Understanding machining chatter and how to avoid or reduce it
Machining chatter occurs in almost all manufacturing processes. Heavy machines used in manufacturing generate a lot of vibrations, which lead to poor surface finish and loss of dimensional accuracy.
Machinists have to deal with this undesirable vibration in different processes such as CNC turning, milling or drilling. However, it is helpful to understand machining chatter and its causes and know how to avoid it as it helps prevent downtime, which is terrible for a business.
This article discusses the definition, types, consequences and how to avoid machining chatter.
1.What is machining chatter?
Machining chatter is the unwanted vibration generated when cutting or drilling a part. Chatter is caused by the vibration imbalance caused by repeated relative movement of the workpiece and the tool.
Vibration occurs when the machined part and the cutting tool move in opposite directions, resulting in a change in the cutting load with each rotation of the machining tool.
This can be caused by improper manufacturing design or inappropriate tooling. Chatter usually produces a lot of noise and visible ripples on the surface of the machined part.
Machining chatter comes in two forms, namely:
- Resonant
- Non-resonant vibration
Non-resonant vibration is caused by using unevenly worn tools on the workpiece. This vibration usually persists throughout the machining cycle and is caused by mechanical reasons that are easy to check.
Resonance, on the other hand, occurs at specific stages of the tool path, such as machining concave corners.
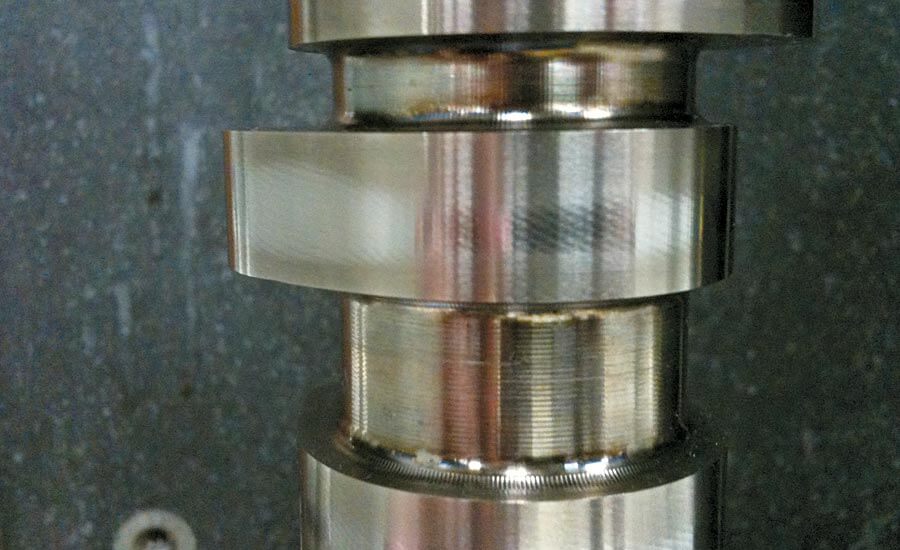
2.Types of machining chatter
In CNC machining, you may encounter two main types of chatter.
These include:
1) Tool chatter
Typically, CNC milling cutters vibrate during cutting operations. They begin to dress while transferring vibrations to the workpiece and add various features. As a result, the tool and workpiece begin to slide against each other, causing the chatter to increase significantly.
2) Workpiece chatter
Sometimes, when you incorrectly fix the workpiece on the milling machine table, it can cause some deflection and vibration. As a result, the thin walls of the workpiece may begin to vibrate when transferred to the cutting tool.
It is worth noting that some chatter is often unavoidable. If the vibrations occurring during machining exceed 100µm, scratches may appear on the workpiece surface.
However, for the sake of product quality, it is best to consider taking measures against tool and workpiece chatter. We will discuss how to avoid chatter below.
3.What are the consequences of chatter in machining?
If not controlled, machining chatter can lead to various adverse effects, such as reduced machining efficiency. Here are some of them:
1) Shortened tool life
The cutting tool cannot withstand the vibration shock generated by the collision between the tool and the workpiece. These vibration effects can cause the cutting tool to chip and dull, damaging the surface quality of the cut part.
In addition, it also reduces tool life and cutting efficiency, and the tool replacement cost is expensive.
2) Shortened machine life
The machine tools used to process different parts are composed of various parts, so when vibration occurs, these parts vibrate at the same frequency. The spindle and other important parts that produce different axes of motion may wear faster than expected.
Therefore, machine chatter puts excessive stress on machine parts, which may reduce machining efficiency and cause downtime if not controlled.
3) Poor surface finish
Chatter during machining affects the aesthetics of the workpiece and, in extreme cases, reduces its tolerance. One of the most obvious consequences of machine chatter is poor surface finish. Chatter can cause obvious ripples on the surface, which affects the quality and durability of the part.
4) Reduced Dimensional Accuracy
When a cutting tool chatters during CNC machining, it deviates from the path that the CAM initiated. However, this deviation may result in an improper fit of the parts. These parts may be too tight, too long, too short, or too loose due to dimensional inaccuracies.
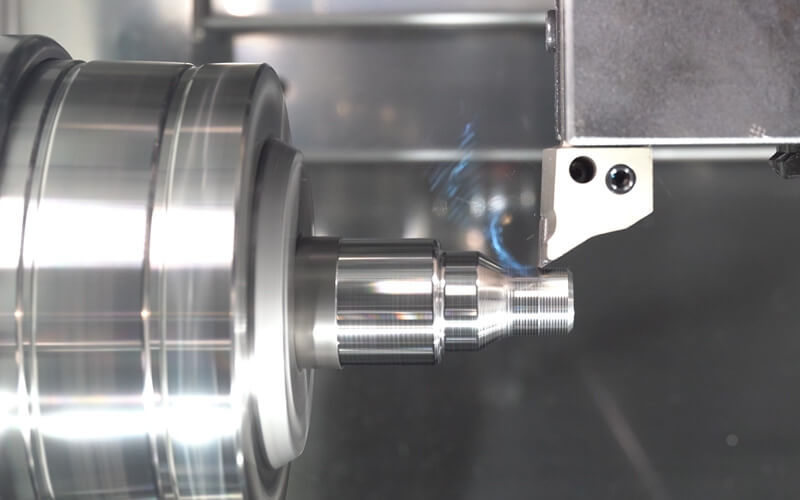
4.How to avoid or reduce machining chatter?
Manufacturing companies use different methods to minimize chatter in machining operations and ensure that both the workpiece and the cutting tool are in good condition.
Here are some steps on how to reduce CNC machining chatter:
1) Optimize machining strategies
The degree of engagement of the tool with the workpiece varies with traditional milling. As the milling cutter moves along the path, it is often subjected to excessive forces. Therefore, the best way to reduce chatter is to obtain a regular, engaged tool path. You can reduce the depth of cut as an alternative.
Also, try rethinking the configuration of the spindle. For example, if resonant chatter is the cause of machining chatter, increasing or decreasing the machine’s rotational speed by 5% will minimize the resonant vibration that occurs.
Note that some CAM software has a feature that allows you to continuously change the spindle speed. Most manufacturers adopt this feature because it is widely used.
2) Use the right workholding method
A balanced machine tool has better adjustment capabilities. A variety of factors such as incorrect positioning and fixing are the main causes of chatter in CNC machining.
However, a tool holder with end and tape contact helps ensure maximum rigidity during machining. Therefore, the surface quality of the part will not be affected even at the lowest rotation speed.
You also need to check whether the mechanical vise, vacuum table, chuck or other workholding device applies enough pressure to the workpiece to keep it firm and fixed.
However, when considering the use of clamps and fixtures to apply clamping pressure as required, do not clamp only one end of the extended thin workpiece. Thin-walled parts have difficulty absorbing shocks. Therefore, filler materials can enhance their overall rigidity and reduce chatter. Tailstock or similar forms of stable support are ideal for such parts.
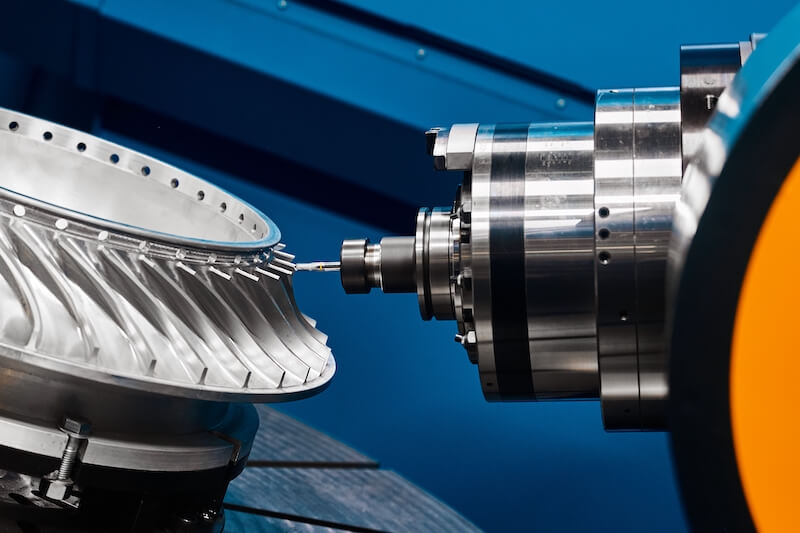
3) Use the right cutting tool
Using the right cutting tool can help avoid machining chatter. Some cutting tools produce more vibration than others. Eliminating tool chatter is not as easy as eliminating workpiece chatter.
Therefore, when selecting any tool, you should consider the following factors:
- Tool coating
- Correct substrate geometry
- Tool aspect ratio
If it meets the technical specifications, machinists and engineers will usually use the largest machine tool that fits the job. The sturdier the tool, the less likely it is to chatter. Long or thin tools often deflect. Therefore, consider choosing a shorter tool with the largest diameter.
However, using a combination of tools with various flutes is the most effective way to reduce chatter in machining. Also, consider reducing the tool protruding from the tool holder and firmly fixing it. When you do this, the machine is less likely to chatter.
Make sure the tool has a sharp blade to minimize the cutting force of the CNC milling machine. You should always consider the stability of the machining environment and timely maintenance of the tool. Likewise, it is crucial to apply appropriate and consistent tool pressure to keep the chip load regular.
4) Determine the ideal tool path
There are two types of CNC milling operations: up milling and down milling. Chatter of curved parts can be reduced if the cutting force is applied in the same direction as the clamping direction. This is often an important aspect of cutting that needs to be considered.
Typically, CNC milling machines come pre-installed with ball screws that help improve the efficiency and precision of CNC machine technology. Therefore, you can use a vertical machining center to prevent chatter during cutting.
5) Machine Setup and Maintenance
As expected, your CNC machine should be mounted on a concrete floor without any cracks, deformations, or discontinuities. You should know that the arrangement of the machine plays a vital role in minimizing chatter that occurs during machining.
This is because elastic, soft, or damaged flows may increase the chatter of the CNC entity. Therefore, you should consider using anchors and adjustment feet to keep the CNC unit firm and stable to minimize chatter.
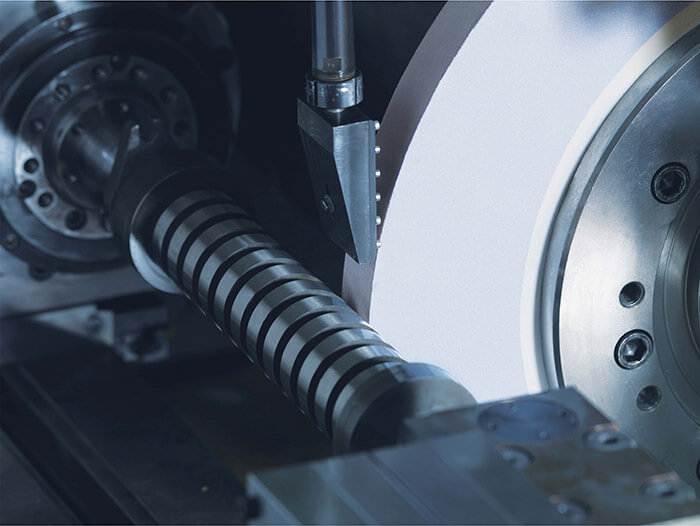
5.Conclusion
Machining chatter is a machining phenomenon that leads to a significant drop in productivity. It affects machine performance, workpiece quality, cutting tools, and machine tool life. Various factors, from the machine’s mounting position to the tool path, can cause chatter.
However, whenever you experience severe vibration, thoroughly check what is happening. Make sure the tool and workpiece are properly fixed and the configured machining options are correct to effectively mitigate this chatter.
1 Comment