Ways to Save on Custom CNC Parts Cost
Custom CNC parts can be a significant investment, especially for small businesses or individuals working on a tight budget. However, there are several ways to save costs on producing these parts without compromising quality. One effective strategy is to optimize the design for cost-effective CNC part production. This article will focus on how to optimize the design.
(1)When it comes to CNC machining, the design of the part plays a crucial role in determining the overall cost. By making a few design adjustments, it is possible to reduce the complexity and intricacy of the part, resulting in lower production costs. One way to achieve this is by simplifying the geometry of the part. Complex shapes and intricate details often require more time and resources to produce, driving up the cost. By simplifying the design and eliminating unnecessary features, it is possible to streamline the production process and reduce costs.
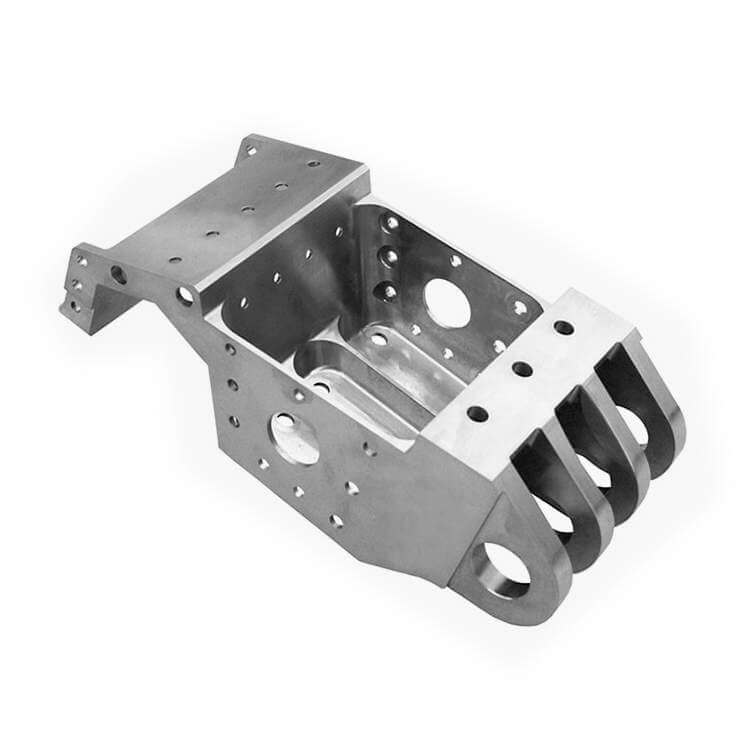
(2)Another important consideration when optimizing the design for cost-effective CNC parts production is the choice of materials. Different materials have varying costs, and selecting a more affordable material can significantly impact the overall cost of the part. It is essential to carefully evaluate the requirements of the part and choose a material that meets those requirements while also being cost-effective. Additionally, considering the availability and sourcing of the chosen material can help reduce costs further.
(3)Furthermore, it is crucial to consider the tolerances required for the part. Tight tolerances often require more precise machining, which can increase the cost. By loosening the tolerances slightly, it is possible to reduce the machining time and, consequently, the cost. However, it is important to strike a balance between cost savings and maintaining the functionality and quality of the part.
(4)In addition to optimizing the design, another way to save on custom CNC parts cost is by maximizing the efficiency of the production process. One effective strategy is to minimize the number of setups required for machining. Each setup involves changing tools and fixtures, which can be time-consuming and costly. By designing the part in a way that minimizes the need for multiple setups, it is possible to reduce production time and costs.
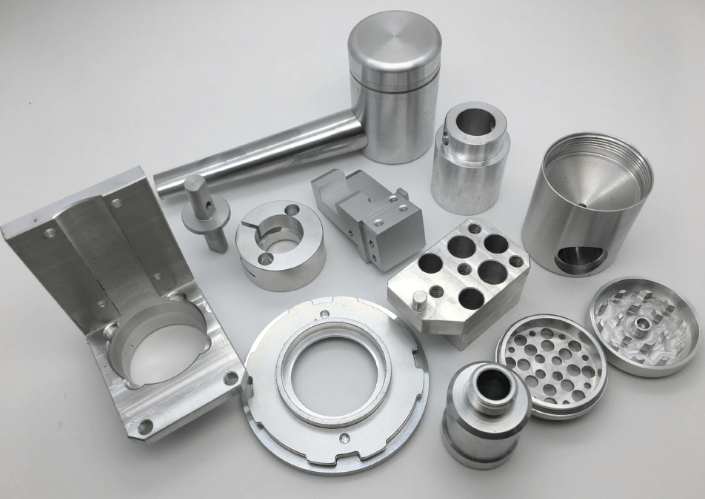
(5)Then, it is important to consider the nesting or arrangement of parts on the CNC machine bed. Because by optimizing the layout, machine utilization can be maximized and material waste reduced. This can result in significant cost savings, especially for larger production runs.
(6)Additionally, it’s worth exploring the use of standard tools and fixtures wherever possible. Because custom tooling and fixtures can be expensive, especially for one-off or low-volume production. By using standard tooling and fixtures, costs can be reduced and benefits maximized without compromising quality.
(7)Lastly, it is essential to work closely with the CNC machining service provider to explore cost-saving opportunities. They have extensive knowledge and experience in the field and can provide valuable insights and suggestions for optimizing the design and production process. By collaborating with the service provider, it is possible to find innovative solutions that can help save on custom CNC parts cost.
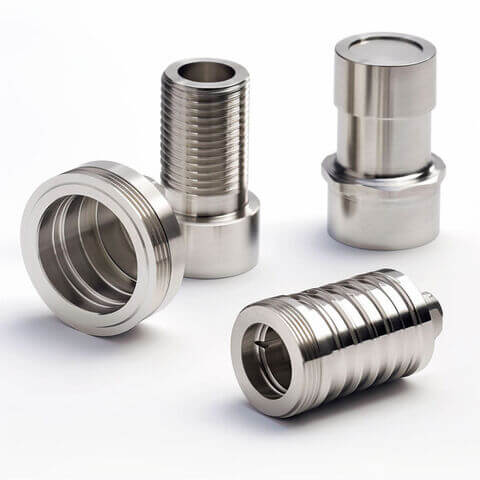
In conclusion, optimizing the design for cost-effective CNC parts production is a crucial strategy for saving on custom CNC parts cost. By simplifying the design, choosing cost-effective materials, considering tolerances, maximizing production efficiency, and collaborating with the service provider , it is possible to achieve significant cost savings without compromising on quality. These strategies can be particularly beneficial for small businesses or individuals on a tight budget, allowing them to access high-quality custom CNC parts at a more affordable price.