Importance of Vacuum Casting
Vacuum casting and CNC (computer numerical control) machining are very different manufacturing techniques. The former is a rapid prototyping and production process used primarily with polymers, while the latter involves the precise removal of material using computer-controlled cutting tools. However, their combination, casting machining, has achieved remarkable results in the manufacturing industry.
Let’s explore the various ways these two methods can complement each other and how vacuum casting can be used in conjunction.
1.Prototyping and Model Verification
Vacuum casting is known for its rapid prototyping capabilities. By creating a silicone mold of a master model and then using a vacuum to draw in liquid polymer, manufacturers can quickly produce multiple high-fidelity replicas. Vacuum cast prototypes can be utilized to verify design, fit, and functionality before investing in expensive CNC machining equipment. This approach reduces the risks associated with errors or design oversights.
2.Combining Strength with Aesthetics
CNC machining is known for its precision and ability to machine a wide range of materials, including metals. Parts manufactured using CNC are often characterized by high strength and durability. On the other hand, vacuum cast parts, especially those made from polyurethane resins, can closely mimic the aesthetics of a wide range of materials, including various plastics, rubbers, and even some metals.
3.Master Model Creation
Master models are essential to the vacuum casting process. The silicone mold is based on this model. CNC machining is an excellent way to create this master model because of its accuracy and ability to reproduce intricate details. A CNC machined master model ensures that all subsequent vacuum cast parts will be of high quality and detail fidelity.
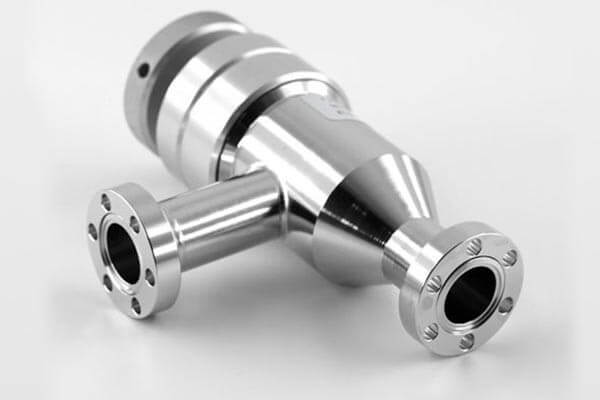
4.Hybrid Components
In some applications, a single component may require both the intricate details and material properties provided by CNC machining and the advantages of a specific polymer or elastomer provided by vacuum casting. In this case, CNC machined parts are combined with vacuum cast components to create a hybrid part that meets its intended use.
5.Cost-Effective Short Runs
For limited production runs, it may not be cost-effective to create a full CNC setup. Vacuum casting, on the other hand, can produce small quantities at a very low cost. Once the master model has been CNC machined, multiple replicas can be produced using vacuum casting. This combination strikes a balance between accuracy and cost, making it ideal for short-run production or limited edition products.
6.Simulated Injection Molded Parts
Vacuum casting can simulate the look and feel of an injection molded production part. By first creating an accurate master model using CNC machining, vacuum casting can then be used to replicate a part that closely resembles the look, texture, and even material properties of an injection molded part. This process is useful for testing and validation before scaling up to large-scale injection molding.
7.Custom Tools and Fixtures
Sometimes, a CNC machining process requires specialized tools or fixtures. Instead of investing heavily in metal tools, manufacturers can opt for vacuum cast tools. While they may not last as long as metal tools, they can be produced quickly and cost-effectively, making them ideal for short-run production runs or specialized, one-off projects.