Understanding CNC Machining Centers: The Ultimate Guide
CNC machining centers are one of the important advancements in manufacturing technology, bringing unprecedented precision, repeatability, and efficiency in producing complex parts.
These machines are automated and controlled by computers with pre-programmed software that uses a unique control system to direct the movement of cutting tools, thereby performing complex machining operations without much human assistance. They are used in various fields such as the aerospace industry, the automotive industry, medical device manufacturing, and consumer electronics production.
1.What is a CNC machining center?
1) Different types of machining centers
We can roughly divide machining centers into horizontal (HMC) and vertical (VMC) types.
- Horizontal machining center (HMC): The spindle of HMC is oriented horizontally. This design allows for better chip removal and is best suited for high-volume production. These machines are favored because they can handle heavy, large workpieces with greater efficiency and accuracy.
- Vertical machining center (VMC): The spindle of VMC is placed vertically, suitable for precision machining of smaller parts, mainly metal parts. They are generally easier to use and more flexible, suitable for operations such as mold making, drilling or contouring that require high visibility or easy access to the workpiece.
Each machine tool has its own unique advantages, depending on the manufacturer’s needs for a particular job.
2) How do CNC machines work?
A machine equipped with computer numerical control (CNC) operates under the guidance of coded programming instructions without the need for any manual operator. It starts with a computer-aided design drawing (CAD), which is then converted into a computer-aided manufacturing file (CAM).
This CAM file is then converted into a CNC program, which contains all the commands needed to direct the machine. The CNC machine’s controller reads these commands and then instructs its motor to move the cutting tool along a predetermined path to produce the desired part.
The machine uses a feedback system to track and adjust the tool position, ensuring high accuracy and repeatability of the manufacturing process. With the automation of such complex machining tasks, CNC technology has improved production efficiency and accuracy through different departments.
3) Advantages of using CNC machining centers
① Precision and correctness
One of the most important advantages of CNC machining centers is their ability to produce highly precise and accurate parts. They can always maintain strict tolerances, which is necessary for industries that handle complex parts. Computer automation and control eliminate human error, ensuring that all parts produced are of uniform quality.
② Increased production speed
Unlike manual machining, which needs to stop at a certain point in time, CNC machining centers can work continuously and uninterrupted, even for a week, thereby increasing production speed.
This is achieved by using fast cutting tools and powerful motors, which facilitate a rapid manufacturing process, thereby reducing turnaround time and improving overall production efficiency.
③ Versatility and flexibility
CNC machining centers are versatile because they can perform a variety of functions, such as drilling and milling. They can be quickly reprogrammed so that different tasks can be completed with one machine, making the transition between manufacturing different parts smooth without wasting a lot of time setting up another device or changing its configuration parameters.
This adaptability is particularly useful during custom manufacturing or prototyping when new designs need to be adjusted quickly.
④ Cost economy
While the purchase price of a CNC machine may seem high at first, in addition to labor costs, it can save operators money in the long run unless maintenance costs are incurred. In addition, precision cutting can reduce the generation of scrap, thereby saving materials.
In addition, labor costs are reduced due to mechanization. In addition, the faster speeds and less downtime achieved during mass production ultimately reduce unit costs.
⑤ Safety Improvement
The use of CNC machining centers can significantly improve the safety of workplaces where such tasks are performed by minimizing direct contact between personnel and the machines used for cutting. Such automated systems only require operator supervision, which reduces the risk of exposure and the possibility of accidents during operation.
The overall effect of using CNC machining centers is that they bring higher precision, faster speeds, greater flexibility, greater cost-effectiveness, and greater safety to different manufacturing industries.
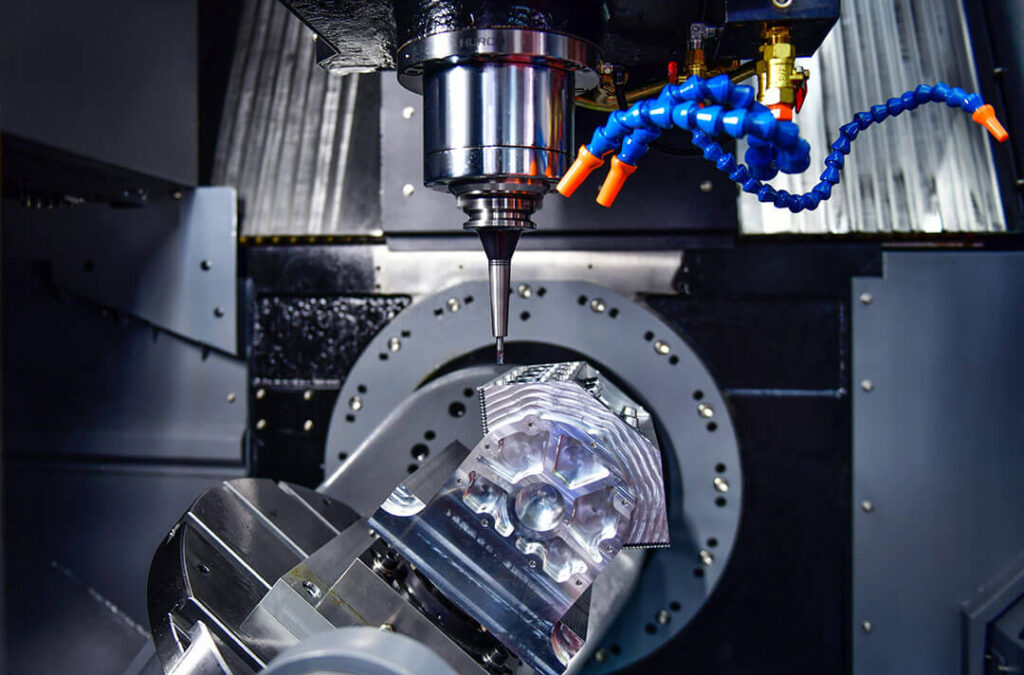
2.How to choose the right CNC machining center?
1) Factors to consider when selecting a CNC machining center
When selecting a CNC machining center, consider a variety of factors based on your needs to achieve the best performance.
- Machine size and capacity: Consider the size and capacity of the machining center to take into account the size and weight of the parts you plan to produce. Make sure it has enough travel and work area to handle the largest workpieces.
- Spindle speed and power determine the machine’s processing capabilities and surface finish requirements. Higher spindle speeds and higher power ratings allow for precise milling operations on harder materials, such as stainless steel or titanium.
- Toolchanger capacity: How many tools can be stored in the tool magazine? A large-capacity toolchanger allows for unattended production runs, while a small-capacity toolchanger limits versatility but may save space if there is limited space near other machines used simultaneously in a mass production process.
- Control system capabilities: Is it easy to use? Does it support automation (e.g., toolpath generation)? Is the system also compatible with my current software?
- Rigidity/stability characteristics: Will vibrations affect accuracy? Pay attention to rigid designs whenever possible, as they minimize deformation caused by cutting forces, resulting in better finished product quality.
- Service/support availability: Choose reputable manufacturers who offer strong technical support services, such as training courses, scheduled maintenance visits, etc.
Considering these aspects, one can choose the right CNC machining center that not only meets their technical needs but also improves overall production efficiency.
2) Difference between Vertical Machining Center and Horizontal Machining Center
The main difference is the orientation of the spindle – a vertical machining center (VMC) has a vertically arranged spindle, while a horizontal machining center (HMC) has a horizontally mounted spindle.
- Spindle orientation: Face milling operations on small workpieces are best performed using a machine with a vertical spindle, such as a VMC. In contrast, an HMC is designed with a horizontal spindle, allowing multiple sides of larger, more complex parts to be machined.
- Workpiece handling: VMCs may require manual repositioning of the workpiece to access different sides, thus increasing the labor required and the time taken. In contrast, HMCs are often equipped with a pallet changer and horizontal positioning that automatically rotates and repositions the workpiece, thereby increasing efficiency by reducing operator intervention.
- Chip removal: Since chips are generated during the cutting process, they need to be effectively removed from the cutting zone to avoid affecting the surface finish achieved, while also preventing tool wear. This is why HMCs are better able to use gravity to evacuate chips than VMCs, allowing them to maintain a higher quality surface for longer, thus extending the life of the tool used; however, additional chip removal systems may be required because chips tend to accumulate on the workpiece itself when using such tools.
Each type has its own advantages and areas of strength. Therefore, the selection process should not only consider which type is suitable for a specific need, but also other factors such as size and complexity, as well as other related materials being worked on.
3) The impact of 3-axis vs. 5-axis CNC machines
The main difference between 3-axis CNC machines and 5-axis CNC machines is the number of directions the cutting tool can move. For simple tasks such as drilling holes or cutting basic shapes into flat surfaces, a 3-axis CNC machine operates along the X, Y, and Z axes. It is capable of performing a variety of operations, but its ability to handle complex geometries is limited.
On the other hand, a 5-axis CNC machine has two rotary axes (A and B) in addition to the linear X, Y, and Z axes. This additional flexibility enables the machine to reach hard-to-access parts of the workpiece, making it possible to mill complex and compound shapes without repositioning, especially with a 5-axis machining center.
This capability is very beneficial for components that require high precision and detail, such as those used in the aerospace, automotive, or medical industries.
The decision to use a 3-axis or 5-axis CNC machine depends primarily on the complexity and precision of the intended machining task. 3-axis machines are cheaper and simpler to program than 5-axis machines, but 3-axis machines are more flexible because they allow repositioning during operation, so 3-axis machines cost more and require advanced programming.
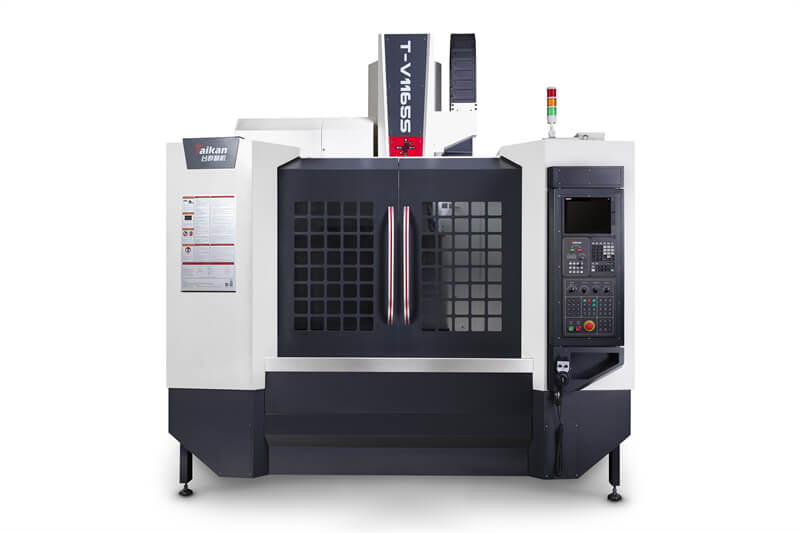
3.How to maintain a CNC machining center?
1) Daily maintenance tips
Proper maintenance of CNC machine tools is very important to ensure that they have a long life and perform optimally. Here are some key points to consider when performing regular maintenance:
- Daily inspection: Check basic components such as coolant level, hydraulic system, lubrication system, etc. every day. Make sure all fluids are at the recommended level and top up when necessary.
- Cleaning: Clean the machine regularly to avoid accumulation of chips, dust and other debris. Clean the filter frequently so that airflow and coolant flow are maintained at optimal levels; also remove chips from the work area.
- Lubrication: Apply sufficient lubricant to all moving parts to reduce friction, which causes these parts to wear over time; refer to the manufacturer’s instructions for the frequency of applying oil in different locations.
- Check the spindle/tool holder: Visually inspect the spindle/tool holder and note any signs of wear or damage. Make sure the tool is properly mounted and well balanced to prevent vibrations that may damage other nearby components.
- Software/Firmware Updates: Always keep your software and firmware updated as they often contain new features and bug fixes designed to enhance performance and reliability; regularly check with the vendor/manufacturer for any releases.
- Alignment/Calibration: Occasionally align or calibrate your machine tool by checking its positioning accuracy against the given target value and making necessary adjustments for precise cutting operations.
- Monitor Temperature: Pay attention to the operating temperature of the equipment and, unless otherwise specified, should not exceed certain limits as overheating can lead to serious failures; therefore, ensure good ventilation and proper functioning of cooling systems such as fans.
- Replace worn parts such as belts/seals/bearings, etc. in a timely manner; this can prevent sudden failures, thus saving repair costs after unexpected failures, especially in Mazak machining centers.
These simple steps will help you keep your CNC machining center running smoothly and reliably while continuously producing high-quality products.
2) Importance of Using Coolants and Lubricants
There are many important reasons for using coolants and lubricants in CNC machine tools. First, they can reduce the heat generated inside the machine tool during machining, thereby extending tool life and improving the surface finish of machined parts.
Secondly, these materials act as lubricants, thereby reducing friction between the cutting tool and the workpiece material, thus increasing the precision and efficiency of the machining operation. Lastly, coolants and lubricants help to remove chips and swarf from the cutting area, thus protecting the workpiece and tool from any form of damage.
In every case where I have used coolant or lubricant regularly, it has ensured that my machine tools have a long life while providing high-quality output after machining.
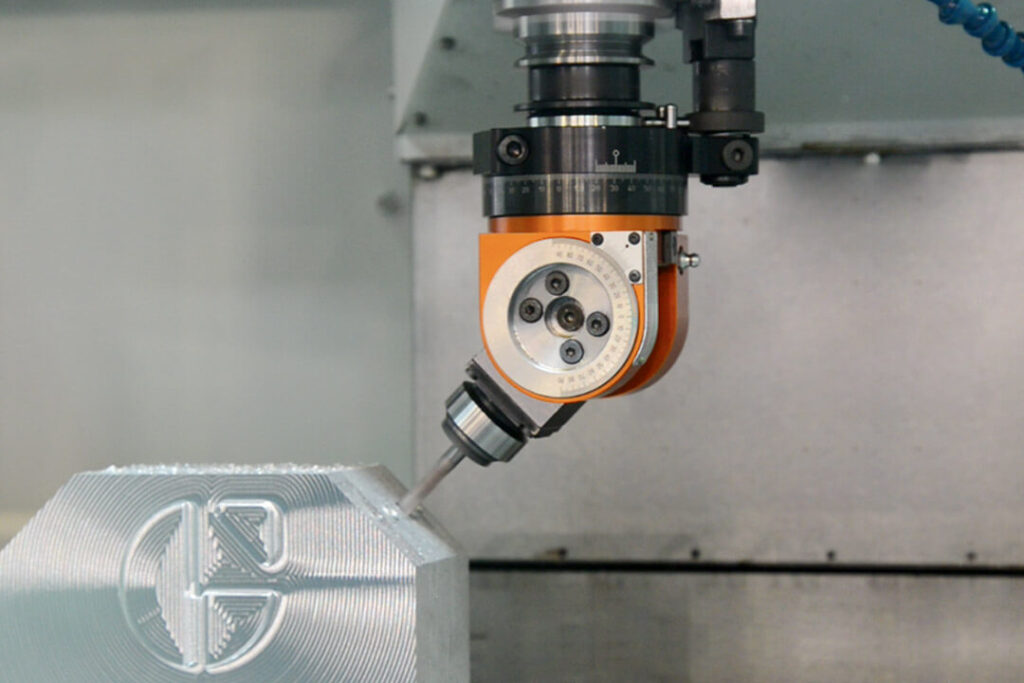
4.What are the applications of CNC machining centers?
1) Industries that use CNC machining centers
CNC machining centers are used in many industries for their accuracy, reliability, and efficiency. In the aerospace sector, they manufacture complex parts such as turbine blades or structural parts that require very tight tolerances to fit accurately, usually using 5-axis machining centers.
Automakers rely on these machines to produce engine blocks, etc., while medical companies need them to manufacture surgical instruments with precise dimensions – any mistake can be fatal.
Therefore, this technology helps such businesses achieve high productivity while still maintaining the quality control measures needed to save lives, time, and money, both of which are equally important factors in today’s global healthcare system.
2) Common Materials Processing
From what I have seen, there is no better machine than a CNC machining center when it comes to processing different materials. The most common material used in machining is aluminum, which is lightweight and easy to machine, so it is often used in the aerospace and automotive industries.
Similarly, stainless steel is strong enough to not corrode easily, while being tough enough to be used in medical devices or any other high-stress parts that may require this material, and can therefore benefit from precision machining on a center with an rpm spindle.
It should also be noted that plastics such as ABS or polycarbonate can be machined; they are versatile in the manufacturing process and are particularly useful during the prototyping stage or when making custom pieces.
Essentially, by effectively processing these materials, precision, reliability, and quality can be guaranteed in different areas through the use of CNC machining centers, both vertically and horizontally.
3) Best Practices for Extending Tool Life
Based on my experience and research on top industry resources, there are several practices that can help extend tool life in CNC machining. Firstly, it is very important to select the right cutting tool according to the material being machined as this will reduce wear and improve chip evacuation.
Secondly, using better coatings such as titanium nitride (TiN) or diamond-like carbon (DLC) can improve tool durability and performance.
Thirdly, cutting parameters such as speed, feed rate and depth of cut should be optimized as they greatly affect the life of the tool.
Fourthly, both the machine itself and its components should be regularly maintained to ensure that everything runs smoothly without unexpected breakdowns.
In addition, proper cooling methods and suitable lubrication techniques must be adopted for efficient heat dissipation, thereby reducing friction, which further extends tool life.
4) Tips for Improving Surface Finish
In order to achieve a perfect surface finish in CNC machining, there are steps that must be followed.
Firstly, you must use a sharp and high-quality cutting tool because if the tool is not sharp, it may cause irregularities on the surface of the material.
Secondly, reducing the feed rate can greatly improve the surface finish as it allows the tool to make lighter cuts, thereby promoting better chip evacuation. Another is that the spindle speed should be higher, as it reduces the scallop height on the workpiece, making the workpiece smoother than before.
In addition, using the right coolant or lubricant helps reduce heat and friction so that no defects are left on the surface.
It is also important to ensure that the machine is well calibrated and free of vibrations, as vibrations can cause chatter marks on the surface.
By incorporating these techniques into the production process of the workpiece, machinists can greatly improve the surface quality of CNC machined parts.
5) Importance of Regular Calibration
In order to achieve maximum accuracy and consistency in the manufacturing process, CNC machines must be calibrated regularly. This process ensures that all components are functioning properly within a given accuracy range, enabling the production of high-quality products that meet strict quality control standards.
It also detects and corrects any potential mechanical or system failures before they become big problems. In addition, frequent calibration improves machine efficiency, minimizes downtime and avoids expensive production interruptions.
A complete calibration program prolongs equipment life and increases productivity levels in all areas of a CNC machining center, while ensuring its reliability at every stage.

5.What is the role of automation in CNC machining centers?
1) Benefits of Automated Machining Processes
There are many benefits to using computer numerical control systems in machining centers that can greatly improve the manufacturing process, especially when working with metal parts.
First, production capacity can be increased through automation because the machine can run uninterrupted with minimal human monitoring; therefore, high production output can be achieved.
Second, the technology guarantees consistency of quality by minimizing the fluctuations inherent in manual operations, thereby improving accuracy and reducing the rate of defective parts.
Third, automated systems are designed to make full use of existing resources and materials, thereby improving efficiency while reducing a lot of waste.
Fourth, safety standards are greatly improved when dangerous tasks are left to robots because they do not make mistakes as often as humans and do not need to rest or sleep.
Last but not least, data collection becomes easier than before, and process tracking becomes easier, allowing predictive maintenance, etc., resulting in a more streamlined workflow to shorten production cycles.
2) Types of CNC machining automation
① Fixed automation
Also known as hard automation, refers to the use of dedicated equipment designed specifically to perform a specific task or set of tasks. This approach is highly efficient and cost-effective in mass production, but lacks flexibility for changes or different product designs. Transfer lines and automatic assembly machines are examples.
② Flexible Automation
These systems can be quickly reprogrammed to perform different tasks or produce a variety of products. They are suitable for low to medium production with frequent product changes. For example, robotic arms and multi-function CNC machine tools can be easily adjusted or reassembled to suit different jobs.
③ Integrated Automation
Integrated automation involves integrating different automation processes into a system that is under a single control. This includes computer integrated manufacturing (CIM) systems, in which machine tools are integrated with automated material handling systems as well as production planning software.
The main benefit here is that all links involved in the production process become coordinated, thereby increasing productivity levels and reducing delivery times.
These types of CNC machining automation provide manufacturers with a variety of options for improving efficiency, accuracy and adaptability according to specific production requirements.
3) The impact of automation on production efficiency
Because the automation system ensures uniform quality, full utilization of resources, and optimization of manufacturing processes. As a result, production increases while unit costs decrease, especially in machining centers with efficient chip removal functions. All of these advantages suggest that if automation were adopted on a large scale, productivity could be greatly increased.
If you are looking for an experienced CNC machining manufacturer, Xavier is your ideal choice. The Xavier team is well-equipped to provide high-quality CNC machining solutions. If you need more information or to discuss your machining needs with us, please feel free to contact us.