Advantages and limitations of 3D printing
It is an additive manufacturing technology that stacks and fuses successive layers of materials to create precise and complex functional parts or products. Therefore, 3D printers do not use blocks of material to manipulate shapes. Instead, the nozzle deposits material layer by layer on the print bed from bottom to top according to the slice pattern of the uploaded design.
Slicing patterns, meanwhile, refer to dividing the CAD model into horizontal layers. Each slice represents a cross-sectional area of the model along which the printer deposits layers of material.
Additionally, there are several 3D printing technologies that you may need clarification on. They follow the same basic principles. However, they differ in working mechanisms, material compatibility, and printing capabilities.
Advantages of 3D printing
3D printing manufacturing has several application benefits. It offers design flexibility, faster delivery times, customization, and more.
1.Design flexibility and complexity
3D printing can create highly complex geometries and contours. It is more complex than traditional methods such as CNC lathe machining or injection molding. It does not have the same restrictions as subtractive manufacturing, such as complex hollow parts, sunken parts and internal meshes.
Additionally, the ability to create complex shapes directly benefits designers. They can produce more innovative and complex designs to address manufacturing needs. Additionally, designers do not need to consider draft angles, tool channels, thickness uniformity, large assemblies and other limitations when designing for 3D printing. Therefore, it brings ultimate design flexibility.
2.rapid prototyping
Production speed, accuracy, and cost-effectiveness make 3D printing a solid choice for rapid prototyping. Part production time varies from minutes to hours, depending on complexity and 3D printing materials. And 3D printing does not require upfront tooling costs, making the design change process simple and reducing prototype costs.
3.Customization and personalization
The 3D printing process involves manufacturing directly from digital files and can handle complex designs. As a result, 3D printing allows parts and products to be customized to specific needs. If you have a custom design (3D model), you can accurately translate it into physical reality using the right materials and printing equipment. This kind of customization can be very beneficial for medical applications. For example, 3D printing can create customized implants for patients.
4.Cost-effectiveness of small batch production
The main reason why 3D printed parts are less expensive in low-volume production is that it does not require expensive manufacturing equipment such as molds or tooling. Meanwhile, other methods such as injection molding involve significant upfront investments in molds, which results in higher casting volumes per part produced in small batches or batches. For example, low-volume production of nylon parts first requires aluminum injection molds that cost at least $10, 0 00, whereas 3D printing requires no such cost.
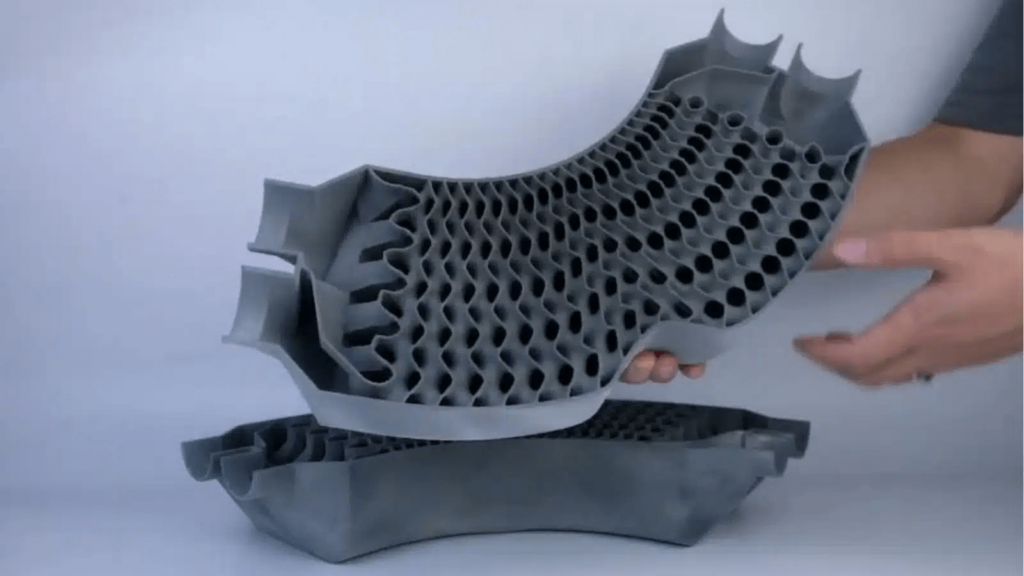
Limitations of 3D printing
1.Material limitations
Compared to other processes, such as CNC machines, 3D printing has a smaller selection of materials. 3D printers are generally compatible with plastics (ABS, PETG, and TPU), photopolymers, and some thermosets (steel, titanium, and aluminum). However, 3D printing has rapidly expanded its range of materials beyond basic thermoplastics.
2.Less strong and durable
When a 3D printer transforms a design by adding layers of material, the mechanical strength of the final part can be compromised. For example, FDM parts can delaminate or perform poorly under stress in a specific direction (usually the Z-axis). Additionally, parts may lose their original properties, such as hardness or fatigue strength. Parts also become less durable for these reasons.
3.Surface finish and precision
There will be obvious layer marks left, and sometimes some support material will remain. Therefore, post-processing is required, such as sandblasting, deburring, and even machining. The surface roughness value of 3D printed parts can be as low as 4 microns (approximately). Secondly, its accuracy is also lower than other popular manufacturing technologies, with a typical accuracy of ±0.2 mm, while CNC can achieve an accuracy of ±0.005 mm and compression molded rubber parts can achieve an accuracy of ±0.025 mm.
4.size limit
Compared to other processes such as injection molding or laser cutting, 3D printing has part size limitations. Size capabilities are limited by the build volume and bed size (print chamber) of the 3D printer machine. For example, 3D printing can make long wind turbine blades due to size constraints. However, large parts can be made by assembling individual 3D printed small segments.