The Importance of Quality Assurance in Ultra Precision Machining
Ultra precision machining is a highly specialized field that involves the manufacturing of components with extremely tight tolerances and high surface finishes. These components are used in a wide range of industries, including aerospace, medical, and electronics. Given the critical nature of these components, it is of utmost importance to ensure that they meet the highest quality standards. This is where quality assurance comes into play.
Why is quality assurance so important in ultra precision machining?
Quality assurance is a systematic approach to ensuring that products or services meet specified requirements. In the context of ultra precision machining, it involves a series of processes and procedures that are designed to monitor and control the manufacturing process to ensure that the final product meets the desired specifications.
One of the key reasons why quality assurance is so important in ultra-precision machining is the high accuracy required. Because parts manufactured through ultra-precision machining often have tolerances in the micron or even sub-micron range, this means that even the slightest deviation from the required specifications can render the component unusable or perform poorly. So by implementing quality assurance measures, manufacturers can minimize the risk of producing defective parts and ensure that the final product meets the required accuracy.
Another reason why quality assurance is crucial in ultra precision machining is the high cost associated with manufacturing these components. Ultra precision machining requires specialized equipment, tooling, and skilled operators, all of which come at a significant cost. If a defective component is produced due to a lack of quality assurance, it can result in wasted resources and increased production costs. By implementing quality assurance measures, manufacturers can identify and rectify any issues early in the manufacturing process, minimizing the risk of producing defective components and reducing costs.
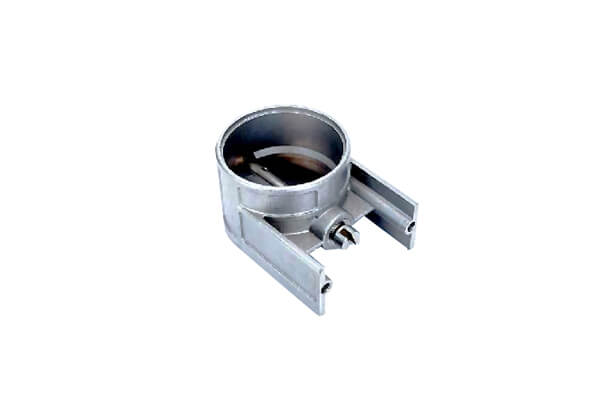
Furthermore, quality assurance plays a vital role in ensuring the reliability and performance of components manufactured through ultra precision machining. These components are often used in critical applications where failure can have severe consequences. For example, in the aerospace industry, a faulty component can lead to catastrophic accidents. By implementing quality assurance measures, manufacturers can identify any potential issues that may affect the reliability or performance of the component and take corrective actions to ensure that the final product meets the required standards.
To achieve effective quality assurance in ultra precision machining, manufacturers employ a range of techniques and tools. These include statistical process control, where data is collected and analyzed to monitor and control the manufacturing process. Additionally, advanced inspection techniques such as coordinate measuring machines and optical profilometers are used to measure and verify the dimensions and surface finishes of the components. By utilizing these tools and techniques, manufacturers can ensure that the manufacturing process is under control and that the final product meets the desired specifications.
In conclusion, quality assurance is of utmost importance in ultra precision machining. It ensures that components meet the required precision, reduces production costs, and ensures the reliability and performance of the final product. By implementing quality assurance measures and utilizing advanced tools and techniques, manufacturers can minimize the risk of producing defective components and ensure that the final product meets the highest quality standards.