Vertical Machining Center Basics: A Detailed Guide
Vertical machining centers have been around for many years and remain an integral part of modern CNC technology. CNC vertical machining centers and CNC horizontal machining centers can efficiently process different industrial parts. You can also contact vertical machining center manufacturers to get your equipment.
These machines are versatile and efficient. They remove layers of material from a base material to produce desired parts with various features.
This article discusses vertical machining centers, how they work, components, applications, and everything you need to know to choose the right machining center for your project. Let’s dive in!
1.What is a Vertical Machining Center?
Vertical machining technology is one of the most productive tools in a CNC machine shop. It has a variety of tools in the tool changer and other options to increase and customize productivity.
CNC vertical machining centers are flexible and versatile tools that help machine holes and other attributes on parts with flat surfaces. It operates in a vertical direction using a spindle that works at a steep angle.
Computer control of vertical milling machines allows for automation, tool selection/rotation, repeatability, and contour control.
These modern CNC machines have taken the productivity of milling machines to the highest level, bringing CNC vertical milling centers. These machining centers vary based on their axes, features, and other available options.
You can call a vertical machining center an industrial workhorse because it can deliver parts with extremely high precision and shorter delivery time.
Its components have a sturdy design and provide excellent torque, horsepower and processing speed. The level of automation of vertical milling centers also enables them to cut a variety of materials and reduce overall manufacturing costs.
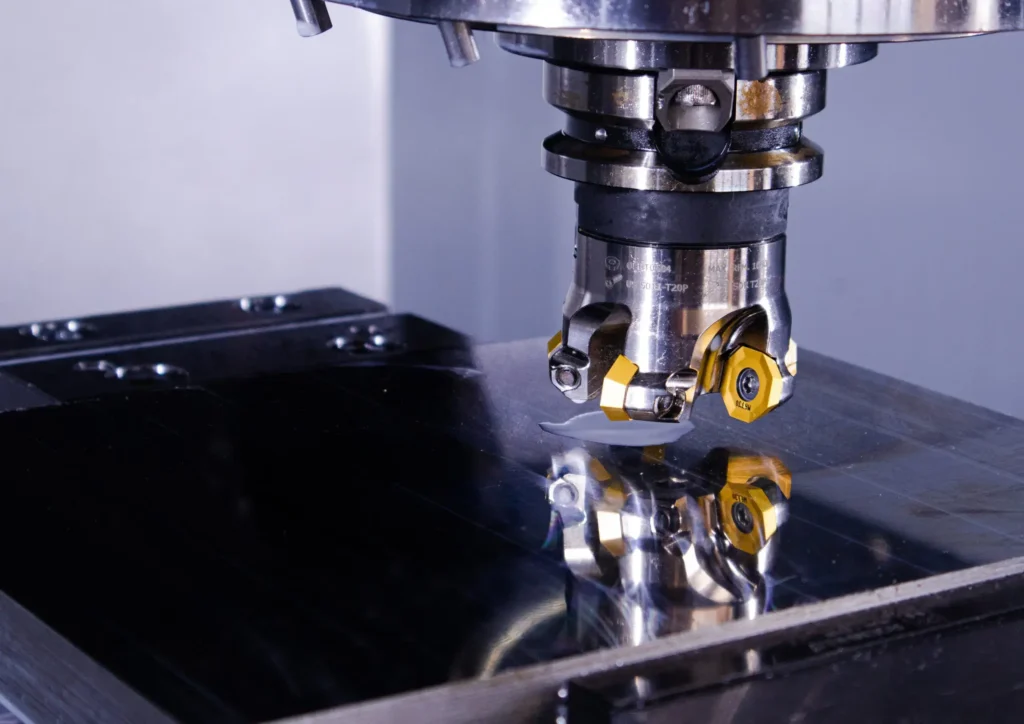
2.How a vertical machining center works
Based on the design model of the parts, the vertical machining center converts the numerous machine tool data generated during the machining process and the machining parameters required for the parts into information codes that are generally accepted and read by the machine tool CNC device.
The machining program is a CNC program used to automatically process parts. These instruction codes are usually stored on information carriers such as disks or punched tapes.
These carriers are sent to input devices, which can read this information and transmit it to CNC equipment, or use computers to send information directly to the machining center to realize the input and output of part programs.
A vertical machining center generally has three linear motion coordinates, and a horizontal axis rotary table is also attached to the workbench, which can easily process round workpieces.
3.Components of a vertical machining center
A vertical machining center consists of many important components. These components are combined to manufacture parts according to ISO manufacturing standards.
These components include the following:
- Rotary Spindle: The milling spindle is usually perpendicular to the table. It is a rotating axis with a device for fixing the tool or workpiece. Generally speaking, the spindle axis plays the role of positioning, supporting and rotating the workpiece.
- Work Table: The worktable is flat and the workpiece can be placed directly on it or using multiple fixtures (such as hard clamps or milling aluminum parts). The table has an X-axis that includes left and right movement, while the Y-axis moves forward and backward. These axes and the Z-axis allow you to add unlimited functions to the workpiece in the plane of movement.
- Tool Changer: The tool changer can automatically select the right tool for different tasks (from rough cutting to fine hole drilling), thereby increasing the productivity of the vertical machining center.
- Rotary Table: By adding additional axes to the vertical milling machine, a simple 3-axis milling machine can be transformed into a 4-axis or 5-axis machine, which can produce complex parts with different surfaces (such as turbine blades), significantly improving productivity.
- Coolant System: Most CNC vertical milling centers use a recalculated coolant system to ensure that the parts and tools are well lubricated. This coolant system usually uses a variety of liquids such as water and soluble oils.
- Enclosure/Full Cover: These covers help reduce splashing caused by milling operations. Likewise, it protects the machinist and the environment from the effects of machining operations.
- Quick Loader: Shuttle tables or other automated part loading systems help increase the productivity of CNC vertical machining centers while reducing downtime.
- Auger/Chip Conveyor: Chip conveyors or augers can help move chips away from the work area to increase productivity and eliminate downtime caused by manual shoveling of waste chips.
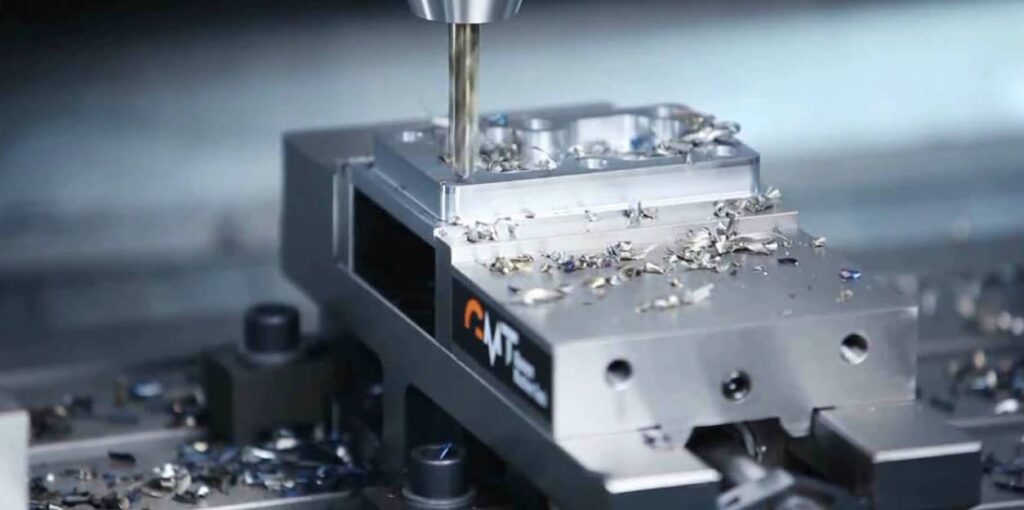
4.Applications and Uses of Vertical Machining Centers
CNC vertical machining centers can process a variety of parts and products for different industries and uses. Industries such as aerospace, manufacturing, machine manufacturers, and medical all utilize this CNC machining technology because of its high accuracy, high precision, and mass production applications.
Here are some machined parts:
1) Unusually shaped parts
Structures such as baskets or bases have irregular shapes. Most of these machined parts require multi-point mixed machining of points, lines, and surfaces. Vertical milling centers with automatic machining functions allow you to machine these complex parts that are usually difficult to manufacture using traditional technology.
2) Box parts
Box CNC parts are parts with a single hole system and multiple cavities. These box parts are common in automobiles and aircraft. Engine blocks, spindle boxes, gear pump housings, diesel engine blocks. With a vertical machining center, you can perform 60% – 95% of standard machine tool operations in one clamping.
Moreover, the vertical machining center has high precision, high efficiency, good rigidity, and is equipped with an automatic tool changer. As long as the machining program is compiled and the appropriate fixtures and tools are used, the difficult problems of box-type parts processing can be solved.
3) Complex parts with a large number of curves
Parts with complex curves such as propellers, cams, and impellers are standard parts in aviation and transportation. It is difficult for traditional machine tools to manufacture these parts with curved parts, surface contours and closed inner cavities with the required machining accuracy.
However, multi-axis vertical machining centers with integrated CNC machine tool technology help to efficiently produce curved parts with the highest precision and accuracy in a shorter time.
4) New parts in trial production
Vertical machining centers have high flexibility and adaptability. When changing the processing object, new programs can be established and entered, certain program segments can be changed, or specific special instructions can be utilized.
For example, you can use the scaling function to produce parts with the same shape but different sizes. It provides great convenience for small batch production, new product trial production or multi-variety production. In addition, it also reduces production preparation and trial production cycles.
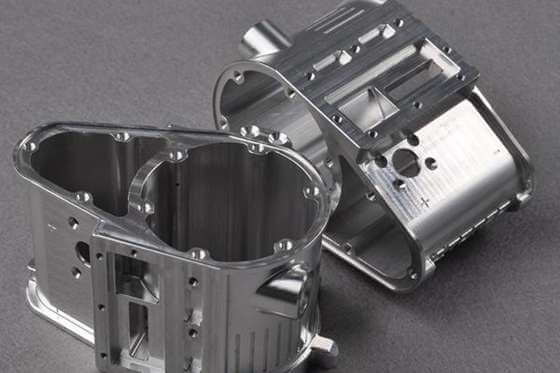
5.The difference between vertical machining center and horizontal machining center
CNC machining center is a precision machine tool that integrates automation, compound processing, multi-function and high speed. Horizontal machining center and vertical machining center are standard CNC milling machines. This section discusses the differences between the structural capabilities and technical performance of these machine tools.
1) Spindle Orientation
Both machines have different orientations that allow you to enjoy the depth offered by a horizontal machining center or the precision offered by vertical machining. This is the main difference between these two machines. The orientation or structure of the spindle determines how the tool interacts/relates with the workpiece.
2) Tool Geometry
The geometry of the tool usually affects the cutting specifications and results. Horizontal machining centers are shorter and thicker, which means they have the stability required to withstand resistance when machining deeper cuts.
On the other hand, vertical machining is more precise and better suited for smaller workpieces. However, this also has its disadvantages. It cannot machine deeper cuts due to vibration, which leads to design deviations.
3) Cutting Specifications and Precision
In terms of removal rate, horizontal centers perform better than vertical centers. Horizontal centers are extremely stable and can produce deeper cuts.
Generally speaking, vertical machines are usually used for limited operations such as grooving and facing. But their cutting and finishing surfaces are very precise. Therefore, this limited cutting capability leads to lower removal rates.
4) Number of machining faces
Vertical machining centers, especially 5-axis milling machines, are better suited for machining multiple sides of a workpiece. They are usually equipped with an integrated pallet to which a fixture or column is attached.
Vertical machining centers also have a much higher spindle utilization rate. Therefore, it is easier to access the front and sides of the workpiece. This increases productivity and reduces human errors. However, these features are limited to horizontal machining centers.
5) Cost per machine
Horizontal machines are much more expensive to purchase and maintain. In addition, they also require professional machinists to handle the operation. Therefore, this increases the overall manufacturing cost.
On the other hand, vertical machine tools cost less than horizontal machines. Similarly, vertical turning and milling centers are much simpler to operate and maintain than horizontal machines. Therefore, they are suitable for all small-scale production.
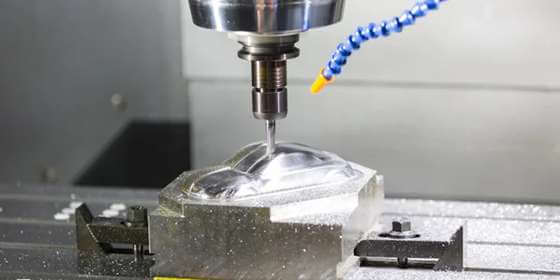
6.How to choose the right machining center for your project?
Vertical machining centers are undoubtedly the machine tools widely used by many professional machine shops. However, when choosing a vertical machining center for your project, its powerful features must be considered.
Some VMCs can perform different machining operations, while others are geared toward specific, specialized tasks. VMCs offer a wide range of adjustment capabilities and versatility, and are very durable.
More importantly, conduct a critical evaluation of your project specifications and the capabilities of the VMC to determine if it is the best fit for your project.
7.Conclusion
The VMC is a versatile and rugged machine that can handle complex machining operations. Advanced models of CNC VMCs feature advanced technology that enables them to machine parts with the tightest tolerances.
In addition, it provides increased uptime and can often be customized to fit part specifications. VMCs are fast and provide excellent quality.
If you are looking for an experienced CNC machining manufacturer, Xavier is your ideal choice. The Xavier team is well-equipped to provide high-quality CNC machining solutions. If you need more information or to discuss your machining needs with us, please feel free to contact us.