Manufacturing of Brass Turned Parts
In the intricate world of precision engineering, the spotlight often falls on the impeccable craftsmanship that goes into the manufacture of brass turned parts.
Carefully crafted from brass, these parts play a key role in a wide range of industries, from automotive to electronics.
In this comprehensive exploration, we delve into the subtle processes that go into making these beautiful parts, revealing the layers of skill and technology involved in their manufacture.
1.Getting to the bottom of it: What are brass turned parts?
Before we embark on our journey into the maze of manufacturing, let’s first gain a basic understanding of brass turned parts.
As the name suggests, these parts are made through a turning process, where a lathe precisely shapes the raw brass material into the desired shape.
The allure of brass lies not only in its aesthetic appeal, but also in its exceptional properties, including corrosion resistance and excellent machinability.
2.The Alchemy of Brass Tubes: Composition Matters
At the heart of brass turned parts lies the alchemy of brass composition. Brass is an alloy composed primarily of copper and zinc, with different proportions of brass producing a wide range of brass varieties.
The choice of brass alloy plays a key role in determining the final characteristics of a turned part. The synergy between copper and zinc creates a material that is not only durable but also has a golden sheen that adds a touch of elegance to the final product.
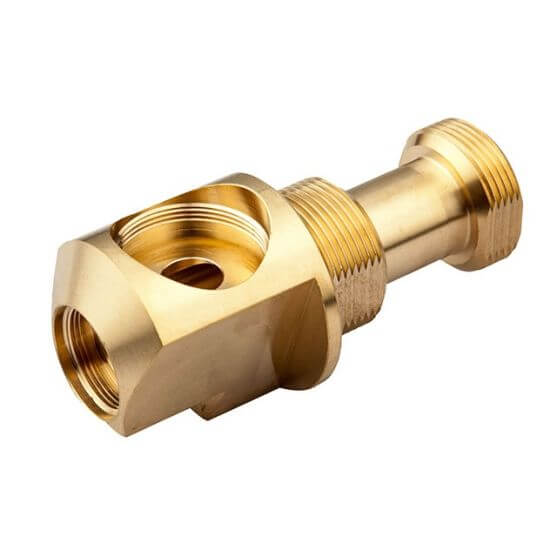
3.Precision Turning Process
1) The Beginning
The manufacture of brass turned parts begins with the turning process, a delicate process where the raw brass material undergoes a dance of transformation on the lathe. This type of machining requires great skill and a solid foundation to complete.
2) CNC Machining
Computer Numerical Control (CNC) machining takes center stage in the contemporary world of manufacturing. This avant-garde technology takes precision to the extreme, ensuring that every cut and every contour on the brass canvas is a reflection of superb craftsmanship.
When the CNC lathe begins its work, guided by complex programming, the turning machine carves out the brass turned part with unparalleled precision.
3) Swiss Turning
For those who seek the ultimate in precision, Swiss turning is a niche craft in the world of brass part manufacturing. Originated from the watchmaking industry, this technique has the extraordinary precision to produce intricate and miniature brass turned parts.
4.The Role of Design and Tools
1) Design Engineering
Before the machines start running, the blueprint takes shape through design engineering. Every detail of a brass turned component is carefully planned with functionality, aesthetics, and manufacturability in mind.
The design phase is where innovation begins, where ideas are crystallized into tangible shapes.
2) Tools
Behind every masterpiece is a set of carefully crafted tools that make the craftsman’s vision a reality. In the world of brass turning, specialized cutting tools and fixtures become the craftsman’s arsenal.
The choice of tools is as important as the design itself, affecting the surface finish, accuracy, and overall quality of the final product.
5.From Raw Brass to High Precision Parts
When the raw brass material undergoes a metamorphosis, transforming from a humble lump of metal into a refined and elegant brass turned component, several essential steps are taken.
1) Material Selection
The journey begins with the careful selection of the brass alloy. Whether it is a high content of copper for enhanced ductility or zinc for enhanced strength, the alloy composition sets the tone for the entire manufacturing process. This choice sets the stage for the final aesthetic and functional attributes of the turned component.
2) Preparing the Raw Material
The selected brass alloy, in the form of bar stock, becomes the craftsman’s canvas. The bar stock is carefully prepared to ensure uniformity and purity.
This step lays the foundation for the precision turning process, during which the bar stock will gradually reveal its potential and transform into a beautiful brass turned part.
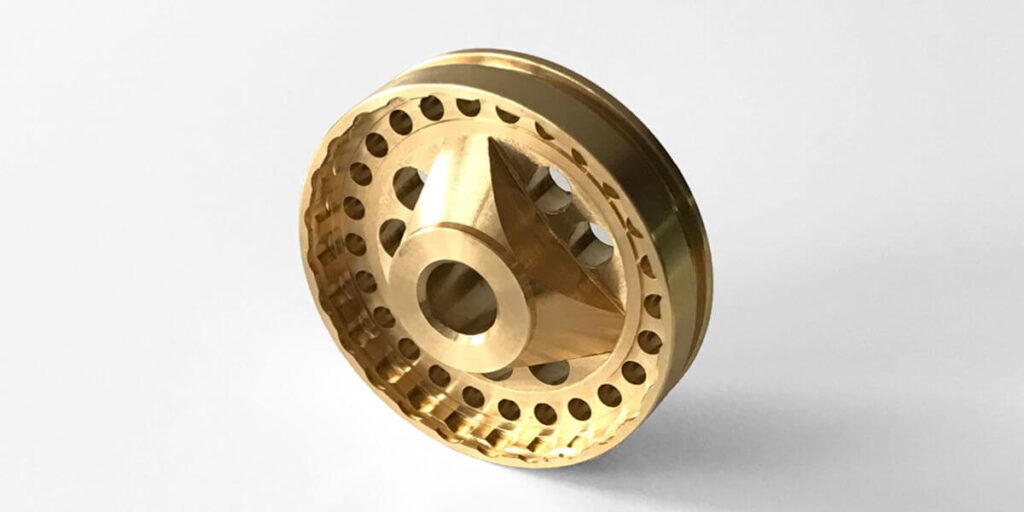
6.Processing Brass Turned Parts
1) Setting and Fixturing
After the bar stock is fixed, the setting and fixing process marks the beginning of the turning performance. The fixture is like a baton, holding the raw material in place, allowing the lathe to coordinate its intricate dance. The precision of the fixture is crucial because it ensures consistency throughout the production line.
2) Turning Operation
The turning operation is like the dance of the lathe, skillfully carving the brass. From surface and groove to threading and knurling, each operation leaves its mark on the material.
Guided by the craftsman’s expertise, the lathe shapes the brass into the desired shape, reflecting the essence of brass turned parts.
3) Quality Control
In the pursuit of perfection, quality control becomes a coordinating force. Each turned component is meticulously inspected to ensure it meets exacting standards for precision and functionality.
This step is the culmination of the craftsman’s expertise and technical precision to create an unrivaled brass turned component.
7.Expertise
1) Thread Rolling
Thread rolling adds precision to brass turned parts. Commonly used to make threaded components, this technique enhances the mechanical properties of the threads, ensuring optimal functionality and durability.
2) Knurling
Knurling is a handcrafted process that adds texture and grip to turned parts. This not only enhances beauty, but also serves a practical function, providing a tactile surface to the turned component and improving handling.
8.Post-Machining Finishing
1) Deburring
After the brass turned part has been turned and machined, the deburring process smooths the edges and eliminates any imperfections left by the cutting tool. This meticulous step ensures a flawless look and safety.
2) Surface Treatment
The final act of the brass symphony is surface treatment. Whether it’s a shiny polish, a soft matte finish, or a protective coating, surface treatment adds the finishing touch to brass turned parts, elevating them from mere components to works of art.
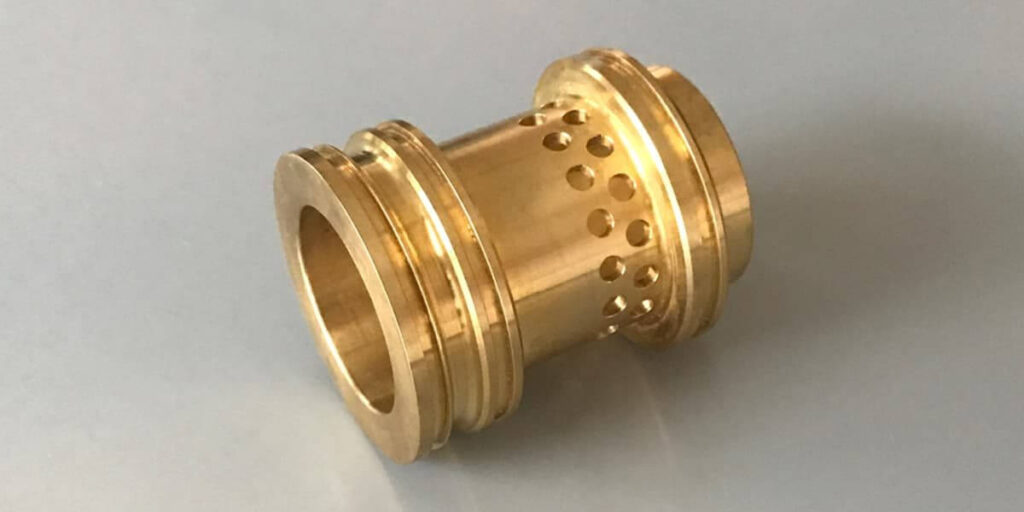
9.Uses of Brass Turned Parts
Brass turned parts are used in many industries, including:
- Plumbing and plumbing fixtures
- Electrical applications
- Medical applications
- Automotive applications
- Hydraulic applications
- Computer industry
- Architectural applications
- Construction industry
- Rifle ammunition
- Heat exchangers and fluid control valves
Brass turned machine parts have a wide range of uses in a variety of industries. These parts are essential for creating smooth surfaces and fixtures in everything from plumbing to construction.
10.Conclusion
In the world of manufacturing, the manufacture of brass turned parts is a testament to the heritage of craftsmanship. From the careful selection of brass alloys to the precision turning process to the artistry of specialized techniques.