical.
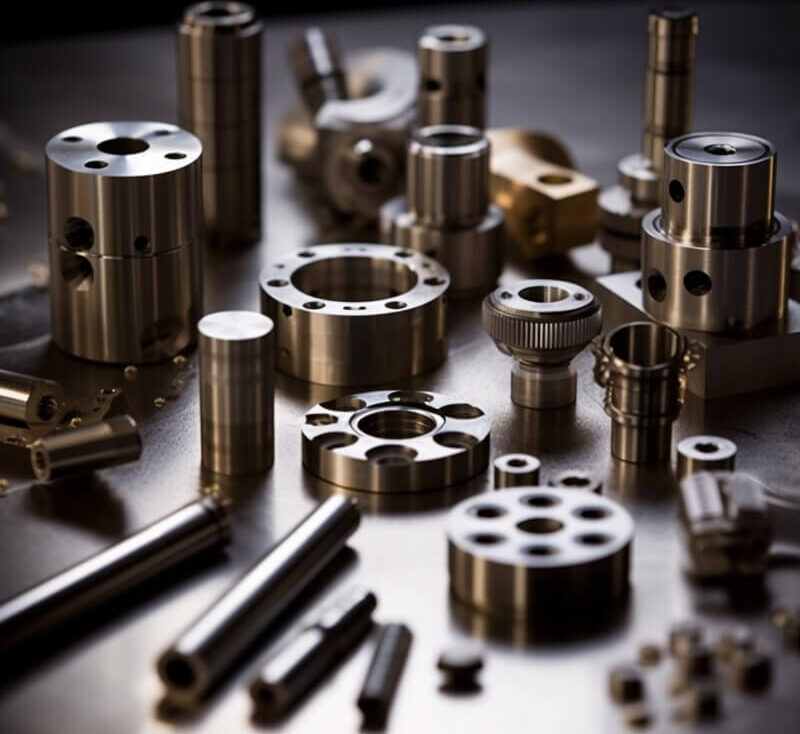
Small batch CNC machining offers several advantages over traditional manufacturing processes. Firstly, it allows for greater flexibility and customization. With CNC machines, it is possible to quickly and easily change the design or specifications of a part, making it ideal for businesses that require frequent design iterations or customization for specific customer requirements.
Secondly, small batch CNC machining offers improved accuracy and precision. CNC machines are capable of producing parts with extremely tight tolerances, ensuring that each piece meets the required specifications. This level of precision is essential for industries that demand high-quality and reliable components.
Furthermore, small batch CNC machining offers increased efficiency and cost-effectiveness. CNC machines can operate continuously, reducing the need for manual labor and minimizing the risk of errors. This results in faster production times and lower production costs, making it an attractive option for businesses looking to optimize their manufacturing processes.
In conclusion, small batch CNC machining encompasses various processes such as milling, turning, drilling, tapping, and grinding. Each of these methods offers unique advantages and is suitable for different industries and applications. Small batch CNC machining provides businesses with greater flexibility, improved accuracy, and increased efficiency, making it a valuable tool in modern manufacturing.