Introduction to Threading: Processes and Methods
Threading is a cool machining project that can be used in a variety of industries such as manufacturing, construction, and even fashion. It involves machining threads on a material, usually a metal rod or tube, in order to attach a nut, bolt, or other component.
The process is a precise and complex one that requires careful attention to detail and adherence to specific cutting guidelines. In this article, we will introduce the process, discuss the processes involved, the methods used, and the cutting guidelines that must be followed, and look at practical applications in parts.
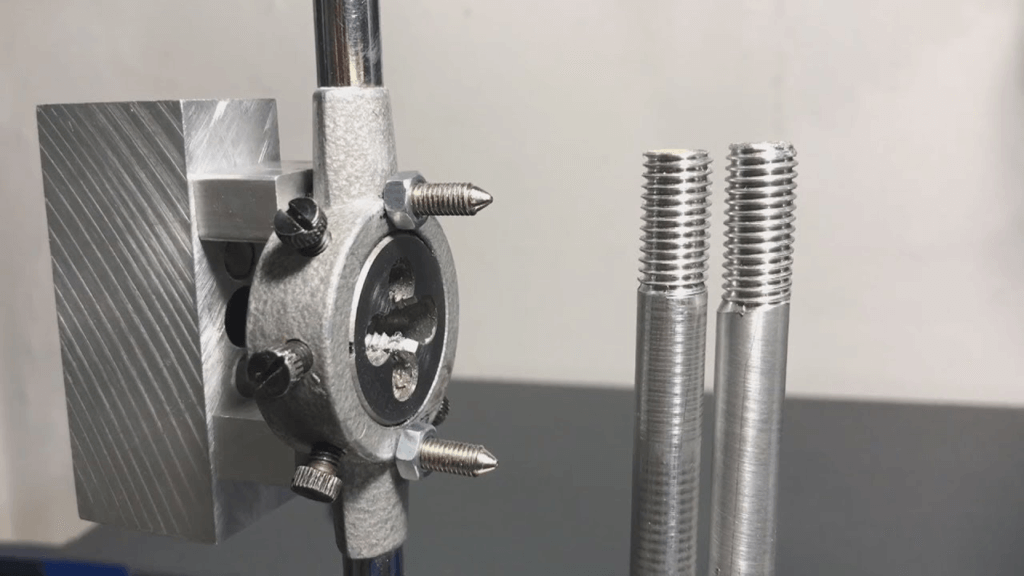
1.Types of machining processes
The process can be broadly divided into two types: internal threading and external threading. Internal threading involves machining threads on the inside of a hole or cylindrical object, while external threading involves machining threads on the outside of a rod or tube. Both of these machining processes require different tools and techniques to achieve the desired results.
1) Internal Threading
It is usually performed using a tap, which is a cutting tool with multiple flutes or cutting edges. The tap is inserted into the hole and as it rotates, it cuts threads into the material. The tap must be carefully aligned with the hole to ensure accurate and precise threads.
The process is usually done in multiple stages, starting with a roughing tap to remove excess material and then a finishing tap to create the final threads.
2) External threading
It is usually done using a die, which is a cylindrical tool with cutting edges on the inner surface. The die is placed around the rod or tube and as it rotates, it cuts the threads into the material. Like internal threads, external threads also require multiple stages, starting with a roughing die to remove excess material and then a finishing die to create the final threads.
During the process, it is critical to maintain proper alignment and apply consistent pressure to ensure that the process is uniform and accurate.
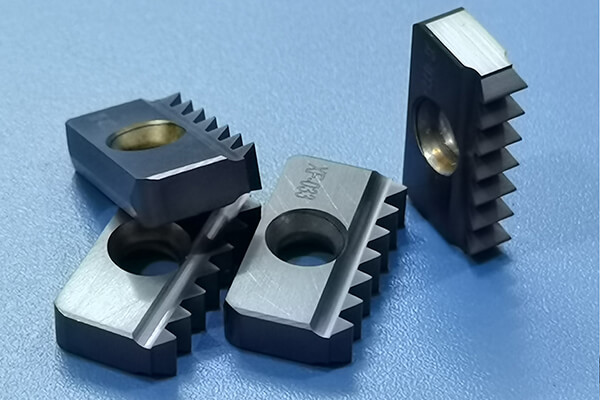
2.Processing methods
May vary depending on the specific requirements of the project. The most common processing methods include hand threading, machine threading, and CNC threading.
- Hand threads is a manual process that requires a skilled operator to use a tap or die to create the threads. It is usually used for small projects or projects where precision is critical.
- Machine threads require the use of power tools such as lathes or threading machines to automate the processing process. This method is faster and more efficient than hand threads and is suitable for large-scale production or projects that require a large number of threaded parts.
3.CNC threads take automation to a new level with computer numerical control (CNC) machines. These machines are programmed to perform precise machining operations with minimal human intervention. CNC threads offer unparalleled accuracy and repeatability, making them ideal for complex projects or projects with tight tolerances.
Regardless of the machining process or method used, specific cutting guidelines must be followed to ensure optimal results. These guidelines include selecting the appropriate cutting speed, feed, and cutting fluid.
Cutting speeds should be selected based on the thread material, with harder materials requiring lower speeds to prevent tool wear. Feed rates determine how fast the tap or die enters the material and should be adjusted to achieve the desired pitch. Finally, the use of cutting fluids is essential to reduce friction and heat during machining, extend tool life, and improve thread quality.
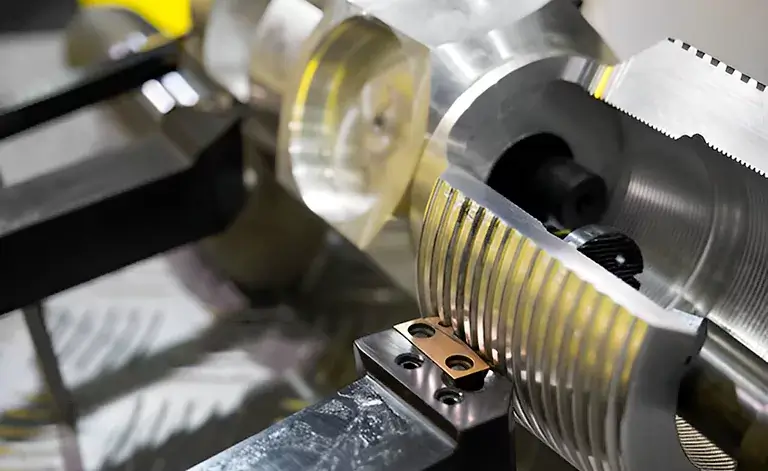
In summary, this process is a fundamental process for machining threads on materials across a wide range of industries. It involves either internal or external threads, each requiring specific tools and techniques. Machining methods range from manual threading to automatic CNC threading. Optimal machining results can be achieved by following cutting guidelines, such as choosing appropriate cutting speeds, feed rates, and cutting fluids.