Water Jet CNC Machine Best Guide: Types, Uses, Prices, Features
A water jet CNC machine is a versatile piece of equipment for any fabrication shop that can precisely cut a wide range of materials and thicknesses. The machine works by jetting a stream of water at high speeds and pressures, effectively eroding the material being cut, similar to machining, but without the need for cutting tools.
It is an industrial powerhouse capable of cutting metals, plastics, composites, ceramics, and even harder materials. For softer materials like wood and rubber, pure water is sufficient, while harder materials require abrasive additives, such as garnet or aluminum oxide, to enhance the cutting force.
The process is typically performed underwater to reduce noise and mess, and the water jet exerts a force of over 60,000 PSI – 30 times more powerful than a standard pressure washer. This high-pressure water jet is delivered through a microscopic nozzle with a diameter between 0.010 inches and 0.015 inches.
A water jet system consists of a pump and a critical filtration component. Only clean water can achieve the pressure required for sustained cutting, protecting the machine’s sensitive high-pressure parts from damage by impurities and minerals.
Water jet CNC machines have become powerful and popular tools used in many manufacturing processes around the world. Read on to learn why.
1.What are the components of a water jet CNC machine?
Three main components are required to produce the high-pressure water stream that allows for precise cutting edges.
1) High-pressure water system
The system includes the pump that produces the pressurized water and all the piping required to deliver the pressurized water.
2) The machine
A multi-axis water jet (X, Y, Z axis) machine includes a cutting head, a water jet table, an abrasive cutting nozzle, and a material support catcher.
3) Control system
The software in a high-performance control system manages the operator interface, X, Y, Z axis motion control, nozzle positioning, and velocity feedback systems.
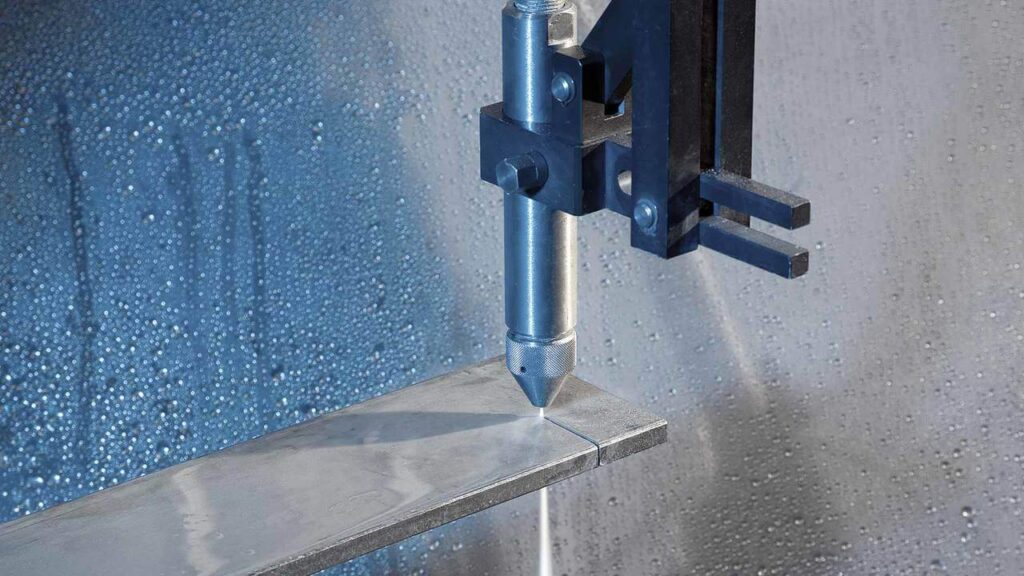
2.How does a water jet CNC machine work?
The water jet CNC process is versatile and can be accomplished in a variety of ways. Most methods involve adding abrasive to the water to help cut particles on the workpiece into shapes that meet precise specifications. Here’s how the water jet process works:
1) Determine the kerf width
Kerf width refers to the amount of material removed during the CNC water jet machining process and is typically 0.040 inches or less in width. The kerf size is a critical design factor that must be considered when determining the dimensions of the final product. Only if the kerf is considered upfront will the dimensions of the final part be accurate.
2) Initial water jet piercing
Piercing is another way of saying the first cut made by the water jet CNC machine, and it starts the water jet CNC process just as a plunge cut might start a lathe process. The most common piercing methods include fixed, linear, circular, and low pressure, depending on the material and the amount of waste generated to minimize scrap.
3) Pressurize the water
The most common method of pressurizing the water is a linear intensifier pump. A linear intensifier pump uses pressurized hydraulic oil at 3000 psi. The low-pressure oil pushes against a piston, which has twenty times the surface area of the high-pressure plunger pushing against the water. Because the low-pressure pump is twenty times larger than the high-pressure pump, the pressure on the larger plunger is intensified twenty times, creating a water pressure of 60,000 psi.
4) Through the pipe
The pressurized water flows to the cutting head through the high-pressure pipe. The high-pressure pipe is made of thermoplastic or stainless steel, with excellent tensile strength, yield strength and smooth inner surface.
5) Water jet CNC machine head
The pressurized water and garnet flow out of the orifice of the cutting head at nearly four times the speed of sound, which can cut steel more than one foot thick. When the water flows through the orifice of the cutting head, which is made of diamond, ruby or sapphire with an aperture of 0.010 inches to 0.015 inches, its velocity increases to more than 90,000 psi, directly affecting the water jet CNC machine process.
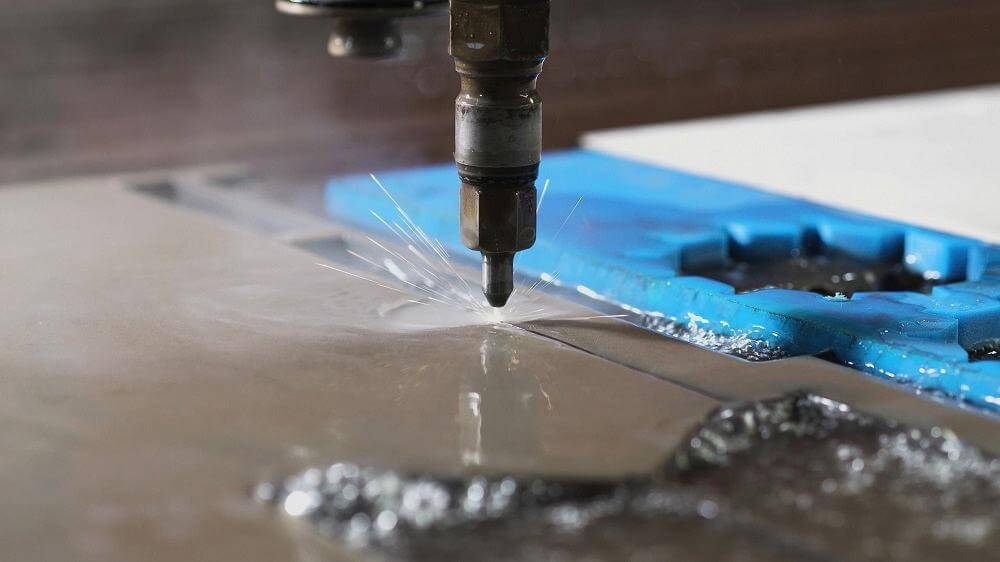
3.Pure water jet CNC machine tools and abrasive water jet CNC machine tool systems
Pure water jet CNC machine tools are the original pure water jet CNC machine tool tools. Pure water jet CNC machines cut soft materials such as foam, plastic, paper, insulation, cement board and car interior. The fine stream they produce provides excellent detail with little material waste.
Abrasive water jet CNC machines are very similar to pure water jet CNC machines, except that garnet abrasive is sucked into the head and mixed with water at high speed. The resulting abrasive water jet is a thousand times stronger than pure water jet cutting, enabling it to cut hard materials such as metal, ceramic, stone, glass and composites.
1) Other types of water jet CNC machines
There are other types of water jet CNC machines, including 3D printers, micro water jets and robotic water jets. However, the style of any water jet CNC machine is determined by its gantry design, which is the system that holds and supports the cutting head:
- Cantilever gantry machine: This machine has an arm above the worktable that holds the cutting tool. This machine is convenient to use, but cannot handle large pieces of material.
- Bridge gantry machines: These machines have a crossbar on the table along which the cutter moves. These machines are known for their stability and are suitable for cutting large objects.
- Flying bridge gantry machines: Similar to the bridge type, but the entire top moves with the cutter. They are used for very precise cuts on large machines.
- Articulated arm gantry machines: These cutters have a bendable arm, like a robotic arm, that is used to move the cutter. They are best suited for fine cuts or tight spaces.
2) Waterjet vs. Other Machine Tools
Water jet CNC machines offer several advantages over other cutting processes, such as laser cutters or plasma cutting. Waterjet systems are more accurate, can cut intricate designs, and can handle heat-sensitive surfaces. The process does not heat the material or change its toughness, and the cut edges are clean and sharp, eliminating the need for secondary finishing.
4.Types of Water jet CNC Machines
In some ways, the waterjet CNC process is similar to using a bandsaw to remove material. However, material cutting in today’s manufacturing environment is much more complex than a bandsaw can handle. On the other hand, water jet CNC machines can perform many different cuts depending on the application.
The following list shows the many capabilities of CNC water jets:
1) One-dimensional cutting
One-dimensional water jet motion is a stationary cut made with a single pass through the workpiece. These cuts are primarily used for finishing and are the most basic operation in a water jet CNC machine, and you can do these operations with or without the addition of abrasives to the water.
2) Two-dimensional (X and Y)
Two-dimensional cutting requires CNC control and programming. CNC machines are equipped with servo motors to control positioning and cutting speed. The Z axis controls the height of the cutting head and accommodates a variety of material thicknesses. The water-filled collection tank has notches to support the workpiece.
3) Three-dimensional (X, Y, and Z)
Three-axis cutting includes the X axis (left to right), Y axis (front to back), and Z axis (top to bottom). The workpiece remains stationary while the cutting head moves along three planes.
4) Four-Dimensional (X, Y, Z, and A)
With four-axis cutting, the workpiece is machined by the X, Y, and Z axes, with a rotational motion added. The A axis flips the workpiece so that the water jet removes material from both sides of the workpiece or cuts a hole in its side.
5) Five-Dimensional (X, Y, Z, A, and B)
A 5-axis water jet system allows the workpiece to move along five axes simultaneously. The workpiece moves along the two-dimensional X, Y, and Z axes, and performs a 180-degree rotation with different rotational motions around these three axes. Five-axis machines can make complex shapes and components, but require extensive CNC programming.
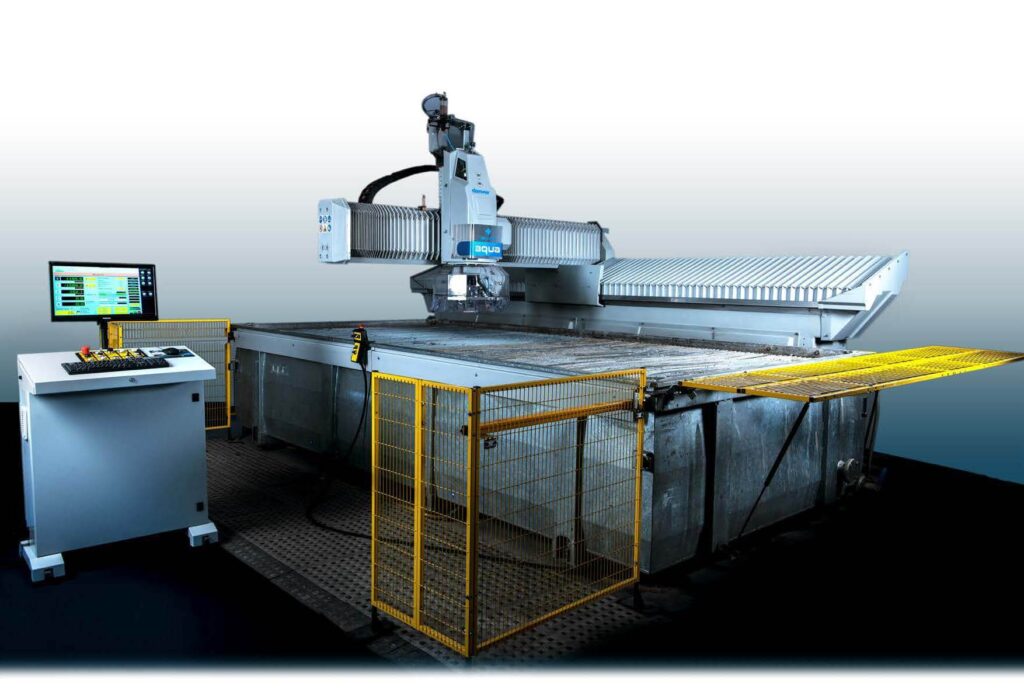
5.What are the applications of CNC water jet?
Water jet systems have become a precision manufacturing process with fast turnaround times, making it the preferred cutting method for several industries, especially those that require tight tolerances. Water jet CNC machines are favored by several industries for a variety of reasons. Here are some of those reasons:
1) Aerospace Industry
Aerospace components are often complex, require high precision, and essentially have no room for error. This is one of the main reasons why water jet CNC machines have become an integral part of manufacturing aerospace parts such as control panels and jet engine components.
Abrasive water jets are the best choice for cutting steel, brass, Inconel, and aluminum used in turbine blades, wing sections, brake components, and landing gear.
2) Automotive Industry
Robotic systems are the backbone of the automotive industry, and water jet CNC machines fit well into automated systems. However, the automotive industry uses both water jet CNC machine methods, and pure water jet CNC machines can shape interior carpets, insulation, and headliners while generating minimal material waste.
Water jet CNC machines do not produce heat-affected zones (HAZs), do not produce toxic fumes, and do not put pressure on the workpiece. Instead, it produces a burr-free surface, eliminating the need for secondary finishing.
3) Pharmaceuticals
In the medical field, water jet CNC machine technology can replace traditional surgical cutting tools for specific surgeries. For example, high-pressure spiral water crushes and aspirates liver parenchymal cells when treating tumors. It does not generate heat that could damage other organs, thus minimizing the possibility of bleeding. By varying the pressure and flow rate, human tissue can now be dissected with less trauma, bleeding, and post-operative problems.
4) Glass
Cutting glass is a tricky process that requires precision tools to avoid puncturing or shattering the glass. As in the medical industry, with water jet CNC machine glass, the water flow can be modified and adjusted to avoid damaging the glass. The water flow can cut any shape, form, configuration, or workpiece to the finest detail. The precise high-pressure water flow can cut holes and grooves without worrying about deformation.
5) Electronics
Manufacturers are always looking for ways to reduce costs and increase efficiency. Cost is a significant issue in the production of electronics, and the efficiency of water jet CNC machines makes them an essential part of electronics production. CNC water jets are ideal for cutting circuit boards or stripping wires without damaging them.
6) Fiberglass
The water jet CNC machine can shape and mold fiberglass without creating dust or excessive waste. The rigidity of fiberglass is not usually a factor, as the water jet CNC process can be used whether shaping insulation or building ships.
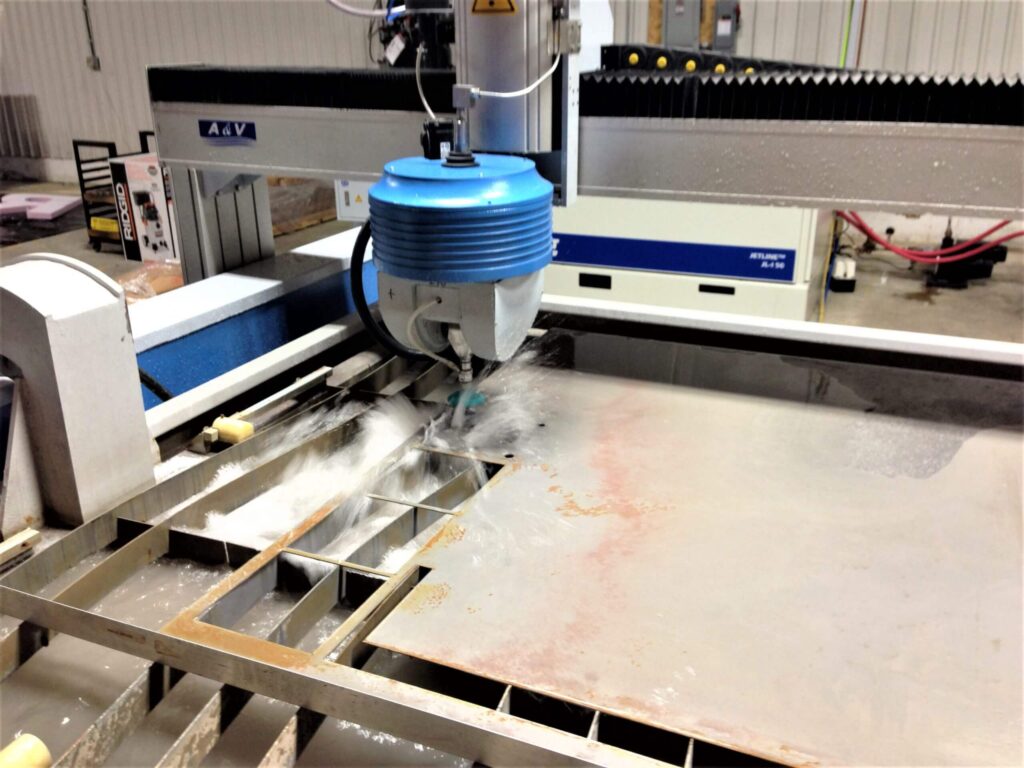
6.What are the advantages of water jet CNC machine?
Water jet CNC machine tools provide manufacturers with unparalleled versatility and flexibility. A series of advantages of using water jet CNC machine tools make this technology superior to other technologies such as laser and saw cutting.
1) No heat affected zone
What is the heat affected zone? This is an area in the metal that has not yet melted but has changed its properties due to exposure to relatively high temperatures. The cutting process generates high heat, which brings problems such as edge hardening and deformation to the workshop. Manufacturers overcome these problems by using cold cutting process water jet CNC machine tools.
2) Precise internal cutouts
The water jet CNC process can produce a variety of custom patterns, unique designs and logos. With cutting accuracy up to ±0.0005”, waterjet CNC machines are the tool of choice for precision cutting of internal components.
3) Excellent Edge Quality
Manufacturers achieve smooth, burr-free edges by combining the correct water velocity, pressure, nozzle size, and flow. In most cases, waterjet CNC machines eliminate the need for secondary finishing, saving significant time and money while increasing the efficiency of your production line.
4) No Tool Changes
Waterjet CNC machines allow you to process different materials without changing tools. Simply adjust the feed rate for the new material and thickness, and start the next cut.
5) Reduce Shop Costs
Waterjet CNC machines are a cold cutting process. Other machining methods that generate heat create hot zones, which often cause parts to warp, making them out of tolerance or even unusable. With the cold cutting process, CNC Water jets minimize or eliminate the possibility of scrapping machined parts.
And because water jet CNC machined parts require little to no edge preparation or secondary finishing, you can save money on these additional operations.
6) Material and thickness are not the main factors for water jet CNC machines
High-pressure cutting water and abrasive solutions can cut most materials. In addition, material thickness is not as important because water jet CNC machines can cut aluminum, multi-layer materials, composites, and hardened steels that are more than an inch thick.
7.What are the disadvantages of water jet CNC machines?
Although the advantages of CNC water jets are significant, there are still some disadvantages you need to consider:
1) Longer cutting time
Compared to traditional manufacturing processes such as CNC milling and lathe turning, CNC water jet CNC machines are significantly slower.
2) Expensive process
Hobbyists, DIY enthusiasts, and small shops may find CNC Water jet technology is beyond their reach.
3) Thicker materials are difficult to maintain dimensions
For very thick materials, water jet CNC machines may not work well and will have issues maintaining dimensional accuracy.
4) EDM may be a better choice
Depending on tolerances, metal type, and complex shapes, EDM may be a better choice than water jet CNC machine.
If you are looking for an experienced CNC machining manufacturer, Xavier is your ideal choice. The Xavier team is well-equipped to provide high-quality CNC machining solutions. If you need more information or to discuss your machining needs with us, please feel free to contact us.