Ultimate Guide to Aerospace Machining
The aerospace industry is home to modern technology and innovation, and is highly dependent on precision and efficiency. Key to achieving these attributes is CNC machining, a process that can significantly increase the efficiency of producing critical aerospace components. Commercial Machining Inc. is a provider of CNC machining and turning process services to the aerospace, defense and commercial industries.
This introduction explores how CNC machining is not only a part of the aerospace industry, but a key element to its continued growth and success.
1.What is aerospace?
The aerospace industry encompasses a wide range of sectors, including commercial aviation, space exploration, and military applications, with a global market value of approximately $800 billion.
Aerospace manufacturing involves a multitude of technologies, from traditional casting and welding to advanced metal additive manufacturing processes.
In between these two extremes is aerospace machining, known for its precision and ability to innovate materials and design processes, which is essential to the dynamic needs of the industry.
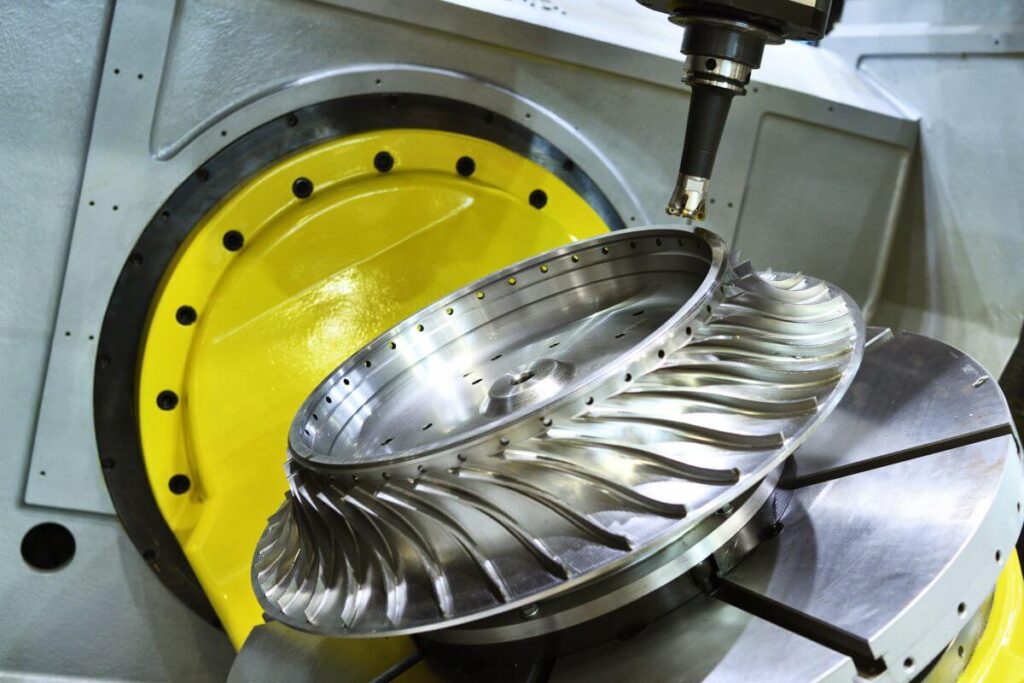
2.What is aerospace machining?
Aerospace machining is one of the many applications of CNC machining technology, a specialized manufacturing technique that combines advanced digital technology with precision engineering to produce critical components for the aerospace industry.
Since its introduction around 1942, CNC machining has played an important role in the manufacture of critical aerospace components such as bulkheads and wing skins that require high levels of precision and consistency.
The process involves removing material from a workpiece using a computer-controlled, powered cutting tool. Digital technology allows new parts to be produced quickly and precisely.
Today, aerospace machining processes have evolved to include a wide range of components, such as gearboxes, landing gear, and electrical components. The technology is also essential for adding detailed features to existing parts or engraving critical information such as serial numbers.
Aerospace machining processes require very exacting precision, especially for jet engine components, which require tolerances as low as 4 microns, which is much tighter than standard CNC machining tolerances.
High-quality 5-axis CNC machining centers are often used to achieve this precision, highlighting the role of this technology in producing end-use parts and prototyping for research and development.
This dual capability ensures that CNC machining remains at the forefront of aerospace manufacturing, meeting both current production needs and future technological advances.
3.What are the benefits of using CNC to machine aerospace parts?
CNC machining has significantly improved the manufacturing process and enhanced the performance of aerospace parts.
This section explores the many benefits of CNC machining, with a particular focus on its contribution to the manufacture of lightweight, error-free, and highly consistent components.
1) Lightweight Components
One of the most notable benefits of CNC machining in the aerospace industry is its ability to create lightweight components. Aerospace engineers are constantly seeking ways to reduce component weight to improve fuel efficiency and aircraft performance.
CNC machining can produce complex geometries that are not only strong but also much lighter than those made using traditional manufacturing methods.
Utilizing materials such as aluminum and titanium, which are known for their strength-to-weight ratio, CNC technology ensures that aerospace components are used to their best potential without compromising durability.
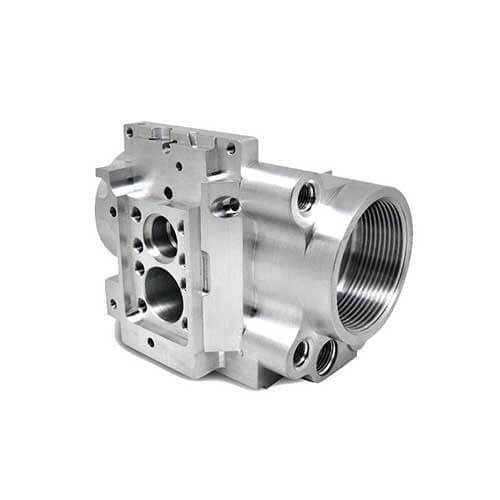
2) Minimizing Part Errors
The precision inherent in the CNC machining process is essential to minimizing errors in the production of aerospace parts.
Advanced CNC machine tools are highly repeatable and have tight tolerances, which is essential in the aerospace industry where every micron counts.
This precision reduces the risk of part failure, thereby improving the safety and reliability of aerospace components.
By automating the machining process, CNC technology can also minimize human error, ensuring that each part is produced to exact specifications.
3) Accuracy and Precision
CNC machining has unparalleled accuracy and precision, which is indispensable in the aerospace industry. The ability to adhere to stringent manufacturing standards and achieve tolerances accurate to a few microns makes CNC machining ideal for aerospace applications.
This level of precision is essential for components that must withstand extreme conditions and pressures to ensure they perform reliably in critical applications, such as in engines and structural components of spacecraft and aircraft.
4) Consistency
Another benefit of CNC machining is the consistency it brings to part production. Whether it is a single part or thousands of parts, CNC machines produce each component with the same precision and specifications, reducing variability that can affect the performance of aerospace parts.
This consistency is essential to maintaining the quality and reliability of different batches of parts, supporting the aerospace industry’s need for consistency in a high-volume production environment.
5) Efficiency
CNC machining stands out in the aerospace sector for its efficiency. The integration of CNC machines facilitates the automation of the production process, allowing for continuous operation without the inconsistencies associated with manual labor.
This not only speeds up the manufacturing cycle, but also maximizes the utilization of materials and resources.
The precision of CNC machinery ensures that each part is produced with minimal waste, thereby optimizing the use of precious materials such as titanium and aluminum alloys.
This efficiency is critical in an industry where time and resource management directly impact financial and operational success.
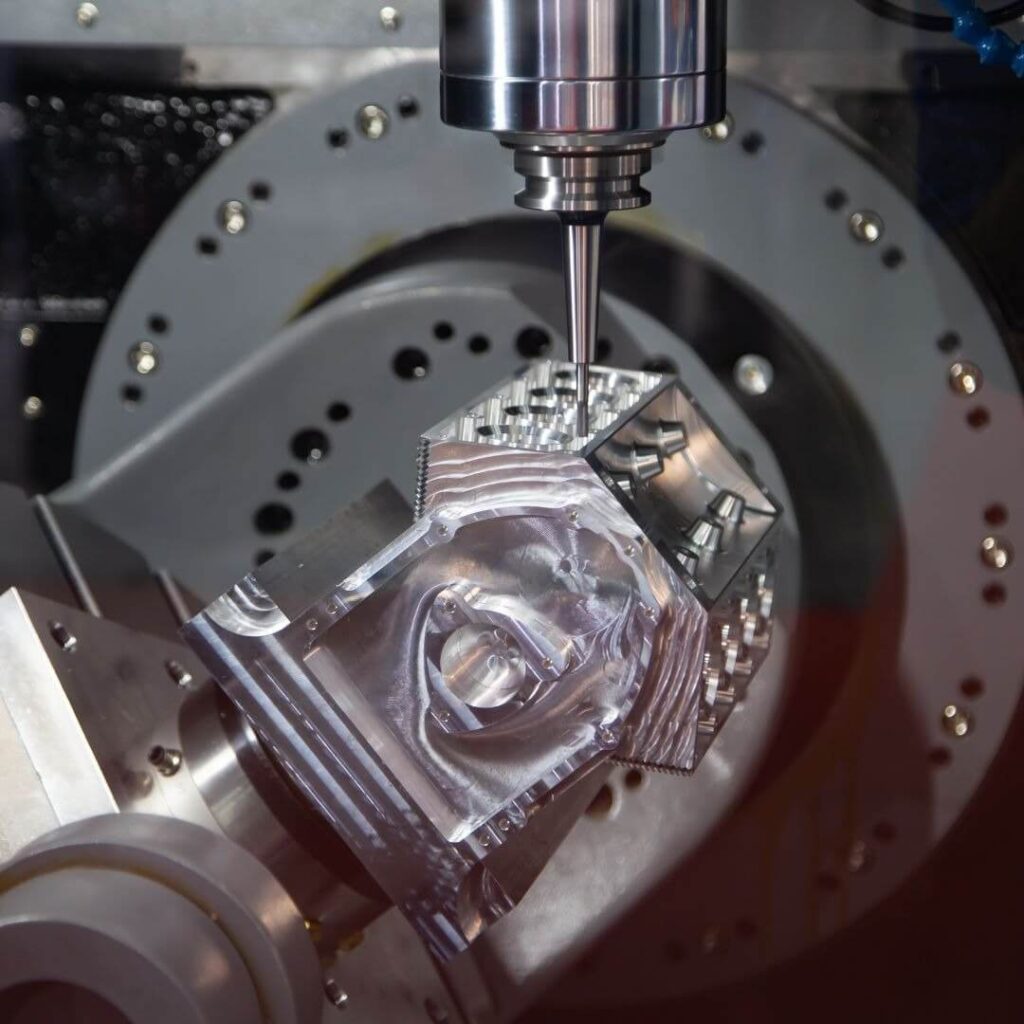
6) Reduced Manufacturing Costs
Implementing CNC machining in the aerospace manufacturing industry can significantly reduce costs. By automating many processes that are traditionally done by hand, CNC machines reduce the need for a large labor force, which is a significant expense in any industry.
In addition, the high precision of CNC machining minimizes material waste and reduces the incidence of errors that can lead to costly rework or scrap.
The ability to quickly and accurately produce parts also reduces time to market, further reducing overhead costs and increasing the profitability of aerospace manufacturing operations.
7) Achieve Complex Geometries
CNC machining is able to achieve complex geometries, which is particularly useful in the aerospace industry. Aerospace components often require complex designs with precise dimensions and tolerances, which are difficult to achieve with traditional manufacturing methods.
CNC machine tools, especially those with 5-axis capabilities, can create detailed, complex shapes that meet the stringent requirements of aerospace parts.
This capability allows for the design and production of more advanced and efficient aerospace systems, which can help improve aircraft performance and functionality across the board.
8) Speed
Speed is another key benefit of CNC machining. CNC machining produces parts significantly faster than traditional manufacturing methods, which is critical in an industry where meeting project deadlines can make or break an aerospace program.
The rapid production capabilities of CNC machines also speed up prototyping, allowing aerospace engineers to test and improve their designs more quickly. This speeds up development cycles and brings innovations to market faster, providing a competitive advantage in the fast-moving aerospace sector.
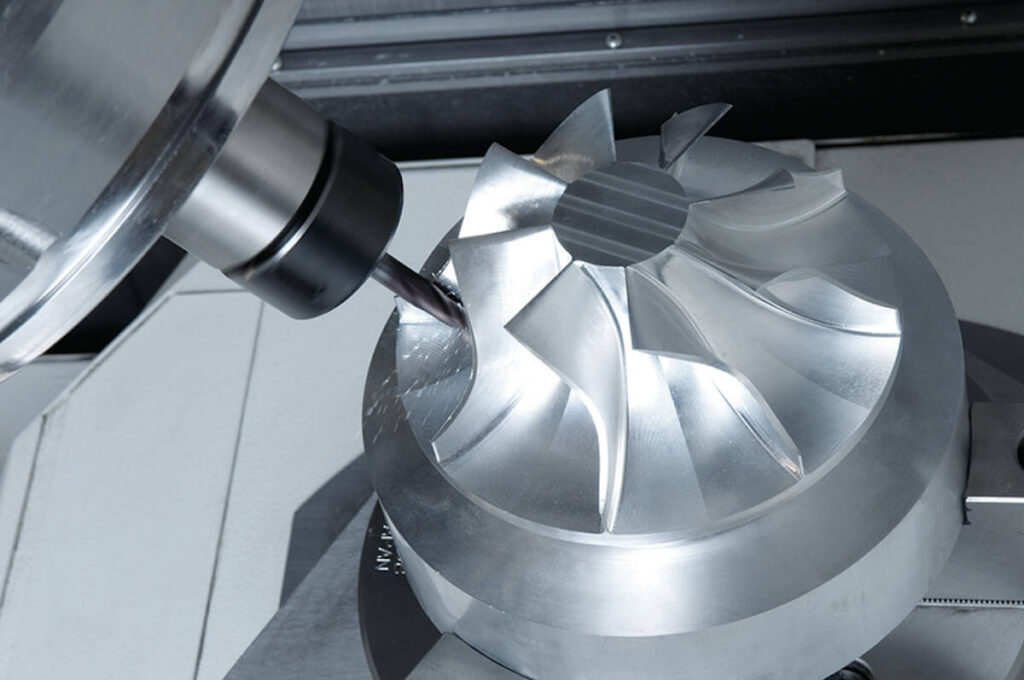
4.What materials are used in aerospace machining?
In aerospace machining, the choice of materials is crucial due to the harsh environment these parts are subjected to.
Not only must the materials used have extraordinary strength and durability, they must also meet specific criteria, such as weight, corrosion resistance, and high-temperature performance.
Let’s take a look at some of the main materials that are indispensable in aerospace machining.
1) Carbon Steel
Carbon steel is highly valued in aerospace machining for its versatility and strength. It is mainly used to make structural parts due to its high tensile strength and ability to withstand huge stresses without deformation.
The material’s robustness makes it ideal for making parts that are critical to the safety and stability of aerospace vehicles, such as landing gear assemblies and parts of aircraft frames.
2) Brass
Brass is another commonly used material in aerospace machining, especially for parts that require corrosion resistance and electrical conductivity. It is often chosen for electrical connectors, terminals, and housings in aerospace engineering.
The machinability of brass allows it to have precise dimensions and clean surfaces, which is essential for precise and high-risk aerospace applications.
3) Bronze
Bronze stands out in aerospace machining for its corrosion resistance and resistance to metal fatigue. These properties make it suitable for bearings, bushings, and similar components that are subject to considerable mechanical wear and need to maintain a long service life under harsh operating conditions.
The durability and strength of bronze ensure that these components can withstand the rigors of aerospace operations without frequent replacement.
4) Copper
Copper is indispensable in the aerospace industry due to its excellent thermal and electrical conductivity, making it a must-have material for cooling systems and electrical components.
In aerospace machining, copper is often used in heat exchangers, wiring, and other heat-dissipating components that play a key role in maintaining the operational integrity of aerospace systems. Its efficient thermal conductivity helps manage the extreme temperature changes encountered during flight and space exploration missions.
5) Aluminum and aluminum alloys
Aluminum and its alloys have long been a staple in aerospace machining, highly regarded for their light weight yet high strength. Aluminum alloys, especially those such as 7075, are favored for their high tensile strength and corrosion resistance.
This resistance is largely due to the oxide coating that naturally forms when aluminum is exposed to air – a property that greatly enhances its durability in harsh environmental conditions.
7075 alloy, with zinc as its main alloying element, is not as easy to machine as other alloys, but has extremely high fatigue strength. This makes it ideal for critical structural components such as wings, fuselages, and support structures.
Other aluminum alloys are also widely used, such as 4047 (which can be used as a cladding or filler), 6951, which is often used in tail fins, and 6063, which is known for structural applications.
The 6000 series alloys are known for their machinability, making them the first choice for complex aerospace components that require precision and complex machining capabilities.
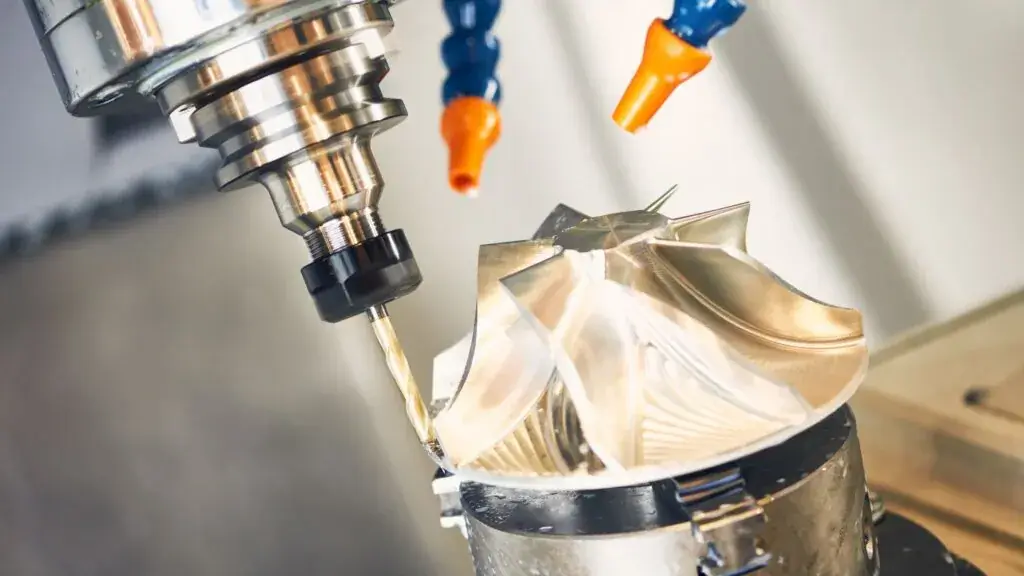
6) Titanium and Titanium Alloys
Titanium alloys are indispensable in the aerospace industry, where the demand for materials with excellent strength-to-weight ratios and excellent performance at high temperatures is non-negotiable.
Titanium’s strength and corrosion resistance make it the material of choice for fuselages and jet engine components, including disks, blades, shafts, and casings.
Titanium is widely used in commercial and military aircraft, as evidenced by models such as the Airbus A380, Boeing B787, F-22, F/A-18 and UH-60 Black Hawk helicopter.
These applications highlight the critical role of titanium in modern aerospace engineering. However, machining titanium presents unique challenges due to its high hardness, which can lead to increased tool wear and heat buildup.
To address these issues, aerospace machining often requires adjustments to the machining process, such as reducing machine speed and increasing chip loads.
Despite these challenges, advanced CNC machining equipment common in aerospace environments can still handle titanium alloys well, ensuring that the advantages of titanium alloys are fully utilized without compromising the quality or integrity of the machined parts.
7) Inconel Superalloys
Inconel superalloys, especially Inconel 718, play a vital role in aerospace machining due to their excellent heat resistance and high-temperature strength.
Developed by Specialty Metals, Inconel 718 is a nickel-chromium-based superalloy designed for demanding applications. It was originally used in jet engine diffuser housings for the Pratt & Whitney J58 engine, which powers iconic aircraft such as the Lockheed SR-71 Blackbird.
The alloy’s properties are also used in modern aerospace programs, including SpaceX’s Falcon 9 launch vehicle, where it is used in the engine manifolds of the Merlin engine. Its use also extends to a variety of aerospace components, such as turbine blades, ductwork, and engine exhaust systems.
The machining of Inconel 718 requires careful handling to minimize work hardening; therefore, it is typically machined using slow but aggressive cutting methods, using hard tools to control its toughness and reduce tool wear.
Despite these challenges, its excellent weldability and durability make it a top choice for aerospace applications, where reliability under extreme pressures and temperatures is critical.
8) Engineering Plastics
In addition to metals, the aerospace industry is increasingly relying on high-performance engineering plastics such as PEEK, polycarbonate, and Ultem. These plastics are valuable alternatives to metals due to their lightweight and excellent mechanical properties, including impact and vibration resistance, sealing capabilities, and chemical resistance.
They also offer superior electrical insulation properties compared to metals, which is critical to the safety and functionality of aerospace applications.
Engineered plastics are used in a variety of aerospace components, from cabin interiors such as tray tables and armrests to critical operating components such as insulation, piping, and valve components.
These materials must meet stringent flame, smoke, and toxicity regulatory requirements to ensure safety in aerospace environments.
Notable plastics used in aerospace machining include Nylon 6, PEEK, Ultem, and PPS, each favored for their ability to meet specific performance criteria required for commercial and military aerospace applications.
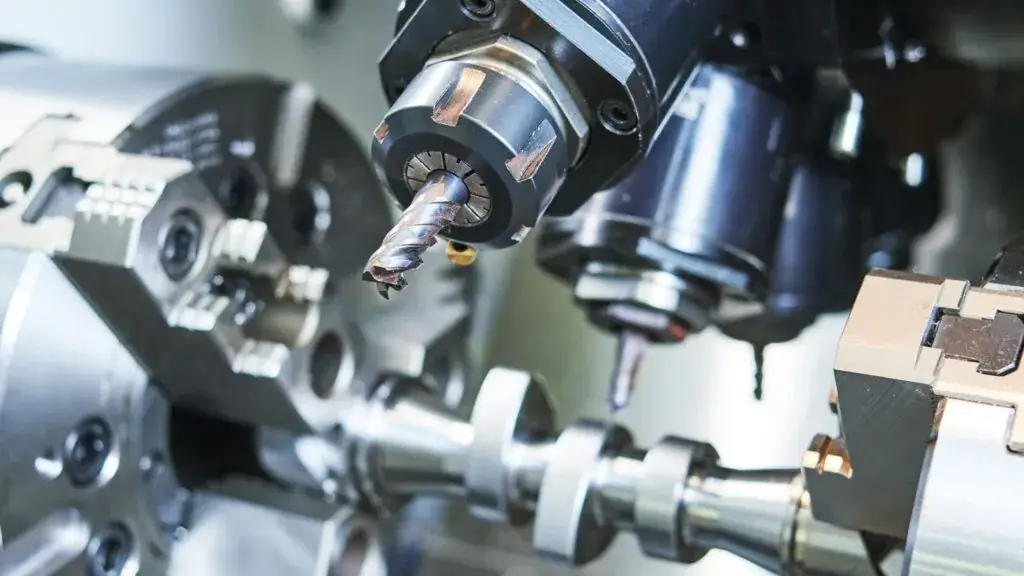
5.What are Aerospace Machining Processes?
CNC machining processes are an integral part of aerospace manufacturing, providing the precision and flexibility required to produce complex components that meet stringent industry standards.
Let’s explore how different CNC machining processes are used in the aerospace sector and why they are particularly well suited to this sector.
1) CNC Milling
CNC milling is a versatile process that is widely used in the aerospace sector to manufacture complex components such as fuselages, engine mounts, and aerospace prototypes. The process involves using a rotating multi-point cutting tool to remove material from the workpiece, creating precise shapes and details.
Capable of machining a wide range of materials, including aluminum alloys, titanium, and advanced composites, CNC milling is ideal for aerospace applications where lightweighting and strength are critical. Its precision allows for the production of parts with tight tolerances, which is critical to the safety and functionality of aerospace components.
2) CNC Turning
CNC turning is another technology used in the aerospace industry, particularly for the production of round or cylindrical parts such as shafts, pins, and bushings. The process involves a single-point cutting tool that runs parallel to the material being cut, allowing for high-precision machining.
The turning process is valued in the aerospace sector because it is able to achieve an excellent surface finish and meet the tight tolerances required for parts that must withstand high stresses and temperatures during flight.
3) CNC Drilling
CNC drilling is used to drill holes in aerospace components, which are often used to fix parts or hydraulic systems. The process uses a multi-point drill to accurately and efficiently drill holes in the material.
CNC drilling can be performed on flat or curved surfaces, making it highly adaptable to aerospace applications, where drilling precise holes is often critical to both the structural integrity and functionality of the part.
4) 5-Axis CNC Machining
5-axis CNC machining stands out in the aerospace manufacturing industry because of its ability to machine the extremely complex geometries that are often required in modern aerospace designs.
Unlike traditional 3-axis machining, 5-axis machines can rotate on two additional axes, allowing the cutting tool to approach the workpiece from any direction.
This capability reduces the need for multiple setups, increases productivity and significantly reduces machining time. 5-axis CNC machining is particularly useful for parts such as turbine blades, fuselage components and wing panels, which require complex shapes and deep cuts with the highest precision.
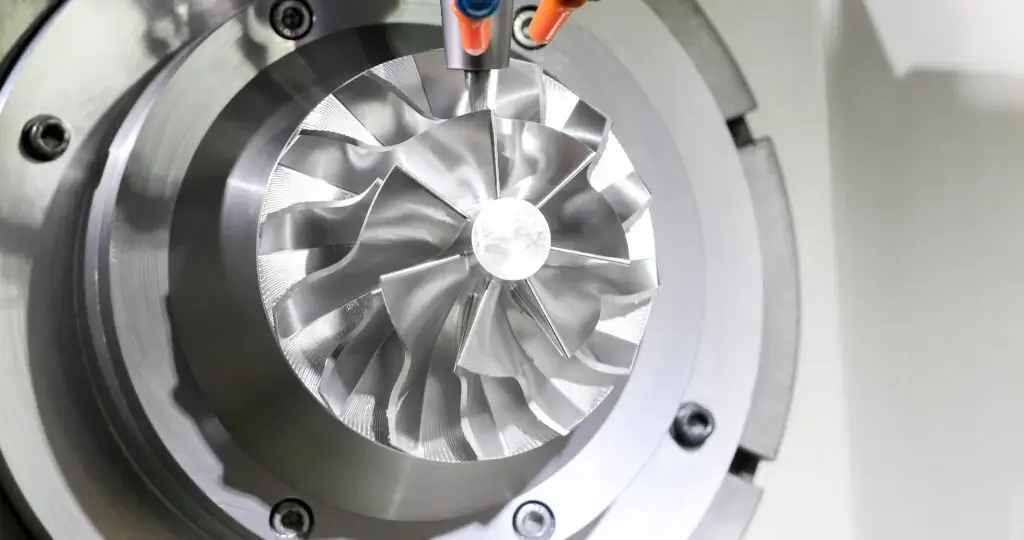
6.Standard Surface Finishes for CNC Machined Aircraft Parts
Surface finishes for CNC machined aircraft parts are important to improve the durability, performance and aesthetics of the parts. These surface finishes also protect the parts from environmental factors and reduce wear.
Here is an overview of 8 standard surface finishes used in aerospace machining:
1) Anodizing
Anodizing is a process that enhances corrosion and wear resistance by electrochemically converting the metal surface into a durable, corrosion-resistant anodized coating. This coating is particularly useful for aluminum parts and helps them withstand the harsh conditions of the aerospace environment.
2) Passivation
Passivation involves treating or coating a metal to reduce the chemical reactivity of its surface. In the aerospace industry, stainless steel parts are often passivated to remove surface contaminants and enhance corrosion resistance, ensuring longevity and reliability.
3) Polishing
Polishing makes the surface smooth and shiny by physically rubbing the material or using chemicals. This surface treatment not only enhances the beauty of aerospace parts, but also reduces the adhesion of surface contaminants.
4) Powder coating
Powder coating uses a free-flowing dry powder that forms a skin-like coating after being cured by heat. It has excellent durability and resists chipping, scratching, fading and wear, making it ideal for parts exposed to harsh operating conditions.
5) Painting
Spray painting is used to apply a specific color or protective layer to aerospace parts. It is corrosion-resistant and solar reflective, and can also be used to apply company colors or visibility markings that are critical to safety and branding.
6) Hard coating
Hard coating refers to applying a hard and durable film to the part substrate to improve wear resistance and service life. In the aerospace industry, this may mean a ceramic coating that also provides thermal insulation.
7) Thermal Spray Coatings
Thermal spraying involves spraying molten or semi-molten material onto a surface to form a coating. The process is used to improve or restore the properties or dimensions of a surface, thereby extending the service life of aerospace components by providing heat, corrosion, and wear protection.
8) Electroplating
Electroplating is the process of adding a metallic coating to an object by applying a negative charge to it and then immersing it in a solution containing the metal salt to be deposited. The process is used in aerospace to improve conductivity, reflectivity, corrosion resistance, or reduce friction on parts.
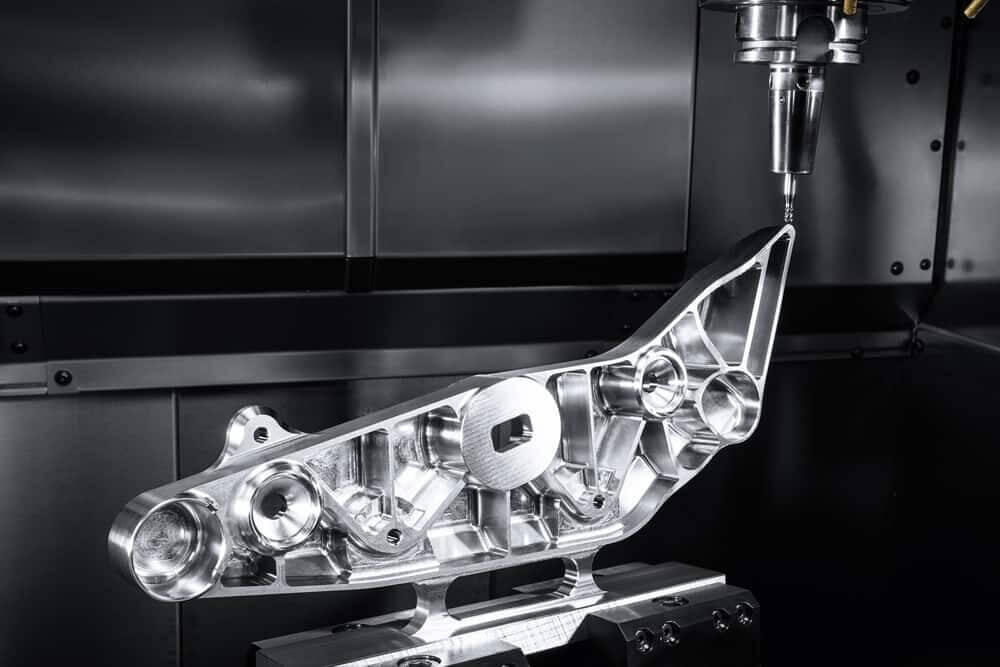
7.What does the future hold for aerospace machining?
Technology is constantly evolving and innovating at an astonishing rate. Aerospace manufacturers must keep up with these trends to compete.
Several important trends are likely to drive the future of CNC machining in the aerospace industry:
- Additive Manufacturing: Combining additive manufacturing (3D printing) with traditional CNC machining can produce complex parts with unique geometries that were previously impossible or too expensive to produce.
- Smart Manufacturing: The adoption of Industry 4.0 technologies (such as IoT devices) will allow for real-time monitoring, data collection, and analysis during CNC machining. This will enable manufacturers to optimize operations, improve quality control, and reduce waste.
- Digital Twin: Creating a digital replica of a physical CNC machine to analyze and optimize its performance is another technology that is gaining a lot of attention. This process can facilitate more efficient machine setup, preventive maintenance, and remote troubleshooting.
If you are looking for an experienced Precision machining manufacturer, Xavier is your ideal choice.The Xavier team is well equipped to provide high quality aerospace parts machining solutions. If you require more information or would like to discuss your machining needs, please feel free to contact us.