Common Materials for Turning Metal Parts
Turning metal parts is a common process in the manufacturing industry. It involves removing material from a workpiece to form a desired shape or size. To achieve this, a variety of materials are used, each with its own unique properties and benefits. In this article, we will explore some of the common materials used for turning metal parts.
1.High Speed Steel (HSS)
One of the most widely used materials for turning metal parts. HSS is a type of tool steel containing a combination of carbon, tungsten, chromium, and vanadium. It is known for its excellent hardness, wear resistance, and heat resistance. These properties make HSS ideal for cutting and shaping metal parts. In addition, HSS tools can withstand high cutting speeds, making them efficient and productive.
2.Carbide
Another popular material used for turning metal parts is carbide. Carbide tools are made from a combination of tungsten carbide and cobalt. This material is extremely hard and can withstand high temperatures, making it suitable for cutting and shaping the hardest metals.
Carbide tools also last longer than HSS tools, reducing the need for frequent tool changes and increasing productivity.
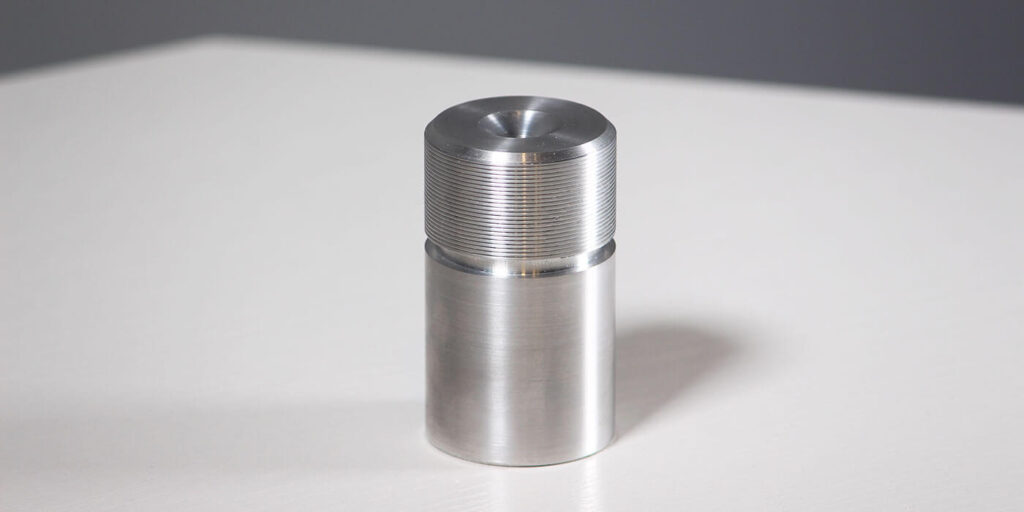
3.Ceramic materials
In recent years, ceramic materials have become increasingly popular in the field of turning metal parts. Ceramics are known for their excellent hardness, wear resistance and thermal stability. They can withstand high cutting speeds and high temperatures, making them ideal for machining hard metals.
In addition, ceramic tools have a longer service life than high-speed steel and carbide tools, further improving productivity and reducing costs.
4.Diamond
Diamond is another material used for turning metal parts, especially in high-precision applications. Diamond tools are made by coating a layer of synthetic diamond on a carbide or ceramic substrate. Diamond is the hardest material known and is ideal for machining extremely hard metals.
It also has excellent thermal conductivity, which can effectively dissipate heat during the cutting process. However, diamond tools are expensive and require careful handling and maintenance.
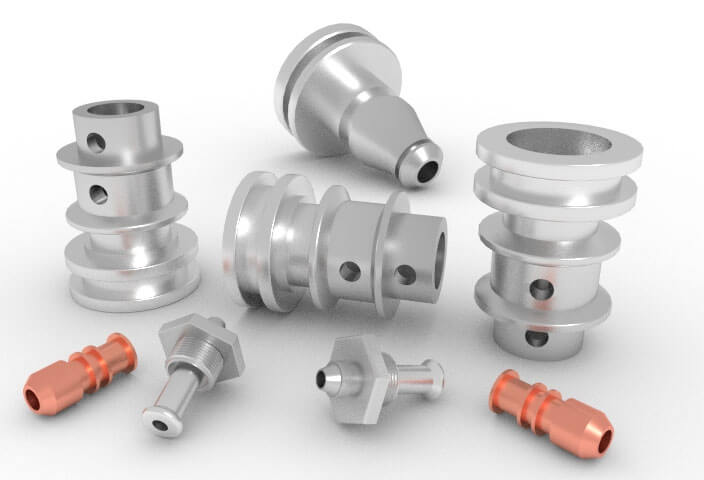
5.In summary
In addition to these materials, there are specialized coatings that can be applied to cutting tools to improve their performance. For example, titanium nitride (TiN) coatings can extend tool life and reduce friction, while titanium carbonitride (TiCN) coatings can provide higher wear resistance. These coatings can all be applied to high-speed steel, carbide, ceramic, and diamond tools, further extending their functionality and versatility.
Turning metal parts is a common process in the manufacturing industry, and the choice of cutting tool material is critical to achieving the desired results. High-speed steel, carbide, ceramic, and diamond are some of the common materials used to turn metal parts. Each material has unique properties and advantages that allow for efficient and precise machining of a variety of metals.
In addition, specialized coatings can be applied to further enhance the performance of cutting tools. By understanding the properties of these materials, manufacturers can select the most appropriate options for their specific applications, thereby increasing productivity and reducing costs.